Can an Air Pressure Regulator Work on Vacuum
Choosing a gas regulator size larger than necessary might seem like a good idea, but it can lead to several issues. Here’s why precision in selecting the right size is crucial.
Can An Air Pressure Regulator Work On Vacuum
Air pressure regulators aim to stabilize output pressure, countering input pressure variations. A vacuum, characterized by the absence or near-absence of air, complicates this function due to the absence of a pressure differential, a critical factor for the regulator’s operation.
In vacuums, with minimal atmospheric pressure, the regulator lacks a medium to adjust. Its mechanism, designed to alter flow to achieve a set pressure, fails without a pressure gradient. Thus, using an air pressure regulator in a vacuum overlooks the essential requirement for a pressure variance.
Moreover, air pressure regulators are not built for vacuums. Components like seals and diaphragms, crafted for pressurized air, may not perform well in vacuums. This could cause leaks or the regulator’s inability to maintain set pressure, deeming it ineffective.

What Is Air Pressure Regulator
An air pressure regulator is a device crafted to maintain steady pressure. It’s key in situations requiring precise pressure for optimal operation. Essentially, it comprises a valve, spring, and diaphragm or piston. These parts work together to adjust and stabilize pressure, reacting to changes in air flow or input pressure.
You’ll see these regulators in various places. They’re in industrial setups, medical devices, and home AC systems. Their role in controlling air flow and maintaining desired pressure is crucial.
In essence, an air pressure regulator ensures consistent output pressure. It balances incoming pressure changes and air flow rate adjustments. This device is indispensable for precision-based applications across multiple industries.
How Does Air Pressure Regulator Work
An air pressure regulator stabilizes output pressure, unaffected by input fluctuations. It comprises a valve, diaphragm or piston, and a spring. The valve regulates air flow. Linked to it, the diaphragm or piston adjusts based on downstream pressure changes. The spring, preset in tension, counters this pressure. This interplay between spring tension and air pressure adjusts the valve’s position.
Adjusting the spring sets the desired output pressure. If downstream pressure falls, the spring expands, opening the valve to increase flow until equilibrium is restored. If pressure rises, the spring compresses, reducing the valve opening and air flow, achieving balance.
This device ensures consistent output pressure. It optimizes pneumatic tool and system performance, even with varying supply conditions.
What Is Vacuum Regulator
Vacuum regulators are key for precise vacuum control in many settings. They adjust vacuum force, ensuring it stays within needed limits. This prevents damage to delicate materials or components. These devices are fine-tuned for exact vacuum levels, crucial in both research and manufacturing. They protect equipment from excessive vacuum force, which can cause failure or harm product quality.
These regulators are vital for operational efficiency and safety. They are used in diverse applications, from scientific experiments to industrial processes. By managing vacuum levels, they prevent potential harm to sensitive operations. Vacuum regulators also enhance energy efficiency. They adjust vacuum force to the minimum required, cutting down on energy use. This reduction in energy consumption lowers costs and benefits the environment. Their role in promoting sustainability in industries is increasingly important.

How Does Vacuum Regulator Work
A vacuum regulator maintains a specific vacuum level by adjusting the pressure. It lowers vacuum to a setpoint. It uses a control mechanism to manage gas flow, affecting the vacuum intensity. If the vacuum is too strong, it lets in gas to decrease it. If too weak, it restricts gas, strengthening the vacuum.
The regulator’s core relies on a diaphragm. This diaphragm senses vacuum changes and moves. Its movement controls the valve, adjusting the gas flow. This maintains the vacuum at the desired level.
Vacuum regulators allow setpoint adjustments. This ensures precise vacuum control for different applications. It is crucial for processes needing exact vacuum conditions. It ensures consistent performance and avoids damage from incorrect vacuum levels.
What Are The Key Differences Between Air Pressure Regulators And Vacuum Regulators?
You must understand that air pressure regulators are tailored for gases at pressures above atmospheric levels, while vacuum regulators handle pressures below these levels. Their operational ranges reflect this distinction; vacuum regulators are specifically designed for negative pressure environments, unlike their air pressure counterparts. The internal design and mechanisms differ due to the contrasting nature of managing vacuum versus positive pressure scenarios.
Pressure Vs. Vacuum
Air pressure regulators and vacuum regulators serve distinct functions based on their operating pressure realms. Air pressure regulators work with pressures above the atmospheric level. They ensure a stable output pressure, compensating for any input pressure variations. This stability is crucial for systems requiring a consistent gas flow. On the other hand, vacuum regulators operate under atmospheric pressure. They precisely manage the negative pressure or suction force. This capability is vital for processes needing controlled vacuum conditions.
The correct application of these regulators is essential. Using the wrong type can disrupt system operations, leading to inefficiencies or even failures. For instance, employing an air pressure regulator where a vacuum regulator is needed could result in inadequate suction, affecting the process’s outcome. Conversely, using a vacuum regulator in a system requiring pressurized gas could lead to uncontrolled gas flow.
Operational Range
Air pressure regulators and vacuum regulators have distinct operational ranges. Air pressure regulators work above atmospheric levels. They ensure a consistent, controlled gas flow. Essential for many applications. Vacuum regulators, however, manage negative pressures. They’re crucial for maintaining vacuum conditions. This prevents contamination and ensures consistent conditions. Vacuum regulators are vital for specific atmospheric needs. Each type serves a unique purpose, depending on the pressure environment required. Air pressure regulators stabilize pressure above the atmosphere. Vacuum regulators maintain below atmospheric pressures. Both are critical in their respective fields for maintaining desired conditions.
Design Differences
Air pressure regulators and vacuum regulators differ fundamentally due to their operational environments. Air pressure regulators are designed to manage positive pressure. They typically incorporate a spring-loaded diaphragm or piston. This setup ensures output pressure remains constant despite fluctuations in input pressure. The mechanism dynamically adjusts. Its goal: to equalize the force downstream with the pressure coming from upstream.
Vacuum regulators, conversely, are crafted to handle vacuums. Their design usually involves a spring-loaded mechanism too. However, its function contrasts with that of air pressure regulators. It modulates the air intake into the system. This regulation aims to maintain a stable vacuum pressure. Such design distinctions are not arbitrary. They are essential for each regulator’s efficacy in its specific role. One ensures precise air pressure management. The other, a consistent vacuum condition.
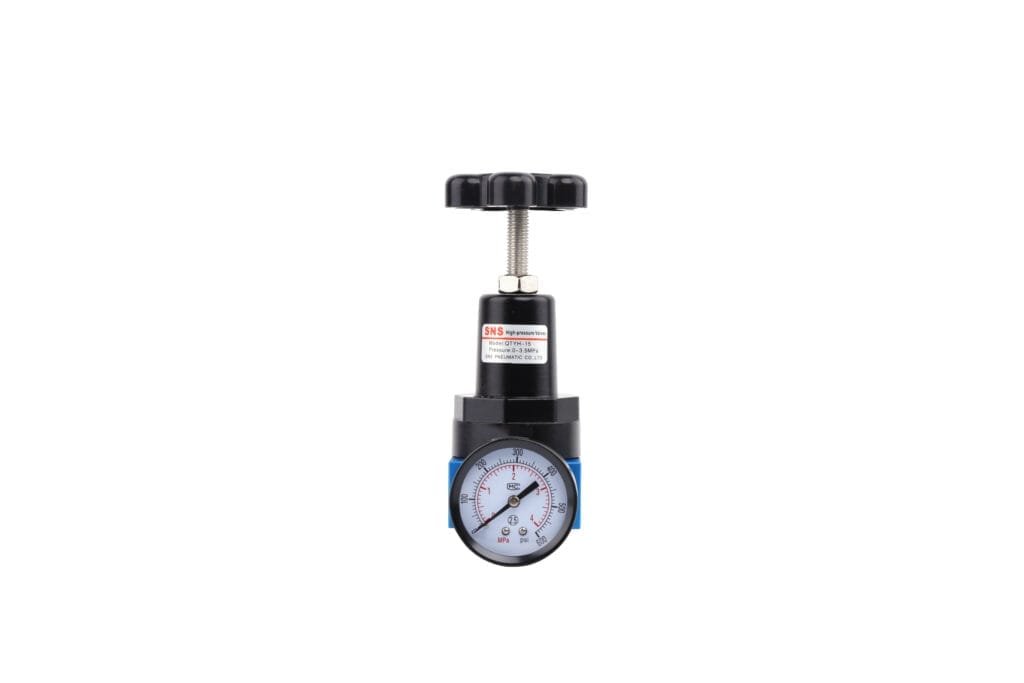
Faqs
Can You Use A Pressure Regulator For Vacuum?
Many wonder if a pressure regulator can work for vacuum needs. This requires understanding their differences. Pressure regulators control gas pressure entering a system. They ensure a stable output. Vacuum systems, however, remove air or gas to create a vacuum. This is a distinct process. Using a pressure regulator for vacuum isn’t simple. Pressure regulators manage downstream pressure. They don’t create or maintain a vacuum. For vacuum conditions, a device designed for negative pressures is necessary. These devices are engineered to handle and sustain vacuums safely.
Is A Back Pressure Regulator The Same As A Vacuum Regulator?
Back pressure regulators and vacuum regulators serve distinct purposes. Back pressure regulators keep the pressure before them constant by letting out extra pressure after them. This is crucial in systems needing steady upstream pressure for optimal operation. On the other hand, vacuum regulators manage vacuum levels. They work by letting air or gas into a system to keep the vacuum from getting too strong, based on a set limit. While both tools adjust pressure, they work in different areas. Back pressure regulators deal with the pressure of liquids or gases in pipes. Vacuum regulators focus on vacuum conditions. Each plays a unique role in various settings.
How Do I Control The Pressure On My Vacuum Pump?
To control your vacuum pump’s pressure efficiently, it’s crucial to first identify its type. Different pumps like rotary vane, diaphragm, or turbomolecular have unique control methods. Control often involves adjusting inlet or outlet valves. These adjustments affect the flow rate and, consequently, vacuum levels. Monitoring pressure with a vacuum gauge is essential for precise control. Consider the pump’s capacity and the system’s volume. These factors impact the achievable vacuum level. Proper pressure maintenance enhances your vacuum pump’s efficiency and longevity.
How Does A Vacuum Pump Regulator Work?
A vacuum pump regulator finely tunes the vacuum level produced by the pump. This tuning aligns with specific needs for precision across various tasks. It changes the pump’s suction power. This can be done by hand or set to adjust automatically. This ensures the vacuum level stays where it’s needed. A key part of the regulator is its feedback system. It continuously checks the vacuum level. If changes occur, it adjusts in real time. This keeps performance steady, even if the workload varies. The regulator also prevents too strong a vacuum. This is important because too much vacuum can harm delicate parts or upset the process it’s supporting. By keeping the vacuum level just right, the regulator makes the pump work better. It also helps control the process more tightly and makes the whole system last longer.
Conclusion
Oversizing a gas regulator can lead to inefficiencies and potential safety issues in gas distribution systems.
To ensure optimal performance and safety, it’s crucial to select the right size gas regulator for your specific needs. Consult with experts and refer to technical guides to make an informed decision.