Complete Guide: How to Use and Choose an Air Pressure Regulator
How to Use an Air Pressure Regulator
Effectively using an air pressure regulator is crucial for ensuring the optimal performance of pneumatic tools. Start by turning on the air compressor and allowing it to fill the tank completely. This step ensures that the pressure gauge readings are accurate. Once the compressor is ready, connect your pneumatic tool to the air hose, and then attach it to the compressor.
Next, locate the regulator knob, which is usually found on the right side of the regulator. To increase pressure, turn the knob clockwise; to decrease pressure, turn it counterclockwise. You should see an immediate change in the readings on the pressure gauge. Be sure to lock the knob in place once you reach your desired pressure setting to prevent accidental adjustments during use.
How Does an Air Pressure Regulator Work?
An air pressure regulator operates by controlling airflow from a supply source (like an air compressor) to maintain a desired outlet pressure. When compressed air enters through the inlet port, it acts against a diaphragm or piston connected to a spring mechanism inside the regulator.
As outlet pressure builds up, it pushes against this diaphragm until it reaches a predetermined level set by adjusting the control knob. If outlet pressure exceeds this level, the diaphragm moves to close off airflow until equilibrium is restored. This automatic adjustment ensures that downstream equipment receives consistent air pressure regardless of fluctuations in supply conditions. This way, you can confidently use various pneumatic tools without worrying about how unstable air sources might affect work quality.
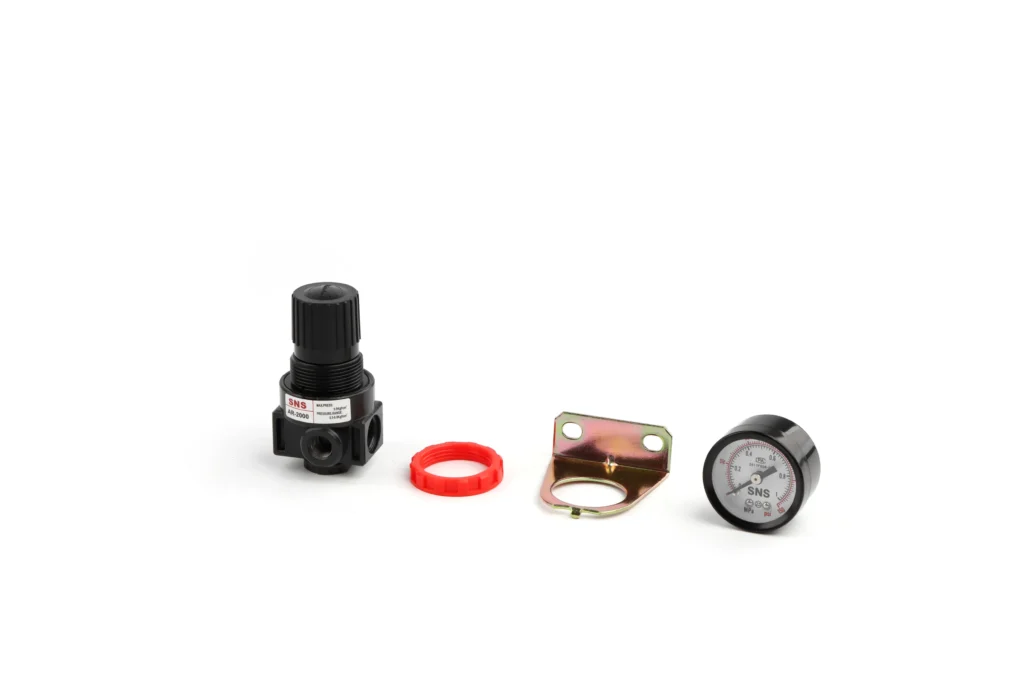
Function of the Air Regulator
The primary function of an air pressure regulator is to reduce and stabilize inlet air pressure to a lower, consistent outlet pressure. This is essential for protecting pneumatic tools from damage caused by excessive pressure, which can lead to accelerated wear or failure. Regulators maintain this outlet pressure even when there are fluctuations in supply, ensuring that tools operate efficiently and safely.
Air regulators are commonly used in various applications, including:
- Pneumatic automation systems: To regulate compressed air.
- Medical equipment: For controlling oxygen and anesthesia gases.
- Gas grills: To manage propane flow.
- Industrial machinery: To ensure consistent operation under varying conditions.
How to Choose the Right Air Pressure Regulator
Selecting the right air pressure regulator involves considering several key factors:
1.Pressure Range: Identify the minimum and maximum pressures required by your tools. The regulator should adequately cover this range. For instance, if your tools require a maximum of 60 psi, choose a regulator that includes this value.
2.Flow Rate: Determine the total flow rate needed for your tools (measured in cubic feet per minute or CFM). Ensure that the regulator can handle this flow without causing significant drops in performance.
3.Type of Regulator: There are several types of regulators:
- General-purpose regulators: Suitable for everyday applications.
- Precision regulators: Designed for more sensitive equipment requiring accurate control.
- High-flow regulators: Ideal for applications needing greater airflow.
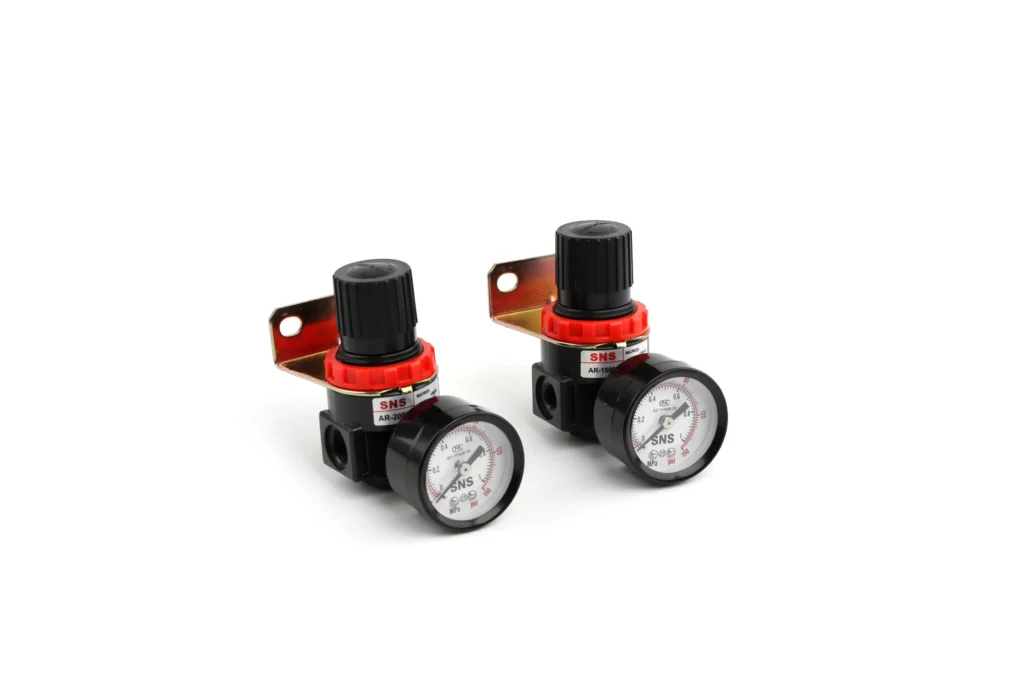
4.Material and Build Quality: Consider materials like brass or aluminum alloys that suit your environment and resist corrosion or wear over time.
5.Additional Features: Look for features such as built-in filters or gauges that can enhance functionality and ease of use. For example, regulators with built-in filters can prevent contaminants from entering your system, thereby extending tool life.
Features of Air Pressure Regulators
Air pressure regulators come equipped with various features that enhance their functionality:
- Relieving vs. Non-relieving Regulators: Relieving regulators vent excess pressure to maintain set levels even in dead-end situations, while non-relieving types do not release trapped air automatically.
- Adjustable Knob: Most regulators include an adjustable knob for easy manual control of output pressure, allowing users to quickly adjust settings as needed.
- Pressure Gauges: Integrated gauges allow users to monitor both inlet and outlet pressures at a glance, helping avoid potential losses due to unnoticed anomalies.
- Diaphragm Mechanism: Many modern regulators utilize a diaphragm system for precise control over outlet pressure, minimizing friction and improving response times. This design ensures stable output even under high load conditions.
These features significantly enhance system performance and safety while providing greater convenience and flexibility for users.
Replacing an Air Pressure Regulator
If you notice issues such as fluctuating pressures or leaks, it may be time to replace your air pressure regulator. Start by turning off your compressor and releasing any residual pressure from the system. Carefully use an adjustable wrench to disconnect the old regulator from its fittings.
When installing a new regulator, apply Teflon tape on threaded connections to ensure a secure fit. Attach it firmly, reconnect any hoses or gauges, and power on your compressor again. After allowing it to fill up, check for leaks before using your tools again.