What Are the Parts of Hydraulic Cylinder
Hydraulic cylinders are essential components in many machines, but do you know what makes them work?
In this blog post, we’ll break down the key parts of a hydraulic cylinder and explain their functions.
By the end, you’ll have a clear understanding of how these powerful devices operate and why each component is crucial.
Cylinder Body
The cylinder body is main structural component of a hydraulic cylinder, consisting of the cylinder barrel, end caps (cylinder heads), and the cylinder base or gland. These parts work together to contain the hydraulic fluid, support the piston and rod, and facilitate the linear motion of the cylinder.
Cylinder Barrel
The cylinder barrel is the cylindrical tube that forms the main body of the hydraulic cylinder. It is typically made from high-strength materials such as steel or aluminum, with a precision-machined inner surface to ensure a smooth and leak-free interface with the piston and seals.
The barrel’s inner diameter determines the piston’s size and the cylinder’s force capacity, while the wall thickness is designed to withstan high pressures of the hydraulic fluid. The outer of the barrel may have features such as mounting points, ports, or fins for heat dissipation.
End Caps (Cylinder Head)
End caps, also known as cylinder heads, are the components that seal the ends of the cylinder barrel, allowing the hydraulic fluid to be contained and pressurized. They are typically made from the same material as the barrel and can be attached via threading, welding, or bolts.
The end caps have ports that allow hydraulic fluid to enter and exit the cylinder, as well as provisions for mounting the cylinder to the machine structure.
In some designs, one end cap may be integral with the cylinder barrel. The end caps also support the piston rod and the sealing components, such as rod seals and wipers.
Cylinder Base or Gland
The cylinder base, also referred to as the gland, is the portion of the cylinder body that seals the piston rod at end of the cylinder where the rod extends. Its primary function is to prevent hydraulic fluid leakage while allowing the piston rod to move smoothly in and out of the cylinder.
The gland is typically designed with a bore that matches the diameter of the piston rod, and it houses sealing components such as rod seals, bushings, and bearings.
The gland may be threaded or bolted to the cylinder barrel, and it often has features for mounting the cylinder to the machine structure or load.
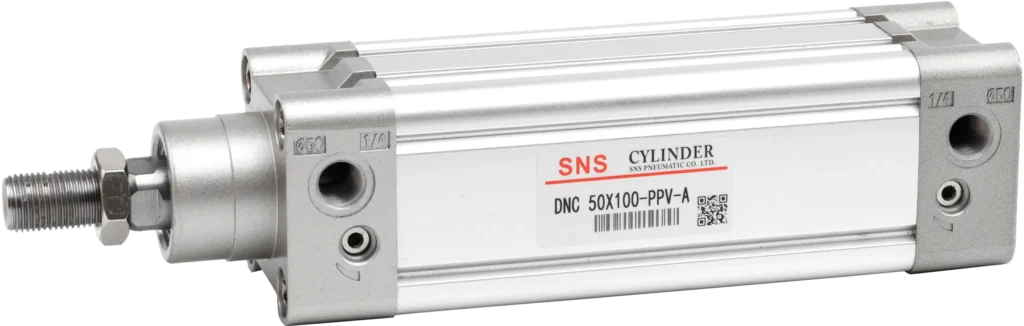
Piston Assembly
The piston is a critical component of a hydraulic cylinder, consisting of the piston and the piston rod. This assembly is responsible for converting the hydraulic fluid pressure into linear mechanical forced motion.
Piston
Piston is cylindrical component that slides back and forth within the cylinder barrel, driven by the pressure of the hydraulic fluid. It is typically made from high-strength materials such as steel or aluminum, with a precision-machined outer surface to ensure a tight seal with the piston seals.
The piston has grooves or channels machined into its circumference to accommodate the piston seals, which prevent fluid leakage between the two sides of the piston. In some designs, the piston may also have a wear band or coating to reduce friction and wear against the cylinder wall.
The face of the piston, which comes into contact with the hydraulic fluid, may be flat or contoured to optimize fluid flow and pressure distribution.
Piston Rod
The piston rod is a cylindrical rod that is attached to the piston and extends through one end of the cylinder barrel. Its primary function is to transmit the linear force and motion generated by the piston to the external load or mechanism.
Piston rods are typically made from high-strength, corrosion-resistant materials such as chrome-plated steel or stainless steel to withstand the high forces and harsh operating environments. The rod’s diameter is determined by the required load capacity and buckling resistance, while the length is based on the desired stroke of the cylinder.
The end of the piston rod that extends outside the cylinder is often machined with features such as threads, flanges, or clevises for attaching to the load or machine structure.
Sealing System
The sealing system in a hydraulic cylinder is essential for preventing fluid leakage, maintaining pressure, and ensuring efficient operation. The two main types of seals in a hydraulic cylinder are piston seals and rod seals.
Piston Seals
Piston seals are responsible for sealing the gap between the piston and the cylinder barrel, preventing fluid leakage from one side of the piston to the other. They are typically made from elastomeric materials such as nitrile rubber, polyurethane, or Teflon, and are designed to withstand high pressures, temperatures, and wear.
Piston seals come in various designs, such as O-rings, U-cups, or composite seals. The seals are installed in grooves machined into the piston’s circumference and are compressed against the cylinder wall to create a tight seal.
Rod Seals
Rod seals are located in the cylinder base or gland and are responsible for sealing the interface between the piston rod and the cylinder body. Their primary function is to prevent hydraulic fluid from leaking out of the cylinder along the rod, as well as to prevent contaminants from entering the system.
Rod seals are typically made from similar materials as piston seals and come in various designs, such as U-cups, V-packing, or wiper seals. They are installed in the gland and are compressed against the piston rod to create a dynamic seal.
Rod seals must be designed to withstand not only high pressures but also the sliding motion and potential side loads of the piston rod. In addition to the main rod seal, cylinders often incorporate secondary seals, such as wipers or scrapers, to remove contaminants from the rod surface as it retracts into the cylinder.
Fluid Connections
Fluid connections allow the hydraul fluid to enter and exit the cylinder, enabling the piston to move and generate force. The two main types of fluid connections in a hydraulic cylinder are ports and fittings.
Ports
Ports are openings or passages in the cylinder body, typically located in the end caps or the cylinder base, that allow hydraulic fluid to flow in and out of the cylinder. The number and location of the ports depend on the type of cylinder and its application.
In a single-acting cylinder, there is typically one port that allows fluid to enter and push the piston in one direction, while a spring or external force returns the piston to its original position.
In a double-acting cylinder, there are two ports, one for extending the piston and another for retracting it. Ports are usually threaded to accommodate fittings and are designed to withstand high pressures without leakage. The size of the ports is determined by the required flow rate and pressure drop of the hydraulic system.
Fittings
Fittings are mechanical components used to connect the hydraulic lines or hoses to the cylinder ports, allowing fluid to flow in and out of the cylinder. Some common types of fittings used in hydraulic cylinders include:
- Straight thread fittings (NPT, BSPT): These fittings have a tapered thread that creates a seal when tightened, and are commonly used in low to medium-pressure applications.
- Parallel thread fittings (SAE, BSPP): These fittings have a straight thread and rely on an additional seal, such as an O-ring or a bonded seal, to prevent leakage. They are often used in high-pressure applications.
- Flare fittings (JIC, SAE 45-degree): These fittings have a cone-shaped end that mates with a corresponding flare on the hydraulic line, creating a metal-to-metal seal. They are commonly used in high-pressure, high-vibration applications.
- Quick-disconnect fittings: These fittings allow for fast and easy connection and disconnection of hydraulic lines without tools, making them ideal for applications that require frequent cylinder changes or maintenance.
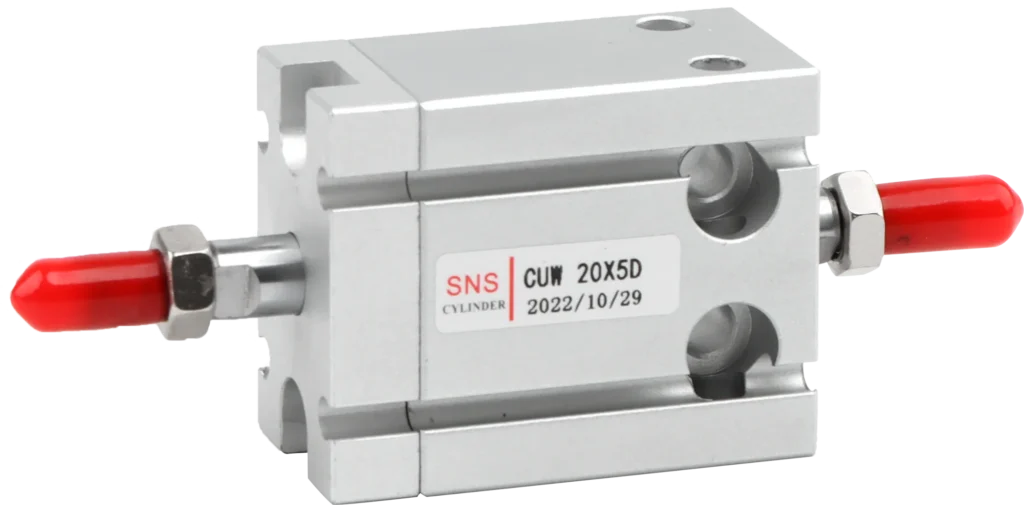
Additional Components
In addition to the main components of a hydraulic cylinder, such as the cylinder body, piston assembly, and sealing system, there are several additional components that can enhance the performance, safety, and versatility of the cylinder. Two important additional components are cushions and mounting components.
Cushions
Cushions are devices installed in hydraulic cylinders to decelerate the piston near the end of its stroke, preventing abrupt stops and reducing the impact forces on the cylinder and the connected machinery.
Cushions work by restricting the flow of hydraulic fluid through a small orifice near the end of the cylinder stroke, creating a back pressure that slows down the piston gradually.
There are two main types of cushions:
- Adjustable cushions: These cushions have a variable orifice or a needle valve that allows the operator to adjust the cushioning effect according to the specific application requirements. Adjustableions provide flexibility and can be fine-tuned to optimize the piston deceleration.
- Fixed cushions: These cushions have a fixed orifice size and provide a constant cushioning effect. They are simpler and less expensive than adjustable cushions but offer less flexibility in terms of performance tuning.
Cushions are typically installed in the end caps of the cylinder, either in the head end, the rod end, or both, on the application requirements. They may be integral to the end cap design or installed as separate components.
Mounting Components
Mounting components are the parts of a hydraulic cylinder that enable it to be attached securely to the machine structure and the load being actuated. Some common types of mounting components include:
- Flanges: Flanges are flat, circular plates with bolt holes that are attached to the end caps of the cylinder. They provide a large, stable surface for mounting the cylinder to the machine structure.
- Clevises: Clevises are U-shaped brackets with pin holes that allow the cylinder to be connected to the machine structure or the load using a pin or bolt. They provide a pivoting connection that can accommodate misalignment and are often used in mobile equipment and agricultural machinery.
- Trunnions: Trunnions are cylindrical protrusions with a hole or bore that allow the cylinder to be mounted using a or bolt. They are typically welded or bolted to the cylinder body and provide a compact, low-profile mounting solution.
- Spherical bearings: Spherical bearings are mounting components that allow the cylinder to pivot in multiple directions, accommodating misalignment and reducing bending stresses on the piston rod. They are often used in applications where the cylinder is subjected to side loads or where precise alignment is difficult to achieve.
FAQs
What Are the Main Parts of a Hydraulic Cylinder
The main parts of a hydraulic cylinder include the cylinder barrel, piston, piston rod, end caps, and seals.
What Are the Ends of a Hydraulic Cylinder Called
The ends of a hydraulic cylinder are called the capd and the rod end.
What Holds a Hydraulic Cylinder in Place
Mounting components, such as flanges, clevises, trunnions, or spherical bearings, hold a hydraulic cylinder securely in place by attaching it to the machine structure.
Does Hydraulic Cylinder Size Matter
Yes, hydraulic cylinder size matters. The size of the cylinder determines the amount of force it can generate and the speed at which it can move, which are critical factors in the performance of hydraulic systems.
Conclusion
In conclusion, understanding the parts of a hydraulic cylinder and their functions is essential for anyone working with hydraulic systems.
From the cylinder barrel and piston to the seals and mounting components, each element plays a crucial role in ensuring smooth, efficient operation.
To learn more about hydraulic cylinders and how to maintain them, visit our website or contact our expert team today.