What is an air regulator?
An air regulator is a device used in pneumatic systems to control the pressure of air supplied to tools and equipment. It ensures that the output pressure remains stable regardless of fluctuations in the input pressure or air demand, thus preventing damage and enhancing performance. Air regulators are essential components in various industrial, automotive, and DIY applications where precise air pressure management is necessary.
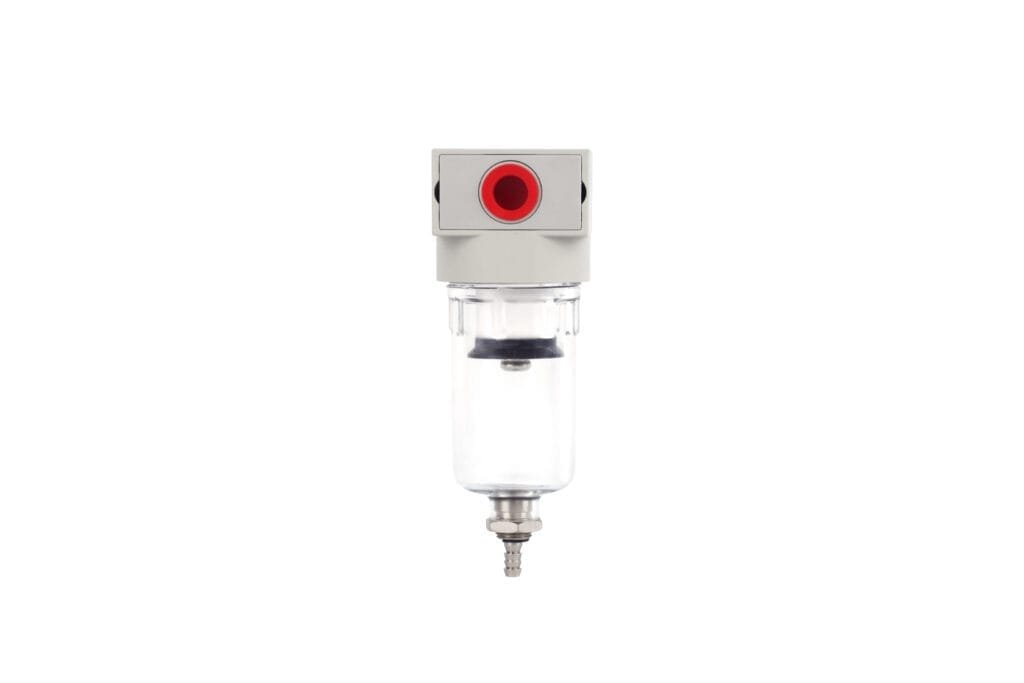
What is an Air Regulator?
An air regulator is a device designed to control and maintain a consistent air pressure level in various types of pneumatic systems. Its primary function is to receive air at a fluctuating inlet pressure and deliver it at a steady, preset downstream pressure, regardless of changes in the upstream supply or variations in demand from downstream components. By performing this vital role, air regulators ensure that tools and equipment connected to the compressed air system operate efficiently and safely.
The utilization of an air regulator is widespread across numerous industries where compressed air is a key energy source. Its operation hinges on internal mechanisms such as diaphragms or pistons which react to downstream pressure fluctuations. These responsive elements actuate control valves within the regulator body that adjust the flow of air, thereby stabilizing the output pressure.
What Is The Purpose Of An Air Regulator?
The air regulator primary purpose is to reduce and maintain a stable working pressure, regardless of fluctuations in the incoming pressure from the air supply. This steady output is crucial for the consistent operation and longevity of downstream equipment since many pneumatic tools and processes require precision regarding their operating pressures.
Furthermore, an air regulator assists in saving on energy costs by minimizing wasted compressed air and ensuring that no more pressure is used than necessary for each application. It also contributes to safety, as excessive pressure can be dangerous and lead to equipment failure or hazards to personnel. By employing an air regulator within a pneumatic system, operators can achieve more accurate control over the pressure delivered to end-use applications, which translates into improved efficiency, product quality, and process reliability.
How Air Regulators Work
Air regulators control pneumatic systems by modulating the flow of air to maintain a desired pressure level. They operate through an intricate internal mechanism that typically comprises a regulating valve, spring mechanism, and a diaphragm or piston. The air regulator responds to changes in downstream pressure and automatically adjusts the airflow to maintain consistent output pressure.
When air enters the regulator, it pushes against the diaphragm or piston connected to the spring-loaded valve stem. This movement adjusts the size of an orifice, controlling flow rate. Should downstream pressure drop below the set value due to increased demand or leakage, more air is allowed through until nominal conditions are re-established. Conversely, should the pressure rise above the desired setting, less air is permitted through as the valve’s opening decreases.
One critical aspect of how these devices work lies in their ability to react swiftly and accurately to changes in system demands. A delicate balance between the spring tension and pneumatic force acting on it ensures that any fluctuations are promptly corrected with minimal deviations from prescribed settings.
How To Choose The Right Air Regulator
Factors to Consider | Considerations |
---|---|
Operating Pressure | Evaluate the required pressure range for your system. Ensure the regulator can maintain stability within this range. |
Flow Rate | Assess the desired flow rate to meet peak system demands without excessive pressure drop. |
Precision Control | Choose a precision regulator for applications requiring exact pressure control, while general-purpose regulators may suffice for less critical tasks. |
Filter Regulator | In environments with airborne particulates or moisture, consider a filter regulator for combined filtration and regulation. |
Material Construction | Select a material (e.g., aluminum or stainless steel) that aligns with environmental conditions to prevent corrosion or degradation. |
Compatibility & Maintenance | Ensure compatibility with existing fittings and consider ease of maintenance for efficient setup and servicing. |
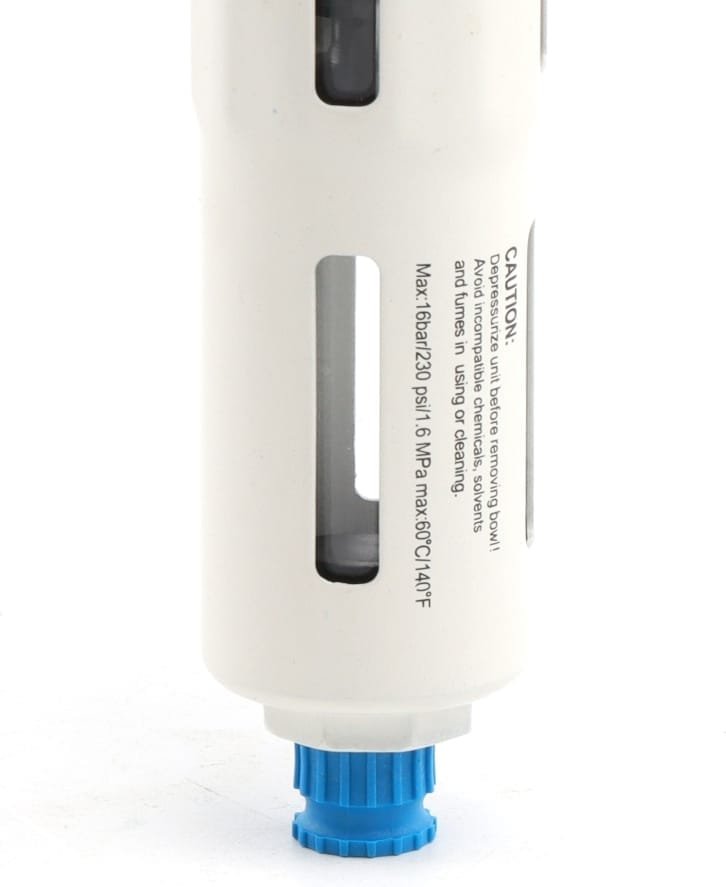
What Are The Types Of Air Pressure Regulators?
Type of Air Pressure Regulator | Description |
---|---|
Precision Regulators | Designed for applications requiring extremely stable and accurate control over pneumatic pressure, even in the presence of supply pressure fluctuations or changes in flow demand. |
Filter Regulators | Combines a filter and regulator into one unit, removing solid particles and condensing moisture from compressed air. They ensure a clean and regulated air supply, extending the life of pneumatic equipment. |
General Purpose Regulators | Widely used for a variety of applications, offering good control over air pressure. They may lack the precision or filtration capabilities required for more sensitive operations. |
Precision regulators
Precision air regulators are designed for applications that require a consistent and exact outlet pressure, which might not be achievable with standard regulators. These sophisticated devices maintain output pressure with a high level of accuracy, often within very tight tolerances. Due to their precision, they are crucial in applications where even minimal fluctuations in pressure can lead to significant variations in performance, quality, or results.
The main advantage of precision regulators is their ability to provide stable control over downstream pressure. This stability is achieved through an intricate design that typically includes a sensitive diaphragm or valve arrangement configured for fine-tuning. As such, precision regulators often react promptly to changes in flow or input pressure and make swift adjustments to maintain the set output pressure.
Filter Regulators
Filter regulators are specialized devices engineered to address the need for both air pressure regulation and contamination removal within pneumatic systems. Their design integrates a filter element with a pressure regulator, providing a two-in-one solution that not only regulates air pressure but also ensures that clean, debris-free air is delivered to downstream components.
The importance of maintaining purity in compressed air cannot be overstated; particulates, moisture, and oil can lead to equipment malfunction or premature wear. Filter regulators tackle this challenge head-on by featuring a filtration unit—commonly using elements such as sintered bronze or polymer fibers—to capture impurities before the air passes through the regulator component.
In practical use, technicians often encounter situations where precise pressure control must be accompanied by clean-air delivery; paint-spraying systems and dental equipment are prime examples. In these scenarios, the dual functionality of filter regulators proves indispensable. Moreover, they generally afford ease of maintenance with replaceable filter elements—a critical feature for applications where consistent quality and hygiene are paramount.
General Purpose Regulators
Manufactured to suit an array of environments, general purpose air regulators typically embody a simple yet effective mechanism. They incorporate a control spring and diaphragm assembly that responds dynamically to changes in system flow and pressure. By adjusting the tension on the spring, users can set the desired output pressure which is sustained by the diaphragm’s movement in correspondence with downstream requirements.
The utility of general purpose regulators extends from straightforward plant air supply lines to tools requiring consistent pneumatic operation. Their adaptability makes them suitable for many industries including manufacturing, automotive, and construction where they ensure that equipment operates safely and efficiently.
One of their key attributes is durability; these regulators are constructed to endure harsh work conditions and continue functioning reliably over time. Likewise, they offer ease of maintenance—crucial for minimizing downtime—and often feature gauge ports for convenient monitoring of system pressures.
Continuous Flow Rate Regulation and Load/Unload Regulation in Industrial Air Compressors
Regulation Type | Description |
---|---|
Continuous Flow Rate Regulation | Continuous flow rate regulation involves adjusting the compressor’s output linearly in response to varying demand for compressed air. It utilizes sophisticated control systems that monitor demand and adjust the motor speed for optimal efficiency. This approach minimizes energy waste by ensuring the compressor operates at peak efficiency relative to current needs. |
Load/Unload Regulation | Load/unload regulation operates in binary states: fully loaded (maximum capacity) or completely unloaded (no compressed air production). When demand drops below a certain threshold, the compressor switches to ‘unload’ mode, reducing power consumption. It reverts to ‘load’ mode when demand increases. This technique is effective for applications with well-defined high and low usage periods but may provide less precise energy management compared to continuous flow rate control. |
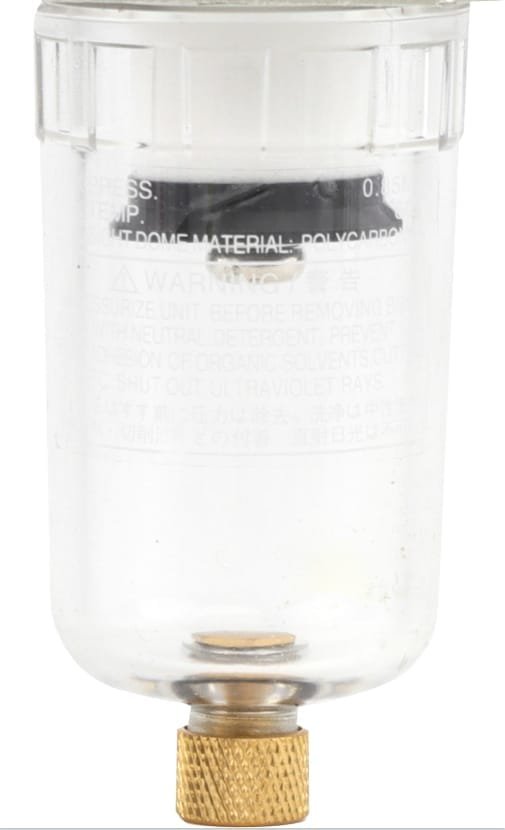
Continuous Flow Rate Regulation
Continuous flow rate regulation within industrial air compressors refers to the consistent management of airflow output, maintaining a steady and controlled delivery. This form of regulation is integral for applications that demand a constant supply of air at a uniform rate, ensuring that processes are not disrupted by fluctuations in pressure or volume.
The main mechanism behind continuous flow rate regulation involves a feedback system which continuously monitors the downstream pressure. If variations occur, the regulator adjusts the orifice size through which the air passes, compensating for any drops or spikes in pressure. This adjustment happens in real-time and is often managed by highly responsive diaphragms in conjunction with control springs and valves that work together to achieve balance.
Load/Unload Regulation
Load/unload regulation is a control mechanism used primarily in industrial air compressors to manage the power consumption and maintain system pressure within a specified range. This method involves two distinct states, ‘load’ and ‘unload.’ During the load phase, the compressor generates compressed air because the demand exists, thereby maintaining the required pressure level in the air system. When the demand for air decreases, or when the system pressure reaches its upper limit, the compressor switches to the unload phase. During this time, it reduces or ceases air production, often running idle without generating additional compressed air which prevents unnecessary energy use.
A key advantage of load/unload regulation is its ability to reduce wear on the compressor components and improve energy efficiency since the compressor is not constantly running at full capacity. It’s an effective way to maintain constant pressure while dealing with fluctuating demand without stopping and starting the compressor repeatedly — a process that can cause mechanical stress and increased energy consumption.
Most load/unload systems include a storage tank or receiver that helps stabilize pressure levels during transition phases. With adequate storage capacity and well-tuned controls, an air compressor can operate smoothly under different loads while minimizing energy usage.
When Do I Need an Air Compressor Regulator?
The need for an air compressor regulator arises in various scenarios, the most common being when you have applications that demand consistent air pressure, or when you’re looking to enhance tool performance and lifespan. If you experience fluctuations in air pressure that lead to inconsistent tool behavior or if your project specifications call for a strict adherence to specific pressure settings, an air regulator becomes necessary.
In operations where multiple tools are connected to a single compressed air source, there will likely be varying requirements for pressure levels; this is where regulators play their part. They allow each tool to receive the appropriate pressure needed for optimal functioning without affecting others in line. Additionally, if the direct output of your air compressor does not match the recommended operating pressure for your device, attaching an appropriately adjusted regulator can prevent damage and reduce energy consumption.
Another indicator for needing a regulator is observable through your equipment’s performance—if your pneumatic tools operate erratically or show signs of premature wear due to overpressure conditions, it’s time to integrate an air regulator into your setup. Moreover, some specific processes require very precise pressure adjustments; without a reliable regulator at such instances, achieving accuracy can be challenging if not impossible.
Assuring safety by preventing over-pressurization incidents is also another vital aspect one should consider. An air regulator aids in maintaining the desired pressure level within safe limits despite variations that could occur with changes in temperature or demand from different parts of the system.
Identifying Faulty Air Regulator Symptoms
- Fluctuating air pressure: One prevalent sign is fluctuating air pressure, which might be observable on the regulator gauge; the needle may fluctuate excessively or fail to maintain a set pressure level.
- Inability to adjust pressure settings: An inability to adjust pressure settings, where turning the knob does not change readings on the gauge, also points toward a malfunction.
- Audible leaks: Audible leaks which indicate compromised seals within the regulator. Air escaping from joints or abnormal noises during operation are tell-tale signs of internal leakage or damage affecting the unit’s integrity and subsequently its efficiency.
- Accumulation of moisture or oil: If there is an accumulation of moisture or oil around the regulator, this could signal that it’s failing to properly manage condensation or filter contaminants effectively – tasks for which some regulators are specifically designed.
- Overall decline in system performance: An overall decline in system performance, such as inconsistent tool speed and torque in power tools or erratic movement in pneumatic cylinders, can also infer that an inadequate supply of regulated air is being delivered due to a compromised air regulator.
What PSI should I set my air compressor?
Determining the correct PSI for your air compressor depends on the tools you intend to use. As a general rule, most air tools require a PSI setting between 70 to 90. It’s essential to consult your tool’s manual to identify the precise PSI requirement. For optimal performance and safety, always adhere to the recommended settings provided by the tool manufacturers.
Do I need a high or low pressure regulator?
Deciding whether you need a high or low pressure regulator depends on the equipment or application you’re using. High pressure regulators are suited for applications requiring a significant reduction in pressure, offering precise control over high-pressure situations. On the other hand, low pressure regulators are designed for applications with less stringent pressure demands, providing adequate control for lower pressure requirements. Understanding your specific needs and the pressure requirements of your application is crucial in making the right choice.

Can an air regulator increase pressure?
No, an air regulator cannot increase pressure. It is designed to reduce and stabilize the pressure from an air compressor to a lower, consistent value desired for specific tools or processes. The main function of an air regulator is to control the output pressure, not to increase it beyond the original source pressure.
Can air flow backwards through a pressure regulator?
NO, generally air cannot flow backwards through a pressure regulator in its normal operation. Pressure regulators are designed to maintain a constant output pressure regardless of changes in the input pressure or flow, thereby preventing backward flow under standard conditions. This ensures that the system operates efficiently and safely, controlling the direction and pressure of air flow as intended.
Can Air Regulator Be Used For Nitrogen
YES, an air regulator can be used for nitrogen.
Can Air Regulator Be Used For Propane
No, typically an air regulator is not recommended for use with propane. Air regulators are designed specifically for air and may not provide the appropriate safety and performance standards required for handling propane. Propane systems often require regulators that can manage its higher pressure and flammable nature safely.
Can Air Regulator Be Used For Water
No, an air regulator should not be used for water. Air regulators are designed for gas flow control, such as air, and typically do not provide the necessary seals and materials resistant to corrosion from water. Using an air regulator for water can result in damage to the regulator and potential system failure.
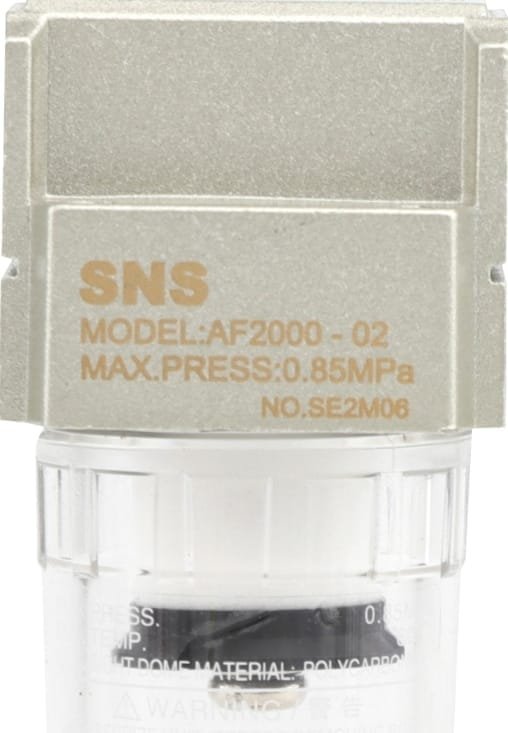
Do Air Regulators Have Check Valves
Yes, many air regulators do have check valves integrated into their designs. These check valves help prevent the backflow of air or other gases, ensuring a one-way direction of flow. This feature is crucial for maintaining the regulator’s efficiency and safety, acting as a safeguard against potential pressure reversals.
In Conclusion
In summary, an air regulator is an essential tool for maintaining steady and controlled pressure in compressed air systems to ensure the safety and efficiency of pneumatic tools and applications.
To maintain optimal performance in your air-powered operations, consider investing in a reliable air regulator suited to your specific needs. Don’t hesitate to reach out to industry professionals for guidance on selecting the right equipment to enhance your system’s functionality and safety.