What Are Pneumatic Components
Pneumatic components are parts of machines or systems that use compressed air to perform various tasks, such as moving, gripping, and controlling mechanisms. These components of pneumatic include air cylinders, valves, tubes, and fittings essential for the operation of pneumatic systems.
Pneumatics is a branch of engineering that utilizes the properties of compressed air to effect mechanical motion. Understanding pneumatic components is crucial for designing efficient and reliable systems in various industrial applications, highlighting the need for a detailed exploration of these elements.
What Are Pneumatic Components
Pneumatic components form the building blocks of pneumatic systems. These systems use compressed air to transmit and control energy. Pneumatic parts are diverse, each serving a specific function within the system. Their design focuses on manipulating air to perform tasks like lifting, moving, and holding materials.
How Do Pneumatic Components Work?
- Compressor and Air Preparation: It starts with a compressor that generates compressed air. This air is then cleaned and dried to prevent damage to the components. Moisture separators, filters, and dryers are used to prepare the air.
- Pressure Regulation: The compressed air’s pressure is regulated through a regulator to ensure it is at the correct level for the system’s requirements. This step is crucial as different pneumatic tools and components require different operating pressures.
- Control Valves: Valves control the flow of compressed air. They can start, stop, and regulate the flow of air through the system. Valves can be manually controlled, solenoid operated (electrically controlled), or pneumatically controlled. The design and configuration of these valves can vary greatly depending on the complexity and requirements of the pneumatic system.
- Actuators: The actuators are the components that do the work. They convert the energy of the compressed air into mechanical motion. There are various types of actuators, but the most common are cylinders (linear motion) and motors (rotary motion). Cylinders can push, pull, lift, and lower loads, while pneumatic motors can drive wheels or turn gears.
- Ancillary Components: Other components like fittings, tubing, and hoses are used to connect everything together, allowing the compressed air to flow through the system. Sensors and switches can be used to monitor and control the system’s performance.
- Exhaust and Release: After the air has done its work in the actuator, it needs to be released or exhausted. This release of air usually occurs through valves, and it’s often vented into the atmosphere.
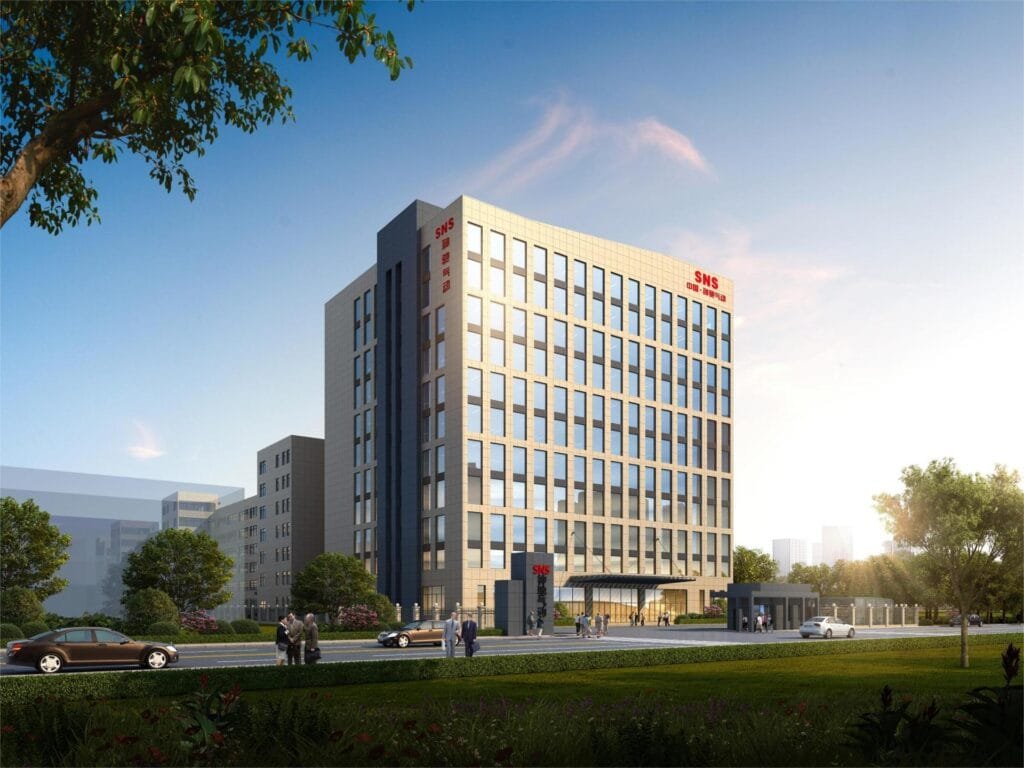
Types Of Pneumatic System Components
Pneumatic systems consist of various components, each serving a unique purpose in the system. These include air compressors, air reservoirs, FRL (Filter-Regulator-Lubricator) units, pneumatic valves, circuits, cylinders/actuators, fittings and tubings, sensors and switches, pressure switches and gauges, plus silencers and mufflers.
Air Compressors
Air compressors are essential in pneumatic systems. They convert power into potential energy stored in pressurized air. This process involves drawing in atmospheric air, which the compressor then confines within a limited space. It decreases the volume of the air, causing pressure to increase.
Air Reservoir
An air reservoir, also known as an air tank, stores compressed air for use in pneumatic systems. Its primary function is to maintain a constant supply of air under pressure. This consistent supply ensures that pneumatic devices operate smoothly without interruptions caused by fluctuations in pressure.
FRL (Filter-Regulator-Lubricator)
FRL stands for Filter, Regulator, and Lubricator. These components are essential in a pneumatic system. They prepare compressed air to be used within the system efficiently and safely. The FRL unit ensures that the air is clean, at the correct pressure, and properly lubricated before it reaches pneumatic tools or cylinders.
Pneumatic Valves
Pneumatic valves control air flow. They start, stop, and direct this flow. Each valve type has a specific function. There are several key types, including directional control valves, flow control valves, and pressure relief valves. Directional control valves manage the path of airflow. Flow control valves regulate speed by adjusting air flow. Pressure relief valves maintain system pressure to prevent damage.
Pneumatic Circuit
A pneumatic circuit forms the backbone for any system using compressed air to perform work. It is an integrated assembly of pneumatic components. These include valves, actuators, and fittings, designed to control the movement and pressure of air within a pneumatic system. The circuit ensures that air flows in a controlled manner from the compressor to the pneumatic actuator.
Pneumatic Cylinders/Actuators
Pneumatic cylinders or actuators convert compressed air power into mechanical movement. They act as the muscle in pneumatic systems, creating linear or rotary motion. These components come in a variety of types and sizes tailored for specific functions and performance requirements.
Fittings And Tubings
Fittings and tubings are crucial components in pneumatic systems. They serve the purpose of connecting various parts, ensuring a seamless flow of compressed air throughout the system. Made from diverse materials like plastic, brass, and stainless steel, these components are selected based on the specific requirements of the pneumatic system they are part of.
Sensors And Switches
Sensors and switches are critical in pneumatic systems for monitoring and control. They detect changes in pressure, flow, and other parameters. This detection allows the system to respond appropriately. Different types provide various functions. For example, pressure sensors identify when the pressure reaches a specific level. Flow sensors monitor the rate of air movement. Temperature sensors measure air temperature in the system.
Pressure Switches And Gauges
Pressure switches and gauges monitor the air pressure. If the pressure reaches a specific level, pressure switches can activate or deactivate the system. This maintains system safety and efficiency.
Gauges display current pressure levels. They allow for real-time monitoring. This helps prevent system damage by alerting operators to pressure changes that may indicate leaks or blockages.
Silencers And Mufflers
Silencers and mufflers are designed to reduce noise produced by the exhaust air. Pneumatic systems can generate significant noise levels when air is released. This noise can be detrimental to worker health and operational efficiency.
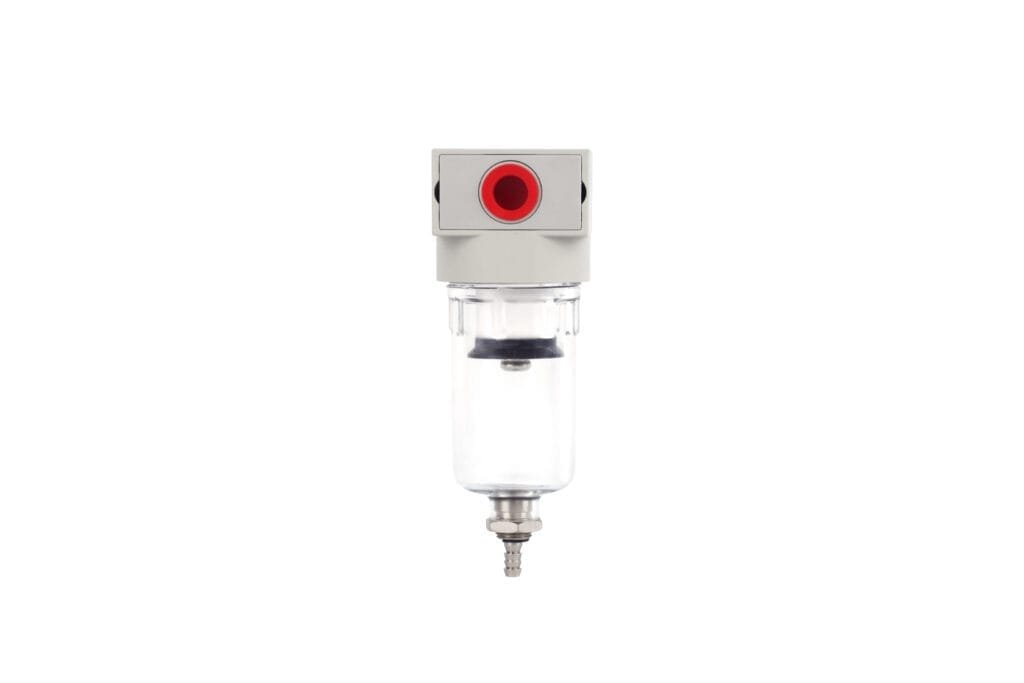
Benefits Of Pneumatic Components
Simplicity and Reliability: Straightforward use and maintenance due to fewer moving parts.
Safety: Minimized risk in explosive environments due to the use of air.
Cost-effectiveness: Generally less expensive to install, operate, and maintain.
Speed and Efficiency: Rapid start, stop, accelerate, decelerate through simple control of air flow.
Cleanliness: Air as the primary medium can be filtered and does not contaminate if leaked.
Flexibility and Versatility: Ease of customization and reconfiguration as per changing requirements.
Energy Efficiency: On-site generation of compressed air, reducing transmission losses.
Durability: Designed to withstand harsh conditions with minimal wear.
Portability: Light weight owing to the use of air instead of hydraulic fluids.
Rapid Response Time: Instant response to control signals.
Simplicity and Reliability
Pneumatic components stand out for their simplicity. Their design centers around air. This is a readily available resource. Using air means fewer parts. Fewer parts mean there is less that can go wrong.
Reliability is another key trait of pneumatic systems. These components consistently perform well over time. Air is a clean energy source. It does not leave residues that could impair function.
Safety
Safety stands as a paramount benefit of pneumatic components. These systems are inherently safer than their hydraulic or electrical counterparts due to the use of compressed air rather than hazardous fluids or electricity. A significant advantage is the minimal risk of fire, as compressed air does not ignite easily compared to hydraulic oil. Furthermore, in the event of a leak, there is no risk of contamination from dangerous chemicals or the complications associated with cleaning up such spills.

Cost-Effectiveness
Pneumatic accessories offer significant cost advantages. They are generally cheaper to purchase than their hydraulic or electric counterparts. The installation process is straightforward, requiring less specialized labor. This decreases initial costs.
Operating expenses for pneumatic systems are also lower. These systems use air as the primary resource, which is abundantly available and free. In contrast, hydraulic systems rely on expensive oils, and electric systems consume costly electricity.
Speed And Efficiency
This trait is crucial in many applications, from manufacturing to robotics. These systems rely on compressed air, allowing rapid movement of parts and tools. Speed is a key advantage of pneumatics over other technologies. Pneumatic systems can start, stop, and change directions quickly. This capability makes them ideal for tasks requiring fast responses.
Cleanliness
These systems use air as the primary medium for operation. Air is abundant, clean, and does not contaminate products. This quality is vital in industries where cleanliness is crucial. For example, the food, pharmaceutical, and semiconductor sectors rely heavily on pneumatics.
The operation of pneumatic systems produces no pollutants. Unlike hydraulic systems, which can leak oil or other fluids, pneumatics pose no risk of contamination through leaks because they use air. This feature makes pneumatics preferable in sterile environments.
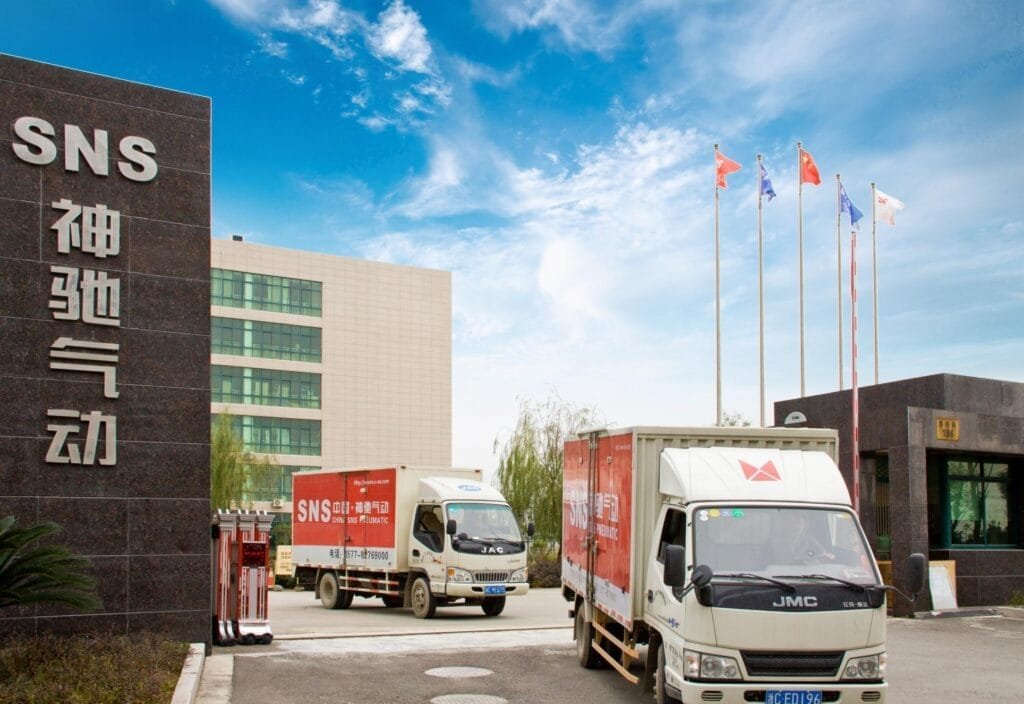
Flexibility and Versatility
Pneumatic components offer unmatched flexibility and versatility. These systems can easily adapt to various applications, thanks to the wide range of components available. Users can customize pneumatic systems based on specific needs by selecting from different types of air compressors, valves, cylinders, and other accessories. This customization capability makes pneumatic technology suitable for a broad array of industries including manufacturing, automotive, robotics, and medical fields.
The ability to integrate with different machinery is a key feature. Pneumatic systems can work alongside existing mechanical processes seamlessly. This integration extends their applicability without necessitating major overhauls of current setups.
Energy Efficiency
Pneumatic components stand out for their energy efficiency. They use air, an abundant resource. Air powers these systems, leading to lower operation costs. Pneumatic systems convert compressed air into mechanical energy effectively. This process minimizes energy loss.
They require less electricity compared to hydraulic systems. The design of pneumatic components allows minimal leakage. Thus, maintaining efficiency over time. These systems are optimal for short-distance and repetitive tasks. Such applications reduce the overall energy consumption.
Durability
They are designed for endurance, resisting wear and tear from regular use. These components handle the pressures and cycling demanded in industrial environments efficiently. Materials used in manufacturing pneumatic systems, such as metals and strong plastics, contribute to their longevity. Durability means these systems require less frequent replacement or repair, proving cost-effective over time.
Portability
Portability is a key advantage of pneumatic components. These systems are designed for easy movement. They can be relocated with minimal effort. This makes them ideal for various applications, especially where mobility is essential.
Rapid Response Time
Pneumatic components react quickly to control signals. They convert these signals into physical movement or action faster than many other actuation methods. This speed is due to the nature of compressed air as a driving force, which allows for immediate transmission of power.
Applications Of Pneumatic Components
Manufacturing: Powers machinery for tasks like drilling, grinding, and painting, ideal for automation.
Automotive Sector: Used in assemblage, lifting heavy items, and controlling robotic arms.
Robotics: Provides force and movement for tasks like object picking and placing, enhances overall efficiency of robotic systems.
Medical Field: Used in ventilators and patient handling systems, suited for sterile environments.

Factors To Consider When Selecting Components of Pneumatic
Operating Pressure: The force per unit area supplied by the air compressor, varies based on application.
Flow Rate: Indicated by cubic feet per minute (CFM), it denotes how fast air moves through the system.
Environment: The conditions where the system operates like dust, moisture, temperature extremes, and chemical exposure.
Reliability: Quality of components to withstand operational demands, reducing downtime.
Operating Pressure
Operating pressure refers to the maximum pressure at which a pneumatic system or component is designed to operate safely and efficiently. It’s measured in pounds per square inch (PSI) or bar. Selecting the correct operating pressure is vital for the performance, safety, and longevity of pneumatic components. Too low pressure might not power the system effectively. Conversely, exceeding the recommended operating pressure can lead to equipment failure or hazardous situations. Manufacturers specify this parameter to ensure optimal functionality and safety. Users must adhere to these guidelines to avoid risks and maintain system integrity.
Flow Rate
It measures the volume of air that can move through a component in a given time, typically expressed in cubic feet per minute (CFM) or liters per minute (L/min). A higher flow rate means more air can be delivered quickly to operate tools or machinery efficiently.
Selecting the correct flow rate for pneumatic components ensures optimal performance. If the flow rate is too low, it may lead to inadequate operation of the system, causing delays or malfunctions. Conversely, an excessively high flow rate can result in wasted energy and potential damage to components due to excessive pressure.
Environment
Different environments can affect the performance and longevity of these components. Harsh conditions, such as extreme temperatures, high humidity, or the presence of corrosive chemicals, demand materials and designs that can withstand these challenges. For example, in industries where temperature fluctuations are common, components must be able to operate effectively within this range without degradation.
Reliability
These components ensure machines operate smoothly without frequent breakdowns. A reliable pneumatic system reduces downtime and maintains production efficiency. The reliability of these systems hinges on several factors, including quality materials and proper maintenance.
High-quality materials enhance the durability and lifespan of pneumatic components, contributing to overall system reliability. Manufacturers often stress the importance of selecting high-grade metals and polymers for parts such as valves, cylinders, and fittings. This ensures they can withstand repeated use and adverse conditions without failure.
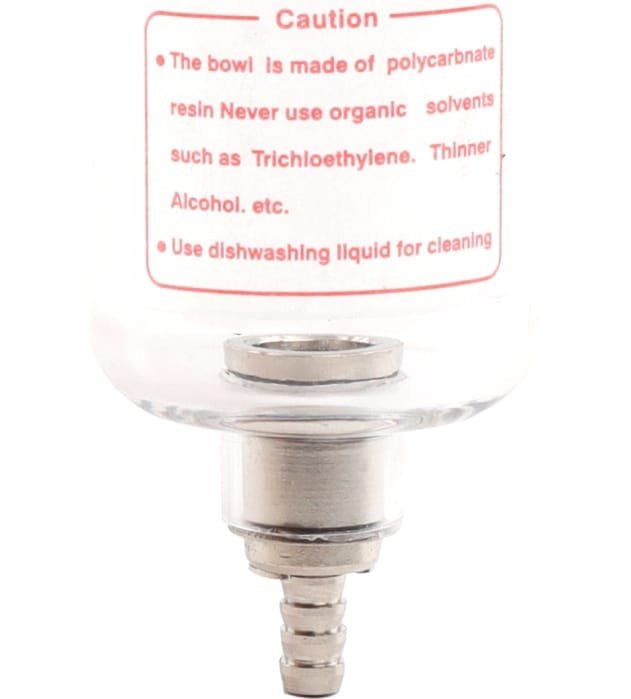
What Maintenance Is Required For Pneumatic Components?
Routine Inspections: Check for wear and tear, leaks leading to inefficiency and power loss.
Cleaning: Essential to remove dust and debris that can impair functionality.
Lubrication: Reduces friction between moving parts, extends lifespan. Specific components may require specific lubricants.
Filter Replacement: Prevents system contamination by impurities.
Moisture Monitoring: Prevents system corrosion and freezing in cold conditions. Draining condensate from air reservoir is common.
Valve Maintenance: Requires cleanliness and proper operation. Cylinders, actuators checked for smooth operation and seal integrity.
Pressure Settings Verification: Ensures settings are optimized for efficiency and safety.
Tubing and Fitting Inspection: Checks for damage or wear compromising system integrity or causing leaks.
Sensor and Switch Testing: Ensures control and safety systems are functional.
Manufacturer Recommendations: Follow the provided maintenance schedules to prevent sudden failures and extend component life.
What Are The Most Common Issues With Pneumatic Systems?
Leaks: The most common issue, leading to inefficiency and increased operational costs.
Contamination: Dirt and moisture can damage internal components, affecting performance.
Inadequate Lubrication: Causes wear and tear of moving parts.
Incorrectly Sized Components: Can overload the system or fail to achieve performance expectations.
Clogged Filters: Reduce air flow and pressure, impacting system efficiency.
Inadequate Maintenance: Leaves issues unchecked, leading to escalated system failures over time.
Are Pneumatic Systems Energy Efficient?
Yes, pneumatic systems can be energy efficient. They utilize compressed air which is a readily available and renewable resource. However, their energy efficiency can vary based on factors such as how well the system is maintained and used. Optimizing these factors can improve the energy efficiency of a pneumatic system.
Can Pneumatic Components Be Used In Harsh Environments?
Yes, pneumatic components can be used in harsh environments. Due to their robust design, they can endure conditions like extreme temperature, heavy dust, and high vibration. However, specific factors may affect their lifespan, so proper maintenance is crucial.
In Conclusion
In essence, pneumatic components are essential elements within various industrial applications, offering efficiency and reliability through the power of compressed air.
To ensure your machinery operates at its peak performance, consider exploring and integrating high-quality pneumatic components. Reach out to experts today to discuss how these robust solutions can enhance your operational workflow.