How Often Should You Replace A Air Regulator?
Understanding the lifespan of your air regulator is crucial for maintaining your system’s performance. Let’s dive into how often it should be replaced and the signs of wear to watch for.
How Often Should You Replace A Air Regulator?
Typically, an air regulator lasts between 5 and 10 years. However, this timeframe can vary based on how frequently and under what conditions it’s used.
For air regulators employed in commercial or industrial settings, you might find the need for replacement edges closer to the 5-year mark due to heavier usage and potentially more challenging environments. On the other hand, air regulators used less intensively, such as in hobbies, could reach or even exceed 10 years of effective service.
The longevity of an air regulator strongly depends on its quality. High-quality regulators tend to last longer and perform better throughout their lifespan. Nevertheless, no regulator is immune to the effects of wear and tear, environmental conditions, or contamination from air system particulates and moisture.
Proactive maintenance and timely replacement are key to avoiding system downtime or damage. Regular checks can help extend your air regulator’s life, but recognizing when to replace it preemptively ensures your air system continues to operate reliably.

How Do I Know If My Air Regulator Is Bad?
You’ll recognize a failing air regulator through a few clear signs. If you’re experiencing inconsistent pressure, spotting physical damage, or hearing noisy operation, it’s time to contemplate a replacement. These symptoms indicate your air regulator’s performance is compromised.
Inconsistent Pressure
When you observe inconsistent pressure, it’s a strong indicator that your air regulator might require some attention. This situation often arises when there are fluctuations in pressure that cannot be attributed to any changes in settings or operational demands.
Such irregularities can cause tools or machinery to work less efficiently and may even lead to damage over time. It’s crucial to investigate if these inconsistencies continue even after you’ve attempted basic troubleshooting methods. This can include checking for any leaks or trying to adjust the regulator to rectify the issue.
Persistent problems usually mean that the internal components of the regulator are either worn out or broken.
Physical Damage
Visible cracks, dents, or corrosion signs on the regulator’s body or its fittings are immediate red flags. Such damage can cause leaks, diminishing your air system’s efficiency and potentially leading to safety hazards.
Noisy Operation
Unusual noises during the operation of your air regulator, such as hissing, whistling, or banging, are clear signs that you should inspect the device. These sounds can point to various problems, including internal damage, seal leaks, or misalignment.
How Do Air Regulators Fail?
Air regulators are essential for controlling air pressure in various applications, but they are not invulnerable to failure. A common reason for their malfunction is wear and tear. Over time, essential parts like springs and diaphragms can wear down. This deterioration affects the regulator’s ability to maintain consistent pressure, potentially leading to total failure.
Contaminants such as dust, dirt, and moisture pose another threat. They can sneak into the regulator if the air intake isn’t properly filtered. Once inside, these particles can clog or even corrode internal components. This makes it challenging for the regulator to keep pressure levels in check. Environments with high moisture or dust levels particularly demand more frequent inspections and maintenance to prevent such issues.
Misuse of air regulators also contributes to their failure. Stressing the regulator by operating it beyond its rated pressure range can damage internal components. Additionally, neglecting routine maintenance tasks, like cleaning or replacing filters, compromises the regulator’s functionality. Adhering to the manufacturer’s guidelines for operation and maintenance is crucial for extending the life of the device.
Accidents can instantly damage or gradually weaken an air regulator. Dropping or striking the regulator might not always cause immediate failure, but it can impair its structural integrity, leading to problems over time. Despite their sturdy design, air regulators cannot endure significant physical impacts without consequence.
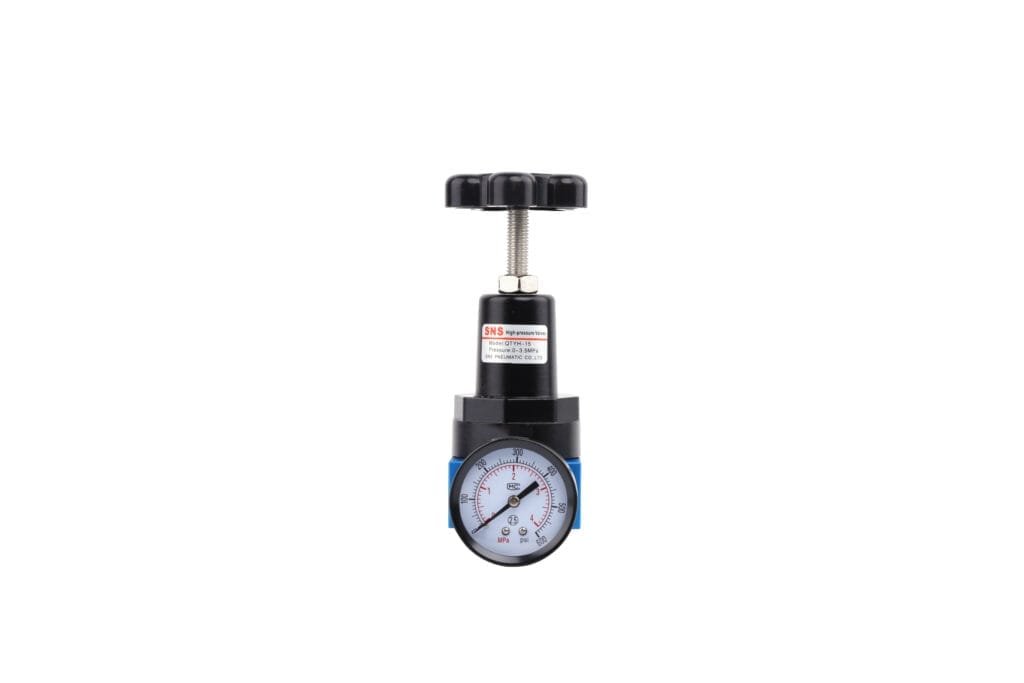
Factors Affecting Air Regulator Lifespan
Understanding the factors that influence the lifespan of your air regulator is key to ensuring its longevity. The frequency of use and the environmental conditions it’s exposed to play critical roles. You’ll need to monitor these aspects closely to maintain peak performance and timely replacement.
Usage Frequency
The frequency with which you use your air regulator plays a crucial role in determining its longevity. Regular, intense usage, especially in commercial or industrial environments, tends to wear it down more quickly compared to occasional use in less demanding settings, like a hobbyist’s workshop.
Each time you use the air regulator, particularly for tasks that require a lot of power, it puts stress on its internal components. This doesn’t just relate to the number of hours it’s in operation but also to the intensity of its workload during those hours. Consequently, air regulators deployed in settings where they are constantly in action are likely to need replacement sooner than those used less frequently.
Environmental Conditions
The environment in which your air regulator functions significantly influences its durability. Factors such as extreme temperatures, high humidity, and the presence of corrosive gases can drastically reduce its lifespan.
In areas filled with dust, chemicals, or other pollutants, air regulators face additional challenges. These contaminants can obstruct, erode, or damage the regulator’s internal parts, leading to diminished efficiency or outright failure.
How To Replace A Air Regulator?
Before starting, ensure the air supply to the regulator is turned off to avoid accidents. Wear the right protective gear for safety.
Begin by loosening the fittings that connect the old regulator to both the air supply line and the tool or hose. You might need to apply some strength or use a wrench if they’re tight. After loosening, carefully detach the regulator.
Check the fittings and hoses for wear or damage. Replace or repair any defective parts to ensure the new regulator functions properly.
To install the new regulator, first apply Teflon tape or a similar thread sealant to its threads to prevent leaks. Align it with the air supply line and the tool or hose. Hand-tighten the fittings to attach it, then use a wrench to secure them firmly. Avoid over-tightening to prevent thread damage.

How To Maintenance And Care?
To ensure your air regulator remains efficient and lasts longer, it’s crucial to conduct regular inspections for any signs of wear or damage. Check for any cracks, leaks, or visible damage that could affect its performance. Addressing these issues quickly can prevent further complications.
Keeping the air regulator clean is essential. Over time, dust and debris can build up, potentially clogging the system and reducing its functionality. Use a soft, dry cloth to gently clean the exterior. For the interior, follow the manufacturer’s cleaning recommendations to avoid damage.
Lubrication plays a vital role in maintaining your air regulator. It helps prevent rust and corrosion, ensuring the regulator operates smoothly. Be sure to use the specific lubricant recommended by the manufacturer to avoid any malfunctions or damage to the regulator’s components.
Faqs
What Causes Air Regulator To Leak?
Identifying the reasons behind a leaking air regulator involves looking at several common issues. One major cause is the wear and tear experienced by internal components, such as O-rings and seals. These essential parts can deteriorate over time due to factors including exposure to air, fluctuations in pressure, and the presence of particulates within the air system.
Another factor contributing to leaks is incorrect installation or the overtightening of components. This mistake can lead to damaged parts, which compromises the integrity of the air regulator, resulting in leaks.
Moisture in the air system can also cause corrosion, weakening the regulator’s body or its fittings. This deterioration can eventually lead to failure, underlining the importance of keeping the system dry and well-maintained.
How Do You Test An Air Pressure Regulator?
Testing an air pressure regulator effectively ensures it operates at its best and lasts longer. Begin by securing a reliable pressure gauge to the regulator’s downstream side. It’s essential to halt any air flow through the system as you start this process.
Increase the air supply gradually while keeping an eye on the gauge. You should observe the pressure rising steadily until it reaches the predetermined set point, where it should remain stable. A significant overshoot or wide fluctuations in pressure could signal a problem with the regulator’s internal components.
Be alert for any unusual sounds during the test. These noises might indicate internal damage or leaks that need addressing. Once the test concludes, ensure the system is fully depressurized before removing the gauge. This methodical approach helps identify issues early, helping avoid unexpected operational interruptions.
What Are The Risks Of Not Replacing My Air Regulator On Time?
Failing to replace your air regulator on schedule can lead to several operational and safety issues. When an air regulator isn’t functioning correctly, it can result in unpredictable air flow. This variability forces machinery to work harder than necessary, leading to inefficiency. Such inefficiencies not only ramp up energy costs but also place extra strain on your equipment. Over time, this can reduce the lifespan of your machinery, leading to premature replacements.
Moreover, an outdated or faulty air regulator raises significant safety concerns. It could lead to dangerous leaks or even explosions, putting the safety of workers at risk. This scenario underscores the importance of timely maintenance and replacements.
Ignoring the need for a timely air regulator replacement doesn’t just affect machinery performance. It directly impacts workplace safety and can lead to considerable financial setbacks. These setbacks come from the costs associated with repairs, buying new equipment, and the downtime required to address these issues. To avoid these problems, it’s crucial to follow the recommended replacement schedules for your air regulator.

Can Regular Maintenance Extend The Lifespan Of My Air Regulator?
Proper maintenance significantly enhances the performance and longevity of your air regulator. By engaging in regular checks, you actively prevent sudden malfunctions and maintain the equipment’s quality. It’s critical to adhere to the manufacturer’s maintenance recommendations to ensure both efficient operation and safety.
Regular cleaning and inspection are essential. During these checks, be vigilant for any signs of deterioration, such as cracks or leaks, and rectify these issues promptly. Swiftly addressing these signs can avert more serious problems in the future.
Another key aspect of maintenance is the replacement of worn-out components. This proactive step can forestall more complex and costly repairs later on. A well-maintained air regulator not only operates more effectively but also poses fewer safety risks.
Maintaining your air regulator diligently is crucial for optimizing its performance and safety. This routine care is instrumental in extending the lifespan of your equipment.
Conclusion
In conclusion, the need to replace an air regulator is determined by its performance and condition, not merely its age.
Ensure your air regulator is functioning optimally by regularly assessing its condition and performance. If you encounter any issues, don’t hesitate to replace it to maintain efficiency and safety in your operations.