What are the parts of a solenoid valve
A solenoid valve is an electromechanically operated valve that is commonly used to control the flow of a fluid or gas. The valve is actuated by an electric current through a solenoid, which is essentially a type of electromagnet.
Understanding the various components of a solenoid valve is essential for selecting the right valve for your application and troubleshooting any issues that may arise. Join us as we delve into the intricacies of each part, unveiling their functions and how they coalesce to manage precise flow control in countless industrial processes.

What is a Solenoid Valve?
A solenoid valve is an electromechanically operated valve commonly used to control the flow of liquid or gas. The foundation of its operation lies in the solenoid, which is a coil wound into a tightly packed helix. When electrical current passes through this coil, it generates a magnetic field that actuates a plunger within the valve body. This action either opens or closes the valve, depending on the design and application requirement.
The basic function of a solenoid valve is to control fluid flow; however, this simple description belies the complexity and precision with which it executes this task. Such valves are integral components in applications ranging from household appliances to large industrial machinery, enabling sophisticated control over fluid dynamics with simple electrical inputs.
What Does a Solenoid Valve Consist Of?
A solenoid valve is an electromechanically operated valve that controls the flow of fluid or gas. It consists of several integral components that work together to ensure its proper function.
Component | Function |
---|---|
Inlet Port | Connection point for incoming fluid |
Outlet Port | Connection point for outgoing fluid |
Spring | Returns plunger to default position when de-energized |
Plunger | Moves to open/close valve under magnetic influence |
Armature Tube | Ensures smooth plunger movement; aligns with coil |
Seal | Prevents leaks; varies based on media specifications |
Orifice | Flow control opening; sized for rate capacity |
Shading Rings | Minimize noise and vibration from electromagnetic force |
Valve Body | Contains all parts & withstands operational pressures |
Lead Wires | Electrical conductors connecting power supply to solenoid coil |

Inlet Port
The inlet port on a solenoid valve is a critical component, serving as the entry point for the medium that is to be controlled—whether it be air, water, oil, or another fluid. This port is typically threaded to facilitate secure connection to piping systems where the flow originates. Constructed with precision, the inlet port must ensure a tight seal to prevent leakage and maintain system pressure. It works in conjunction with other parts of the solenoid valve, such as the seal and orifice, which will be discussed in their respective sections.
Outlet Port
The outlet port of a solenoid valve is integral to its functionality, serving as the exit path for fluid or gas after it has been controlled by the valve’s operation. This port is designed to facilitate the flow away from the valve, allowing the medium to continue on its designated route within an application such as a hydraulic system or pneumatic circuit.
Solenoid Coil
The solenoid coil is an essential component of a solenoid valve; it serves as an electromagnet when electric current passes through it. The coil consists of a wire, typically copper, wound around a hollow form or bobbin, creating the magnetic field necessary to actuate the valve’s plunger mechanism. When activated by electrical power, the solenoid coil generates a concentrated magnetic force that pulls on the ferromagnetic plunger attached to the valve stem. This action either opens or closes the valve depending on its default state—normally open (NO) or normally closed (NC).
To ensure optimal performance and durability, solenoid coils are often encapsulated in high-strength resin and housed within a protective casing to prevent damage from environmental factors like dust, moisture, and temperature extremes. Manufacturers design the coil to be compatible with different voltages and currents to cater to various application needs and ensure reliable operation under specific electrical conditions.
Spring and Plunger
The spring and plunger assembly is an essential component of a solenoid valve, ensuring reliable operation by governing the movement of the valve. The spring, typically made from a robust metal, maintains pressure that keeps the valve in its default position, either closed or open. When electricity flows through the coil, creating a magnetic field, the plunger – often a cylindrical piece of ferromagnetic material – is compelled to move within the armature tube. This action overcomes the spring’s resistance and induces state changes in the valve from open to closed or vice versa upon de-energization.
The plunger’s precision in alignment and movement directly affects the sealing performance of the valve when it engages with an orifice to stop fluid flow. Additionally, it must retract smoothly when the coil is de-energized to allow fluid to pass once more. Ensuring a resilient fit between these elements minimizes wear and prolongs their lifespan under repeated cycling conditions.

Armature Tube
The armature tube is cylindrical in shape and houses the moving parts of the solenoid, such as the plunger and spring. Made from a ferromagnetic material, usually stainless steel, it serves as a guide for the plunger to move in a linear direction when magnetic force is applied.
During operation, when the solenoid coil is energized, it creates a magnetic field that pulls the plunger into the armature tube. The precision with which this tube is manufactured directly affects the response time and sealing reliability of the valve. It must ensure smooth movement without detracting from the magnetic forces at play.
Inside this tube, there is typically some clearance between its inner surface and the plunger to allow for free movement. However, it must be tight enough to maintain proper alignment and minimize leakage of fluid or gas. Besides guiding the movable parts, the armature tube also acts as a magnetic flux conductor, enhancing efficiency.
Seal
The seal within a solenoid valve serves a critical function by preventing the leakage of media between the various internal components and external environment. It ensures that the inlet and outlet ports are securely separated when the valve is in a closed state, maintaining system integrity and pressure. Seals are typically made from robust materials like Nitrile, Viton™, PTFE, or EPDM, which offer varying levels of resistance to temperature, chemicals, and wear. Moreover, their composition is carefully chosen based on the specific application requirements to enhance durability and performance. In operation, seals must provide an effective barrier while enduring cycles of engagement and disengagement as the solenoid activates or deactivates. The precise fitment of these seals is paramount in guaranteeing that they can withstand both dynamic and static pressures without degradation over time.
Orifice
The orifice functioning as the passageway through which the controlled fluid flows. It is precisely machined to regulate the flow rate and maintain consistent operation when the valve transitions from open to closed states or vice versa. The size of the orifice determines the maximum flow rate of the fluid; thus, it is carefully selected based on application requirements regarding fluid type and pressure. Fit for purpose, the orifice works in conjunction with the seal, opening and closing under electromagnetic actuation to either allow or prevent fluid passage.
Shading Rings
Shading rings in solenoid valves are designed to prevent or minimize the buzzing or chattering noise traditionally associated with AC solenoids. These rings are typically composed of a magnetic material, often copper, that is fitted around or inside the solenoid’s core tube. Their key function is to reduce the electromagnetic vibrations that occur when the alternating current operates, thereby providing a smoother transition as the valve opens and closes.
The positioning of shading rings is crucial for their effectiveness; they must be located at a strategic point on the armature (the movable part of the core) where they can counteract the residual magnetism caused by the inherent nature of AC. By doing so, shading rings ensure stable operation of the valve under various electrical conditions without disruptive noise and wear on the moving parts.
Valve Body
The valve body of a solenoid valve is acting as the primary enclosure that houses the internal parts needed for operation. It is responsible for withstanding both the mechanical stresses exerted by the flow of media and ensuring that no leakages occur. The configuration of the valve body can vary substantially between different types of solenoid valves. For instance, in indirect (pilot) operated solenoid valves, the valve body includes additional chambers and pathways necessary for utilizing system pressure to assist in operating the valve. Alternatively, semi-direct operated solenoid valves feature design adaptations allowing them to function effectively under a low differential pressure situation.
Valve bodies are usually constructed from robust materials such as brass, stainless steel, or plastic, depending on the application requirements including chemical compatibility, pressure ratings, and temperature ranges they must endure. Ultimately, the specific design of a solenoid valve’s body aids in defining its operational capabilities and suitability for various industrial or commercial applications.
Lead Wires
The lead wires of a solenoid valve are critical electrical components that facilitate the supply of power to the solenoid coil. These wires must be correctly sized for electrical load and insulated to prevent any short-circuiting or electrical hazards. The material used for lead wires often needs to possess high thermal and electric conductivity, such as copper, but equally important is the quality of insulation which guards against degradation over time due to heat, chemicals, or abrasion.
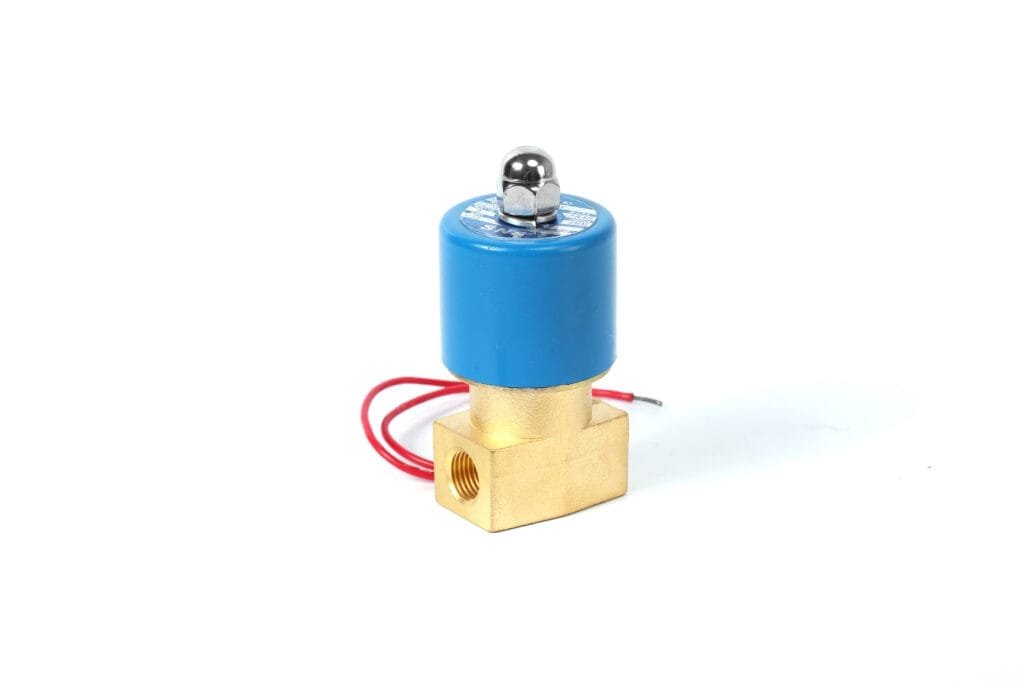
The Design of the Valve Body Varies Between Different Solenoid Valve Types
The valve body of a solenoid valve, while fundamental to its function, is subject to variations in design that are necessary to accommodate different operational modes and applications. These variations primarily involve the way in which the valve body manages flow paths within the valve.
Solenoid Valve Type | Operational Principle | Flow Rate | Pressure Differential Requirement |
---|---|---|---|
Indirect Operated | Requires pilot orifice; relies on fluid power | Moderate-to-large | Required; must have sufficient differential |
Semi-direct Operated | Combines direct and indirect features; uses plunger | Large | Zero-to-low; operates without differential |
Direct Acting | Uses magnetic field for movement control | Small | Not required; operates independently of fluid pressure |
Indirect (Pilot) Operated Solenoid Valves
Indirect operated solenoid valves, also known as pilot operated valves, incorporate a design that leverages the differential pressure of the medium across the valve to function effectively. These types of solenoid valves consist of two chambers separated by a diaphragm or piston, where the upper chamber is connected to the inlet port through a pilot orifice. The working principle relies on an electromagnetic field generated by the solenoid coil which actuates a small pilot valve integrated within the assembly.
When de-energized, this pilot valve remains closed, allowing pressure to build up in the upper chamber through the pilot orifice and keeping the main orifice closed due to pressure differential. Once energized, the solenoid coil lifts the plunger attached to the pilot valve off its seat, relieving pressure from above the diaphragm or piston. Consequently, process media pressure at the inlet port overcomes resistance and opens up pathways between inlet and outlet ports for flow.
This configuration requires less energy as compared with direct acting valves since it does not directly lift against full line pressure. The effectiveness of an indirect operated solenoid valve is heavily reliant on having sufficient differential pressure; therefore, they may not operate efficiently under low-pressure conditions.
Semi-Directed Operated Solenoid Valves
A semi-directed operated solenoid valve combines the principles of direct and indirect operation. These valves are designed to handle medium flow rates and are generally more tolerant of impurities within the fluid than their direct-acting counterparts, making them suitable for a range of applications that demand reliability under less strict filtering conditions.
The unique characteristic of a semi-directed operated solenoid valve is its utilization of both an orifice and a smaller pilot orifice within the design. During operation, when the coil is energized, it creates a magnetic field that lifts the plunger linked to the main orifice seal against the force exerted by the spring. Simultaneously, fluid pressure helps open the smaller pilot orifice. This dual-action allows for better control over fluid flow even at lower pressures compared to solely direct-operated valves.
A notable feature about these valves is that they require some differential pressure across the inlet and outlet ports to function optimally, although typically less than what would be necessary for fully indirect operated valves. The balance between utilizing system pressure and electromagnetic force provides operational flexibility for varying pressure systems.
In conclusion
In conclusion, a solenoid valve is an intricate device comprising of an electromagnetic solenoid coil, a plunger, a spring, the valve body itself, and various seals and orifices that work together to control the flow of fluids in numerous industrial and domestic applications.
To ensure proper functionality and longevity of your equipment, we recommend choosing high-quality solenoid valves tailored to your specific needs. Contact us for personalized assistance in selecting the right components for your systems or to learn more about our range of solenoid valves designed for precision and reliability.