What is an air filter regulator?
An air filter regulator is a vital component in pneumatic systems, designed to perform two crucial functions: filtering airborne particles and moisture from compressed air and regulating the air pressure to ensure consistent, optimal performance of pneumatic tools and equipment. By integrating these dual functionalities, an air filter regulator enhances the reliability and efficiency of pneumatic systems across various industrial applications.
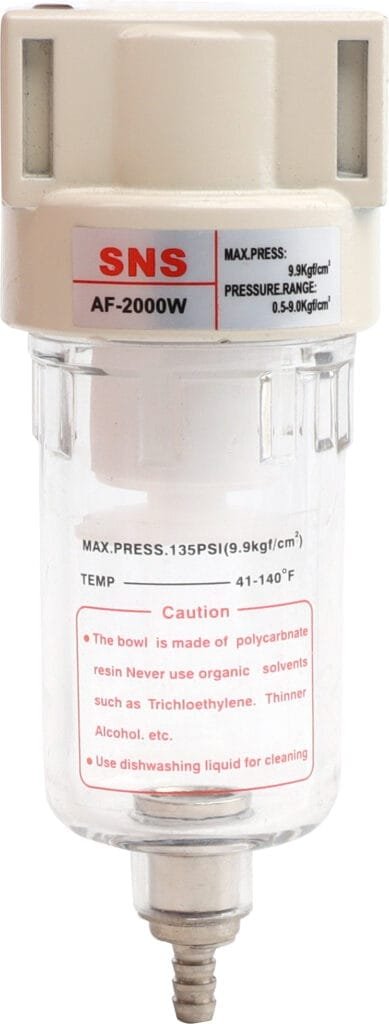
What is an Air Filter Regulator?
An air filter regulator is a specialized device commonly utilized in various pneumatic systems. Its primary function is to clean and regulate the pressure of the air flowing through these systems, ensuring optimal performance and prolonging equipment lifespan. The device integrates two critical components: an air filter and a pressure regulator, into a single compact unit. This integration facilitates the removal of particulate contaminants like dust, rust, and moisture from the air stream, while also providing precise control over the downstream air pressure.
Air filter regulators are pivotal for maintaining the integrity and efficiency of pneumatic tools, actuators, and other equipment that rely on compressed air for operation. By delivering clean, controlled air, these devices help to minimize wear and tear on machinery parts caused by impurities in the air supply or erratic pressure levels. Moreover, they play a significant role in enhancing operational safety by preventing potential malfunctions associated with contaminated or poorly regulated compressed air.
Designed to cater to a wide range of industrial applications, these devices come in various sizes and specifications to suit different requirements concerning airflow rate, filtration capability, and pressure settings. The versatility of an air filter regulator makes it an indispensable component in sectors such as manufacturing, automotive repair, and food processing where reliable pneumatic system performance is crucial.
What does an air filter regulator do
An air filter regulator plays a critical role in controlling and maintaining the necessary operating conditions in pneumatic systems. Essentially, it performs two primary functions: filtering the air and regulating pressure. First, as air passes through the system, the device filters out dust, debris, moisture, and any particulate matter that could potentially harm pneumatic tools and equipment. This purification process helps in preventing clogging and wear on the internal components of machinery, thus ensuring a smoother operation and extending the lifespan of equipment.
Secondly, an air filter regulator adjusts the pressure of the compressed air to a desired level before it reaches pneumatic tools or machinery. This regulation is vital because too high or too low pressure can lead to inefficiency or damage to pneumatic devices. By providing a stable and consistent airflow at the optimal pressure, this device significantly enhances performance and energy efficiency across various applications.
Together, these actions facilitate a cleaner operational environment for pneumatic systems while optimizing their efficiency and reliability. An air filter regulator thus serves as an indispensable component in numerous industrial settings, where precise control over air quality and pressure is essential for operational success.
Benefits of an Air Filter Regulator
- Contaminant Removal: Ensures the delivery of clean, dry air by removing contaminants like dust, oil vapors, and moisture from compressed air. This protects downstream equipment from damage and wear, reducing maintenance costs and extending service life.
- Pressure Control: Enables precise adjustment of air pressure, preventing energy waste and damage to pneumatic equipment. This promotes energy efficiency and long-term cost savings.
- Safety: Minimizes the risk of accidents by managing air pressure accurately, reducing the likelihood of burst lines or unexpected equipment behavior. Enhances workplace safety and operational reliability.
- Convenience and Space Savings: Integration of filtration and regulation into a single unit simplifies system design and installation, saving space and reducing the need for additional components. This leads to cleaner setups and easier maintenance routines.
- Operational Efficiency: Ensures clean, conditioned air at optimized pressures, resulting in lower operating costs, improved safety standards, and better equipment protection. An indispensable component within any pneumatic system.
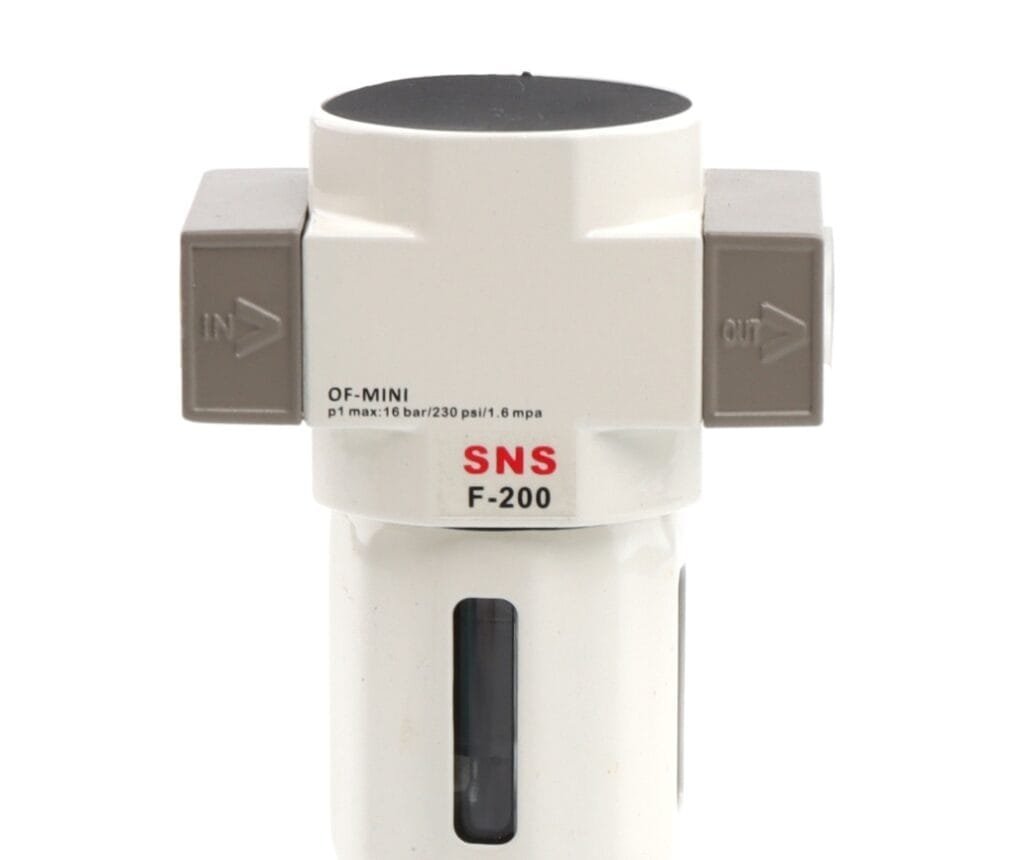
What Does an Air Filter Regulator Consist of?
The primary components of an air filter regulator include:
- Filter Element: This crucial component is responsible for removing impurities from the air, such as dust, particulate matter, and moisture. Constructed from materials like sintered bronze or synthetic fibers, the filter element’s porosity is calibrated to trap contaminants effectively while allowing air to pass through with minimal resistance.
- Pressure Regulator Valve: The valve plays a pivotal role in controlling the output pressure of the air. It adjusts the flow rate based on downstream demand, ensuring that the output remains constant even with variations in input pressure or flow requirements. This is achieved through a mechanism involving a spring-loaded diaphragm or piston.
- Housing: The housing encases both the filter element and regulator valve. It is typically made from robust materials such as aluminum or stainless steel to withstand varying pressures and environmental conditions found in industrial settings.
- Drain Mechanism: Accumulated moisture and debris removed by the filter element are collected at the bottom of the housing. A drain mechanism facilitates their removal. This can be manual, requiring periodic opening by an operator, or automatic, where a float-triggered valve releases collected water when it reaches a certain level.
- Pressure Gauge Port: For monitoring purposes, most air filter regulators are equipped with ports where pressure gauges can be attached. These gauges display both inlet and regulated pressures to help operators maintain optimal performance according to system requirements.
- Adjustment Knob or Screw: This component allows personnel to set desired output pressure levels manually. Turning the knob adjusts tension on the regulating spring within the valve, changing how much force is applied to either open or close it based on required downstream pressure.
Combining these elements into a single assembly streamlines operations by reducing connection points between separate filters and regulators. Consequently, this arrangement leads not only to easier installation but also enhanced reliability due to fewer potential leak paths within pneumatic systems.
How Does an Air Filter Regulator Work?
The process begins as compressed air enters the unit. Initially, the air passes through a filtering element. This component is responsible for removing particulates such as dust, debris, and moisture that can damage equipment or impair system performance. By capturing these contaminants, the air filter effectively prevents operational issues and prolongs the lifespan of pneumatic tools.
Following filtration, the now-clean air moves toward the regulator section. The primary role of this stage is to control the pressure level of the outgoing air. Air pressure within a pneumatic system must be managed precisely; too much pressure can lead to equipment damage or safety hazards, whereas insufficient pressure may result in inadequate system performance. The regulator achieves this balance by employing a spring-loaded mechanism adjusted via an external knob or screw. This adjustment sets a desired output pressure level that remains constant despite fluctuations in incoming air pressure.
At its core, a diaphragm within the regulator responds to changes in downstream pressure. If downstream pressure drops below set levels (for example, when a tool is used and requires more air), the diaphragm compresses the spring further, opening up passage for more air until equilibrium is reestablished at the predetermined setting. Conversely, should downstream pressure exceed desired levels (perhaps due to decreased demand), the diaphragm relieves excess force on the spring, reducing airflow until proper balance is restored.
How to choose an air filter regulator
Choosing the right air filter regulator for your system is a critical step in ensuring that your pneumatic equipment operates efficiently and effectively. To make an informed decision, several key factors need to be considered.
Application and Environment: Understand the specific needs of your application and the environment in which the air filter regulator will operate. High humidity, extreme temperatures, or the presence of corrosive chemicals all impact your choice.
Flow Requirements: Calculate the maximum flow rate required by your pneumatic system. The air filter regulator must be capable of supporting this flow rate without significant pressure drop to maintain optimal performance.
Filtering Needs: Consider the level of filtration needed for your application. Different regulators come with varying grades of filters able to remove particles of different sizes from the air supply. Ensure the chosen model can provide the clean, particle-free air necessary for your equipment’s sensitive components.
Pressure Range: Identify both the minimum operating pressure required by your downstream equipment and the maximum available supply pressure. The selected air filter regulator should comfortably operate within these limits while providing stable output pressure adjustment capabilities.
Material Compatibility: The materials used in construction of an air filter regulator should be compatible with any environmental challenges and substances it may encounter, including oils, moisture, and chemicals present in compressed air.
Size and Portability: Depending on installation constraints or needs for mobility, size may play a significant role in choosing a suitable unit. Compact designs might be preferred for applications with limited space or where portability is essential.
Taking time to assess these considerations will greatly assist in selecting an appropriate air filter regulator that not only meets but exceeds operational requirements, extending equipment lifespan and enhancing productivity through consistent, clean, and well-regulated compressed air delivery.
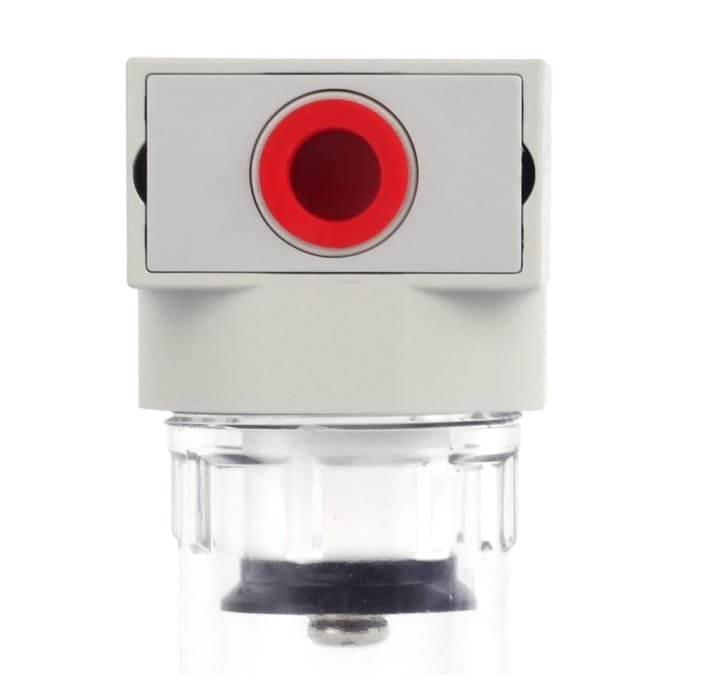
How to Maintain an Air Filter Regulator
Step 1: Routine Inspection Regularly inspect the air filter regulator for any signs of damage, wear, cracks, leaks, or other indicators that it may not be functioning optimally.
Step 2: Cleaning Carefully remove the filter element and clean it according to the manufacturer’s instructions. Some filters may be disposable and should be replaced rather than cleaned.
Step 3: Check Regulator Operation Ensure the regulator maintains specified pressure levels accurately. If there are fluctuations or it fails to hold pressure, adjustment or replacement may be necessary.
Step 4: Lubrication If applicable, lubricate moving parts within the regulator mechanism using lubricants recommended by the manufacturer to prevent damage to internal components.
Step 5: Consult Manual Refer to the air filter regulator’s manual for specific maintenance recommendations tailored to your model.
Step 6: Follow Regular Maintenance Schedule Establish a regular maintenance schedule to ensure periodic checks and maintenance tasks are performed, maintaining the air filter regulator’s reliability over time.
In Conclusion
An air filter regulator is a key component in pneumatic systems that purifies the air supply and maintains consistent pressure, ensuring optimal performance and longevity of the equipment.
To understand more about how an air filter regulator can enhance your pneumatic system and for advice on selecting the right model for your needs, explore our comprehensive range. Take the first step towards optimizing your operations by contacting our experts today.