Can I Add Additional Gauge To My Air Regulator
Yes, you can add an additional gauge to your air regulator to monitor pressure more accurately or to keep track of different pressure readings.
For detailed steps and considerations on how to enhance your air regulator with an extra gauge, continue reading the full article.
Types Of Gauges For Air Regulators
You’ll find several types of gauges for air regulators, each with its unique mechanism and application.
Bourdon Tube Gauges
Bourdon tube gauges stand out in air regulation systems due to their unique curved tube design. This design is key to their operation. As internal pressure rises, the tube’s curvature changes. This change, though mechanical, is precise. It directly influences the dial indicator, providing a clear pressure reading. Such direct translation of mechanical action to readable data underscores the gauge’s reliability.
The simplicity of these gauges is noteworthy. Despite their basic mechanical operation, they deliver durable and accurate performance. This makes them particularly valuable in settings where precision is critical. The robustness of Bourdon tube gauges is another highlight. Designed to endure tough conditions, they maintain accuracy even in demanding industrial environments.
Choosing a gauge for an air regulator involves considering compatibility and accuracy needs. Bourdon tube gauges meet these requirements efficiently. Their wide-ranging pressure measurement capability ensures versatility. This adaptability, coupled with their proven durability, positions them as a top choice for precise pressure monitoring in various applications.
Diaphragm Gauges
Diaphragm gauges stand out in air regulation, thanks to their unique design. They employ a flexible membrane, distinguishing them from Bourdon tube gauges. This membrane reacts to air pressure changes. As pressure alters, the diaphragm moves. This movement is then accurately measured. Unlike the mechanical deformation in Bourdon tubes, diaphragm gauges excel in detecting low pressures.
They consist of a chamber, split by the diaphragm. This setup ensures precise pressure readings. Their design leads to minimal measurement errors. Thus, they’re perfect for tasks needing exact pressure control. They shine in handling gases needing careful pressure adjustments.
Moreover, diaphragm gauges are built to last. They withstand pressure pulsations or spikes well. This durability makes them reliable components in air regulation systems. Their sturdy construction enhances their lifespan. In summary, diaphragm gauges offer accuracy, precision, and reliability for managing air pressure, especially in delicate applications.
Capsule Gauges
Capsule gauges represent a crucial tool for measuring very low pressures and vacuums with exceptional precision. These instruments are particularly useful in applications where detecting subtle variations in pressure is critical. They operate on a simple yet effective principle: two metal capsules, joined together, react to changes in pressure by either expanding or contracting. This physical movement is accurately converted into a measurement, which is displayed on the gauge’s dial.
The design of capsule gauges makes them highly sensitive to small pressure changes, setting them apart from other types of pressure gauges. This sensitivity is both a strength and a limitation. On one hand, it allows for highly accurate readings in low-pressure scenarios, making these gauges indispensable in certain technical setups, such as air regulators. Here, the precise control and monitoring of pressure can be vital for optimal performance.
On the other hand, the very feature that makes capsule gauges so valuable in low-pressure applications—their sensitivity—also renders them unsuitable for high-pressure environments. The delicate structure of the capsules can be easily damaged by excessive pressure, limiting their use to applications where pressure levels remain relatively low.
Incorporating a capsule gauge into an air regulator setup can significantly enhance the system’s precision. This improvement is not just marginal; it can be the difference between adequate performance and peak efficiency. The ability to detect and adjust to the slightest changes in pressure allows for a level of control that is hard to achieve with other gauge types.
Differential Pressure Gauges
Differential pressure gauges are a step up from capsule gauges. They are crucial in air regulator systems. They measure pressure differences accurately. This accuracy is vital for optimal air regulator performance. These gauges offer more than simple pressure readings. They provide precise pressure differential data. This is key for controlling flow rates accurately, especially in pneumatic and HVAC systems. Adding a differential pressure gauge improves your system. It helps maintain efficiency and consistent performance.
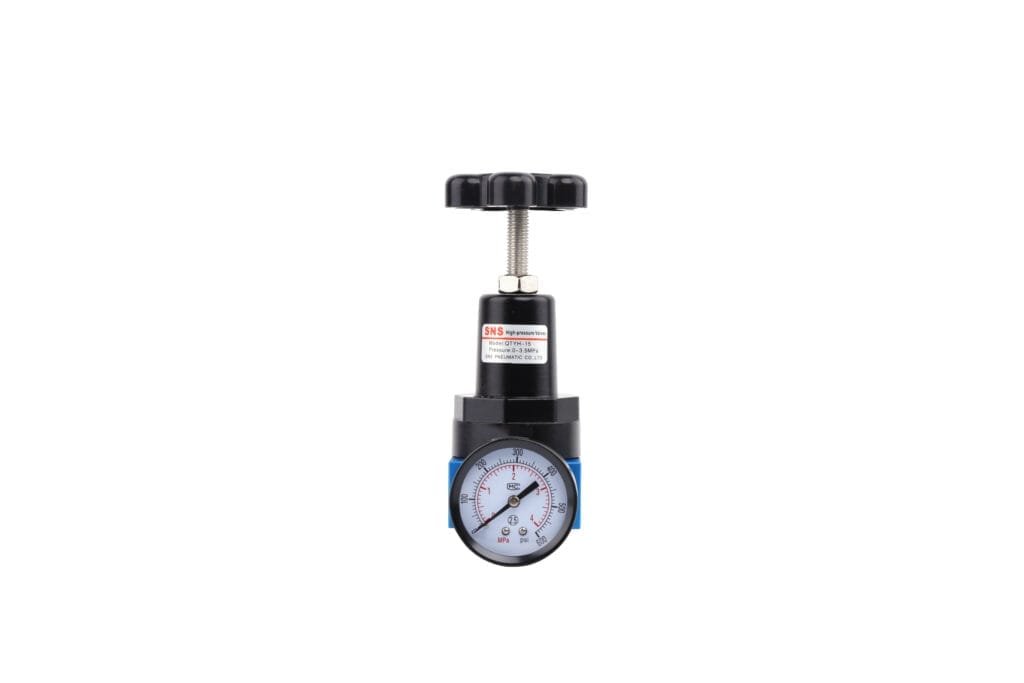
Purpose Of Adding An Additional Gauge
When you add an additional gauge to your air regulator, you’re equipping yourself with the ability to monitor both incoming and outgoing pressure simultaneously. This dual reading capability is vital for ensuring precise control in sensitive applications, such as painting or airbrushing. Additionally, it improves safety by allowing you to detect overpressure situations early and offers convenience by improving visibility and providing essential information based on your specific setup needs.
Dual Reading
Adding an extra gauge to your air regulator is a smart move. It lets you keep an eye on both the pressure coming in and going out. This is crucial for tasks like painting or airbrushing. Such a setup ensures you use the right pressure for your work. It stops common issues like using too much or too little material.
Precise pressure control improves paint flow and airbrush accuracy. This leads to better finishes and saves materials. You can adjust pressures on the fly, tailoring your approach to different surfaces and paint types. This added control boosts your work quality, making your results consistently good.
Safety
Installing an extra gauge enhances control and safety in painting projects. It helps monitor system performance, preventing overpressure that could damage tools or cause safety hazards. Overpressure leads to tool wear or failure. Monitoring supply and regulated pressures allows for precise adjustments. This keeps air pressure within safe limits, protecting equipment and ensuring operator safety. Adding a monitoring layer prevents overpressure, extending tool life and enhancing safety.
Convenience
Adding extra gauges to an air regulator setup enhances its functionality. It makes it easier to see and understand what’s happening, increasing both safety and efficiency. With another gauge, you can tailor the system to better meet your specific needs. This means you can keep an eye on different measurements at the same time. Knowing the system’s status at all times helps with quick troubleshooting and adjustments. Adding gauges is a smart choice for precise control and better results. It helps avoid problems before they start.

Considerations Before Adding
Before you proceed with adding an additional gauge to your air regulator, you need to verify a few critical points. First, validate the new gauge is fully compatible with your regulator concerning size, pressure range, and connection type. Additionally, inspect that your regulator has the capacity to support another gauge without compromising its functionality or accuracy, and decide on the gauge’s installation location for best visibility and safety.
Compatibility
Firstly, size matters. The gauge must physically fit the space and ports available on your air regulator. An incorrect size can lead to improper installations, which may cause system inefficiencies or failures.
Secondly, consider the pressure range. The gauge needs to accurately measure the pressures within your system’s operating range. If the gauge’s range doesn’t align with your system’s pressures, it could give misleading readings. This discrepancy can lead to unsafe conditions or damage to your system over time.
Thirdly, the connection type is crucial for a leak-free fit. Common standards include NPT and BSP connections. Using the wrong type can result in leaks, which compromise system safety and efficiency.
Regulator Capacity
To ensure your air regulator can accommodate an additional gauge, it’s essential to conduct a thorough evaluation. Initially, check if the new gauge aligns with the air regulator in terms of size, pressure range, and connection type. This step is fundamental to guarantee compatibility.
Next, delve into the specifics of your regulator. Examine its maximum flow rate and pressure capabilities. It’s crucial because introducing a new gauge could potentially add flow restriction or induce pressure drops. Such changes might occur if your regulator is already operating near its capacity limit. Ensuring there’s enough room for this addition without compromising performance is key.
Furthermore, investigate the design of your regulator. It’s important to understand if it’s engineered to handle another gauge. This involves looking into the internal pathways of the regulator. Check for any areas that might cause pressure losses. The goal is to maintain the regulator’s operational efficiency even with the addition of a new gauge.
Another critical aspect to consider is the installation process. It must be executed in a way that doesn’t affect the accuracy of both the existing and the new gauges. Avoid setups that could introduce turbulence or erratic air flow. Such conditions can lead to inaccurate readings, defeating the purpose of adding a new gauge.
Installation Location
Choosing the right spot for your gauge is crucial. It must be easily seen while working, not hidden or hard to reach. Avoid placing it in damp or sunny spots to prevent damage. Ensure it’s accessible for upkeep but won’t block paths or cause accidents. Consider work flow and space limits to find the best location that ensures safety and efficiency.
Firstly, visibility is key. The gauge should be in clear view during normal operations. This prevents strain and ensures accuracy in readings. Secondly, the environment matters. Avoid dampness and sunlight to protect the gauge. Thirdly, think about maintenance. The gauge should be reachable for repairs without being in the way. Lastly, safety cannot be compromised. The gauge must not obstruct walkways or pose a hazard. Balancing these factors is essential for an effective installation.

How To Add An Additional Gauge
Before you start adding an additional gauge to your air regulator, you’ll need to gather the necessary materials such as an extra gauge, appropriate fittings like T-fittings and nipples, and thread sealant or Teflon tape. It’s important to make sure all pressure is released from the system to avoid any potential hazards before beginning the installation process. Following these preparatory steps, we’ll now discuss the specific installation steps to successfully add the gauge.
Gather Materials
To add an extra gauge to an air regulator, gather essential items: an extra gauge, specific fittings (like T-fittings and nipples), and thread sealant or Teflon tape. Choose a gauge that fits your system’s pressure. Ensure fittings match your regulator’s thread size for a tight seal. T-fittings allow for branching, and nipples connect parts. Use thread sealant or Teflon tape on threads to prevent leaks. Apply sealant correctly, enhancing the seal’s strength for a secure setup.
Safety Precautions
Before starting the installation of an extra gauge, it’s paramount to ensure the system is completely depressurized. Begin by activating the release valve. This step is crucial for your safety. Confirm there’s no air remaining. This action helps prevent unwanted releases or damage to the equipment during the setup.
Safely lowering the pressure in the system is a key safety measure. It helps avert any risks. Once you’ve opened the release valve, pause. This wait is essential. It ensures the system has no pressure left. Listen for silence. No sound of air means it’s safe to move forward.
This careful process protects you. It also keeps the equipment, like the air regulator and the new gauge, safe from harm. Ensuring the system is depressurized is a fundamental safety step. It’s vital before adding any new components. This approach minimizes hazards and ensures a smooth installation.
Installation Steps
Ensure your system is not pressurized before starting. Choose the right spot on your regulator for the new gauge. This spot should not affect the regulator’s usual functions or block any existing connections. Before attaching the gauge, wrap its threads with Teflon tape or apply thread sealant. This step is crucial for preventing air leaks. Start threading the gauge by hand to avoid cross-threading, which can damage the threads. Once it’s hand-tight, use an adjustable wrench to tighten it further. Be careful not to over-tighten, as this could strip the threads. Finally, check all connections thoroughly to ensure there are no leaks. Your system now has an added gauge for better monitoring.

Post-Installation
Once you’ve added an additional gauge to your air regulator, it’s important to validate its functionality and reliability. Start by conducting a leak test using soapy water around the connections to spot any air leaks. Then, perform a calibration check by comparing the new gauge’s readings with a known pressure source or another gauge, and don’t forget to regularly inspect both gauges for accuracy and signs of wear or damage.
Leak Testing
To find air leaks in your air regulator setup, spread soapy water over every connection. Watch for bubbles. Bubbles mean air is leaking. This method is simple but powerful for spotting leaks. Check every joint and seam with the soap mix. Bubbles indicate a leak, harming system performance. Fix leaks quickly by tightening or resealing connections. This ensures your system works well and lasts longer. It’s crucial for keeping the system efficient and stable. Care in this process maintains your setup’s effectiveness over time.
Calibration Check
First, confirm there are no leaks by applying soapy water around connections. Next, test your new gauge’s accuracy. Use a reliable pressure source or another gauge for comparison. Apply a known pressure. Note your gauge’s reading. Check it against the reference. If readings differ, adjust or calibrate your new gauge. Correct calibration ensures safety and performance.
Regular Maintenance
To keep gauges accurate and undamaged, perform frequent checks. After adding a gauge to your air regulator, plan regular reviews. Compare gauge readings with a known pressure source to check accuracy. Look for reading differences, suggesting calibration or sensor issues. Also, examine each gauge’s physical state. Cracks in the glass, for instance, can affect reading reliability. Likewise, dust, dirt, or moisture can hinder performance. Clean gauges with a soft, dry cloth and fix any damage quickly. Consistent upkeep is key for system precision and safety.
Alternatives To Adding An Additional Gauge
Check your air regulator first. It might have what you need already. Sometimes, these devices come with extra functions that can do the job of an additional gauge. Look closely at what your regulator offers.
Think about digital air regulators. These have precise electronic displays showing air pressure, flow, and sometimes temperature. They’re more accurate and can track more than one thing at once. This choice could simplify your setup, making extra analog gauges unnecessary.
Remote monitoring systems are another option. They let you watch and record your air regulator’s performance from afar. This tech keeps an eye on things all the time and lets you change settings without being there. This could make an extra gauge not needed.

Faqs
Do Pressure Regulators Usually Have Two Gauges?
Pressure regulators commonly feature two gauges, a design aimed at precise monitoring of both the incoming and adjusted pressures. This setup is crucial for various reasons. First, it lets users observe the pressure before it enters the regulator and the adjusted pressure that comes out. This is vital for maintaining the system’s operations within safe limits, preventing potential hazards linked to too high or too low pressures.
Most regulators, especially those used in critical applications like pneumatic systems or gas flow control, include this two-gauge configuration. This standard design helps in making immediate adjustments to ensure optimal performance. Knowing what each gauge indicates is key to effectively managing and solving issues within the system, thus guaranteeing its dependable operation and high efficiency.
What Do You Have Two Gauges For On One Regulator?
Two gauges on a regulator serve distinct, vital roles. The first gauge tracks the tank’s pressure. It shows how much air or gas is left. This is key for avoiding sudden run-outs during important tasks. The second gauge shows the outlet pressure. This is the pressure at which air or gas reaches your tools or systems. Adjusting this ensures your equipment works optimally without damage.
Each gauge offers specific insights. The tank pressure gauge helps plan and prevent interruptions. The outlet pressure gauge allows precise control over how much pressure is used. Together, they ensure your system works smoothly and efficiently.
Can An Air Regulator Increase Pressure?
An air regulator is a tool that does not have the capability to increase air pressure beyond the source’s capacity. Its main function is to reduce the pressure from the compressor to a level that is manageable and appropriate for various tools and applications. It serves as a regulatory device, ensuring that the output pressure remains constant and at a lower level than the input pressure. Adjusting the regulator will not result in an increase in pressure; it will only manage the pressure to prevent it from exceeding a certain level. This limitation is crucial for the safety and efficiency of both the equipment and the user. Misunderstanding the purpose of an air regulator and attempting to use it to boost pressure can lead to negative consequences, such as reduced efficiency and potential damage to the equipment. The primary role of the regulator is to ensure stable and reduced pressure, not to enhance the pressure supplied by the compressor.

How Many Pressure Gauges Are In Regulator?
Air regulators can have either one or two pressure gauges. A single gauge shows the output pressure, indicating the pressure level supplied to tools or applications. This is crucial for monitoring and adjusting the pressure to the required level for optimal performance. A second gauge, if present, measures the input pressure from the air supply. This feature is particularly beneficial for diagnosing issues within the system. It helps in identifying any discrepancies between the input and regulated pressures, which can be critical for troubleshooting and ensuring the system operates efficiently. Having both gauges allows for comprehensive monitoring of the air regulator’s performance, making it easier to maintain consistent pressure levels and detect potential problems early. The presence and configuration of these gauges are key to managing system pressure effectively and ensuring the longevity of both the regulator and the tools it serves.
How Can I Ensure That The Additional Gauge Provides Accurate Readings?
Ensuring Accuracy of an Additional Gauge
Choose the Right Gauge: Select a gauge that matches your air regulator’s pressure range and specifications. Compatibility is crucial for accuracy. Using a mismatched gauge can lead to incorrect readings, misleading data about the system’s pressure.
Install Correctly: Installation precision is key. An improperly installed gauge might not provide reliable readings. Ensure it’s installed according to the manufacturer’s guidelines. Use thread sealant tape on connections to prevent air leaks, which could skew the readings.
Calibrate Regularly: Over time, even the best gauges can lose accuracy. Regular calibration against a known standard is essential. This process adjusts the gauge, ensuring its readings remain accurate and reliable. Make calibration a routine part of your maintenance schedule.
Protect the Gauge: Gauges are sensitive to their environment. Exposure to extreme conditions such as vibrations, temperature changes, and corrosive chemicals can damage the gauge. This damage can lead to faulty readings. Keep the gauge in a location where it’s shielded from such conditions.
Can Adding An Additional Gauge Void My Air Regulator’s Warranty?
When considering adding an extra gauge to your air regulator, it’s crucial to think about how it could affect your warranty. Manufacturers set specific warranty terms. These often exclude coverage for changes made without their approval. An added gauge is a change. If you don’t follow the manufacturer’s instructions when making this change, you could lose your warranty.
Check your warranty documents or get in touch with the manufacturer. This way, you’ll know what you can and can’t do. Some warranties clearly say no to any modifications. In these cases, adding a gauge, or any other change, could cancel your warranty. Even a small change can lead to issues. The manufacturer might say the change affects how the air regulator works or its safety. This would mean breaking the warranty terms.
What Are Common Problems That Might Arise After Adding An Additional Gauge, And How Can I Fix Them?
For starters, if the pressure reading seems off, double-check the installation and calibration of the gauge. It’s easy to overlook the importance of proper alignment or to miss a step during installation, leading to false readings.
Leaks are another concern. They can occur at any connection point. To tackle this, scrutinize every fitting and connection. Make sure everything is as tight as it should be. Applying thread sealant to each connection can help ensure they are leak-proof.
However, if these steps don’t fix the issue, the gauge or regulator might be damaged or worn out. Inspecting these components for any signs of wear or damage is crucial. In such cases, replacing the defective parts is the only way to restore optimal functionality.
Conclusion
In conclusion, adding an extra gauge to your air regulator can significantly enhance both monitoring and control of your pneumatic system.
If you’re considering this upgrade, ensure you select the appropriate gauge and follow the installation guidelines carefully. For further assistance or more detailed information, consulting FAQs or seeking professional advice is highly recommended.