What Is Double-Acting Pneumatic Cylinder
A double-acting pneumatic cylinder is a mechanical device that uses compressed air to produce force in both extending and retracting motions. Unlike single-acting cylinders, it requires air pressure for operation in both directions.
Double-acting pneumatic cylinders are pivotal components in modern industrial machinery, facilitating precise movement control and high-force applications efficiently. Understanding how these cylinders function and their advantages can significantly enhance the design and functionality of pneumatic systems.
What Is Double-Acting Pneumatic Cylinder
A double-acting pneumatic cylinder is a mechanical device. It uses air to move in two directions, inward and outward. Such cylinders have two ports. Air enters through one port to push the piston in one direction and exits from the second port to return the piston back. This mechanism allows for more precise control compared to single-acting cylinders, which move in only one direction with a spring return.
Components Of A Double-Acting Pneumatic Cylinder
A double-acting pneumatic cylinder transforms compressed air into mechanical energy. It functions through the motion of air on a piston within a sealed cylinder. Understanding each component is crucial for recognizing how these devices operate efficiently.
Cylinder Barrel
The cylinder barrel forms the main body of the pneumatic cylinder. It’s manufactured from materials like steel, stainless steel, or aluminum, providing durability and resistance to wear. This hollow tube houses the piston and the compressed air which drives it.
Piston
Situated inside the barrel is the piston. This element separates the two sides of the cylinder and moves back and forth under air pressure changes. The piston’s design ensures efficient energy conversion from compressed air to mechanical work.
Piston Rod
Attached to the piston, the piston rod transfers the linear motion and force outside the cylinder. Made from robust materials, it withstands bending and buckling forces during operation.
End Caps
At each end of the cylinder barrel sit end caps or heads. They close off the barrel, hold components in place, and often have mountings for installation purposes. Their design minimizes leaks and maintains pressure integrity.
Seals
Seals are critical for preventing air leaks between various moving parts within a pneumatic cylinder. Positioned around pistons, rods, and in other joints, they ensure efficiency by keeping compressed air where needed for proper function.
Ports
Air ports in double-acting cylinders facilitate entry and exit points for compressed air. Located on end caps or along them, these ports allow controlled airflow into either side of the piston chamber to enable precise movement control.
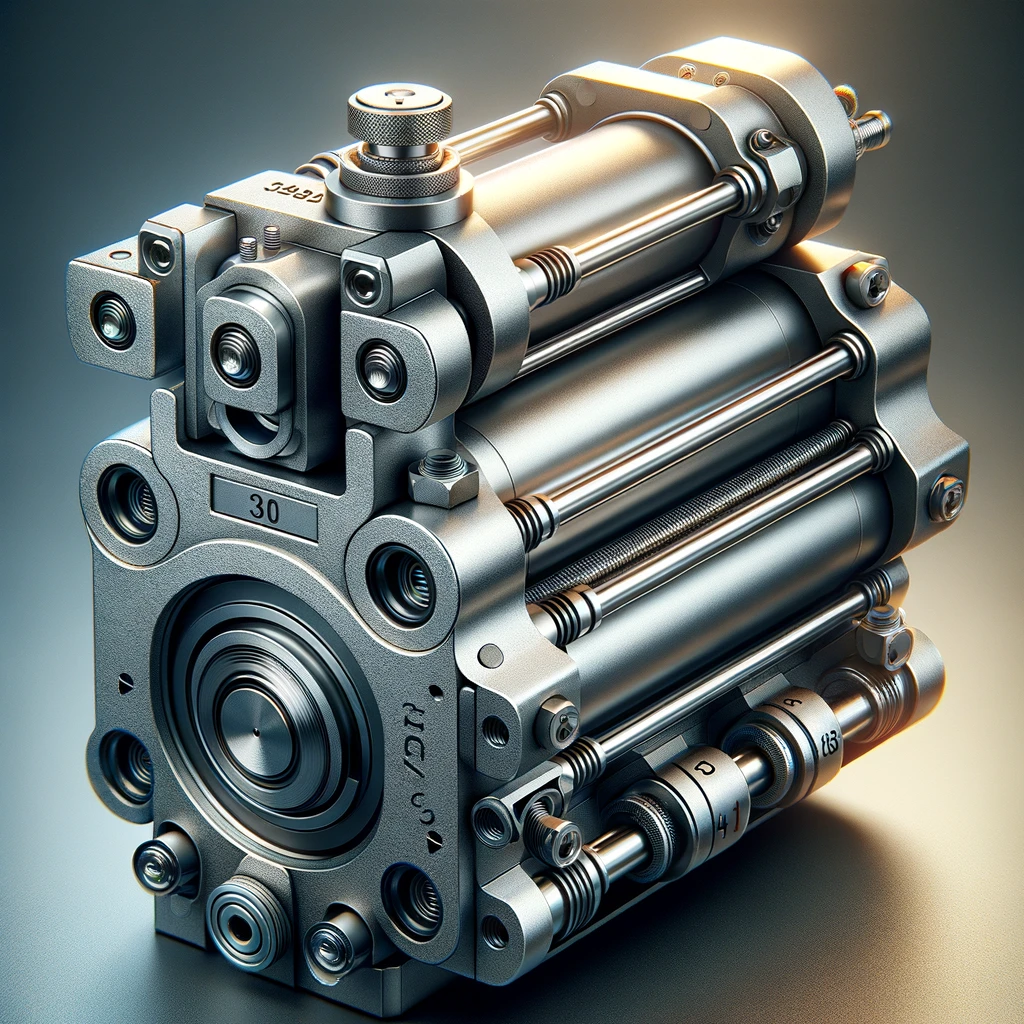
How Does Double-Acting Pneumatic Cylinder Work
A double-acting pneumatic cylinder uses air pressure to move in two directions, typically in and out. These cylinders have two ports to allow air in, one on each end. When pressurized air enters through one port, it pushes the piston to move in one direction. Then, air entering through the second port moves the piston back.
The process begins with compressed air entering through the port at one end of the cylinder. This forces the piston to move away from that end. The movement of the piston is linear and can be used to perform work, such as lifting or pushing objects.
Once the task is accomplished or a change in direction is needed, air pressure is applied through the opposite port. This causes the piston to return to its original position or continue moving in the opposite direction. During this phase, air from the initial side needs to escape; hence, that port turns into an exhaust port allowing air to exit.
Control valves often regulate this bidirectional flow of air into and out of a cylinder. They precisely control when and how fast each movement occurs by directing airflow appropriately.
Double-acting pneumatic cylinders are distinct because they require a supply of compressed air at both ends for operation. This contrasts with single-acting cylinders that use a spring mechanism for one direction of motion and compressed air for the other direction.
Types Of Double-Acting Pneumatic Cylinders
Double-acting pneumatic cylinders come in various types. These variations primarily stem from differences in construction, design, and cushioning mechanisms. Understanding these categories helps in selecting the right cylinder for a specific application.
Based On Construction And Design
- Tie Rod Cylinders make use of tie rods to hold the cylinder’s end caps against the cylinder barrel. This type is known for its robustness and easy maintenance.
- Welded Body Cylinders have their end caps welded directly to the cylinder barrel, eliminating the need for tie rods. This design offers a compact profile ideal for applications with limited space.
- Telescopic Cylinders display a unique design that allows them to provide a longer stroke while maintaining a shorter retracted length. They achieve this through multiple stages of cylinders that telescope outwards as they extend.
Based On Cushioning Type
- Adjustable Cushioning systems allow the user to modify the cushioning effect to protect against impact at the end of the stroke, making it suitable for varying loads and speeds.
- Fixed Cushioning is set by the manufacturer and cannot be adjusted. It’s designed to absorb impact in standard applications where operational conditions remain constant.
Special Types
- Rodless Cylinders differ fundamentally from traditional designs by lacking an external rod, utilizing an internal mechanism to create linear motion within a compact footprint.
- Compact Cylinders are designed for tight spaces, delivering power without requiring much room, making them perfect for applications where space is at a premium.
Based On Construction And Design
Tie Rod Cylinders
Tie rod cylinders are a type of double-acting pneumatic cylinder. They use metal rods to maintain integrity. These rods extend through the cylinder barrel and are secured by nuts at both ends, holding the assembly together. This design allows for easy maintenance and disassembly. Tie rod cylinders can handle both high pressure and large loads, making them versatile.
They come in various bore sizes and stroke lengths, offering flexibility in applications. Unlike welded body cylinders, tie rod design simplifies repairs since components can be easily accessed and replaced. Furthermore, the tie rod construction ensures robustness and durability, even in demanding industrial contexts.
However, their construction can make them bulkier than other types of cylinders, such as compact or rodless designs. Despite this drawback, their reliability and ease of repair have made tie rod cylinders a popular choice for many applications.
Welded Body Cylinders
Welded body cylinders have a robust design. Their structure eliminates the need for tie rods by welding components directly together. This approach enhances strength and durability. Welded body cylinders are known for their compactness, which makes them suitable for use in confined spaces. They endure high stress and pressure conditions well, attributing to their solid construction.
These cylinders cater to diverse industrial applications. They find use in heavy machinery and off-road vehicles due to their resilience. The welding guarantees a leak-proof operation, crucial for maintaining system integrity under harsh conditions.
One significant advantage of welded body cylinders over other types is maintenance ease. Their design minimizes potential leak points, reducing the need for frequent inspections and repairs. However, if repair is necessary, it can be more complex due to the welded structure.
Telescopic Cylinders
Telescopic cylinders are a type of double-acting pneumatic cylinder known for their extended stroke capability from a very compact initial size. These cylinders use a series of steel tubes, called stages, that sequentially extend or retract. The design uniquely allows for a much longer stroke than the cylinder’s physical length when fully retracted. Each stage is slightly smaller in diameter than the previous one, enabling them to fit inside each other.
The operation of telescopic cylinders involves air pressure acting on the base of the first stage, propelling it outward. As this stage reaches its full extent, the pressure then shifts to move the successive stage until all have extended. Retraction works in reverse order, with air pressure applied alternatively to bring each stage back into the housing cylinder.
Two main types of telescopic cylinders exist: single-acting and double-acting. Double-acting telescopic cylinders can extend and retract using hydraulic or pneumatic power, which offers more control and versatility in operation compared to their single-acting counterparts that typically use gravity for retraction.
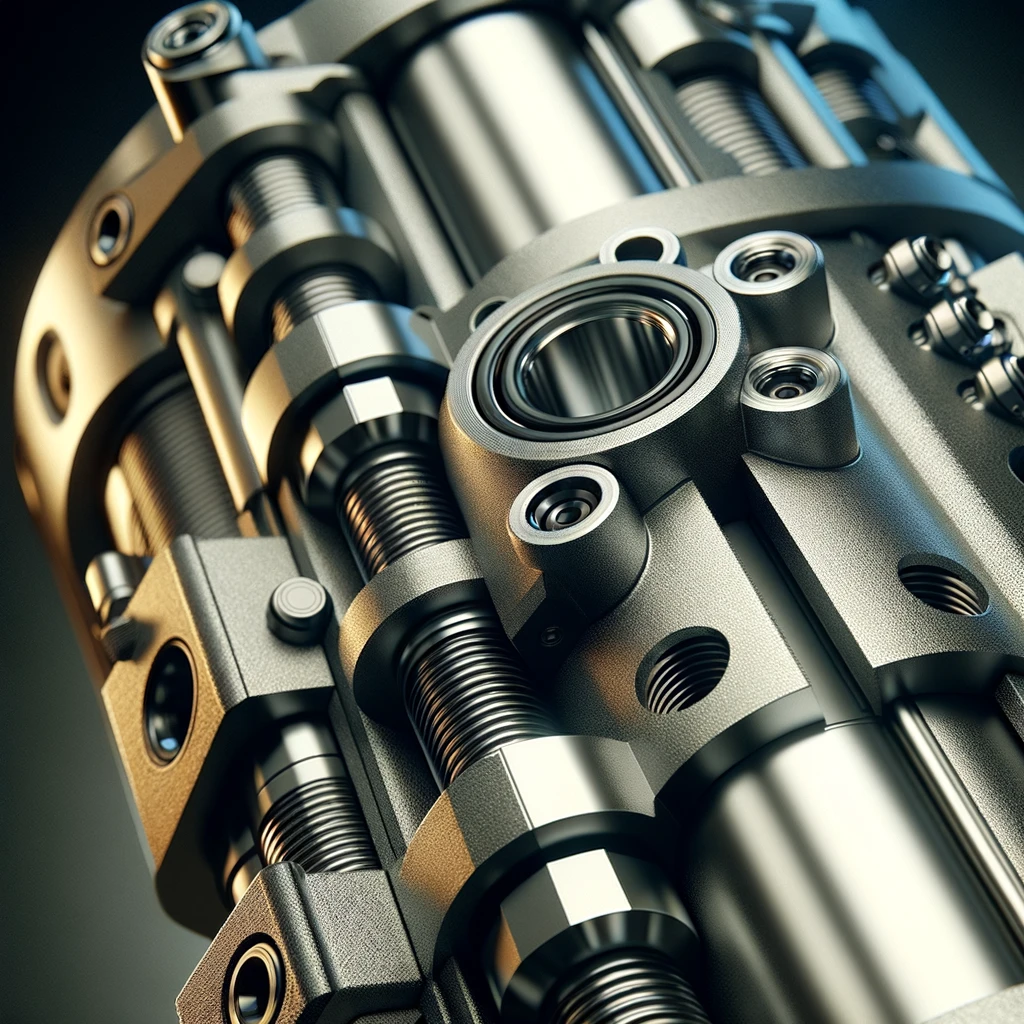
Based On Cushioning Type
Adjustable Cushioning
Adjustable cushioning in double-acting pneumatic cylinders allows for the customization of end-of-stroke deceleration. This feature provides users with the flexibility to precisely control the cylinder’s speed and force as it approaches its stroke limits, minimizing impact and wear on components. Through adjustment screws located at both ends of the cylinder, operators can fine-tune the amount of air that is allowed to escape during the final phase of the piston’s travel. This controlled release of air acts as a buffer, reducing the velocity of the piston before it fully extends or retracts.
The presence of adjustable cushioning is crucial in applications where variable loads or speeds are encountered, ensuring smooth operation and enhancing equipment longevity. By dampening the kinetic energy generated by the moving parts, this feature effectively prevents damage that could arise from harsh contact between metal surfaces. Moreover, adjustable cushioning contributes to noise reduction, making pneumatic systems more suitable for environments sensitive to sound.
Fixed Cushioning
Fixed cushioning in double-acting pneumatic cylinders is a pre-set mechanism designed to decelerate the piston’s motion towards the end of its stroke. This built-in feature aims to reduce the impact when the piston reaches its terminal point. Unlike adjustable cushioning, fixed cushioning does not allow for alterations in the damping characteristics after manufacture.
The mechanism involves incorporating a specific design within the cylinder that restricts airflow near the end caps, naturally decelerating the piston. Because it is not adjustable, the manufacturer must precisely engineer it for anticipated operating conditions. This means calculating the expected load and speed to ensure effectiveness.
Fixed cushioning simplifies cylinder design and operation. There are no external adjustments necessary, which can be advantageous in environments where tampering could be an issue or simplicity is preferred. However, this lack of adjustability might limit application flexibility, making these cylinders best suited for applications with consistent loads and speeds.
Special Types
Rodless Cylinders
Rodless cylinders differ from traditional pneumatic cylinders in that they lack a piston rod extending outside the cylinder body. These cylinders use an internal mechanism to create linear motion without using an external rod. The design offers a compact solution, saving space while allowing for long-stroke applications.
These cylinders operate through a magnetic or mechanical coupling system. The mechanism inside the cylinder moves directly with the piston, translating air pressure into linear force without requiring an external guiding rod. This feature leads to a more streamlined and efficient design.
Given their internalized design, rodless cylinders exhibit reduced potential for leakage compared to conventional cylinders, offering improved reliability. Additionally, their construction minimizes the risk of contaminants entering the cylinder, enhancing their suitability for clean environments.
Compact Cylinders
Compact cylinders are designed for tight spaces where traditional pneumatic cylinders cannot fit. They have a short stroke and a low profile, making them ideal for applications with limited space. Despite their small size, compact cylinders provide the same force as larger cylinders, thanks to their efficient design.
The construction of compact cylinders allows for their direct mounting onto machinery and equipment. This is advantageous in automated systems where precise movement and positioning are required. Their lightweight nature also contributes to less overall system weight, leading to energy savings.
Advantages Of Double-Acting Pneumatic Cylinders
High Force Output: Generates force in both push and pull directions, boosting efficiency.
Precision and Control: Allows exact piston movement control, ensuring accurate positioning.
Durability: Built for rigorous, repeated use leading to reduced maintenance and longer lifespan.
Energy Efficient: Optimizes air pressure use, offering better energy utilization.
Adjustable Speed: Affords flexibility with easy speed adjustments for various tasks.
Versatility: Suitable for diverse environments and applications across multiple industries.
Straightforward Installation: Easier setup process for systems integration, despite initial complexity.
Reduced Manual Intervention: Design supports automation with minimal manual adjustments needed.
Load Holding: Capable of maintaining load positions without power, increasing safety and stability.

Where Would You Use A Double-Acting Cylinder?
In manufacturing environments, double-acting cylinders are essential for powering automated machinery. They adjust positions, control assembly lines, and handle materials with consistency and reliability. Their ability to exert force in two directions enhances the efficiency of production processes.
Robotic systems benefit significantly from the versatility of double-acting cylinders. These components enable robots to perform complex tasks such as picking, placing, assembling, and even more intricate operations that demand controlled movements.
In the automotive sector, these cylinders play a pivotal role in equipment used for lifting heavy parts during assembly or repair works. Their robust design ensures stability and safety when handling substantial loads.
Construction machinery also relies on double-acting pneumatic cylinders. They are found in excavators, backhoes, and loaders where powerful hydraulic versions facilitate digging and material transport activities through precise control of bucket or shovel movements.
Additionally, aerospace applications utilize double-acting cylinders due to their precision and reliability. These devices help adjust flaps, stabilize landing gears, and manage cargo doors with exactitude required by aviation standards.
Difference Between Single-Acting And Double-Acting Cylinders
Single-acting and double-acting cylinders serve as powerful components in various mechanical systems, notably differing in their mechanism and applications. The core distinction lies in the number of action points and the method of movement facilitation within each cylinder type.
Single-acting cylinders possess only one working port to introduce compressed air. This means that air pressure is applied in just one direction, enabling motion to occur either outwards or inwards, but not both. Typically, these cylinders rely on an external force, like a spring or gravity, to return to their original position once the compressed air is exhausted.
In contrast, double-acting cylinders feature two ports for air entry and exit at opposite ends. This design allows for control over motion in two directions—extend and retract—using air pressure alternately on either side of the piston within the cylinder. Consequently, they do not depend on external forces to reverse motion since they can be driven pneumatically in both directions.
This fundamental operational difference leads to varied applications based on power needs and control requirements. Single-acting cylinders are often used where simple tasks are performed, such as lifting or single-direction pushes and pulls. These systems are simpler and may cost less due to their straightforward mechanics.
Double-acting cylinders are suited for more complex operations requiring precise control over movement in both directions. Examples include robotic arms or any application needing reciprocating actions. Their ability to apply force both ways without relying on external mechanisms makes them versatile and essential for tasks demanding greater control.
Efficiency also differs markedly between the two types. Since double-acting cylinders can use compressed air more effectively by utilizing it for both extending and retracting motions, they are typically considered more efficient than their single-acting counterparts.
Lastly, installation complexity varies; single-acting cylinder systems might involve fewer components given their reliance on an external force for movement reversal, potentially simplifying setup and maintenance. However, this simplicity restricts them from performing tasks as dynamically as double-acting systems can.
In essence, choosing between single-acting and double-acting cylinders hinges on specific application needs—whether simplicity and cost-efficiency take precedence or if precise control and versatility are paramount.
In Conclusion
A double-acting pneumatic cylinder is a versatile and efficient device used for precise motion control in various industrial applications.
To harness the full potential of these powerful mechanisms, consider integrating them into your automation projects for improved reliability and performance. Contact us today to explore our range of double-acting pneumatic cylinders tailored to meet your specific needs.