How to Size a Pneumatic Cylinder
Do you need to size a pneumatic cylinder for your application? Correctly sizing a pneumatic cylinder is crucial for optimal performance and efficiency.
In this blog post, we’ll guide you through the process of sizing a pneumatic cylinder step by step. We’ll cover the key factors to consider and provide a simple method to ensure you select the right cylinder for your specific requirements.
Factors to Consider When Sizing a Pneumatic Cylinder
Load Requirements
Pneumatic cylinders must be sized to handle the required load. The force output of a cylinder depends on its bore size, operating pressure, and whether it is single-acting or double-acting.
Larger bore sizes and higher pressures increase the force output. Double-acting cylinders provide force in both directions, while single-acting cylinders only provide force in one direction.
Speed Requirements
The speed of a pneumatic cylinder is determined by the air flow rate and the size of the cylinder ports. Larger ports and higher flow rates result in faster speeds.
However, excessive speed can cause mechanical damage and shock loads. Proper sizing and cushioning can help control the speed and prevent damage.
Stroke Length
The stroke length is the distance the piston travels from one end of the cylinder to the other. Longer strokes require more air volume and can affect the speed and force output of the cylinder.
The stroke length should be sufficient to achieve the desired range of motion without exceeding the available space or causing interference with other components.
Pressure
The operating pressure of a pneumatic system affects the force output and speed of the cylinders. Higher pressures generally result in greater force and faster speeds.
However, excessive pressure can cause leaks, damage seals, and increase wear on the cylinder components.
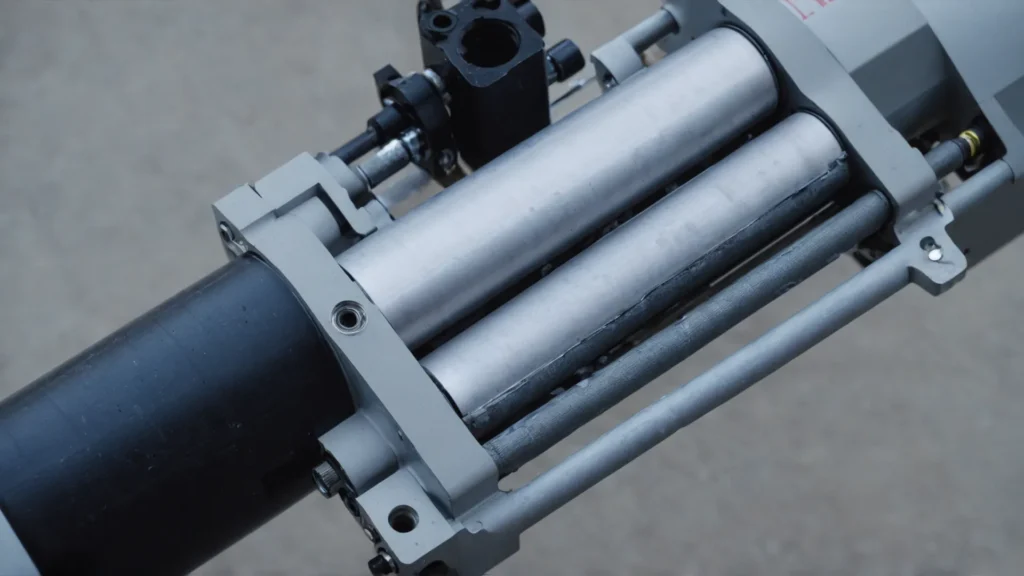
Sizing Calculations
Calculating the required force
The force output of a pneumatic cylinder can be calculated using the formula
F = P * A
where,
- F is the force in pounds (lbs)
- P is the air pressure in pounds per square inch (PSI)
- A is the effective piston area in square inches
For example, if the air pressure is 100 PSI and the bore diameter is 2 inches, the force output would be 314 lbs (100 PSI * π * (2 inches / 2)^2).
Calculating the required bore size
To determine the appropriate bore size for a pneumatic cylinder, use the formula
D = √((4 * F) / (π * P))
where,
- D is the bore diameter in inches
- F is the required force in pounds
- P is the available air pressure in PSI
For instance, if the required force is 500 lbs and the air pressure is 80 PSI, the necessary bore diameter would be approximately 2.82 inches.
Calculating the air consumption
The air consumption of a pneumatic cylinder can be calculated using the formula
V = (π * D^2 * L * N) / (4 * 1728)
where,
- V is the air volume in cubic feet per minute (CFM)
- D is the bore diameter in inches
- L is the stroke length in inches
- N is the number of cycles per minute
As an example, a cylinder with a 3-inch bore, a 6-inch stroke, and operating at 10 cycles per minute would consume 0.32 CFM.
Calculating the rod size
The rod size of a pneumatic cylinder is typically determined based on the bore diameter and the stroke length. A common rule of thumb is to use a rod diameter that is approximately 1/3 to 1/2 of the bore diameter for standard applications.
For instance, a cylinder with a 4-inch bore might have a rod diameter between 1.33 and 2 inches.
Calculating the Cylinder Speed
The speed of a pneumatic cylinder can be estimated using the formula
S = (Q * 28.8) / A
where,
- S is the speed in inches per second (IPS)
- Q is the air flow rate in CFM
- A is the effective piston area in square inches
For example, if the air flow rate is 10 CFM and the effective piston area is 3 square inches, the cylinder speed would be approximately 96 IPS.
Common Mistakes When Sizing a Pneumatic Cylinder
- Not considering the required force and speed
- Ignoring the effects of friction
- Neglecting the impact of air pressure
- Overlooking the importance of stroke length
- Failing to account for load orientation
- Not considering the duty cycle
- Ignoring the effects of temperature
- Not accounting for pressure drops
- Overlooking the need for cushioning
- Not leaving room for future adjustments
FAQs
What is the Bore Size of a Pneumatic Cylinder?
The bore size of a pneumatic cylinder refers to the internal diameter of the cylinder’s body. Larger bore sizes generate greater force output but consume more compressed air. Conversely, smaller bore sizes produce less force but offer more efficient air consumption and compact design.
What Determines the Speed of a Pneumatic Cylinder?
The speed of a pneumatic cylinder is primarily determined by the flow rate of compressed air entering and exiting the cylinder. This flow rate is controlled by the size of the ports and the valve that regulates the air flow.
In Conclusion
Proper sizing of a pneumatic cylinder is crucial for optimal performance and efficiency. By following the steps outlined in this guide, you can select the right cylinder for your application.
If you have any questions or need further assistance, don’t hesitate to reach out to our team of experts.