What Is Pneumatic Manifolds
Pneumatic manifolds are devices used to distribute air or gas from a single source to multiple outlets, allowing for the control of fluid flow in various components of a pneumatic system. They play a crucial role in optimizing the functionality and efficiency of pneumatic systems by centralizing connections for air distribution.
Understanding the function and importance of pneumatic manifolds is essential for those involved in the design and maintenance of pneumatic systems. This knowledge not only aids in system optimization but also ensures the reliability and efficiency of pneumatic operations.
What Is Pneumatic Manifolds
Pneumatic manifolds act as a central hub in pneumatic systems. They distribute air or gas from a single source to various outputs. This component simplifies connections between the air supply and control valves. They streamline the design of pneumatic systems. A key feature is their ability to consolidate multiple valves into a single body.
Pneumatic manifolds offer flexibility in system design and expansion. Systems can start small and grow by adding more manifold blocks. This modular nature reduces the need for complex piping, saving space and reducing potential leak points.
Operationally, these manifolds allow for efficient control over the distribution of pressurized air. Users can accurately manage airflow to various parts of the system through individually controlled outlets.
Components of Pneumatic Manifolds
Pneumatic manifolds are essential parts of pneumatic systems. They serve as a central hub for distributing air or gas. Each component plays a significant role in the functionality and efficiency of a manifold system.
Body: Serves as the durable frame made from materials like aluminum or brass, ensuring longevity and corrosion resistance.
Valve Stations: Integral for controlling airflow, ranging from simple on/off to complex proportional valves for precise management.
Ports: Serve as connection points; inlet ports take in pressurized air, and outlet ports distribute it to designated areas.
Mounting Options: Vary per design, with some suited for wall mounting and others for direct machine attachment, enhancing installation flexibility.
Pressure Release Valves: Important safety features that prevent over-pressurization and potential damage or injury.
Solenoids and Sensors: Provide automation, with solenoids for electronic valve actuation and sensors for monitoring system metrics.
Accessories: Include seals for leak-proof connections and labels for easy identification and maintenance tracking.
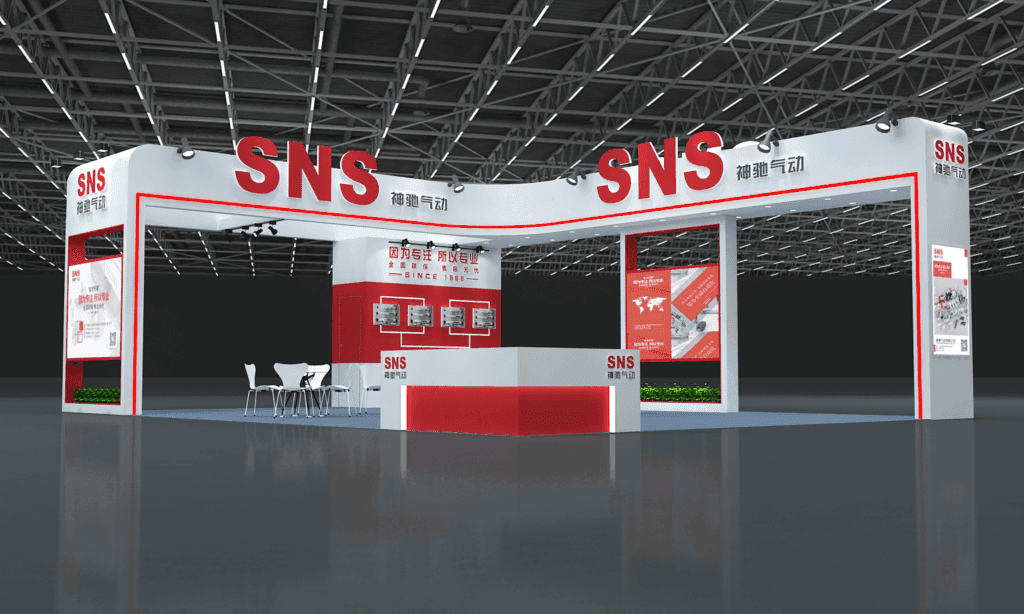
Advantages of Pneumatic Manifolds
Centralized Connections: Manifolds reduce the need for multiple hoses and fittings, centralizing connections to decrease potential leaks and enhance reliability.
Streamlined Maintenance: Simplifies troubleshooting by offering a single point for connection management, thus easing maintenance efforts.
Space Efficiency: By consolidating components, manifolds ensure efficient use of space within systems.
Precise Air Distribution Control: Manifolds enable even pressure distribution and maintenance, leading to energy savings and reduced operational costs.
Flexible Design: Available in various sizes and configurations, allowing for easy system expansion or modification without major redesigns.
Enhanced Safety: Centralized control minimizes high-pressure risks, with built-in features like pressure relief valves to prevent over-pressurization.
Decreased Installation Time and Costs: Less assembly time needed with fewer parts to connect, cutting labor costs and downtime.
Promotes Standardization: Facilitates standardized designs for machinery and production lines, improving manufacturing and training efficiency due to uniformity.
How Does Pneumatic Manifold Work
The process begins when compressed air enters the manifold. This air is supplied from a compressor and is the primary power source for the entire system. The manifold then channels this air through its various ports, which are connected to different pneumatic devices.
As the operator activates a specific control valve, the manifold redirects airflow to the designated area. This could mean starting a machine, moving a piston, or engaging another device. The valve’s opening allows air to flow through. When closed, it stops this flow, halting operations in that section of the system.
Types of Manifold Systems
Parallel Type Pneumatic Manifolds
Parallel type pneumatic manifolds distribute air or fluid in parallel lines to multiple outputs. This configuration provides a simple, efficient path for fluid flow. It allows each connected component to operate independently without interference.
Serial Type Pneumatic Manifolds
Serial type pneumatic manifolds distribute air or fluid in a sequence. Each port follows the other in a single line configuration. This design simplifies the structure but limits flexibility. It is ideal for linear operations. In serial manifolds, pressure drops can occur. This happens because each subsequent outlet receives slightly less pressure than the one before it.
Sandwich Type Pneumatic Manifolds
Sandwich type pneumatic manifolds offer a unique integration approach. They sit directly between the valve and its base. This configuration creates a compact assembly. It minimizes space requirements. They streamline connections in pneumatic systems.
These manifolds facilitate efficient airflow distribution. They do this by allowing multiple valves to connect in a single, organized unit. The design aims at reducing leakage potential. It achieves this through fewer connection points.
Modular Type Pneumatic Manifolds
Modular type pneumatic manifolds offer flexibility in assembly and system design. They allow for the expansion or reduction of sections without replacing the entire manifold. This adaptability aids in system customization according to specific requirements. These manifolds consist of individual modules that can be easily connected or disconnected. Each module serves a distinct function, facilitating targeted maintenance and upgrades.
The design promotes efficient air distribution to multiple outputs from a single input source. It minimizes leakage risks, thanks to fewer connection points compared to traditional systems. The modular approach also simplifies troubleshooting processes. Identifying and addressing issues becomes more straightforward when components are segmented.
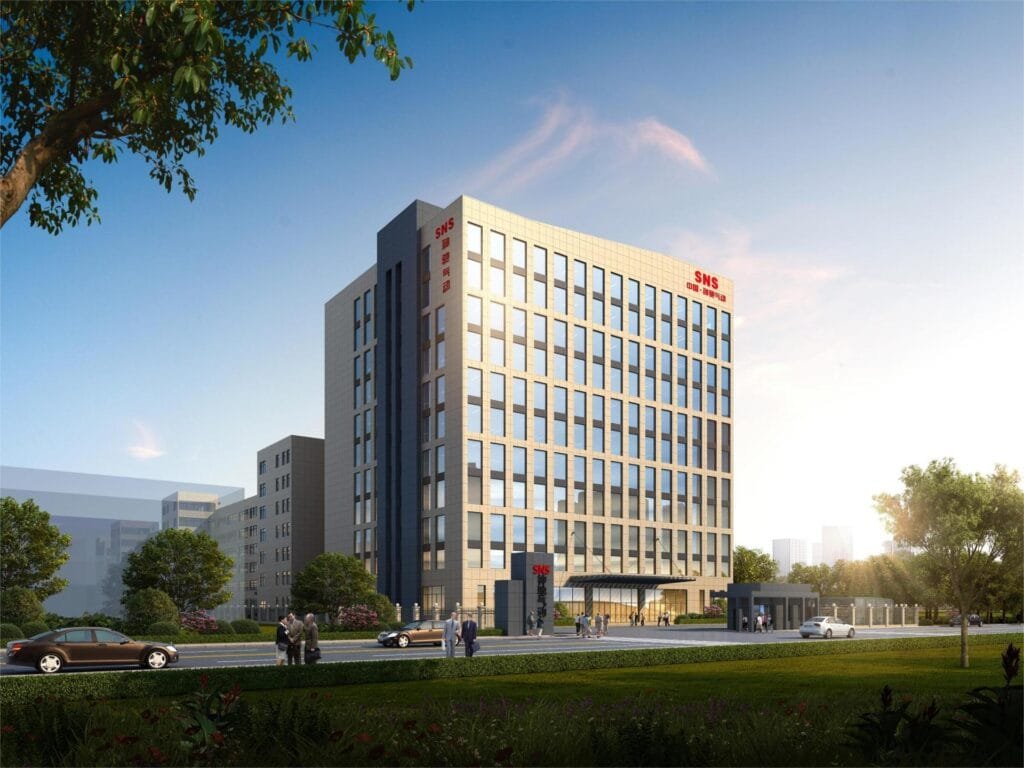
Applications of Pneumatic Manifold
Pneumatic manifolds play a crucial role in various industrial sectors by simplifying the connection of multiple pneumatic components. They serve as central hubs in pneumatic systems, distributing air or gas to various parts efficiently.
Industrial Sector Simplification: Central hubs in pneumatic systems, vital for the connection of components across various industries.
Automotive Production: Provide precision control over assembly tools, crucial for maintaining vehicle construction quality.
Manufacturing Automation: Utilized to manage airflow seamlessly to machinery, enhancing productivity and safety in operations.
Aerospace Reliability: Critical in controlling flight instruments and actuators, valuing their efficiency and dependability.
Robotics Integration: Aid in the fluent movement and control of robotic arms and tools, fitting into systems compactly.
Food Processing Standards: Contribute to packaging and handling while meeting cleanliness and hygiene standards through easy maintenance.
How to Choose the Right Pneumatic Manifold
Valve and Port Count: Match the manifold size and configuration to the complexity of your system.
Material Selection: Choose corrosion and wear-resistant materials like stainless steel for harsh environments; opt for lighter materials if suitable.
Operating Pressure Range: Verify manifold compatibility with the system’s maximum pressure for safety and durability.
Environmental Conditions: Consider manifold materials and design based on temperature, humidity, and chemical exposure.
Maintenance Convenience: Favor modular manifolds for systems needing regular changes, facilitating easier reconfiguration or expansion.
Connection Type Compatibility: Ensure manifold connections match your equipment for a secure, leak-free setup.
Why Are Manifolds Used?
Manifolds serve a crucial role in pneumatic systems. Their primary function is to distribute air or streamline the flow of pressurized gas to various parts of a system. This function is vital for systems that require multiple inputs and outputs to work simultaneously. Manifolds simplify complex configurations, reducing the need for numerous hoses and connections that could clutter the workspace and create inefficiencies.
One key reason for using manifolds is their ability to enhance the overall efficiency of pneumatic systems. By centralizing connections, pneumatic manifolds reduce potential leak points, ensuring a more reliable operation. This centralized approach also makes it easier to maintain and diagnose issues within the system since all critical connections are located in one place.
What is the Pressure Range of a Pneumatic System Manifold?
Pneumatic system manifolds commonly operate within a broad pressure range. Typically, this range starts as low as 20 PSI (pounds per square inch) and can extend up to 200 PSI for standard operations. However, specialized applications may require manifolds that can withstand higher pressures, sometimes exceeding 1000 PSI.
In Conclusion
Pneumatic manifolds serve as essential components in an array of industries, streamlining connections and enhancing the efficiency of systems that rely on compressed air or gas.
To understand more about how pneumatic manifolds can optimize your operational efficiency and reduce downtime, consider reaching out to industry experts. Discover the potential benefits for your business by exploring our range of solutions today.