What Is Difference Between High Pressure And Low-Pressure Regulator
Regulators are crucial for controlling gas flow in various applications. They come in two main types: high-pressure and low-pressure regulators. Understanding the differences between these types is essential for selecting the right one for a specific application.
What Is Low Pressure Regulator
A low-pressure regulator serves the crucial role of reducing gas pressure from high levels to lower, more manageable ones suitable for various applications. This device ensures the safe and efficient operation of gas delivery systems by providing a steady flow of gas at a consistent, controlled pressure. It’s indispensable in connecting high-pressure gas tanks to appliances or equipment that operate under lower pressure conditions.
The operational mechanism of a low-pressure regulator involves receiving gas at high pressure from a storage tank. Through a specialized valve system, it reduces this pressure to a lower level before the gas is directed towards the intended appliance or equipment. The ability of the regulator to maintain this lower pressure steadily, regardless of changes in the tank’s pressure or the demand from the appliance, is a key aspect of its function.
Low-pressure regulators are distinct from their high-pressure counterparts primarily due to the pressure range they’re designed to handle. They typically regulate gas output at pressures below 2 psi, a factor that underscores their suitability for specific applications where low-pressure gas is a requirement. This demarcation ensures that gas-powered systems operate safely and efficiently.
The design and construction of low-pressure regulators incorporate precision engineering to adeptly manage the task of reducing and controlling gas pressure. These regulators are fitted with sensitive control valves and diaphragms, which are finely tuned to react to even minor fluctuations in downstream pressure. Such sensitivity allows the regulator to adjust the gas flow dynamically, ensuring a stable and consistent pressure output to the appliance or equipment it serves.

What Is A Low Pressure Regulator Used For?
Low-pressure regulators are indispensable tools designed to ensure the safe and efficient operation of appliances and equipment by managing gas flow from high-pressure tanks to a lower, usable pressure. These devices serve as a critical safety mechanism, reducing the risk of accidents that could arise from unregulated or excessive gas flow.
In the domestic sphere, low-pressure regulators are commonly found in appliances that many households use daily. For example, they’re integral to the functioning of natural gas or propane-powered grills, ensuring that these outdoor cooking devices operate safely. Similarly, water heaters and kitchen stoves rely on these regulators to maintain a steady and safe gas pressure, preventing potential leaks and ensuring that the appliances work as intended.
The utility of low-pressure regulators extends into the commercial domain, particularly in settings that require the use of gas-powered equipment. Restaurants, for instance, use these devices in their cooking appliances to control the gas flow, ensuring that the cooking process is both safe and efficient. Heating systems in commercial buildings also depend on low-pressure regulators to function properly, safeguarding against the dangers of unregulated gas pressure.
In industrial contexts, the role of low-pressure regulators is even more pronounced. They’re pivotal in processes that demand precise control over gas flow rates, such as in the manufacturing, chemical processing, and pharmaceutical sectors. These industries rely on the accurate and consistent delivery of gas to their equipment, a task that low-pressure regulators fulfill, thereby ensuring the safety and efficiency of industrial operations.
The importance of low-pressure regulators isn’t limited to stationary settings; they’re also crucial in outdoor and camping equipment. Portable stoves and lanterns, for example, utilize these regulators to safely manage the gas pressure, allowing for their safe and efficient use in outdoor environments. This highlights the versatility and widespread need for low-pressure regulators across various applications, from domestic to industrial uses.
Benefits Of Low Pressure Regulator
- Cost-Effectiveness: Low pressure regulators are generally less expensive than high pressure ones because they are designed for lower pressure applications and thus require less robust materials and designs.
- Sufficiency for Low-Pressure Applications: For applications that do not require high input pressures, low pressure regulators are perfectly adequate, making them a more practical and economical choice.
- Ease of Use and Maintenance: Low pressure regulators are typically simpler in design, making them easier to use and maintain, which is beneficial for applications not requiring the complexity and performance of high pressure systems.
- Lightweight and Compact: They are often more lightweight and compact than high pressure regulators, making them ideal for applications with space or weight constraints.
- Lower Energy Consumption: In systems where energy efficiency is a priority, low pressure regulators can be advantageous as they may consume less energy during operation, depending on the application.
What Is Hign Pressure Regulator
High-pressure regulators are devices engineered to control and lower the gas flow from cylinders that are under high pressure, making it usable for a wide array of applications. These devices play a crucial role in guaranteeing both the safety and efficiency of systems that operate using gas at elevated pressures. They’re distinct from low-pressure regulators in their capability to manage significantly higher inlet pressures, sometimes reaching thousands of pounds per square inch (psi). This feature renders them indispensable for tasks that demand such high-pressure conditions.
The core function of a high-pressure regulator is to provide a stable output pressure. This is of utmost importance in applications where a consistent and precise gas flow is essential for operations. To achieve this level of stability, these regulators are constructed using materials and components that are capable of withstanding the intense pressures they regulate. This includes the use of robust diaphragms and valve seats made from materials that offer high strength and durability.
High-pressure regulators are available with a range of features that cater to specific requirements. These features might include the ability to adjust the output pressure, the inclusion of multiple ports to accommodate different gas lines, and the installation of gauges that allow for the monitoring of both inlet and outlet pressures. Moreover, the design and construction materials of these regulators are selected with the nature of the gas in mind. Different gases—such as oxygen, nitrogen, or helium—have unique properties that necessitate specific safety and performance considerations in the design of the regulators.
What Is A Hign Pressure Regulator Used For?
High-pressure regulators are pivotal devices in managing the flow and pressure of gases or liquids within various settings, including industrial, scientific, and energy sectors. Their primary function is to reduce and stabilize gas flow from high-pressure systems to a usable level for specific operations, ensuring both safety and efficiency. This capability is crucial in environments where precise pressure adjustments are necessary for successful outcomes.
In industrial contexts, these regulators play a vital role. They’re integral to manufacturing processes that require controlled atmospheric conditions, such as in the production of chemicals, pharmaceuticals, and food and beverages. By regulating gas pressure, these devices help maintain the necessary environmental conditions for quality and safety standards. Furthermore, in the realm of fabrication, including welding and cutting, high-pressure regulators ensure that operators can perform their tasks safely and effectively by controlling the gas flow used in these processes.
The significance of high-pressure regulators extends into scientific research and laboratory experiments. These settings demand exact pressure control for accurate and reliable results. The regulators are employed to manage gas flows in techniques such as chromatography and spectrometry, which are essential for analyzing materials. They also play a crucial role in instrument calibration and sample preparation, further underscoring their importance in maintaining the integrity of scientific data.
The energy sector’s dependence on high-pressure regulators is another testament to their broad applicability. These devices are essential in managing the flow and pressure of natural gas within distribution networks, ensuring that gas is delivered safely and efficiently to various users, including residential, commercial, and industrial entities. Moreover, in oil and gas production, high-pressure regulators are indispensable in controlling the pressure of fluids extracted from wells, which is critical for the safe and efficient processing, storage, and transportation of these resources.

Benefits Of Hign Pressure Regulator
- Higher Control Accuracy: High pressure regulators can provide more precise control over the output pressure, especially in applications requiring high pressure levels. This precision is essential in industrial and research applications where specific pressure settings are crucial.
- Greater Range of Adjustability: They typically offer a wider range of pressure adjustability, allowing for more flexibility in applications that require varying pressures.
- Suitability for High-Pressure Input: High pressure regulators are specifically designed to handle high-pressure inputs, which low pressure regulators cannot withstand. This makes them indispensable in systems where the supply pressure is significantly high.
- Enhanced Safety Features: They often come with enhanced safety features to handle the high-pressure gas or liquids, reducing the risk of accidents due to pressure overload or failure of the regulator.
- Durability and Reliability: High pressure regulators are built to withstand extreme conditions, including high pressures, temperatures, and corrosive materials, offering longer service life and reliability.
- Efficiency in High-Pressure Systems: They are more efficient in reducing gas or liquid from very high pressures to manageable levels without the need for multiple stages of pressure reduction, which might be necessary with low pressure regulators.
- Versatility: High pressure regulators are used in a wide range of applications, from industrial processes and gas chromatography to high-pressure fluid control in scientific research.
Differences Between High-Pressure And Low-Pressure Regulators
Operating Pressure Range
High-pressure regulators are engineered to manage significantly high pressures, often exceeding 500 PSI. This capability is essential in various industrial environments where controlling gas at such elevated pressures is a requirement. The construction and materials used in high-pressure regulators are specifically chosen to withstand these conditions, ensuring safety and efficiency in their application.
Conversely, low-pressure regulators are designed with a focus on managing much lower pressures, typically not surpassing 2 PSI. This makes them ideal for more common, everyday uses, such as in residential settings. They play a crucial role in regulating natural gas for home appliances or controlling the flow of propane to outdoor grills. The design considerations for low-pressure regulators prioritize precise control at lower pressures, ensuring the safe and effective operation of household appliances.
Materials And Construction
High-pressure regulators are constructed to manage and withstand substantial pressures. To achieve this, they’re typically manufactured using robust and durable materials like stainless steel or brass. These materials are selected for their strength and ability to resist the extreme forces exerted by high pressures. Stainless steel, known for its corrosion resistance and strength, and brass, recognized for its durability, are both ideal for sustaining the structural integrity of high-pressure regulators over time.
The design and construction of high-pressure regulators are complex. They incorporate precision-engineered components and multiple safety features to safely manage the high pressures they’re exposed to. This complexity is necessary to ensure the regulators operate reliably and maintain their performance under the demanding conditions they’re subjected to. These safety features are critical in preventing accidents and ensuring the safe handling of high-pressure gases or fluids.
In contrast, low-pressure regulators are designed for applications where the pressure levels involved are significantly lower. As a result, these regulators can be made from lighter materials, such as aluminum or certain plastics. These materials are chosen for their adequacy in less demanding operational environments, where the pressures don’t require the same level of strength and durability needed for high-pressure applications. Aluminum offers a good balance of lightness and strength, making it suitable for many low-pressure applications, while certain plastics can provide the necessary functionality at a lower cost.
The choice of materials for low-pressure regulators also reflects in their construction, which tends to be less complex than that of high-pressure regulators. Without the need to withstand extreme pressures, low-pressure regulators can be designed with fewer components and simpler safety features. This simplicity allows for easier manufacturing and potentially lower costs, making them more accessible for a wide range of applications.

Performance And Precision
High-pressure regulators are engineered to manage and reduce extreme pressures safely. This capability is crucial for applications that require detailed control across a broad spectrum of pressures. These regulators ensure consistent outlet pressures, a vital feature when facing fluctuating inlet pressures.
Low-pressure regulators, contrastingly, are designed for scenarios where inlet pressures aren’t extremely high. They specialize in providing precise control at lower pressure levels. This precision is particularly important for applications that necessitate a more delicate approach.
In terms of performance under challenging conditions, high-pressure regulators are notably resilient. They’re constructed to withstand and operate efficiently within environments that subject them to high pressures.
Conversely, low-pressure regulators are distinguished by their ability to deliver precision. They excel in situations where control at low pressures is paramount. This makes them the preferred choice for applications that demand meticulous pressure adjustments.
Safety Features
High-pressure regulators are engineered to handle substantial pressure levels. These devices are pivotal in ensuring safety in environments where gas pressures can reach dangerously high levels. To mitigate the risks associated with these pressures, manufacturers equip high-pressure regulators with specialized safety features. One such feature is the safety valve, a critical component designed to release gas automatically if the pressure within the system exceeds a predetermined threshold. This preemptive measure is essential for preventing potential accidents caused by overpressure, which could lead to catastrophic failures or explosions.
Another safety mechanism incorporated into high-pressure regulators is the rupture disk. This device serves a similar purpose to the safety valve, acting as a fail-safe to relieve excess pressure. However, it operates differently. The rupture disk is designed to burst at a specific pressure point, providing an immediate release of gas and thus reducing the pressure within the system. This immediate response is crucial in scenarios where even a slight delay in pressure relief could result in damage or danger.
Low-pressure regulators, while operating under less extreme conditions than their high-pressure counterparts, also feature safety mechanisms tailored to their application. These regulators are equipped with relief valves, devices that manage pressure fluctuations within a lower range. Though the pressures involved are significantly lower, the potential for leaks or minor pressure buildups still poses safety concerns. The relief valves ensure that these regulators can handle such situations effectively, maintaining operational safety and integrity.
Both high and low-pressure regulators are meticulously designed with materials and construction methods that minimize the likelihood of leaks. Leak prevention is paramount in maintaining safety standards, as even small leaks can lead to hazardous conditions. The choice of materials, along with the design of the regulators, plays a critical role in ensuring that they can withstand the pressures they’re subjected to without compromising their structural integrity or functionality.
Applications
High-pressure regulators are crucial in environments where gas must be brought down from extremely high pressures to levels that are safer and more manageable for specific applications. These devices are engineered to handle the stress and demands of significantly reducing gas pressure. Commonly, they’re employed in sectors that require precise control over high-pressure gas flows. This includes industrial settings, where the machinery may depend on such regulated gas supplies for operation. Similarly, welding equipment relies on these regulators to provide a consistent flow of gas, essential for achieving quality welds.
In contrast, low-pressure regulators are designed to cater to applications where the gas pressure doesn’t need to be drastically reduced. Their operation is more suited to everyday uses, where safety and efficiency are paramount, but the pressure levels involved are considerably lower. For instance, in residential settings, these regulators ensure that gas grills and outdoor cooking appliances operate safely, preventing hazards related to over-pressurization. Similarly, recreational vehicles (RVs) utilize low-pressure regulators to maintain a steady flow of gas for heating and cooking purposes, ensuring that the gas systems within these vehicles are safe and reliable.

Faqs
Do I Need A High Pressure Or Low Pressure Regulator?
Determining the appropriate regulator type, whether high-pressure or low-pressure, is crucial and directly dependent on the demands of your specific equipment and its intended usage scenarios. High-pressure regulators, which are indispensable for equipment functioning under significantly elevated gas pressures, are engineered to manage pressures exceeding 500 psi. This makes them perfectly suited for a range of heavy-duty applications. For instance, industries that utilize machinery requiring a consistent and robust gas supply, scuba diving enthusiasts who rely on tanks that must maintain a high-pressure level to ensure safety underwater, and even the operation of gas grills that need a high and steady pressure to cook food evenly, all benefit from these regulators.
Conversely, low-pressure regulators cater to a different spectrum of needs. These are specifically designed for devices and systems that run at much lower pressures, typically not surpassing 2 psi. Their application is widespread in settings that don’t demand the intense pressure levels managed by their high-pressure counterparts. Residential water heaters, which ensure that homes have access to hot water without the risks associated with high gas pressures, RV appliances that are designed to be safe and efficient within the confined spaces of recreational vehicles, and outdoor cooking equipment that provides a leisurely cooking experience without the complications of high-pressure systems, all utilize these lower pressure regulators.
It is of utmost importance to meticulously assess the pressure requirements stipulated for your equipment. This involves a thorough consultation of the manufacturer’s guidelines to ensure that the chosen regulator aligns perfectly with the operational needs and safety standards of your equipment. Making an informed decision between a high-pressure and low-pressure regulator isn’t merely a matter of preference but a critical step in guaranteeing the safety, efficiency, and longevity of your equipment. This careful consideration ensures that you not only adhere to safety protocols but also optimize the performance and efficiency of your equipment by matching it with the most suitable pressure regulator.
Can High-Pressure Regulators Be Used In Place Of Low-Pressure Regulators?
It’s a common inquiry whether it’s feasible or safe to use high-pressure regulators in place of low-pressure ones for various applications. The answer to this question is categorically negative. High-pressure regulators are engineered with the specific purpose of managing and reducing significantly higher inlet pressures to a level that can be safely and effectively used. These devices are essential for ensuring that the gas flow is regulated at a pressure that’s both manageable and usable for specific equipment or applications.
When contemplating the substitution of a high-pressure regulator for a low-pressure one, it’s crucial to understand the potential consequences. High-pressure regulators, by their design, are capable of withstanding and moderating much greater forces than their low-pressure counterparts. If a high-pressure regulator is incorrectly used in a scenario that requires a low-pressure regulator, the outcome can be detrimental. The excessive pressure output can lead to equipment being subjected to forces it wasn’t designed to handle. This mismatch can cause not only damage to the equipment but also elevate the risk of catastrophic failures that may pose serious safety hazards.
The necessity of matching the regulator to the pressure requirements of a specific system can’t be overstated. Each piece of equipment or application has been designed with certain operational parameters in mind, including the pressure at which it can safely and efficiently operate. Utilizing a high-pressure regulator in a setting that necessitates a low-pressure one disrupts this balance, potentially leading to malfunctioning equipment. The implications of such a mismatch can range from decreased performance and efficiency to severe safety risks, including leaks or explosions.
Choosing the appropriate type of regulator for a given application is paramount to ensuring the safety and integrity of the equipment, as well as the safety of the individuals operating it. It’s essential to understand the operational specifications of your system and select a regulator that meets these requirements. In doing so, you mitigate the risks associated with pressure mismatches and ensure that your equipment operates within its designed parameters. This careful selection process is crucial for maintaining both operational efficiency and safety standards.
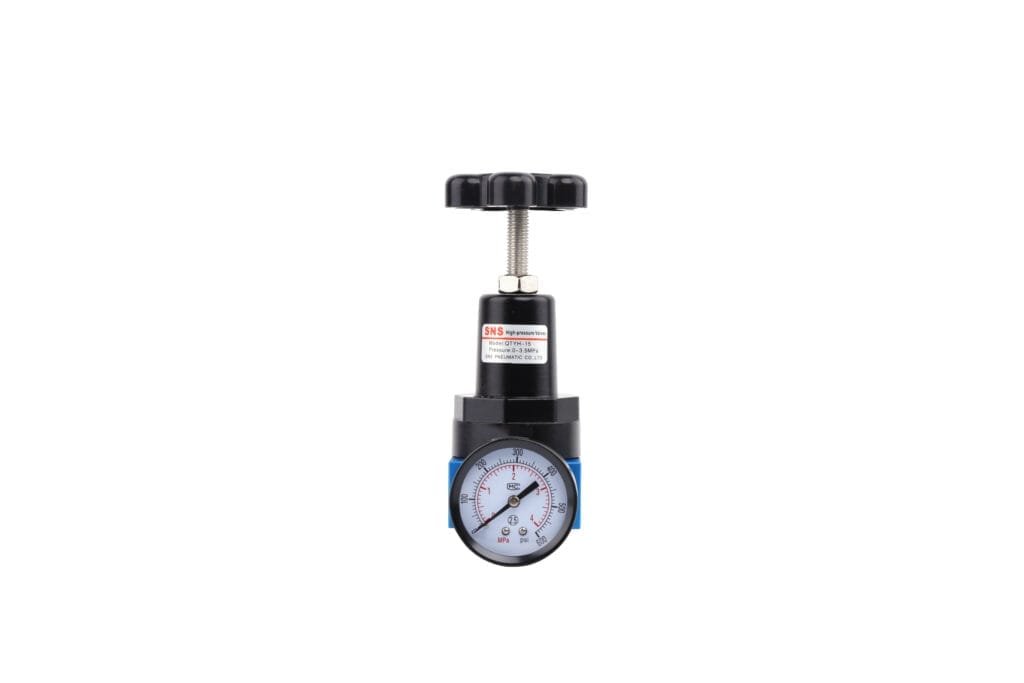
How Do I Choose The Right Pressure Regulator For My Application?
To ensure optimal performance and safety in your application, it’s crucial to select the appropriate pressure regulator meticulously. This selection process begins by identifying the specific type of gas or liquid that the regulator will need to manage. Different substances could have varying effects on regulator materials, thereby necessitating a careful match to avoid premature wear or failure. For example, certain gases might be more corrosive than others, requiring regulators made from materials resistant to such conditions.
Another critical factor in choosing the right pressure regulator involves a detailed understanding of the pressure requirements for your application. This includes both the maximum inlet pressure—the pressure at which the gas or liquid enters the regulator—and the desired outlet pressure—the pressure at which it leaves. Selecting a regulator that can comfortably handle these pressures is vital for maintaining system integrity and preventing equipment damage.
Flow rate, or the volume of gas or liquid that needs to pass through the regulator within a given time frame, is another essential consideration. The chosen regulator must be capable of supporting your application’s specific flow rate requirements without sacrificing stability or performance. If the regulator can’t maintain a consistent flow rate, it could lead to operational inefficiencies or even safety hazards.
The operating environment in which the regulator will function also plays a significant role in the selection process. Factors such as ambient temperature and exposure to potentially corrosive substances can dramatically affect the lifespan and reliability of a pressure regulator. For instance, a regulator used in a high-temperature environment might require materials specifically designed to withstand such conditions without degrading.
Finally, consulting with manufacturers or experts in the field can provide invaluable insights into selecting the most suitable pressure regulator for your application. These specialists can offer guidance based on the specific requirements and constraints of your project, ensuring that you choose a regulator designed to meet your needs accurately. Their expertise can help you navigate the vast array of options available, making the selection process less daunting and more efficient.
Conclusion
In summary, the primary distinction between high-pressure and low-pressure regulators is their ability to handle different pressure levels and applications.
If you’re still uncertain about which regulator is suitable for your requirements, consider reaching out to a professional for advice. Remember, selecting the correct regulator is crucial for the safety and efficiency of your operations.