How do I choose an air regulator?
Choosing the right air regulator is critical for ensuring smooth operation and longevity of pneumatic systems. Air regulators control the pressure of compressed air to ensure it aligns with the specific requirements of tools, machinery, or processes. This guide outlines key considerations for selecting an appropriate air regulator, including factors such as pressure range, flow rate, size, and material compatibility. Accurate selection will enhance performance, efficiency, and safety in applications ranging from industrial manufacturing to automotive repair.
What Factors Need To Be Considered Before Selecting A Air Regulator?
When selecting an air regulator, it is of utmost importance to take into account a variety of factors to ensure optimal performance and compatibility with your system. These considerations include pressure requirements, flow rates, the types of air compressor regulators available, size requirements for the air compressor regulators, operative temperature ranges, the type of media being regulated, exhaust needs, and process sensitivity. Each factor plays a critical role in determining which air regulator will best suit your needs.
Pressure: Understanding the minimum and maximum pressure requirements for your application is essential. The chosen air regulator must be capable of handling these pressures to avoid damage or inefficiency.
Flow: Ensuring the air regulator can accommodate your system’s flow demand ensures efficient operation without overloading or underperforming.
Types of Air Compressor Regulators: Different applications may require different types of regulators such as general-purpose, precision regulators, or those designed for high flow rates. Knowing the distinctions and applications will guide you toward the appropriate choice.
Size of Air Compressor Regulators: The physical size and port size of the regulator should be compatible with your system’s configuration and space constraints. Additionally, correctly sizing affects both performance efficiency and physical integration.
Temperature: The materials used in construction must withstand the minimum and maximum temperatures of their operating environment without degrading.
Media: Compatibility with the media (air or gas) being regulated is vital. Material compatibility ensures longevity and reliability while preventing potential safety hazards.
Exhaust: For applications where downstream pressure relief is necessary, considering how an air regulator handles exhaust becomes important. This ensures that any excess pressure can be safely vented away from sensitive components.
Process Sensitivity: Applications with delicate processes may require regulators with higher accuracy or those that provide more stable control over fluctuations in pressure and flow rates.
Taking time to carefully evaluate each factor relevant to your application significantly contributes to selecting an air regulator that not only meets but exceeds expectations in terms of functionality, safety, and reliability.

Pressure
The pressure requirement is a pivotal parameter that should guide the selection process. It involves considering both the minimum and maximum operating pressures your application demands. An air regulator that cannot sustain the upper limit of required pressure may lead to inadequate performance or even system failure, whereas selecting a regulator rated much higher than necessary can inflate costs without any tangible benefit.
Equally critical is understanding that pressure consistency can significantly affect the efficiency and lifespan of pneumatic tools or processes. An air regulator should offer stability in output pressure even when input pressure fluctuates—a feature vital for applications where precision and reliability are non-negotiable.
Moreover, it’s essential to factor in the desired level of control over the pressure adjustments. Some applications might require fine-tuning capabilities, calling for regulators with precise adjustment controls. In contrast, others might only need a basic setting without much alteration. Selecting an air regulator with an appropriate adjustment range and sensitivity ensures operational efficiency and can dramatically enhance process outcomes.
Flow
The flow rate, usually measured in cubic feet per minute (CFM) or liters per minute (L/min), determines the volume of air that can pass through the regulator over a given period. It’s essential to choose a regulator that can handle the maximum expected flow without creating excessive pressure drop, which could adversely affect the performance of downstream equipment.
Choosing a regulator with an adequate flow capacity ensures that air-operated devices receive a consistent supply at the necessary pressure. Selecting a model with too low of a flow capacity can lead to inefficiencies and potential damage to pneumatic tools and machinery due to insufficient pressure. Conversely, opting for a regulator with too high of a flow capacity might result in unnecessary complexity and higher costs without any tangible benefits.
For applications requiring precise control over airflow, regulators with adjustable settings allow operators to fine-tune the flow rate according to specific demands. This adaptability is particularly valuable in processes where varying operations might require different air volumes.
Types Of Air Compressor Regulators
Air regulators can broadly be categorized based on their design, functionality, and applications.
General Purpose Regulators: General purpose regulators are widely used in various industries for standard operations. They are designed to regulate pressure for typical pneumatic tools and equipment. These regulators offer a balance between performance and affordability, making them a popular choice for many applications.
Precision Regulators: Precision regulators are designed for applications that require highly stable and accurate pressure control. They are often used in sensitive processes where even slight variations in pressure can lead to significant deviations in results or outputs.
High-Flow Regulators: High-flow regulators are tailored to systems requiring a substantial volume flow rate of air. These devices maintain regulated pressure even when there is a high demand for air, ensuring consistent performance in large-scale industrial operations.
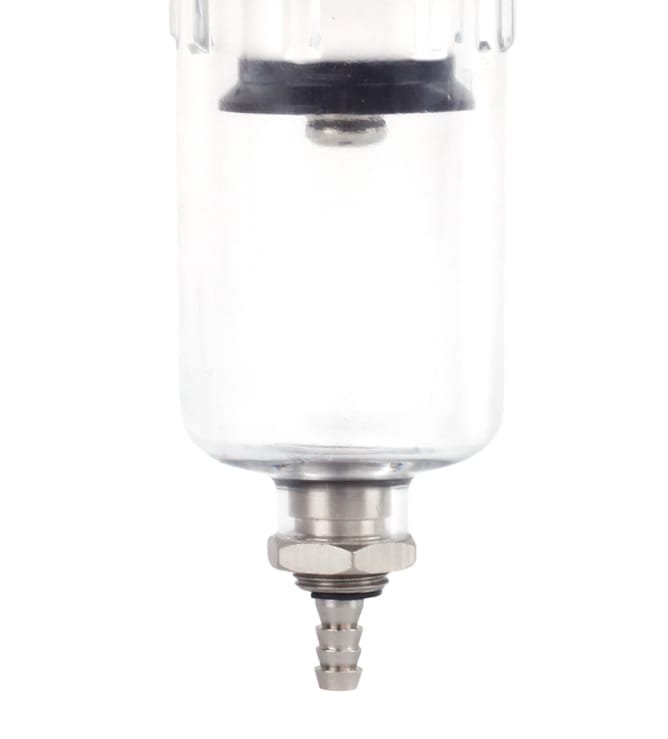
Size Of Air Compressor Regulators
Generally, the principle is to ensure the regulator can handle the system’s highest flow demand without creating excessive pressure drop, which can lead to inefficiencies or equipment damage.
A common misconception is that bigger always means better when choosing a size for air compressor regulators. However, an oversized regulator may not only be more costly but can also result in less stable control of pressure due to its larger internal volume. Conversely, a regulator that is too small can restrict flow severely, causing tools or machinery to operate below their optimum performance levels. Therefore, it’s crucial to strike a balance between operational needs and the physical size of the regulator.
Selecting the optimal size involves assessing your system’s average and peak airflow requirements. Manufacturers typically provide flow curves for their regulators; these charts indicate how much flow you can expect through a regulator at specific pressures, allowing you to match your demand with the product’s capabilities accurately.
Additionally, it’s important to factor in any future expansion plans for your pneumatic system. Opting for a slightly larger regulator than your current demands may allow for growth without requiring immediate replacement as your system evolves or as additional tools and machines are added.
Temperature
Temperature is a vital factor that significantly influences the performance and selection of an air regulator. The operational temperatures, both minimum and maximum, that the air regulator can withstand should be well-understood before making a selection. This pertains not only to the ambient temperature in which the regulator will operate but also to the temperature of the media (air) passing through it.
Regulators are designed with specific materials that have distinct temperature tolerances. These materials can affect the regulator’s durability, functionality, and safety under various temperature conditions. For instance, regulators intended for high-temperature environments might incorporate materials like stainless steel or special polymers that retain their properties under elevated temperatures.
On the contrary, applications involving lower temperatures may require materials that remain flexible and do not become brittle in cold conditions. Selecting an air regulator incompatible with your application’s temperature range can lead to operational failures such as leaks, cracks, or complete breakdowns.
Additionally, consider how temperature fluctuations could impact overall system performance. For example, extreme changes in temperature might cause condensation within the system that could affect air quality or even damage sensitive components downstream. Manufacturers often provide detailed specifications and recommendations to ensure compatibility with your specific application needs centered around operating temperatures.
Media
Media refers to the substance the regulator is designed to control, which in most cases with air regulators, is compressed air. However, specific applications may involve other gases or a mixture of gases where compatibility with the internal components of the regulator becomes paramount. The material composition of seals, diaphragms, and other parts in contact with the media must be resistant to any potential chemical interactions to prevent degradation or failure.
Compatibility issues can lead to leaks, compromised performance, and even safety hazards if not adequately addressed. For instance, certain rubbers and plastics may swell or deteriorate when exposed to oils present in some compressed air systems or specific industrial gases. Therefore, identifying the exact requirements of your application is essential for choosing a regulator that will maintain its integrity and functionality over time.
Moreover, if the media flowing through the air regulator contains particulates or moisture, consider options with integrated filters or separators to prolong the life of both the regulator and downstream equipment. The presence of such contaminants can affect precision and cause wear on sensitive components within the system.
Exhaust
The exhaust capability of an air regulator refers to its ability to quickly release pressurized air back into the atmosphere or a return line once the downstream demand decreases or stops. This aspect is vital for applications where precise pressure control is critical, and the rapid removal of air can prevent potential damage or malfunctioning of pneumatic tools or equipment.
When analyzing exhaust functionalities, it’s essential to assess the regulator’s capacity to handle high volumes of air being exhausted in a short period. Regulators equipped with a quick-exhaust valve are particularly advantageous in scenarios requiring fast depressurization of the system. Additionally, understanding whether the exhaust air needs to be clean or if it carries debris can influence the choice of regulator, as some models come with filters that can capture contaminants before they are expelled into the environment.
Another key component linked to exhaust efficiency is noise reduction. In environments where noise levels are a concern, selecting a regulator that incorporates silencers or mufflers on its exhaust port can significantly mitigate sound emissions.
Lastly, for applications sensitive to environmental contamination or where safety is paramount, such as in food processing or pharmaceutical manufacturing, regulators designed with secondary containment features ensure that any leakage does not escape into the surrounding area but is instead safely contained within the unit.
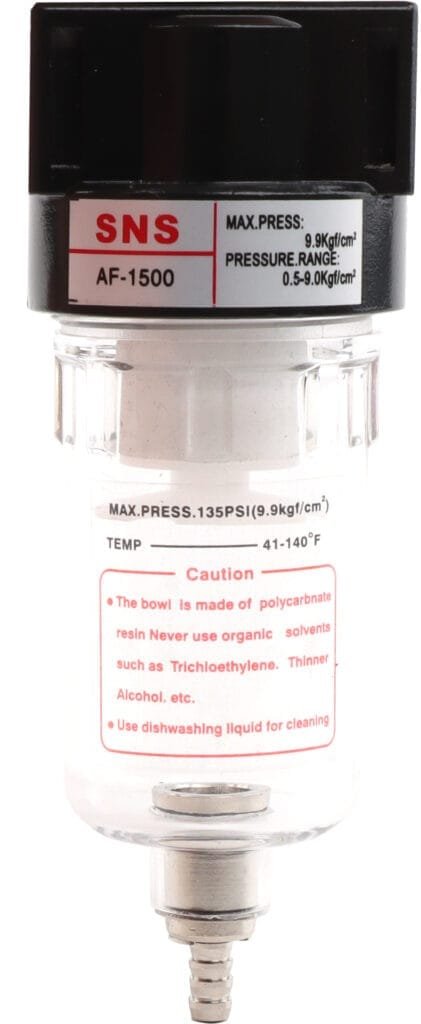
Process Sensitivity
Processes with high sensitivity require regulators that can maintain a very stable output pressure even when input pressure or flow rates vary significantly. Such precision ensures the consistent quality and reliability of the final product or operation.
Process sensitivity impacts not only the choice of regulator type but also necessitates careful consideration of its specifications and features. For applications where minute changes in pressure can have significant effects on performance or outcomes, opting for regulators with finer adjustment capabilities and higher sensitivity is advisable. These might include micro-adjustable regulators or those specifically designed for critical applications where precision is paramount.
It’s also important to assess whether the process involves rapid changes in demand. In these scenarios, a regulator that responds quickly to adjustments and maintains steady pressure despite sudden increases or decreases in flow is essential. The right balance between responsiveness and stability under varying conditions helps in preventing process disruptions and ensures optimal operation.
Moreover, understanding the specific requirements of your process enables you to determine if additional features, such as built-in gauges for real-time monitoring or digital controls for precise adjustments, are necessary. For highly sensitive processes, regulators that offer feedback mechanisms or automated adjustments could greatly enhance performance by actively compensating for any detected deviations from desired pressure levels.
In Conclusion
Choosing the right air regulator requires an understanding of its key features and how they align with your specific needs.
If you’re looking to maximize efficiency and safety in your pneumatic applications, exploring our range could be your next step. Contact us for guidance on selecting the ideal air regulator tailored to your requirements.