How Do Pneumatic Tubes Work
Pneumatic tubes operate by creating a difference in air pressure, propelling carriers through a network of tubes to their destination. This system uses compressed air to move objects efficiently from one point to another.
In the modern era of digital communication, pneumatic tube systems provide an intriguing glimpse into the past and present of physical item transportation. Let’s explore how this seemingly old-fashioned technology plays a crucial role in today’s fast-paced environments like hospitals and banks.
What Is Pneumatic Tubes
Pneumatic tubes are systems designed for transporting objects. They use compressed air or vacuum as a propulsion method. Small canisters, known as carriers, move through a network of tubes. The systems are closed and pressurized.Their primary function is quick transport within a limited area.

How Do Pneumatic Tubes Work
Pneumatic tube systems utilize air pressure for transporting items from one location to another. A simplistic overview conveys a system using air or vacuum to push or pull carriers through tubes. The principle hinges on creating a difference in air pressure.
The process initiates when a user inserts an object into a carrier. This carrier is then placed into a station, where it gets securely sealed and ready for dispatch. Upon sending, the system either sucks or blows air through the tubes. This action propels the carrier towards its destination.
Two types of systems define operation: pressure and vacuum. Pressure systems use compressed air to push the carrier from the sending station to the receiving end. Vacuum systems, conversely, create a suction effect that pulls carriers towards the destination.
Air propulsion units generate necessary force for movement through tubes. These units either increase air pressure behind the carrier or reduce it in front, facilitating movement.
Control over direction and destination is vital. Switching and routing equipment manage these aspects efficiently. They direct carriers at junctions within the network, ensuring accurate delivery to correct destinations.
Each station functions both as sending and receiving points. Users send items by placing them into carriers and entering destination codes on interfaces provided at stations.
Pneumatic tube systems operate cyclically – once a transaction concludes, the system resets to accommodate next sendings or receivings swiftly.
Components Of A Pneumatic Tube System
Pneumatic tube systems consist of several key components: tubes, carriers, air propulsion units, stations, and switching and routing equipment. Each plays a crucial role in the system’s operation.
Tubes
These are the foundational conduits of the pneumatic tube system, providing the pathway for carriers to move. Constructed from durable materials such as steel or plastic, tubes are designed to handle pressure changes and offer a smooth internal surface for efficient carrier travel.
Carriers
Carriers are specially designed containers that transport items through the tube system. They are typically cylindrical, crafted from lightweight yet robust materials, and feature secure closures to protect contents during rapid transit.
Air Propulsion Units
These units are responsible for creating the air flow that propels carriers through the system. They can operate by either pressurizing the system to push carriers forward or generating a vacuum to pull them to their destination.
Stations
Stations are the user interface points of the pneumatic tube system, functioning as both dispatch and receiving areas. Equipped with mechanisms for inserting and retrieving carriers, stations facilitate the system’s interactive component.
Switching and Routing Equipment
This equipment is crucial for directing carriers to their intended destinations within the tube network. Through sophisticated mechanisms, switching and routing devices automatically adjust carrier paths at junctions based on each container’s programmed destination.

Benefits of Pneumatic Tubes
Speed and Efficiency
Pneumatic tubes quickly transport items between various locations, providing a significant efficiency boost, especially critical in time-sensitive environments like hospitals.
Reduced Manual Handling
By automating the transfer process, pneumatic tubes minimize physical strain and potential injuries among employees, contributing to a safer workplace.
Safety of Contents
The closed system design ensures the safe transport of contents, protecting them from external contamination—ideal for sensitive or sterile materials.
Space-saving Design
Utilizing existing spaces within walls and ceilings, pneumatic tubes enable facility layout optimization, distinguishing them from bulkier traditional transportation methods.
Minimal Installation Disruption
Compared to the implementation of large-scale conveyor systems, setting up pneumatic tubes is less intrusive, causing minimal operational disruption.
Lower Operational Costs
Once installed, pneumatic tubes have relatively low maintenance and operational expenses, offering cost efficiency over manual delivery methods.
Reliable Delivery
Operating through a straightforward mechanism, pneumatic tubes ensure dependable delivery with fewer failure points compared to more complex transport machinery.
Versatility
Adaptable to various settings, from retail to healthcare, pneumatic tube systems can be customized to meet the unique requirements and constraints of different industries.
Enhanced Security
By limiting access to transported items to authorized recipients at specific stations, pneumatic tubes bolster the security of transported materials.
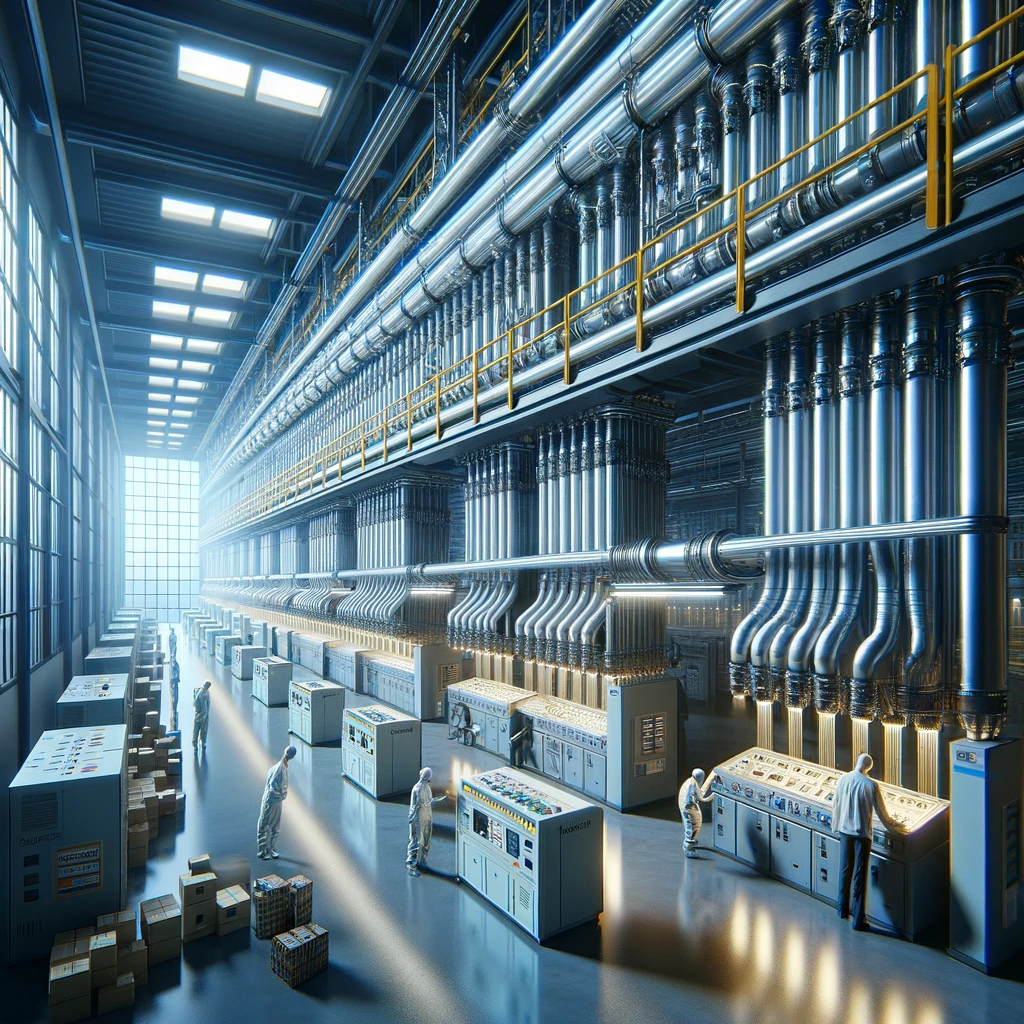
How Do You Use A Pneumatic Tube System?
- Prepare the Item for Transit:
- Place the item to be sent into a cylindrical carrier, ensuring it fits snugly to prevent movement during transit.
- Seal the Carrier:
- Properly seal the carrier to maintain the pressure necessary for movement. Ensure the lid or door clicks or locks in place, indicating a proper seal.
- Insert the Carrier into the Station:
- Place the sealed carrier into a chamber at the station, which serves as the entry point into the pneumatic tube network.
- Select the Destination:
- Use the station’s interface to select the destination. This could involve choosing from pre-programmed locations or manually inputting a code corresponding to the desired destination.
- Confirm the Selection (If Required):
- Confirm your selection according to your system’s interface to proceed with dispatching the carrier.
- Dispatch the Carrier:
- The system uses pressurized air to propel the carrier through the tubes towards its destination. Switching and routing equipment guide the carrier through the network.
- Receipt Notification:
- Upon arrival, the system may signal receipt with a sound or visual cue at the receiving station, indicating an item has arrived.
- Retrieve the Item:
- Open the compartment or drawer at the receiving station to retrieve the sent item. Ensure that only authorized personnel access sensitive or valuable contents.
History Of Pneumatic Tubes
The invention of pneumatic tubes dates back to the 19th century. The concept first materialized in the form of mail dispatch systems.
In 1836, the London Pneumatic Despatch Company pioneered these systems to transport letters across short distances in London. This innovation marked the beginning of pneumatic tube technology’s journey.
By the late 1800s, pneumatic tube systems expanded beyond mail delivery. Major cities in Europe and the United States installed systems for various purposes. Paris, for example, had an extensive network that facilitated communication across the city. These networks operated successfully well into the 20th century.
The functionality of pneumatic tubes evolved with technological advancements. Initially, they relied on manual power for air propulsion. Over time, electric compressors replaced manual efforts, significantly improving efficiency and extending their use cases.
In addition to urban mail delivery, pneumatic tubes found applications in large buildings and industrial settings. Department stores and factories began using these systems for internal communications and transporting small items quickly between different floors or departments.
The advent of digital communication technologies saw a decline in pneumatic tubes for mail delivery. However, specific industries discovered new applications for this old technology. Hospitals became prominent users, employing pneumatic tubes to transport lab samples and medications swiftly across large campuses.
While not as visible as in their heyday, pneumatic tubes remain an integral part of certain sectors today. Their ability to efficiently move small objects over relatively short distances continues to offer unique advantages not easily replicated by other means of transportation or communication.
Applications Of Pneumatic Tubes
Pneumatic tubes serve many fields. Their primary use is in transporting small, lightweight items quickly over short and medium distances. Here’s a deep dive into the diverse applications of pneumatic tube systems:
Banking: Banks use pneumatic tubes at drive-thru tellers to send cash, documents, and receipts between customers and tellers. This system enhances security and efficiency.
Retail: In retail settings, pneumatic tubes transport cash from registers to secure areas. This reduces theft risks and frees employees from manual cash handling tasks.
Healthcare: Hospitals deploy pneumatic tubes to send samples, prescriptions, and documents. Speed is crucial here. It ensures fast delivery of sensitive materials which facilitates better patient care.
Manufacturing: Factories use these systems for moving parts between different sections. It optimizes workflow and maintains cleanliness by minimising human handling.
Administration and Offices: Offices employ pneumatic tubes for sending documents across departments swiftly. This aids in maintaining workflow continuity without electronic interference.
Does Anyone Still Use Pneumatic Tubes?
Yes, pneumatic tubes are still in use today. They’re frequently used in settings such as hospitals to transport small, lightweight items like documents or medications quickly and efficiently.
Why Did Pneumatic Tubes Stop Being Used?
Actually, pneumatic tubes haven’t fully stopped being used. While they’re less common due to technological advancements like email and electronic systems, they still serve important roles in locations like hospitals and banks for quick and efficient transport of small items.
Can Pneumatic Tubes Transport Liquids Or Hazardous Materials?
No, pneumatic tubes are not typically used to transport liquids or hazardous materials. They are designed for light, solid objects like documents or small medical supplies. Using them for liquids or hazardous materials could result in damage or safety risks.
Can Pneumatic Tube Systems Be Used In Residential Settings?
While it’s not common, pneumatic tube systems can be used in residential settings. However, they’re typically seen more in commercial or institutional settings due to the cost and complexity of installation and maintenance.
How Fast Do Carriers Travel In Pneumatic Tubes?
The speed at which carriers travel in pneumatic tubes can vary, but typically, they move at speeds of approximately 25 to 30 feet per second. This allows for quick and efficient transportation over short distances.
In Conclusion
Pneumatic tubes provide an efficient and rapid means of transporting small objects or documents through a network of tubes, using air pressure as the propulsion method.
To discover more about how pneumatic tube systems can streamline operations in various settings, we invite you to explore further. Contact us today to see how these innovative solutions can be implemented into your business or organization.