What Is Air Compressor Regulator
An air compressor regulator is a device that controls the pressure of air released from an air compressor to ensure it is at a safe and usable level. It allows for the adjustment of air output pressure to match the requirements of the tool or application being used.
Understanding how to manage and adjust your air compressor’s output is crucial for both safety and efficiency. The following discourse will elaborate on the importance, functionality, and benefits of using an air compressor regulator in various applications.
What Is Air Compressor Regulator
An air compressor regulator is a device that controls the pressure of air output from an air compressor. Its primary function is to provide consistent pressure to pneumatic tools and equipment, despite fluctuations in the compressor’s tank pressure. It achieves this by automatically adjusting the airflow to maintain a set pressure level, which users can select according to their specific needs.
The regulator is essential for both the performance and lifespan of air-powered tools. By ensuring a stable flow of air at the correct pressure, it prevents damage that can occur from over-pressurization while optimizing tool efficiency and effectiveness.
Air compressor regulators are found on nearly all compressors and are typically located at the point where the air hose connects to the compressor. They consist of several key components: an adjustment knob for setting desired pressure, a gauge showing the current or set pressure level, and a valve that maintains even flow and pressure.

What Does The Air Regulator Do?
The primary function of an air regulator is to ensure that the output pressure remains stable regardless of fluctuations in the input pressure from the compressor tank. This stability is vital for operating pneumatic tools efficiently and safely, as excessive pressure can lead to tool damage or personal injury.
By maintaining a constant output pressure, air regulators also contribute to energy savings. They help minimize wasted compressed air by preventing the system from operating at higher pressures than necessary. This efficiency can significantly reduce energy consumption and operating costs over time.
Moreover, using an air compressor regulator enhances tool performance and lifespan. Many pneumatic tools have specific pressure requirements for optimal operation. Providing too much or too little pressure can result in poor performance, increased wear, or even failure of the tool.
Components Of An Air Compressor Regulator
The components of an air compressor regulator are crucial for its operation. Each part plays a significant role in ensuring precise control over air pressure, which is essential for the efficient functioning of pneumatic tools.
Adjustment Knob
The functionality of the adjustment knob is straightforward. By turning the knob, users can increase or decrease the air pressure according to their needs. This adjustability is vital in applications where specific air pressures are required for different tasks.
Gauge
The gauge on an air compressor regulator serves a critical function. It visually indicates the air pressure level. This can either be the setting you’ve selected or the pressure that’s actually being delivered to your tools at any moment. Precision in monitoring air pressure is crucial for both safety and efficiency during operation.
Air pressure gauges consist of a dial and a needle. The dial is usually marked with numbers and lines to denote specific pressure values, measured in PSI (pounds per square inch) or bar. The needle moves along this dial to indicate real-time pressure levels. For operators, this visual feedback is indispensable. It allows for immediate adjustments, ensuring that the air compressor operates within safe and optimal parameters.
Valve
The valve modulates air flow and ensures pressure constancy. This component is vital for achieving precise air pressure delivery.
An air regulator’s valve operates dynamically to balance changing demands. It adjusts to maintain the user’s set pressure level despite fluctuations in input pressure or demand.
Valves are designed for quick response. They alter the passage size for airflow based on required adjustments, enabling immediate adaptation to maintain steady pressure.
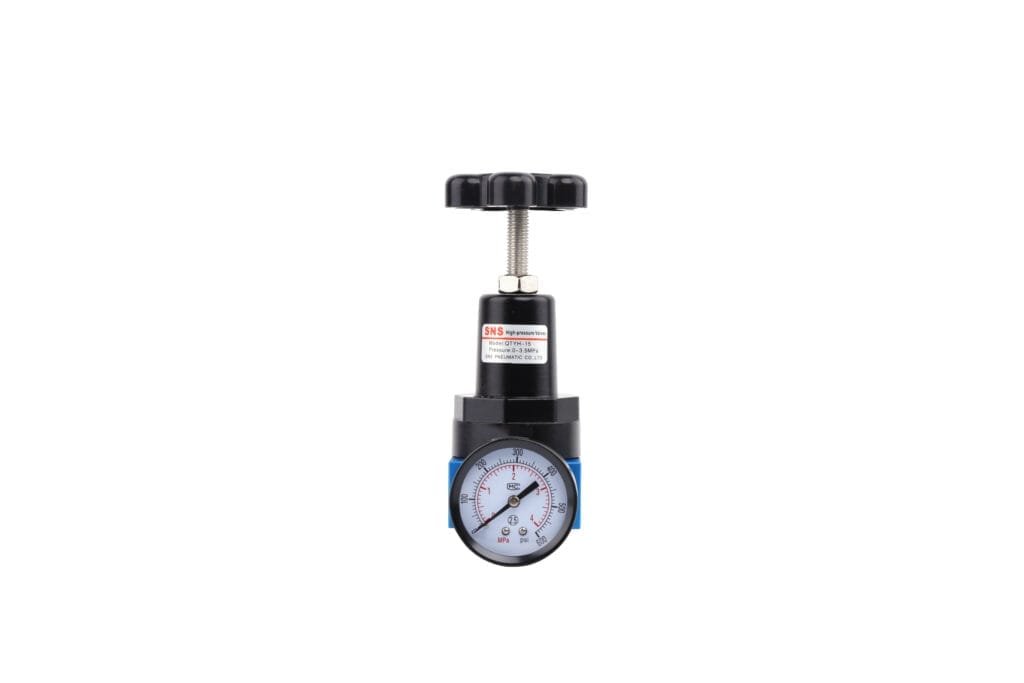
How Air Compressor Regulators Work
The process begins when air enters the regulator. At this point, the internal mechanism, controlled by the adjustment knob, sets the desired pressure level. This knob’s turning increases or decreases tension on a spring that is connected to a valve inside the regulator.
This valve is the core of how regulators manage air flow. When the downstream pressure drops below the set level, the valve opens more to allow more air through, raising the pressure. Conversely, if the downstream pressure exceeds the set level, it closes slightly, reducing airflow and lowering pressure.
This dynamic adjustment keeps the output pressure within a narrow range. The gauge attached to the regulator provides real-time feedback on this process by displaying current pressure levels.
Air compressor regulators ensure that only the required amount of compressed air is used for an operation. By providing precise control over air output, they reduce waste and improve energy efficiency.
Types of Air Compressor Regulators
Air compressor regulators are crucial for managing and maintaining the desired level of pressure in pneumatic tools. They fall into two primary categories: single-stage and dual-stage regulators.
Single-Stage Regulator
A single-stage regulator excels in situations where a consistent pressure output is vital. Its design aims at applications where fluctuations in pressure are undesirable or could lead to operational issues. The regulator maintains a steady flow, ensuring that the output pressure remains unchanged over time despite varying demands or input pressures.
The simplicity of the single-stage regulator contributes to its widespread use. It lacks the complexity of dual-stage regulators, making it not only more straightforward to operate but also easier to maintain and repair if needed. This type of regulator adjusts the air pressure from the compressor to a stable and continuous level suitable for various tools and applications that require a constant supply of air at the same pressure.
Dual-Stage Air Compressor Regulators
Dual-stage air compressor regulators employ two distinct stages for controlling air pressure. This design allows for more accurate adjustments. First, the incoming high-pressure air is reduced to a lower pressure in the first stage. Then, the second stage further refines this pressure to the precise level needed by the user. Each stage operates independently, enhancing precision.
This type of regulator is particularly valuable in settings where variable pressures are essential. The ability to finely tune pressures facilitates optimal operation across diverse tools and processes. The dual-stage setup excels in scenarios demanding meticulous control over pneumatic tool supply lines or in industrial applications with specific pressure needs for different tasks.

Benefits of Using Air Compressor Regulators
Improved Efficiency
Air compressor regulators enhance efficiency. They allow precise control of air pressure, leading to optimal operation of pneumatic tools. Correct pressure settings ensure tools work at their best, without using excess energy or suffering from wear due to overpressure. This precise control minimizes waste and maximizes performance.
Protection of Pneumatic Tools
Air compressor regulators play a crucial role in protecting pneumatic tools. These devices adjust and maintain a consistent air pressure, which is vital for the optimal operation of pneumatic tools. Fluctuations in air pressure can lead to inconsistent performance or even damage to these tools. Ensuring a steady supply of regulated air extends the lifespan of pneumatic equipment by preventing wear and tear caused by excessive pressure.
Cost Savings on Energy Consumption
Air compressor regulators contribute to significant energy cost savings. They optimize the air compressor’s output to meet precisely the demand of the tools or applications in use. Efficient use equals less energy waste. Excessive pressure not only wastes energy but also shortens equipment life.
Adjusting to the exact required pressure reduces energy consumption by preventing over-pressurization. Over-pressurization leads to unnecessary energy use. By maintaining optimal pressure levels, compressors operate within their most efficient ranges, using less power to generate the needed air pressure.
How Do I Know If My Air Pressure Regulator Is Bad?
Identifying A Faulty Air Pressure Regulator
Detecting a malfunctioning air pressure regulator involves observing specific symptoms that signal its failure. Consistent issues in air pressure, such as inability to maintain the set pressure, indicate a problem. A notable drop or spike in pressure beyond the desired setting points towards regulator failure.
Performance Fluctuations
Fluctuating performance of pneumatic tools connected to the compressor often stems from irregular air pressure. Tools operating erratically or not achieving optimal performance may be experiencing varied air delivery due to a failing regulator.
Audible Signs
Listen for unusual noises emanating from the regulator area. Hissing sounds can suggest internal leaks or damage within the regulator mechanism, pointing to compromised integrity and functionality.
Visual Inspections
Regular inspections can reveal physical damage on the regulator body, such as cracks or corrosion. These physical signs often precede functional failures and should prompt further investigation or replacement.
Pressure Gauge Reading
An unchanging pressure gauge reading despite adjustments on the knob is a clear indicator of a malfunctioning regulator. The gauge should respond to changes made through the adjustment knob; if it doesn’t, this signals an issue within the regulating mechanism.
By closely monitoring these signs, identifying a bad air pressure regulator becomes straightforward, allowing for timely maintenance or replacement to ensure continuous and efficient air compressor operation.

What Is The Difference Between a Pressure Regulator and an Air Regulator?
Understanding the Distinction
The terms “pressure regulator” and “air regulator” are often used interchangeably, but there are nuanced differences between them. A pressure regulator is a broad category of devices designed to control the pressure of fluids or gases in various applications. Meanwhile, an air regulator is a specific type of pressure regulator that exclusively manages air pressure.
Specificity in Application
An air regulator focuses solely on controlling the pressure of compressed air in systems such as air compressors, pneumatic tools, and other air-powered equipment. On the other hand, pressure regulators can manage water, oil, gas, or any other fluid besides air, making them applicable in a wider range of industries including water treatment, oil and gas production, and chemical manufacturing.
Functional Differences
Both devices operate on similar principles—reducing incoming pressure from a source to a desired level usable by downstream equipment. However, their design might differ based on the medium they control. For example, materials used in an air regulator need to be suitable for compressed air exposure which may not require the same level of resistance to corrosion or chemical reactions as those used in general pressure regulators dealing with aggressive fluids.
Considerations for Selection
Choosing between these two depends largely on the medium you intend to regulate. If your application involves controlling compressed air for tools or processes, an air compressor regulator is requisite. Conversely, if you’re managing different types of fluids
Do You Need a Regulator for an Air Compressor?
Yes, a regulator is essential for an air compressor. It serves multiple critical functions that contribute to the optimal performance and longevity of pneumatic tools and systems. A regulator helps in maintaining consistent pressure levels as demanded by various tools and applications. Without a regulator, there is a risk of over-pressurizing tools, which can lead to their damage or premature failure.
Can Any Regulator Fit All Types Of Air Compressors?
No, not all regulators can fit every type of air compressor. Air compressors come in various sizes and specifications, leading to differences in their requirements for regulators.
In Conclusion
In essence, an air compressor regulator is a crucial component designed to maintain a consistent pressure output, ensuring optimal performance and safety.
Discover the range of air compressor regulators we offer to enhance your system’s efficiency and reliability. Take the first step towards optimizing your operations by exploring our selection today.