Rodless Cylinder Working Principle
Have you ever wondered how machines achieve smooth linear motion in compact spaces? The rodless cylinder working principle offers a solution.
Rodless cylinders use compressed air to generate linear motion without an external piston rod. This innovative design allows for longer strokes in limited spaces.
What is the Principle of the Pneumatic Cylinder?
Pneumatic cylinders operate on the principle of compressed air to generate linear motion. These devices consist of a piston within a cylindrical chamber. Compressed air enters one side of the chamber, pushing the piston and creating movement.
The piston is connected to a rod that extends outside the cylinder, translating the internal motion into external work. Valves control the airflow, determining the direction and speed of the piston’s movement. When air pressure is applied to the opposite side, the piston reverses direction.
How does a rodless air cylinder work?
Rodless air cylinders operate on the principle of compressed air to generate linear motion without an external piston rod. These cylinders feature a piston that moves within a sealed tube, propelled by compressed air.
The piston is connected to an external carriage through a slot along the cylinder’s length. This slot is sealed by a flexible band to prevent air leakage. As compressed air enters one end of the cylinder, it pushes the piston, moving the carriage along the cylinder’s exterior.
Rodless cylinders offer compact design advantages, allowing for longer strokes in limited spaces. They eliminate the need for external rod support and reduce the overall footprint of the system. These cylinders find applications in various industries, including automation, packaging, and material handling.
The design of rodless cylinders ensures smooth, continuous motion and precise positioning. They can handle higher loads compared to traditional rod-type cylinders of similar size. Rodless cylinders provide versatility in mounting options and can be easily integrated into existing systems.
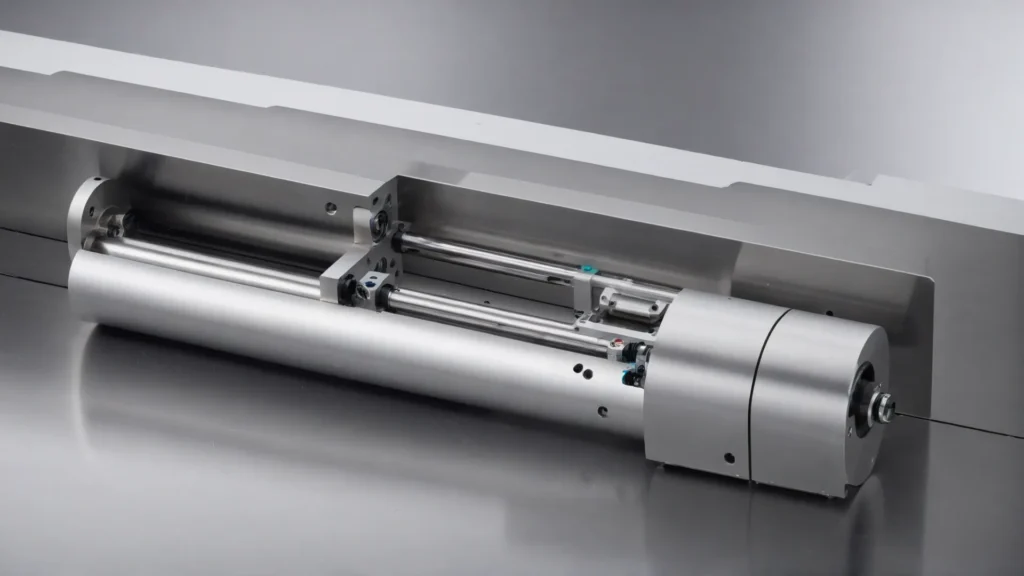
Rodless Cylinder Types
Magnetic pneumatic rodless cylinder
Magnetic pneumatic rodless cylinders utilize a magnetic coupling system to transmit force. The piston inside the cylinder contains strong magnets that interact with an external carriage equipped with corresponding magnets. As compressed air moves the internal piston, the magnetic field pulls the external carriage along the cylinder’s length.
Cable pneumatic rodless cylinder
Cable pneumatic rodless cylinders employ a flexible cable or band to connect the internal piston to the external carriage. The cable runs through a sealed channel along the cylinder’s length. As the piston moves, it pulls the cable, which in turn moves the external carriage.
Slits pneumatic rodless cylinder
Slits pneumatic rodless cylinders feature a narrow slit along the cylinder’s length, through which a connection piece links the internal piston to the external carriage. Sealing strips protect the slit, opening only where the connection piece passes through.
Advantages and Disadvantages of a Rodless Cylinder
Advantages
Rodless cylinders offer significant space-saving benefits compared to traditional rod-type cylinders. They provide longer strokes within a compact footprint, making them ideal for applications with limited space. These cylinders eliminate the need for external rod support, reducing overall system complexity.
Rodless cylinders deliver smooth and precise linear motion, enhancing positioning accuracy in automation systems. They offer excellent load-bearing capacity, often surpassing that of conventional cylinders of similar size. The design of rodless cylinders allows for easy integration into existing machinery and provides versatile mounting options.
Disadvantages
Despite their advantages, rodless cylinders have some limitations. They typically cost more than traditional rod-type cylinders due to their complex design and manufacturing process. Maintenance can be more challenging, particularly for sealing components that prevent air leakage along the cylinder’s length.
Rodless cylinders may be more susceptible to contamination, especially in dusty or dirty environments. This can affect their performance and longevity. Some designs, particularly those using magnetic coupling, may have limitations in load capacity compared to mechanical linkage systems. Additionally, rodless cylinders may require more frequent maintenance to ensure optimal performance and prevent air leaks.
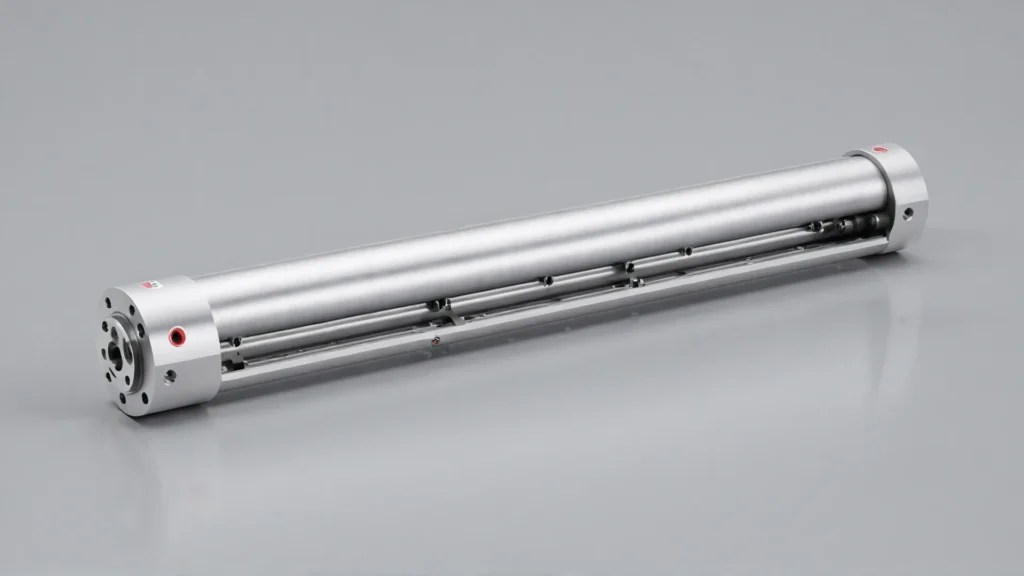
Application areas of rodless cylinders
Manufacturing and Assembly
Rodless cylinders play a crucial role in manufacturing and assembly processes. They are used in production lines for tasks such as material transfer, part positioning, and automated assembly. The compact design of rodless cylinders allows for efficient use of space in crowded factory environments.
Packaging and Material Handling
In the packaging industry, rodless cylinders are widely utilized for various applications. They are employed in box erectors, carton sealers, and palletizing systems. The long stroke capabilities of rodless cylinders make them ideal for pushing or pulling products along conveyor belts or transferring items between different stages of the packaging process.
Material handling systems benefit from the space-saving design of rodless cylinders. They are used in warehouse automation, sorting systems, and logistics operations. Rodless cylinders provide the necessary linear motion for moving goods efficiently and accurately within limited spaces.
Automotive Industry
The automotive industry employs rodless cylinders in various manufacturing and testing processes. These cylinders are used in vehicle assembly lines for tasks such as positioning car bodies, installing components, and operating robotic welding arms. Their compact design allows for flexible integration into complex automotive production systems.
Rodless cylinders also find applications in automotive testing equipment. They are used in suspension testing rigs, brake testing systems, and other quality control processes. The precise motion control offered by rodless cylinders ensures accurate and repeatable testing procedures.
FAQs
1.What is the difference between a rodless cylinder and a normal cylinder?
A rodless cylinder has no piston rod. A normal cylinder has a piston rod. Rodless cylinders are more compact. They provide longer strokes in smaller spaces.
2.How to choose the right rodless cylinder?
Consider the required stroke length. Determine the load capacity needed. Check the available mounting options. Match the cylinder’s size to your application. Ensure compatibility with your system’s pressure and environment.
3.How to mount a rodless cylinder?
Select a suitable mounting method. Common options include flanges, brackets, and direct threading. Ensure proper alignment and support. Securely fasten the cylinder to the machine frame. Connect the air supply lines. Test for smooth operation and leaks.
Conclusion
Rodless cylinders offer innovative solutions for linear motion in compact spaces. Their unique design provides efficiency and versatility across various industries.
Understanding the working principle of rodless cylinders is crucial for optimizing pneumatic systems.
Consider implementing rodless cylinders in your next project for improved space utilization and performance.