Hydraulic Vs. Electric Linear Actuator
Are you choosing between hydraulic and electric linear actuators?
Hydraulic actuators offer immense power and load capacity. They are perfect for heavy-duty tasks but require more maintenance.
Electric actuators excel in precision, energy efficiency, and easy integration. They are ideal for tasks needing exact control.
How Hydraulic and Electric Actuators Work
Hydraulic Actuator Operating Principles
Hydraulic actuators generate motion by utilizing fluid dynamics. They convert the energy from pressurized liquids into mechanical force. The system uses an incompressible liquid, typically oil, to transfer fluid and pressure.
When pressurized fluid enters the actuator, it pushes against a piston, creating linear movement. This enables hydraulic actuators to achieve high-power density. They handle substantial loads despite their compact size.
Electric Actuator Operating Principles
Electric actuators convert electrical energy into mechanical motion by utilizing electric motors and precision components. They operate through an electric motor that drives a series of gears or a screw mechanism to create linear displacement. Unlike hydraulic actuators that rely on fluid pressure, electric actuators achieve motion through controlled electric power.
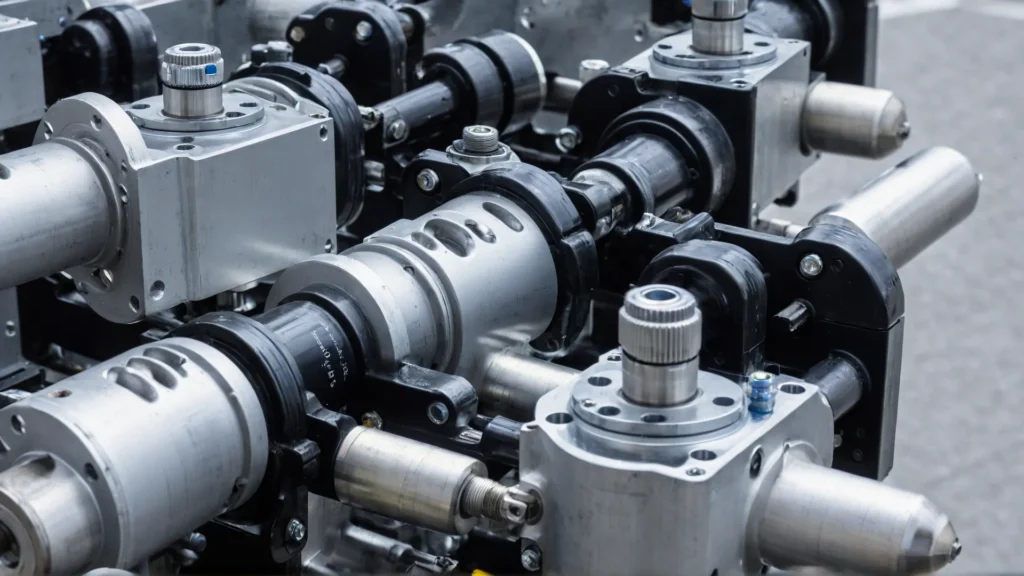
Key Differences Between Hydraulic and Electric Actuators
Force and Power Output
Hydraulic actuators: Deliver immense force through high-pressure fluid. Stand out for their ability to handle high-force applications. Achieve high power density, utilizing pressurized fluid to create significant linear displacement.
Electric actuators: Generate force via current control in the servo motor. Convert torque generated by an electric motor into linear displacement. Generally offer lower force output compared to hydraulics.
Precision and Motion Control
Electric actuators: Electric actuators excel in precision and motion control. They offer unmatched accuracy and repeatability, ensuring precise motion control with minimal error, often within microns. This makes them ideal for applications requiring exact positioning and consistent performance.
Hydraulic actuators: In contrast, hydraulic linear actuators, despite their power, struggle with precise motion control. The compressibility of fluids and the complexity of managing fluid dynamics contribute to this challenge. Hydraulic systems often experience stick-slip phenomena, complicating fine control.
Speed and Acceleration
Electric linear actuators: Electric linear actuators deliver superior speed and acceleration due to their inherent design advantages. They excel in precise motion control, leveraging advanced position, velocity, and acceleration control capabilities. This precision supports rapid and repeatable adjustments, enabling smoother and more controlled motion profiles.
Hydraulic actuators: Hydraulic actuators rely on fluid flow to generate movement, which introduces delays and variability in speed and acceleration. The compressibility of hydraulic fluid and the potential for leaks complicate precise motion control. Although hydraulic actuators can deliver substantial force, their speed and acceleration are often limited by the system’s mechanical complexity and fluid dynamics.
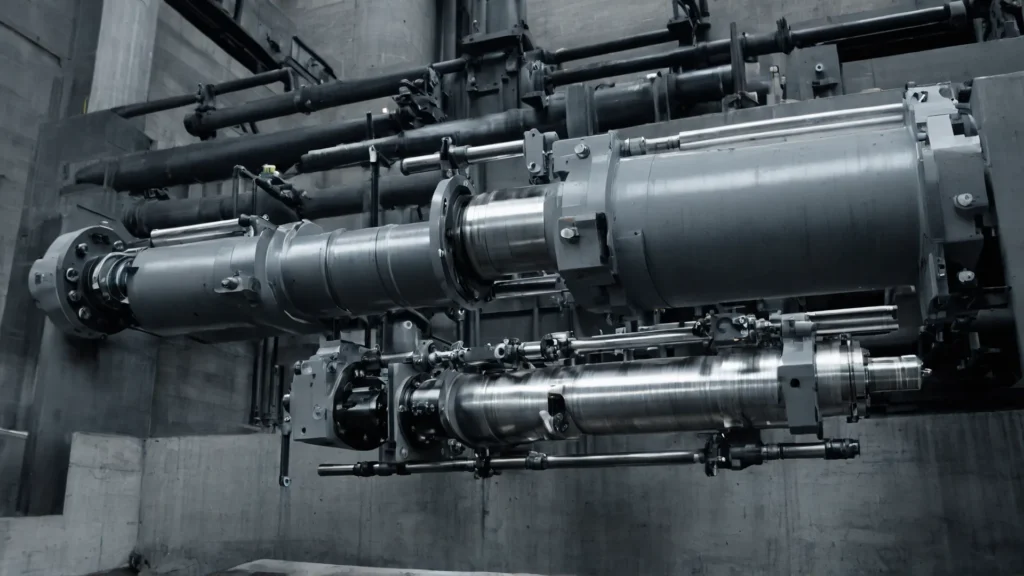
Energy Efficiency
Electric linear actuators convert electrical energy directly into motion, avoiding the inefficiencies of fluid dynamics. This direct conversion achieves higher efficiency, typically operating between 75-80%.
Hydraulic systems generally reach only 40-55% efficiency.
Environmental Impact
Hydraulic actuators: Hydraulic actuators introduce substantial environmental risks due to their propensity for fluid leaks and contamination. During operation, even minor leaks can lead to significant hazards, polluting soil and water sources. This is especially concerning in industries governed by stringent environmental regulations. Contamination often arises from worn-out seals, ruptured hoses, or improper maintenance practices.
Electric actuators: Electric linear actuators present a more environmentally friendly alternative. They do not rely on fluid power, eliminating leak risks entirely. Electric actuators generally feature high-quality seals, which ensure minimal contamination risk. These seals are designed to last the actuator’s lifetime, serving as a reliable barrier against environmental pollutants.
Maintenance Requirements
Hydraulic actuators: Maintaining hydraulic actuators often proves demanding and costly. Hydraulic systems require extensive maintenance tasks to ensure system integrity and performance. Regularly check and replace hydraulic fluid, maintain pressure levels, inspect for leaks, and replace worn seals and hoses. These tasks drive up maintenance requirements and contribute to higher long-term maintenance costs.
Electric actuators: Electric actuators demand much less upkeep. Primarily, check electrical connections and occasionally lubricate moving parts, if necessary. The absence of fluid dramatically reduces the risk of leaks and contamination, simplifying maintenance tasks.
Initial and Operating Costs
Hydraulic actuators: Lower initial cost but higher long-term operating costs.
Electric actuators: Higher initial cost but lower long-term operating costs.
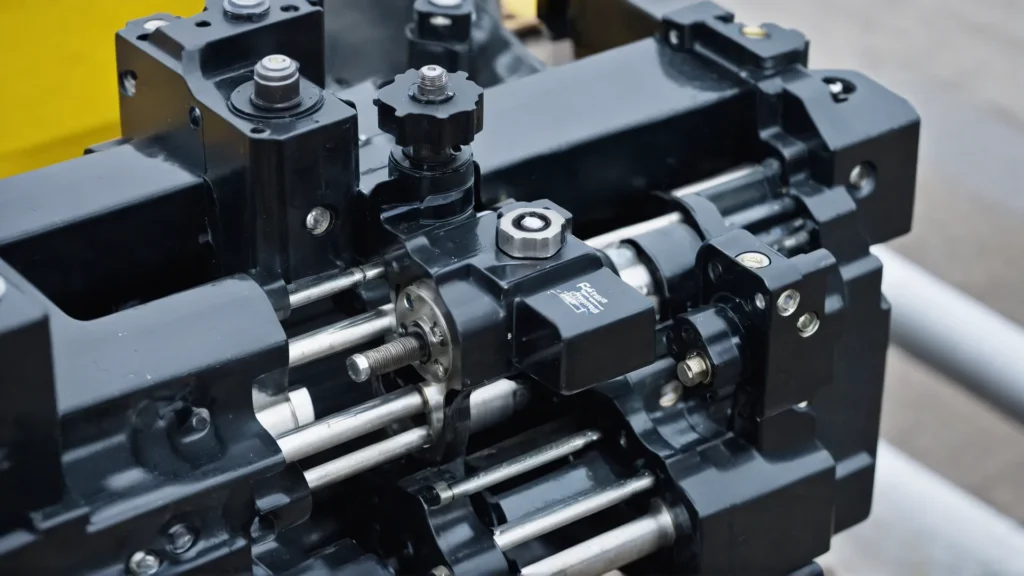
Frequently Asked Questions
What Are the Safety Features of Hydraulic and Electric Linear Actuators?
Hydraulic actuators rely on pressure relief valves and robust construction for safety. Electric actuators use fail-safe brakes and overload protection. Both systems prioritize safety through distinct mechanisms.
How Do Hydraulic and Electric Actuators Perform in Extreme Weather Conditions?
In extreme weather, hydraulic actuators may experience oil thickening in cold conditions and potential seal damage from heat. Electric actuators generally perform better but can overheat in hot environments. Always evaluate based on specific requirements.
What Are the Noise Levels of Hydraulic Versus Electric Linear Actuators?
Electric actuators typically operate more quietly than hydraulic systems. Hydraulic actuators generate considerable noise from pumps and fluid flow, whereas electric actuators offer a more silent operation, suitable for noise-sensitive settings.
Conclusion
When choosing between hydraulic and electric linear actuators, consider the specific needs of your application. Hydraulic actuators offer high force and load capacity. Electric actuators provide precise control and energy efficiency. Evaluate force requirements, precision needs, and system compatibility. Make an informed choice based on these factors. Contact us for more information.