What Is A Pneumatic Cylinder
A pneumatic cylinder is a mechanical device that converts compressed air into linear motion. It operates on the principle of pressurized air expansion, driving a piston to move within a cylindrical chamber.
Pneumatic cylinders are essential components in various industrial applications, providing efficient and reliable means for executing linear movements. Their simplicity, durability, and speed control abilities make them invaluable in machinery operation and automation processes.
What Is A Pneumatic Cylinder
A pneumatic cylinder is a mechanical device. It uses compressed air to produce force in a piston linear motion. This cylinder consists of a cylindrical tube, a piston inside the tube, and end caps. The function of these components is straightforward yet effective for various applications.
Pneumatic cylinders are diverse in their use. They can perform tasks ranging from simple movements to complex automation processes. The working principle involves converting the energy of compressed air into mechanical work through the movement of the piston.
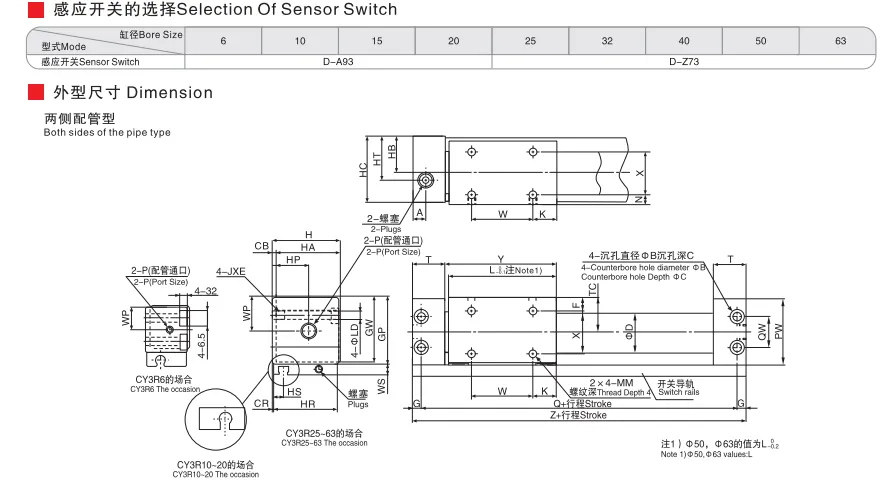
What Is The Purpose Of A Pneumatic Cylinder
A pneumatic cylinder serves as a device that converts compressed air energy into mechanical work. It provides motion and force to industrial automation applications. These cylinders are vital in machinery where precision, efficiency, and safety are paramount. Their primary function is to move a load along a linear path with speed and control.
How Does Pneumatic Cylinder Work
Pneumatic cylinders transform compressed air into mechanical energy. They use air pressure differences to create forceful movements. When compressed air enters the cylinder, it pushes against the piston. This forces the piston to move inside the cylinder barrel.
The movement of the piston transfers through the piston rod. This rod exits the cylinder and acts on an external object or mechanism. The process translates pneumatic energy into linear motion.
Components Of Pneumatic Cylinders
Cylinder Barrel
The cylinder barrel serves as the main body of a pneumatic cylinder and houses the piston and the compressed air. It is constructed from materials capable of withstanding high pressures, and its interior surface is finely finished to minimize friction, facilitating the efficient movement of the piston.
Piston
The piston is a crucial component that moves back and forth inside the cylinder barrel due to variations in air pressure. Its design ensures a snug fit within the barrel to optimize efficiency and prevent air leakage, converting the energy of compressed air into mechanical motion effectively.
Piston Rod
Connected to the piston, the piston rod extends outside the cylinder and can move in and out of one or both ends, depending on the cylinder design. The rod’s movement is the source of linear motion used to perform work or actuate machinery, making it a key component in translating pneumatic power into tangible actions.
Seals and Rings
Seals and rings are essential for maintaining the integrity of the pneumatic system by preventing air from escaping around the piston as it moves within the barrel. These components must be carefully selected to provide a tight seal while still allowing for the smooth operation of the piston, ensuring efficient performance of the cylinder.
End Caps
End caps are fitted at each end of the cylinder barrel, effectively sealing the system while also providing mounting points for the cylinder. Certain designs incorporate cushions within the end caps, which serve to decelerate the piston at the end of its stroke. This cushioning mechanism is vital for reducing the impact and wear on the cylinder, prolonging its lifespan and reliability.

Cushions
Cushions, when present, are integrated into the end caps to minimize the piston’s impact as it reaches the end of its stroke. This feature is especially important in applications where the cylinder operates at high speeds or under heavy loads, as it helps to absorb energy and reduce noise, vibration, and wear.
Types Of Pneumatic Cylinder
Single-Acting Cylinders
Single-acting cylinders apply force in one direction only. They have a single port for air to enter and exit. When air pressure increases, the cylinder extends. A spring within the cylinder retracts it when air pressure decreases.
This type of cylinder has a simple design. It’s most effective for tasks requiring straightforward push or pull actions. Due to the presence of a spring, these cylinders are typically limited in force, especially during retraction.
Double-Acting Cylinders
Double-acting cylinders use air pressure to drive motion in two directions, both extend and retract. Unlike single-acting cylinders, which rely on a spring to return to the original position, these cylinders have ports at both ends. This design allows air to enter one side for extension and the other for retraction. The result is more control over movement.
These cylinders are more powerful than their single-acting counterparts. They can exert force in pushing and pulling actions. This dual capability makes them suitable for more complex applications.
Multi-Stage, Telescoping Cylinder
Multi-stage, telescoping cylinders are complex. They consist of a series of cylindrical tubes, each smaller than the last. These tubes nest inside each other. When activated, they extend sequentially. This design allows for a long extension from a compact form.
The main advantage is their extended reach without needing the length’s space when retracted. They’re perfect for applications with limited space but require a long stroke length. Think of applications like dump trucks or applications requiring high lift but have limited storage space.
Rodless Cylinders
Rodless cylinders differ fundamentally from traditional pneumatic cylinders. They don’t have a piston rod extending outside the cylinder body. Instead, the motion is generated internally by a carriage or slider that moves within or along the cylinder tube. This design saves space and reduces the risk of bending forces on the piston rod, which can occur in long-stroke applications with conventional cylinders.
In terms of construction, these cylinders employ a variety of mechanisms to achieve linear motion without an external rod. Magnetic coupling is one common method, where an internal magnet attached to the piston moves along with an external carriage magnetically coupled to it. Another common type uses a mechanical linkage system inside the cylinder to convert compressed air power into linear motion.
The absence of a protruding piston rod makes rodless cylinders particularly suitable for tight spaces and environments where external moving parts could be problematic. This compactness and enclosed design minimize dust ingress and other environmental contaminants, potentially lengthening the cylinder’s lifespan.
Applications Of Pneumatic Cylinders
Packaging and Robotics
Pneumatic cylinders are widely utilized in packaging and robotics applications. They are responsible for moving, lifting, and positioning goods with precision, which is essential in packaging lines for various products. Their speed and accuracy also make them indispensable in the rapidly growing field of industrial robotics, where they perform tasks ranging from simple material handling to complex assembly operations.
Automotive Assembly
In the automotive industry, pneumatic cylinders are integral to assembly lines, providing the necessary force for pressing parts together, handling components during assembly, and executing precise painting tasks. Their reliability and speed enhance productivity and ensure consistent quality in automotive manufacturing processes.
Food and Beverage Processing
The food and beverage sector benefits significantly from the use of pneumatic cylinders. These devices automate critical processes such as filling, capping, and labeling, thereby increasing efficiency, ensuring hygiene, and meeting high-volume production demands while adhering to safety standards.
Pharmaceutical Production
Pneumatic cylinders are deployed in pharmaceutical clean rooms for drug production and packaging. Their compatibility with clean environments, due to their ability to operate without lubrication and their ease of cleaning, meets the rigorous cleanliness standards required in pharmaceutical manufacturing.
Construction and Mining
In construction and mining, pneumatic cylinders power equipment like jackhammers and drills. Their durability and reliability under extreme conditions make them suitable for the demanding tasks associated with these industries, where equipment must perform reliably despite dust, debris, and harsh environmental conditions.
Printing Industry
The precision offered by pneumatic cylinders is crucial in the printing industry, where they control the movement of paper and printing plates. This precision ensures high-quality printing results, crucial for maintaining the standards expected in the publishing and packaging sectors.
Textile Manufacturing
In textile manufacturing, pneumatic cylinders control fabric movement and various machine operations. Their use ensures consistent quality in fabric production by providing smooth and precise control over the textile machines, contributing to the overall efficiency of the manufacturing process.
Waste Management and Recycling
Pneumatic cylinders are employed in waste management and recycling operations to sort and process materials efficiently. Their ability to provide rapid and precise movement enables the sorting of recyclables at high speeds, enhancing the efficiency of recycling processes.
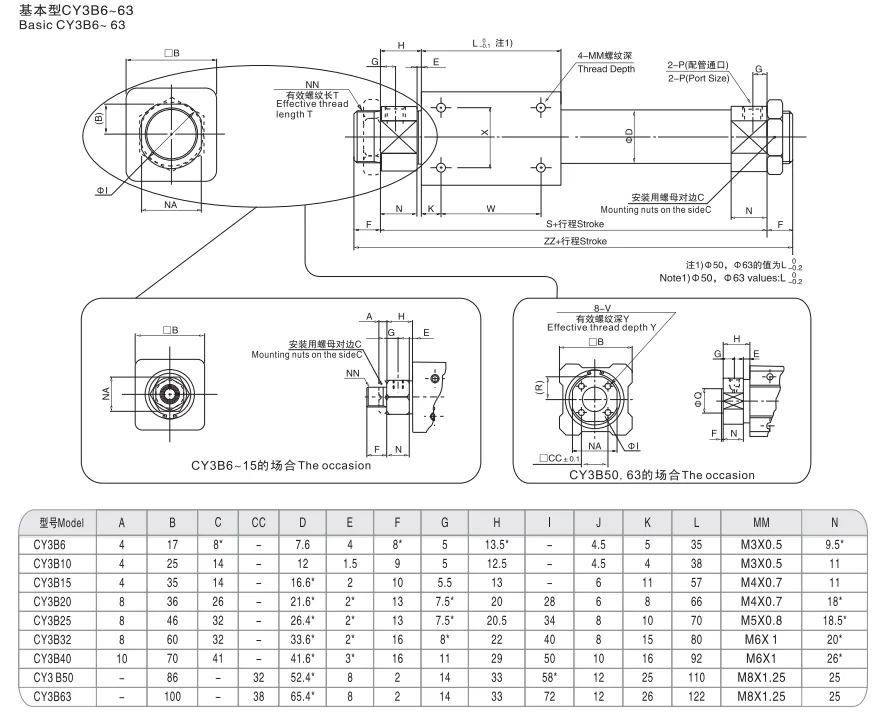
How To Select The Right Pneumatic Cylinder
Selecting the right pneumatic cylinder requires evaluating its intended application and operating conditions. Key factors include force requirements, stroke length, operating speed, and environmental considerations. Each aspect critically influences cylinder performance and longevity.
Force, Stroke Length, Speed, And Environment
Selecting the right pneumatic cylinder requires understanding several key parameters: force, stroke length, speed, and environment.
Force
The force output of a pneumatic cylinder is a fundamental aspect that determines its ability to perform work. It is essential to choose a cylinder that can provide enough force to move the load in question, taking into account not just the weight of the load but also any resistance it may encounter during operation. Calculating the required force accurately ensures that the selected cylinder can perform the intended task without being over- or under-sized.
Stroke Length
Stroke length is the measure of how far the piston inside the cylinder can travel. This parameter must be closely aligned with the requirements of the application to ensure that the full range of motion is achieved without wasting space or energy on unnecessary movement. Selecting the correct stroke length is crucial for the efficiency and effectiveness of the cylinder’s operation.
Speed
The speed at which the piston moves within the cylinder is another critical consideration. Speed control is vital to prevent damage to the load or machinery, as well as to ensure the precision of the operation. The desired speed will influence the design and choice of air flow controls and valves, making it a key factor in the selection process.
Environment
The operating environment has a significant impact on the choice of materials and seal types for a pneumatic cylinder. Environmental factors such as temperature extremes, moisture, exposure to corrosive substances, or the presence of particulate matter can all affect the performance and lifespan of a cylinder. Selecting a cylinder with appropriate materials and seals for the specific operating conditions is essential for ensuring its reliability and durability.
Cylinder Sizing
Selecting the correct size for a pneumatic cylinder is crucial for achieving optimal functionality and efficiency within its application. This decision is guided by a detailed understanding of various parameters, such as bore diameter, stroke length, air pressure requirements, and more. Below, we delve into these essential elements to provide guidance for making an informed choice.
Bore Diameter
- Impact on Force Output: The bore diameter is directly proportional to the force output of the cylinder. A larger bore diameter means the cylinder can exert more force.
- Air Consumption: It’s important to note that a larger bore also leads to higher air consumption with each cycle. To ensure efficiency, the bore size should be closely matched to the force requirements of your application.
Stroke Length
- Defining Movement Range: Stroke length specifies the maximum travel distance of the piston within the cylinder.
- Application-Specific: Choose a stroke length that aligns with the movement needs of your application, avoiding excess that could lead to larger, more costly cylinders than necessary.
Air Pressure
- Influence on Cylinder Selection: The operating air pressure available for the cylinder plays a significant role in determining the appropriate cylinder size.
- Pressure vs. Size Trade-off: Higher operating pressures can enable smaller cylinders to achieve the required force but might necessitate more durable materials, impacting overall costs.
Cylinder Type
- Single vs. Double-Acting: The choice between single-acting and double-acting cylinders affects size and operational considerations. Single-acting cylinders incorporate a spring and typically occupy more space, whereas double-acting cylinders require more intricate control systems but may be more compact for the same force output.
Load Factors
- Anticipating Variations: Consider potential fluctuations in the load that the cylinder will encounter during operation. Planning for potential increases in load ensures that the cylinder remains efficient and effective over its lifespan.
Mounting Style
- Space and Mobility Considerations: The choice of mounting style has implications for how the cylinder integrates into the system, impacting both space utilization and the mobility of the cylinder. It’s essential to select a mounting style that suits the spatial and operational constraints of your application.
Summary
By meticulously analyzing these factors—bore diameter, stroke length, air pressure, cylinder type, load factors, and mounting style—you can select a pneumatic cylinder size that not only meets the performance requirements of your application but also does so in a cost-effective and efficient manner. This careful selection process ensures that the pneumatic cylinder contributes to the overall success and sustainability of the operational system, minimizing waste and maximizing efficiency.

How To Install Pneumatic Cylinders
Step 1: Mount the Cylinder
- Choose the appropriate location for your pneumatic cylinder within the application.
- Ensure the mounting surface is flat and stable.
- Align the cylinder properly to avoid misalignment, which can cause inefficiency or damage.
- Use suitable mounting accessories like brackets or flanges to secure the cylinder.
Step 2: Connect the Air Supply
- Select the correct hoses or piping that match the cylinder’s ports.
- Make tight connections to prevent air leaks.
- If available, install an air pressure regulator in the system to control and optimize airflow.
Step 3: Lubricate (if Necessary)
- Check the manufacturer’s guidelines to see if lubrication is needed for your specific cylinder.
- If required, apply appropriate lubricant to prevent friction and wear.
Step 4: Test the Cylinder
- Begin by applying low air pressure to the cylinder.
- Gradually increase the pressure while observing the cylinder’s operation.
- Check for smooth operation and ensure there are no leaks.
Step 5: Select the Correct Fastening Method
- Use bolts and screws that are compatible with the material of the cylinder to prevent corrosion.
- Ensure all fasteners are secured properly.
What Is The Difference Between Pneumatic Cylinder And Hydraulic Cylinder
Operating Medium and Applications
- Pneumatic Cylinder: Pneumatic cylinders operate using compressed air. Their simplicity and cleanliness make them suitable for environments focused on hygiene, like food production and pharmaceutical sectors. They are also favored in applications that pose less risk for leaks.
- Hydraulic Cylinder: These cylinders function using hydraulic fluid. They can manage heavier loads, making them ideal for applications needing substantial force, such as construction equipment and heavy machinery.
Operating Pressure
- Pneumatic Cylinder: Pneumatic systems usually operate at lower pressures, typically up to 120 psi, which can be a disadvantage for tasks requiring high force.
- Hydraulic Cylinder: In contrast, hydraulic systems operate under much higher pressures, often exceeding 2,000 psi, highlighting their suitability for high-force tasks.
Responsiveness and Cost
- Pneumatic Cylinder: Due to the compressibility and control ease of air, pneumatic cylinders often have quicker response times, making them preferable in rapid sequencing operations. They usually have lower installation and maintenance costs due to the free and readily available air, reducing operational expenses.
- Hydraulic Cylinder: On the other hand, hydraulic cylinders may have slower response times and often come with higher initial investments due to their complex components and the required fluids.
Environmental Impact
- Pneumatic Cylinder: Pneumatic systems have an environmental advantage due to the absence of potentially harmful fluids that could contaminate surroundings.
- Hydraulic Cylinder: Conversely, hydraulic systems can pose risks of environmental contamination due to the potential leak of hazardous hydraulic fluids.
What Is Another Name For A Pneumatic Cylinder
A pneumatic cylinder is also known as an air cylinder. This alternative name highlights its operation mechanism, where air is the primary source of power. The term “air cylinder” clarifies that the device utilizes compressed air to create linear motion or force, distinguishing it from other types of cylinders that might use hydraulic fluid or electricity for operation. In various industries and applications, referring to pneumatic cylinders as air cylinders is common practice, especially in contexts emphasizing their reliance on air for functionality. The simplicity of the term “air cylinder” contributes to its widespread acceptance and usage among professionals and enthusiasts alike in the field of pneumatics.
In Conclusion
Pneumatic cylinders are essential components in numerous industries, providing a reliable and efficient means of converting compressed air into mechanical motion for varied applications.
To learn more about how pneumatic cylinders can enhance your operational efficiency or to explore our range of high-quality pneumatic systems, we invite you to contact our team of experts today. Let us help you select the perfect solution tailored to your specific needs.