Pneumatic Actuator Vs. Electric Actuator
Pneumatic actuators employ compressed air to generate motion, while electric actuators use electrical energy to produce mechanical movement. The primary difference lies in their source of power and the nature of their operation.
Understanding the fundamental distinctions between pneumatic and electric actuators is essential for selecting the appropriate device for various industrial applications. This comparison sheds light on their operational mechanisms, advantages, and disadvantages, guiding professionals in making informed decisions.
What Is An Electric Actuator?
An electric actuator is a device that converts electrical energy into mechanical torque. This equipment powers movement in machines and controls systems across various industries. It operates using an electric motor that drives a gear set to achieve motion. This process might be linear or rotary, depending on the type of actuator and its application.
Advantages Of Electric Actuator
- Precision: They provide better control over motion and positioning.
- Energy Efficiency: They convert electrical energy to mechanical motion more efficiently.
- Installation and Maintenance: They require less infrastructure and are easier to maintain.
- Environmental Friendliness: They don’t introduce contaminants, making them suitable for clean environments.
- Versatility: They can operate in places without an air supply or where air might be hazardous.
- Cost-Effectiveness: Although initially more expensive, they can be cheaper to operate in the long run due to lower energy and maintenance costs.
- Quiet Operation: They generally make less noise.
- Smart Integration: They easily integrate with digital and automated systems for advanced control.
What Is A Pneumatic Actuator?
A pneumatic actuator converts compressed air into mechanical motion. It uses the energy in the pressurized air to move a piston within a cylinder. This movement then executes the task at hand, such as opening or closing a valve.
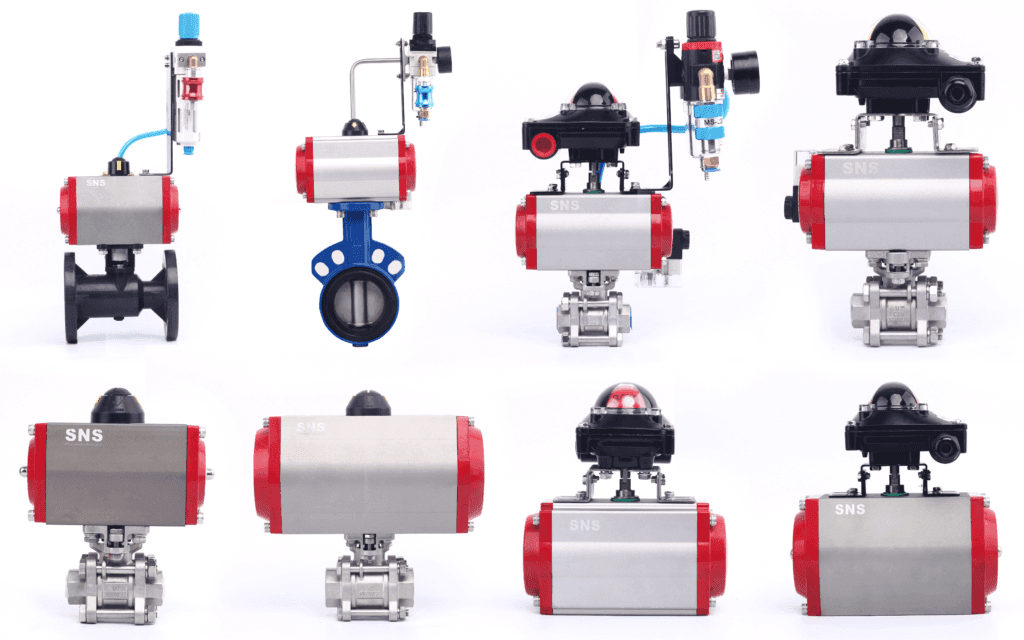
Advantages Of Pneumatic Actuator
- Reliability: Simpler, with fewer moving parts for less wear.
- Cost-Effectiveness: Generally lower initial costs.
- Speed: Faster operation due to quick air compression and release.
- Safety: Safer in explosive environments as they don’t generate sparks.
- Power: Capable of generating high force and torque.
- Durability: More tolerant of harsh conditions like moisture and dust.
- Overload Safety: Less likely to be damaged by overload; they just stall.
- Energy Storage: Compressed air can act as an energy reserve for continued operation during power outages.
The Differences: Electric Vs. Pneumatic Actuators
Aspect | Electric Actuators | Pneumatic Actuators |
---|---|---|
Design Complexity | More complex, precision control components | Simpler, fewer moving parts |
Installation | More complex due to electrical wiring and controls | Easier, mainly air supply connections |
Force & Speed | Variable, precise control of force and speed | High, fast action but less precise |
Stalling | Can overheat or get damaged | Simply stalls, no damage |
Resistance to Moisture and Dust | Less resistant, sensitive electronics | More resistant, suitable for harsh environments |
Temperature Range | Limited by electrical components’ temperature sensitivity | Wider, can operate in extreme conditions |
Component Cost | Higher initial cost | Lower initial cost |
Operating Cost | Lower, more energy-efficient | Higher, requires compressed air supply |
Heating During Operation | Can generate heat, requiring cooling in some cases | Does not generate heat |
Spring Return Feature | Available but adds to complexity and cost | Inherently available |
Torque to Weight Ratio | Generally lower | Higher |
Force | Variable, can be precisely controlled | High, but less precise control |
Speed | Variable, can be precisely controlled | High speed but less precise |
Maintenance | Lower frequency but can be more complex due to electronic components | Higher frequency but generally simpler |
Design
Electric actuators embody advanced technological designs that offer precise control. They integrate seamlessly with modern digital control systems, allowing for accurate positioning and feedback. Their compact structure is optimal for confined spaces.
Pneumatic actuators, contrastingly, exhibit simplicity in their design. They operate on air pressure to create motion, making them robust and well-suited for harsh environments. Their design relies on fewer moving parts, which contributes to durability and reliability.
The design differences extend to modularity as well. Electric actuators often provide modular components, facilitating easy customization for specific applications. This adaptability allows users to modify or upgrade actuation capabilities as required.
Pneumatic designs benefit from a straightforward approach that prioritizes function over complexity. This simplicity ensures easier integration into various industrial settings without extensive modifications or specialized components.
Installation
Electric actuators require a power source and control signal, making their setup more intricate. You need to connect them to the electrical network and ensure compatibility with control systems. This can involve detailed wiring and programming.
Pneumatic actuators, on the other hand, rely on compressed air. Their installation usually involves attaching air supply lines to the actuator. This process is typically less complex than dealing with electrical connections. However, it requires access to a reliable source of compressed air, which might necessitate installing compressors and conditioning equipment.
Force & Speed
Electric actuators provide precise control over force and speed, a key advantage in applications requiring detailed motion control. They offer variability in settings, allowing for adjustments to meet specific demands of an operation. The level of control means that the speed can be increased or decreased and the force modulated according to the task’s requirements without compromising on accuracy.
Pneumatic actuators, on contrast, excel in applications where raw power and speed are paramount. They generate force quickly due to the nature of compressed air expanding rapidly, making them suitable for high-speed operations. However, while pneumatic actuators can operate at varying speeds, their ability to fine-tune these adjustments is less refined compared to electric actuators. The control over force is generally coarser, with adjustments often hinging on altering the air pressure rather than being able to specify a precise force output.
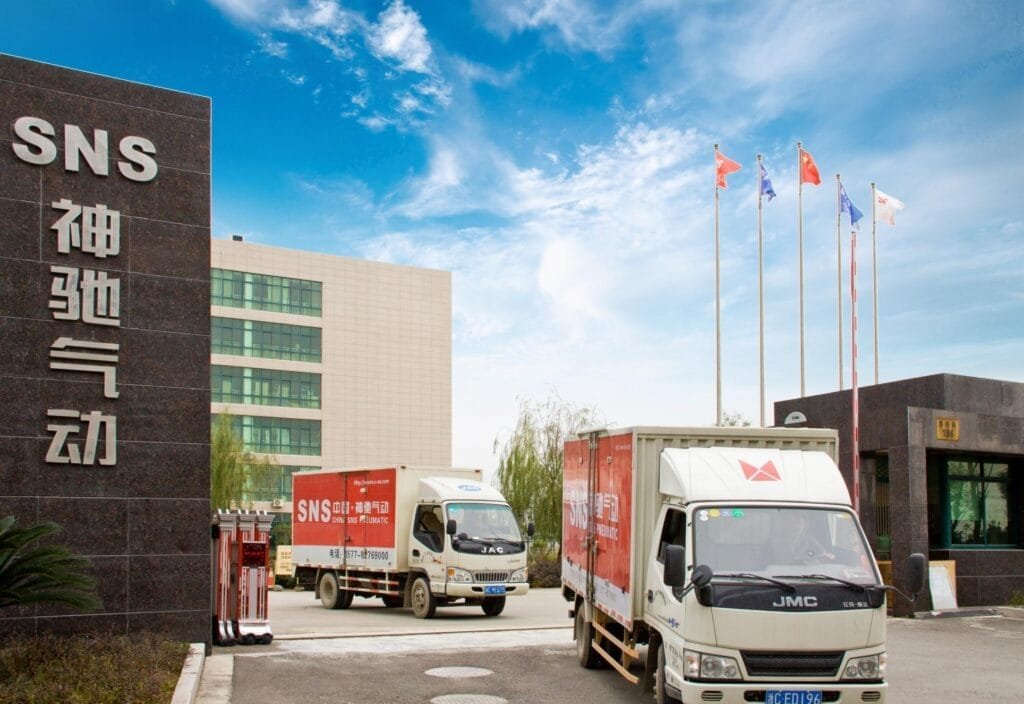
Stalling
Stalling refers to an actuator’s response when it encounters resistance exceeding its capability. Electric actuators handle stalling differently compared to pneumatic actuators. An electric actuator may overheat and potentially suffer damage if stalled for prolonged periods under load. This scenario necessitates monitoring systems or protective mechanisms to prevent overheating or damage.
In contrast, a pneumatic actuator can tolerate stalling better due to its inherent design and operating principles. It can sustain a stalled condition indefinitely without incurring damage, making it more robust in applications where jamming or blocking might occur. However, the continuous air consumption during stall conditions can lead to inefficiencies.
Resistance To Moisture
Electric actuators contain electrical components that are sensitive to water and can be damaged by exposure to moisture, leading to short circuits or corrosion of electrical parts. This susceptibility makes them less ideal for applications in wet or humid environments unless specifically designed with protective measures such as sealing and waterproof casings.
Pneumatic actuators, on the other hand, inherently possess a higher resistance to moisture due to their operating principle involving compressed air. They do not rely on electrical components that can be affected by water. However, it’s important to manage moisture in the compressed air supply to prevent internal corrosion or freezing in colder conditions, which can affect performance and lifespan. This is typically handled through air preparation processes that include drying the compressed air before it enters the actuator.
Temperature
Temperature plays a critical role in the selection and performance of actuators, influencing their efficiency, durability, and suitable application environments. Electric actuators demonstrate significant robustness in a wide range of temperatures. They can operate effectively in extremely low or high ambient conditions, making them versatile for diverse industrial applications. This adaptability is attributed to their design that lacks compressible fluids or gases, which might otherwise be affected by temperature variations.
Contrastingly, pneumatic actuators are more sensitive to changes in temperature. Their performance is directly impacted by the properties of the compressed air or gas used for operation. Lower temperatures can lead to condensation and possible freezing of moisture in the system, which impairs functionality and leads to maintenance issues. At higher temperatures, pneumatic systems may experience reduced efficiency as the heat causes expansion of gases, leading to decreased force output and potential component damage over time.
Component Cost
Electric actuators typically incur a higher upfront cost compared to pneumatic actuators. This difference arises from the complexity of their design and the materials used in construction. Electric actuators incorporate precision electrical components, such as motors and drive systems, which elevate their initial purchase price.
Pneumatic actuators, on the other hand, are simpler in structure. They rely on compressed air to operate, reducing the need for expensive electrical components. This simplicity makes pneumatic actuators more cost-effective to produce and purchase.
However, looking beyond the initial cost reveals a nuanced perspective on long-term investments. Electric actuators often possess longer lifespans compared to their pneumatic counterparts due to fewer moving parts and less wear from operation. This longevity can translate into lower replacement costs over time.
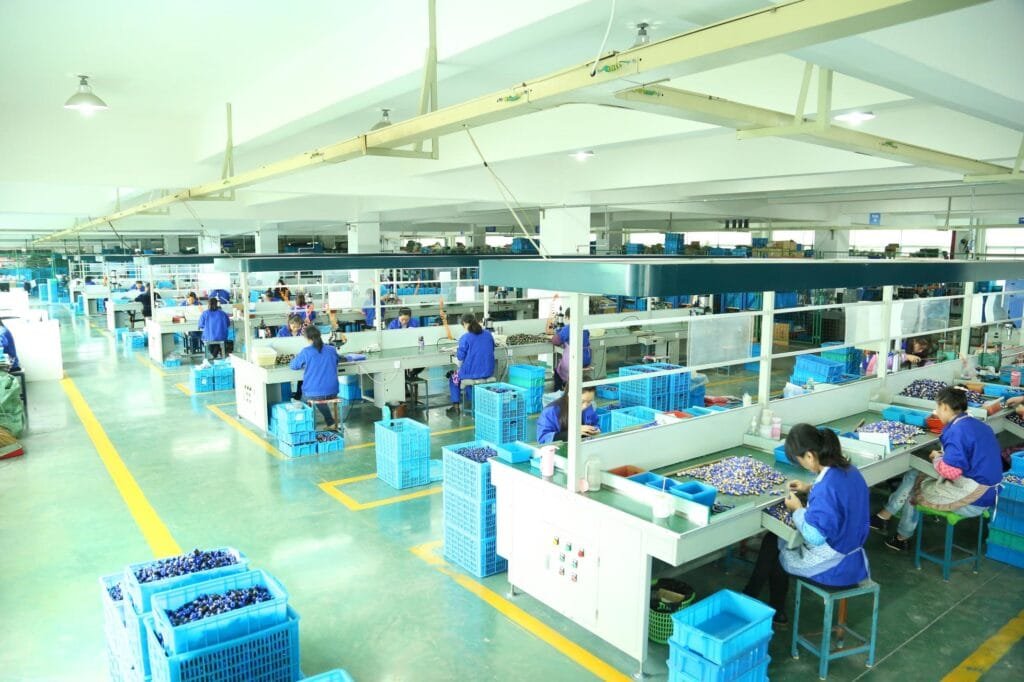
Operating Cost
Electric actuators typically exhibit higher upfront costs due to their sophisticated design but may lead to lower operating costs over time. They consume electrical power only when in operation, making them energy-efficient for applications not requiring continuous movement. Their precise control capabilities also reduce wastage and improve productivity, indirectly affecting operating costs positively.
Pneumatic actuators, on the other hand, rely on compressed air, which necessitates an air compressor and associated infrastructure. While the initial investment in these components can be significant, the overall expense can be moderated by the actuator’s simpler design. However, they can incur higher operational costs because compressors constantly consume energy to maintain pressure in the system. Leaks in the air supply system can further exacerbate these costs.
Heating
Electric actuators generate heat as they operate. This is due to electrical resistance within their components. The heat generation can affect the actuator’s performance and longevity, especially in sensitive applications or environments with strict temperature controls. Cooling systems or additional maintenance may be required to manage this heat.
Pneumatic actuators, on the other hand, tend not to generate significant amounts of heat during operation. This is because they use compressed air to function, which doesn’t inherently produce much heat. In fact, expanding air in a pneumatic system can even cause cooling effects. This makes pneumatic actuators suitable for high-temperature environments or applications where added heat could be problematic.
Spring Return
The spring return feature is critical in actuators, significantly impacting their functionality and safety. Pneumatic actuators inherently incorporate spring return due to their design. When air pressure is lost or intentionally cut off, the internal spring mechanism ensures the actuator returns to its original position. This function is vital for fail-safe operations, where returning the actuator to a safe state upon power or control loss minimizes potential hazards.
Electric actuators may also offer a spring return feature but achieve it differently. In electric models, a mechanical spring may be integrated to ensure that on power failure, the actuator returns to a predetermined position. However, this addition can increase the size and cost of electric actuators.
Spring return capabilities in pneumatic actuators are often seen as more reliable and simpler, due to fewer components involved. The natural integration of a spring in pneumatics means there’s no additional complexity or significant cost increase. For applications requiring fail-safe operation without compromise on reliability, pneumatic actuators with spring return are frequently preferred.
Torque To Weight Ratio
The torque to weight ratio in actuators signifies the relationship between the actuator’s ability to generate rotational force (torque) and its total weight.
Electric actuators often boast a higher torque-to-weight ratio compared to pneumatic actuators. This is because electric actuators can generate significant torque at low speeds without requiring much space or adding excessive weight. Electric motors are inherently efficient in converting electrical energy directly into mechanical energy, thus enabling a compact design with high torque generation capabilities.
Pneumatic actuators, on the other hand, tend to have a lower torque-to-weight ratio. The nature of compressed air as the driving force means that while they can be lightweight due to their simple construction, the actual amount of torque they can produce for their size is generally less than that of electric actuators. Pneumatic systems rely on air pressure and volume to create movement; therefore, achieving high torque might necessitate larger, heavier components like bigger cylinders or more robust valves which inversely affects the ratio.
Force
Electric actuators are recognized for their precise control over force application, which can be finely tuned according to the specific needs of a task. This precision stems from the actuator’s inherent design, integrating seamlessly with electronic control systems that precisely modulate the applied force.
Pneumatic actuators, on the other hand, depend on compressed air to generate movement and hence force. The level of force they can exert is directly proportional to the available air pressure and cylinder size. They are capable of producing significant force outputs, often exceeding what is feasible with electric options. However, their capability to finely control that force is less nuanced compared to electric actuators. Adjustments can be made by regulating air pressure, yet this method lacks the fine-tunability found in electric counterparts.
Speed
Speed in actuators defines how quickly they can move from one position to another. It’s a critical factor, significantly influencing system performance and responsiveness. Electric actuators exhibit variable speeds, controlled through the power supply or by specific drive technologies. They can achieve precise positioning rapidly, making them ideal for applications requiring accurate control and agility.
Pneumatic actuators, on the other hand, have their speed dictated largely by air flow and pressure adjustments. They generally offer higher speeds than electric versions because of the nature of compressed air, which allows rapid movement. However, their speed is less controllable compared to electric actuators.
Maintenance
Maintenance of actuators is a critical aspect that directly influences their lifespan, reliability, and operational costs. Electric actuators require less frequent maintenance compared to pneumatic actuators. Their design minimizes wear and tear because there are fewer moving parts. Electric actuators often need checks on electrical components like the motor and control units. Upkeep typically involves firmware updates or calibration rather than physical repair.
Pneumatic actuators, in contrast, demand regular attention. They rely on air compressors, filters, and hoses to function. These components are susceptible to degradation over time. Moisture can accumulate in the system, leading to rust or contamination of the air supply. Filters must be replaced regularly to ensure clean air flow. Hoses can develop leaks, which reduces efficiency and requires timely intervention.
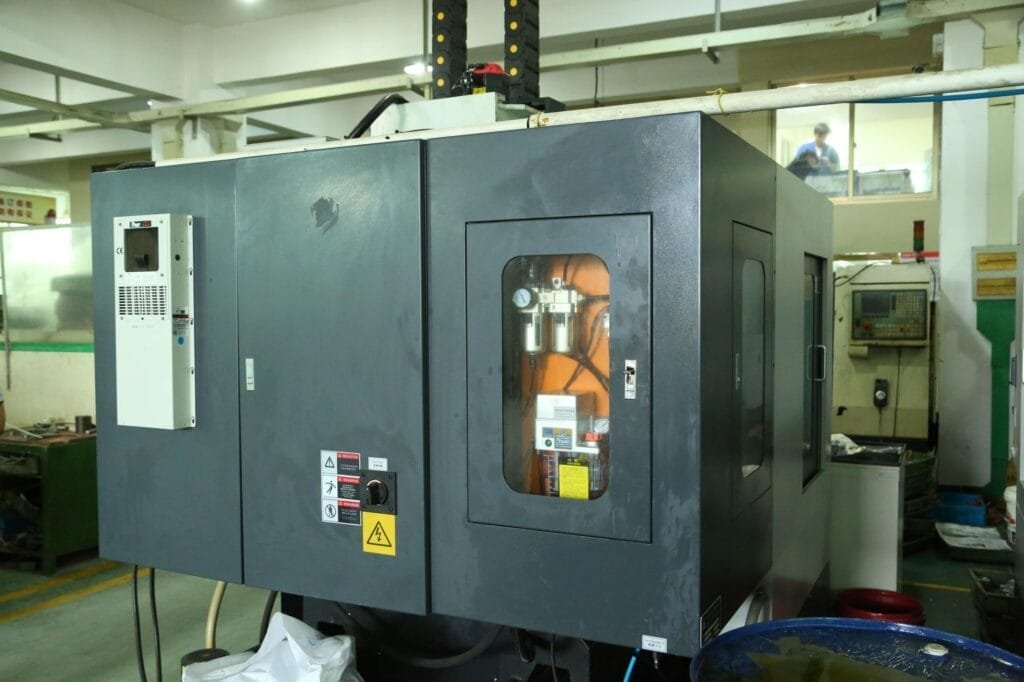
How To Select The Right Actuator
Selecting the right actuator is a process that requires consideration of various factors. These include the application environment, the availability of power sources, the need for control precision and response time, and cost considerations.
Application Environment: This relates to where the actuator will operate. Different environments demand different types of actuators. For example, harsh environments with exposure to moisture or extreme temperatures may be better suited for pneumatic actuators due to their robustness.
Availability Of Power Sources: The choice between electric and pneumatic actuators often comes down to the available power sources at the installation site. Electric actuators require a constant supply of electricity, whereas pneumatic actuators need a supply of compressed air.
Required Control Precision And Response Time: Applications requiring precise control over movement, speed, or position often benefit from electric actuators. They provide superior precision and faster response times compared to pneumatic counterparts.
Cost Considerations: Initial component cost and operating costs are both crucial factors. Pneumatic actuators typically have lower initial costs but can be more expensive in the long term due to continuous consumption of compressed air. Electric actuators might have a higher upfront cost but usually offer lower operating costs over time.
Decision-making involves weighing these considerations based on the specific needs of your application. It’s vital to assess each factor’s relevance and impact on your operation’s efficiency, safety, and effectiveness before making a choice.
In Conclusion
In summary, pneumatic actuators and electric actuators differ fundamentally in their source of power, operation, cost, and application suitability, each offering unique advantages for specific industrial needs.
Discover the ideal actuation solution for your project by exploring our comprehensive selection of both pneumatic and electric actuators. Connect with our experts today to make an informed decision that enhances your operational efficiency.