What Are The Different Types Of Air Regulators?
Air regulators play a significant role in various industries by controlling the pressure of compressed air to ensure efficiency and safety in operations. They are vital components in pneumatic systems, used across automotive, manufacturing, and construction sectors, among others. Given their importance, it is crucial to understand the different types of air regulators available to select the most appropriate one for a specific application. This article explores the primary types of air regulators, including single-stage, dual-stage, precision, and back-pressure regulators, detailing their operational mechanisms and suited applications.

3 Types Of Air Regulators
Air regulators play a pivotal role in pneumatic systems by controlling air pressure, ensuring that apparatuses function efficiently and safely. There are three primary types of air regulators designed to meet diverse requirements and applications: precision regulators, filter regulators, and general purpose regulators.
Precision Regulators are engineered for scenarios where constant pressure control under varying flow rates and supply pressures is necessary. Ideal for applications requiring exact pressure adjustments and stability, these regulators provide high accuracy and minimal pressure fluctuation. Precision regulators are often utilized in laboratories or in manufacturing processes where slight variations in pressure could significantly affect the quality of the output.
Filter Regulators, also known as piggyback regulators, combine the functions of both a filter and a regulator. They are designed to remove solid particles and condensate from compressed air while providing precise pressure control. This dual functionality makes them highly efficient for applications where air cleanliness is crucial along with stable pneumatic control. Commonly found in various industrial applications, they help extend the life of pneumatic equipment by preventing contamination.
General Purpose Regulators are versatile tools used across a wide range of applications to regulate air pressure down to required levels. These regulators are suitable for numerous standard pneumatic systems needing reliable pressure adjustment without the specialized features of precision or filter regulators. Their robust design allows them to be used widely across industry sectors including automotive repair shops, manufacturing facilities, and construction sites.
Precision Regulators
Precision regulators are specifically designed to provide stable air pressure control for applications requiring a high degree of accuracy and consistency. Unlike general-purpose regulators, which may have a broader range of functionality but less precision in control, precision regulators focus on delivering precise pressure adjustments even under varying flow rates and supply pressures. These devices are crucial in environments where the slightest variation in pressure can significantly affect the performance of pneumatic equipment or processes.
The core advantage of precision regulators lies in their ability to maintain a consistent output pressure—a feature that is vital for applications such as airbrushing, medical instrumentation, and laboratory experiments, where precise air flow and pressure levels are necessary for accurate results. Additionally, these regulators often come with enhanced features like fine adjustment knobs and detailed gauges that allow users to make micro-adjustments easily.
For industries and applications that demand exact air pressure control beyond what general-purpose regulators can provide, precision regulators offer the solution. They achieve this through sophisticated design elements including diaphragm sensitivity adjustments, precision valve seats, and sometimes digital feedback mechanisms to ensure top-tier performance is maintained consistently.
Filter Regulators
Filter regulators combine the functions of a filter and a regulator into one compact unit. These devices are designed to provide clean, controlled air pressure to pneumatic systems by removing particulate matter and moisture from compressed air. This dual-action ensures the protection of downstream equipment from harmful contaminants while maintaining the required pressure for optimal operation.
The primary component of a filter regulator is the filtration element, which traps particles and moisture as air passes through. This element can vary in material and pore size, allowing for customization based on the specific requirements of an application. Following filtration, the air meets the regulator component, which adjusts the air pressure to a pre-set level before it continues through the system.
Choosing a filter regulator involves consideration of several factors including maximum operating pressure, flow rate, particle size filtration capacity, and temperature range compatibility. Typically constructed with robust materials such as aluminum or stainless steel, these units can withstand challenging industrial environments.
One key advantage of using filter regulators is their efficiency in improving system performance by preventing the premature wear and malfunctions that can result from contaminated or fluctuating air supply. Suitable for use in a wide range of applications including manufacturing operations, automotive assembly lines, and paint spraying systems; filter regulators represent a critical component for ensuring reliability and longevity in pneumatic systems.
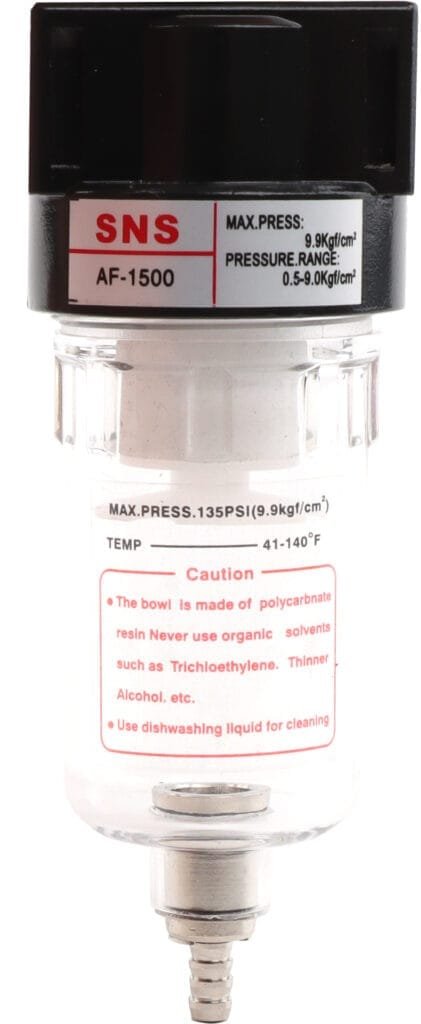
General Purpose Regulators
General Purpose Regulators are foundational components in a wide array of pneumatic systems, designed to maintain a constant output pressure despite variations in input pressure and downstream demand. These regulators are the workhorses of the air regulator family, offering robust performance in a variety of settings including manufacturing plants, automotive repair shops, and within various DIY applications.
One of the key features of General Purpose Regulators is their versatility. They can handle a broad spectrum of pressures and flows, making them suitable for numerous applications where precise control isn’t critically necessary but reliability is paramount. Manufactured with durability in mind, these regulators are constructed to withstand regular use in challenging environments without significant wear and tear.
When selecting a General Purpose Regulator, it’s essential to consider factors such as the maximum operating pressure it can handle and its flow capacity. Additionally, while they’re built for durability, environmental factors like exposure to chemicals or extreme temperatures still play a critical role in choosing the right material construction – typically metal or high-strength plastic – that will offer optimal performance under specific conditions.
How Do I Choose An Air Regulator?
Choosing an air regulator involves several considerations to ensure optimal performance in your system. Air regulators are vital components for controlling pressure in compressed air systems, ensuring tools and processes operate efficiently and safely. Understanding your specific needs is the first step toward selecting the right regulator.
Assess Your Application Requirements: Different applications require varying levels of precision and flow rates. For high-precision applications where even slight pressure fluctuations can cause problems, precision regulators are ideal. These are designed to maintain a consistent output pressure even when input pressure and flow rates vary.
Consider the Required Flow Rate: The flow rate needed by your application significantly influences the size and type of regulator you should choose. A regulator too small for your required flow rate can introduce unnecessary restrictions, reducing efficiency. Each regulator has a maximum flow capacity; make sure your chosen model meets or exceeds your application’s demands.
Evaluate Operating Environment Conditions: The environment where the regulator will be installed plays a crucial role in selection. For harsh environments with exposure to chemicals or extreme temperatures, it’s essential to choose regulators constructed with materials resistant to those conditions.
Filtering Needs: If your system requires clean air free from particulates and moisture, consider integrating a filter regulator—a combination unit that filters incoming air before regulating pressure. This option simplifies installation and maintenance while ensuring clean, dry air for sensitive pneumatic equipment.
Adjustability and Ease of Maintenance: Look for regulators that offer easy adjustability to allow fine-tuning of pressure settings according to operational requirements. Additionally, models designed for easy maintenance can reduce downtime and keep systems running smoothly.
What Type Of Regulator Is Used For Compressed Air?
The most commonly used type of air regulator for compressors is the General-Purpose Regulator. This type of regulator is versatile and suitable for a wide range of applications, providing basic control of air pressure for tools and equipment.
General-purpose regulators are designed to be compatible with most compressed air systems, making them a popular choice for both industrial and DIY applications where precise pressure control is not critical. They offer a good balance between performance, reliability, and cost, making them an excellent choice for general use in compressed air systems.

Can Air Pressure Regulators Be Used In High-Temperature Environments?
No,The most standard air pressure regulators are designed to operate efficiently within a certain temperature range, which typically covers most ambient working conditions.
However, when dealing with applications subjected to elevated temperatures, it is essential to consider specialized air pressure regulators crafted for high-temperature environments. These regulators are specifically engineered with materials that can withstand higher thermal stress without compromising their performance or integrity. The construction often involves the use of heat-resistant seals and diaphragms, as well as robust metal bodies that do not deform or degrade under high temperature.
Before selecting an air regulator for a high-temperature application, it’s important to consult the specifications provided by the manufacturer. These specifications include the maximum operating temperature, which indicates the upper temperature limit that the regulator can handle without failure. Opting for a regulator designed to meet or exceed your specific temperature requirements ensures reliable performance and helps prevent premature wear or failure.
In Conclusion
In conclusion, understanding the different types of air regulators is crucial for selecting the right one to ensure efficiency and safety in various pneumatic applications.
Discover more about how choosing the appropriate air regulator can optimize your systems. Reach out to our team for expert guidance tailored to your specific needs.