Can You Run A Air Compressor Without A Regulator
Is it possible to operate an air compressor without a regulator, and if so, under what conditions?
This article delves into the implications of using an air compressor at full throttle, the associated risks, and situations where it may not be as hazardous as it seems.
Can You Run A Air Compressor Without A Regulator?
Operating an air compressor without a regulator is technically feasible, yet it’s imperative to grasp the associated perils and constraints. Skipping the regulator, though seemingly uncomplicated, can usher in operational dilemmas and safety risks.
Firstly, devoid of a regulator, the air compressor’s full output is unleashed upon your tools and equipment. This scenario is fraught with problems, especially for air tools that are engineered for specific pressure thresholds. Subjecting these tools to excessive pressure can inflict damage, diminish their operational lifespan, or trigger malfunctions. Such outcomes not only compromise the quality of your work but also pose significant safety threats.
Moreover, the absence of a regulator places an undue burden on the air compressor to sustain steady pressure. This extra exertion strains the system, potentially accelerating wear and tear. The ramifications of this include more frequent equipment failures or heightened maintenance demands. The repercussions of such a scenario extend beyond mere inconvenience; they entail additional financial outlays and interruptions to your work processes.
Another aspect to consider is the impact on operational efficiency. A regulator allows for the fine-tuning of pressure according to the specific needs of a task, thereby optimizing tool performance and conserving energy. Without the capacity to adjust pressure, the compressor may consume more electricity than necessary. This inefficiency not only inflates energy expenses but also contributes to a larger environmental footprint.

What Is The Purpose Of The Regulator On An Air Compressor?
The regulator on an air compressor is integral to its operation, primarily tasked with modulating the air pressure output to levels that are both safe and functional for various pneumatic tools. The absence of such a regulator could lead to the application of excessively high pressure on these tools, which mightn’t only damage the tools but also pose significant safety hazards. Air compressors typically store air at high pressures, often exceeding 100 PSI, while the operational requirements for most pneumatic tools hover around 40 PSI. The regulator, therefore, becomes crucial in bridging this gap.
This device is fundamental in ensuring a steady flow of air. In the realm of pneumatic tools, the demand for air can vary drastically depending on the specific tool being used and the nature of the task at hand. The regulator plays a pivotal role in stabilizing the air pressure that’s delivered to the tool, regardless of these fluctuations. Achieving a constant pressure is essential for tasks that demand precision, such as painting or nailing. The regulator ensures that these tasks can be performed with the required accuracy, thereby enhancing the quality of the work.
Moreover, the regulator offers a level of adaptability by allowing the user to adjust the air pressure according to the needs of different tools. This adjustment is often as simple as turning a knob, which means that the user can easily switch between tools and tasks without needing to make any modifications to the compressor itself. This convenience significantly improves the efficiency of work while also maintaining safety standards.
In essence, the regulator serves as a critical intermediary between the compressor’s high-pressure reservoir and the specific demands of various pneumatic tools. It’s a key component that guarantees the optimal performance of these tools by precisely adjusting the air pressure. In doing so, it not only protects the tools from potential damage due to overpressure but also ensures the safety of the user. The regulator thus stands out as an indispensable element in the effective and safe operation of air compressors and pneumatic tools.
Benefits Of Using A Regulator In Air Compressor
Using a regulator with your air compressor brings several key benefits, primarily focusing on tool performance, energy efficiency, and safety.
The primary function of a regulator is to manage the air pressure reaching your tools. This capability is crucial for both the longevity and efficacy of the tools. By allowing precise control over the pressure, a regulator ensures that each tool operates within its optimal range. This precision is especially important for tasks requiring a delicate touch, as too much pressure can cause damage. Thus, a regulator not only protects your tools from wear but also helps in achieving better results in your work.
On the energy efficiency front, a regulator plays a significant role in reducing the operational costs associated with running an air compressor. By enabling precise adjustments to the air pressure, the compressor doesn’t have to exert unnecessary effort. This tailored approach means the compressor uses only as much power as needed for the specific task, which translates into lower energy consumption. Over time, this efficiency can lead to considerable savings on energy bills, making it an economically and environmentally sound investment.
Safety is another critical area where a regulator proves its worth. Working with compressed air carries inherent risks, including the potential for sudden pressure surges that can pose hazards to both the operator and the machinery. A regulator mitigates these risks by ensuring a stable and controlled flow of air at the set pressure level. This stability is crucial for preventing accidents and maintaining a safe working environment. By effectively managing the pressure, a regulator helps to safeguard against the dangers associated with compressed air, contributing to a safer and more secure workplace.

What Happend When You Run A Air Compressor Without A Regulator
Over-Pressure
Operating an air compressor without the inclusion of a regulator introduces a significant hazard known as over-pressure. This condition arises when the air pressure within the compressor exceeds the design limits of the system and its components. The absence of a regulator, a crucial control device, means there’s no way to manage or limit the pressure that accumulates inside the compressor. Consequently, this unchecked pressure increase can surpass the maximum pressure rating specified by the equipment’s manufacturer, leading to possible system failure.
The ramifications of such over-pressure scenarios are multifaceted. Firstly, the structural components of the air compressor system, including hoses, fittings, and any attached tools, are at a heightened risk of catastrophic failure. These parts, designed to withstand specific pressures, may rupture or shatter if subjected to forces beyond their capacity. Such failures not only entail costly repairs or replacements but also pose a grave safety hazard to individuals in the vicinity, potentially causing severe injuries.
Moreover, the air compressor’s motor is another victim of over-pressure conditions. This motor, tasked with compressing air to the desired levels, faces undue stress when required to operate without a regulating mechanism. The strain of generating higher-than-intended pressures can accelerate wear and tear on the motor, diminishing its operational lifespan. This not only leads to increased maintenance requirements but also raises the potential for sudden motor failure, which could interrupt critical processes or operations relying on the air compressor.
Lack Of Control
Operating an air compressor without a regulator presents significant challenges in managing its output pressure. This situation often leads to performance that isn’t only unpredictable but can also be dangerous. The regulator is a vital tool for those seeking to use an air compressor safely and efficiently. Without it, users are forced to rely on the compressor’s factory settings, which may not suit their specific needs or the demands of the tools they’re employing.
The primary consequence of this lack of control is the potential for tools to receive too much power. This excess can lead to inefficiency in their operation, where tools don’t perform as expected or as needed. Beyond inefficiency, there’s a real risk of damage to materials being worked on. Delicate materials, in particular, can suffer from the application of too much pressure, ruining projects and leading to costly mistakes.
Another critical issue stemming from operating without a regulator is the inability to maintain consistent quality in one’s work. The fluctuating pressure that results from a lack of regulation makes it exceedingly difficult to achieve the necessary precision for tasks that require careful, steady application of power. This inconsistency can be particularly problematic for projects that demand a high level of detail and accuracy.
Safety Concerns
Operating an air compressor without a regulator significantly elevates the likelihood of mishaps and injuries. Essentially, a regulator’s role is to maintain the air pressure at a safe and consistent level. Its absence means there’s no mechanism in place to control the air’s force, leading to unpredictable, and often dangerous, outcomes.
When an air compressor releases air without regulated control, the consequences can be severe. Tools and hoses connected to the compressor may be subjected to sudden bursts of high pressure. Such force can turn them into dangerous projectiles, threatening the safety of anyone in the vicinity.
Moreover, the risk extends to the equipment itself. The excessive pressure can lead to the premature failure of hoses and connections. These blowouts not only pose immediate physical dangers but also contribute to the overall unsafe environment.
Tool And Equipment Damage
Operating an air compressor without a regulator isn’t merely a safety hazard but also significantly damages tools and equipment. The essence of this damage stems from the tools’ exposure to unregulated, high-pressure air. This condition subjects them to pressures beyond their designed operational thresholds.
Pneumatic tools are specifically engineered to function optimally within a predetermined pressure range. When subjected to higher pressures than they’re designed for, the consequences extend beyond mere performance degradation. This scenario propels the tools towards accelerated wear and tear, substantially reducing their operational lifespan.
The mechanics of pressure-induced damage are multifaceted. For instance, excessive pressure can cause seals within the tools to rupture. Similarly, the undue strain can lead to the failure of internal components. These failures aren’t trivial; they necessitate either expensive repairs or complete replacements of the tools in question.
It’s crucial to recognize that the impact of using an air compressor without a regulator on tools and equipment isn’t limited to immediate breakdowns. The sustained exposure to inappropriate pressure levels systematically diminishes the tools’ durability over time. This gradual degradation transforms what should have been a durable asset into a recurrent financial burden.
Operational Inefficiency
Neglecting to use a regulator with an air compressor results in a notable decline in the operational efficiency of pneumatic tools. The absence of a regulator means there’s no mechanism in place to adjust the air pressure to the optimal level required by each specific tool for its best performance. This scenario can lead to two possible outcomes: either the air pressure is too high or too low for the task, which isn’t ideal.
When the air pressure is more than what’s needed, it results in wastage of compressed air, increasing operational costs unnecessarily. On the other hand, if the air pressure is too low, the tool may not have enough power to perform the task effectively. This imbalance in air pressure can cause the tools to operate below their capacity, making tasks more difficult and time-consuming than they should be.
Moreover, the inconsistency in air pressure doesn’t just affect the efficiency of the tools; it also impacts their behavior. Tools might start acting unpredictably, which could pose safety risks in addition to further reducing work efficiency. This erratic behavior can lead to uneven work quality, requiring additional time to rectify mistakes or redo work, thus compounding the inefficiency.

Situations Where A Regulator Might Not Be Necessary
You might wonder if there are times when you can safely run your air compressor without a regulator. In scenarios like direct use cases or when you’re doing testing or have temporary setups, going regulator-free can actually function.
Let’s investigate these situations to understand when it’s okay and when it’s not.
Direct Use Cases
In certain scenarios, opting to use an air compressor devoid of a regulator is considered appropriate and meets the requirements efficiently. This decision largely hinges on the type of pneumatic tools being utilized and their specific air pressure needs. For instance, when the task at hand doesn’t demand a precise air pressure setting, foregoing the regulator can lead to a more streamlined operation. This is particularly relevant for tasks such as tire inflation or utilizing blow guns for cleaning purposes. The absence of a need for meticulous pressure control in these activities allows for a simpler setup.
Moreover, there exists a variety of air-driven equipment that’s purposely designed to function optimally at the compressor’s maximum output pressure. This design eliminates the necessity for a pressure regulator. Tools falling under this category are typically engineered with the capability to endure high-pressure levels, thereby ensuring they can be operated safely without the intervention of a regulator. This aspect is crucial for ensuring both the efficiency and safety of operations involving such equipment.
Testing Or Temporary Setups
In some cases, particularly during temporary or testing scenarios, it mightn’t be necessary to use an air compressor regulator. This decision largely depends on the nature of the experiment or diagnostic test being conducted. For short-term applications, where the goal is to observe the compressor’s raw performance, not using a regulator can be beneficial. This approach allows for a clearer understanding of how the compressor functions under various conditions, without the influence of regulated pressure.
Alternatives To A Regulator
Considering alternatives to a conventional air compressor regulator, a manually adjustable pressure relief valve emerges as a vital choice. This type of valve empowers users to directly set the upper pressure limit. This manual intervention ensures the air compressor system remains within the bounds of safety. It’s a direct, uncomplicated approach, particularly suited for environments where maintaining a constant pressure isn’t paramount, yet ensuring operational safety is.
In addition to the manually adjustable valve, integrating a fixed pressure relief valve alongside a manual shutoff valve presents another feasible solution. This combination allows for the cessation of airflow when the compressor is idle, thus mitigating unnecessary strain on the device. The fixed pressure relief valve acts as a safeguard, preventing the system from surpassing a predetermined pressure threshold. While this configuration lacks the precise control afforded by a traditional regulator, it offers a straightforward, efficient method for pressure management in applications with less stringent requirements.
Flow control valves constitute another alternative, especially in situations where the focus shifts from maintaining specific pressure levels to controlling the airflow rate. Through modulation of the airflow, these valves indirectly influence the system’s pressure. This technique demands a deeper understanding of both the tools in use and the specific application requirements but, when applied correctly, provides a balanced solution that prioritizes both performance and safety.
Ultimately, regardless of the alternative chosen, the significance of regular maintenance can’t be understated. Consistent upkeep is essential for ensuring the safety of the air compressor system and for prolonging the service life of both the compressor and the connected tools. Opting for a non-traditional pressure management solution doesn’t diminish the need for diligent maintenance practices.
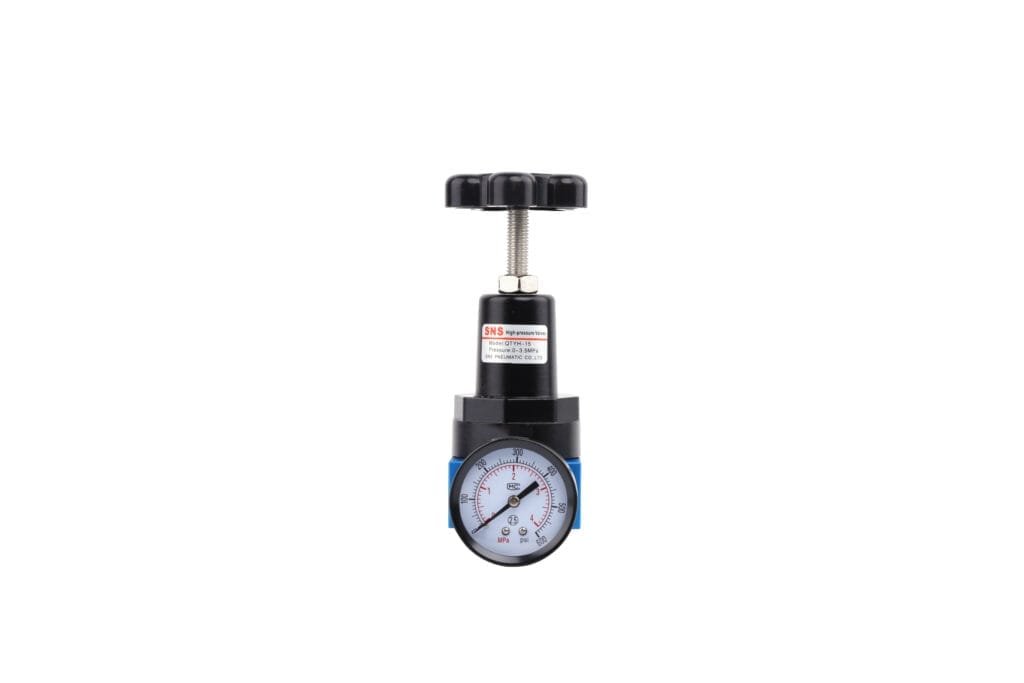
Faqs
Do I Need An Air Pressure Regulator?
To ascertain the necessity of an air pressure regulator, one must delve into the operational requirements of their pneumatic tools and the specific tasks they undertake. Tools that operate optimally at a consistent, predefined pressure are prime candidates for the utilization of a regulator. The purpose of a regulator extends beyond merely maintaining an optimal pressure range; it plays a critical role in safeguarding the tools from potential damage attributed to excessive pressure. The absence of a regulator exposes the equipment to risks, potentially compromising their durability and overall performance.
Moreover, the implementation of a regulator can significantly enhance the efficiency of an air compressor. By ensuring that the compressor generates only the required pressure for a given task, the system operates more efficiently. This efficiency isn’t limited to operational performance but also encompasses energy consumption. The precise control over pressure output translates into energy savings, as the compressor isn’t overburdened by producing unnecessary pressure. Consequently, this not only conserves energy but also mitigates wear and tear on the compressor, thereby extending its service life.
In essence, the adoption of a regulator isn’t merely advantageous but pivotal for tasks demanding precision. It ensures that pneumatic tools operate within their optimal pressure range, thereby maximizing their efficacy and longevity. Furthermore, it contributes to the sustainable operation of air compressors by optimizing their energy consumption and minimizing wear. Given these multifaceted benefits, the investment in a pressure regulator is deemed indispensable for maintaining the integrity and performance of pneumatic systems.
Do I Need A Filter And Regulator On My Air Compressor?
A filter plays a crucial role in the functionality of an air compressor. It’s designed to eliminate various types of contaminants, including dust particles, moisture, and oil vapors, from the compressed air. These contaminants, if not removed, can cause significant harm to the air-powered tools and equipment. The presence of dust and oil in the compressed air can lead to the deterioration of internal components, while moisture can cause rust and corrosion. Therefore, the filter ensures that the air delivered for operations is clean and dry, safeguarding the tools and enhancing their performance and longevity.
On the other hand, a regulator is indispensable for managing the air pressure outputted by the compressor. Different tools and applications demand specific air pressures to operate effectively and safely. A regulator allows the user to precisely adjust the air pressure to the optimal level required by each tool. Without a regulator, there’s a risk of subjecting tools to excessively high pressures, which can cause rapid wear or even catastrophic failure. Conversely, a pressure that’s too low may result in inadequate tool performance, failing to achieve the desired results in operations.
Can I Run An Air Compressor Continuously?
Continuous operation of an air compressor is a complex issue that involves several critical considerations, directly affecting the machine’s functionality, efficiency, and lifespan. Each air compressor comes with its own set of specifications and limitations, and it’s crucial to understand that not every model is engineered to withstand uninterrupted use. The implications of persistently running an air compressor span across various aspects, from operational efficiency to maintenance requirements, and ultimately, its overall durability.
One of the most immediate concerns with non-stop operation is the risk of overheating. The motor and other internal components of an air compressor generate heat during operation. Without adequate intervals of rest to allow for cooling, the temperature within the system can escalate, potentially causing the motor to overheat. This not only reduces efficiency but can also lead to significant damage or even complete failure of the compressor.
Moreover, the continuous use of an air compressor accelerates the wear and tear on its components. Every machine has its limits, and pushing an air compressor to operate beyond its intended capacity can strain the system. This heightened level of wear can result in more frequent breakdowns and necessitates earlier replacement of parts than would otherwise be necessary, increasing maintenance costs and downtime.
Understanding the duty cycle of your air compressor is paramount. The duty cycle, typically expressed as a percentage, represents the duration the compressor can operate within a specific timeframe without sustaining damage. It serves as a guideline for managing the operational schedule of the compressor to avoid overstressing the system. Ignoring the duty cycle can lead to premature wear and the risk of overheating, emphasizing the need for selecting a compressor with a duty cycle that aligns with your usage requirements if continuous operation is anticipated.
For those whose applications demand extensive use, selecting a compressor designed to handle continuous operation is essential. These models are specifically engineered to manage the challenges of prolonged use, including better cooling systems and more durable components, thereby mitigating the risks associated with non-stop operation.
Furthermore, the importance of regular maintenance can’t be overstated, especially for compressors under constant use. Vigilant monitoring of the compressor’s temperature, ensuring proper lubrication, and maintaining clean air quality are critical to preserving the system’s condition and performance. Regular maintenance checks help identify and address potential issues before they escalate, thereby extending the lifespan of the compressor and ensuring reliable operation.
Conclusion
Running an air compressor without a regulator is technically possible but not advisable due to safety and efficiency concerns.
Consider the importance of air pressure management for your tools and equipment.
Explore alternatives and consult with experts to ensure you make the safest and most informed decision.