What Is Pneumatic Valve
A pneumatic valve is a device that controls the flow and pressure of air or gas within a system, using compressed air as its operating medium. It plays a crucial role in directing and managing the pneumatic energy in various industrial applications.
Pneumatic valves are essential components in automation and control systems, providing precision and reliability. Understanding their function, types, and applications can significantly impact the efficiency and effectiveness of pneumatic systems.
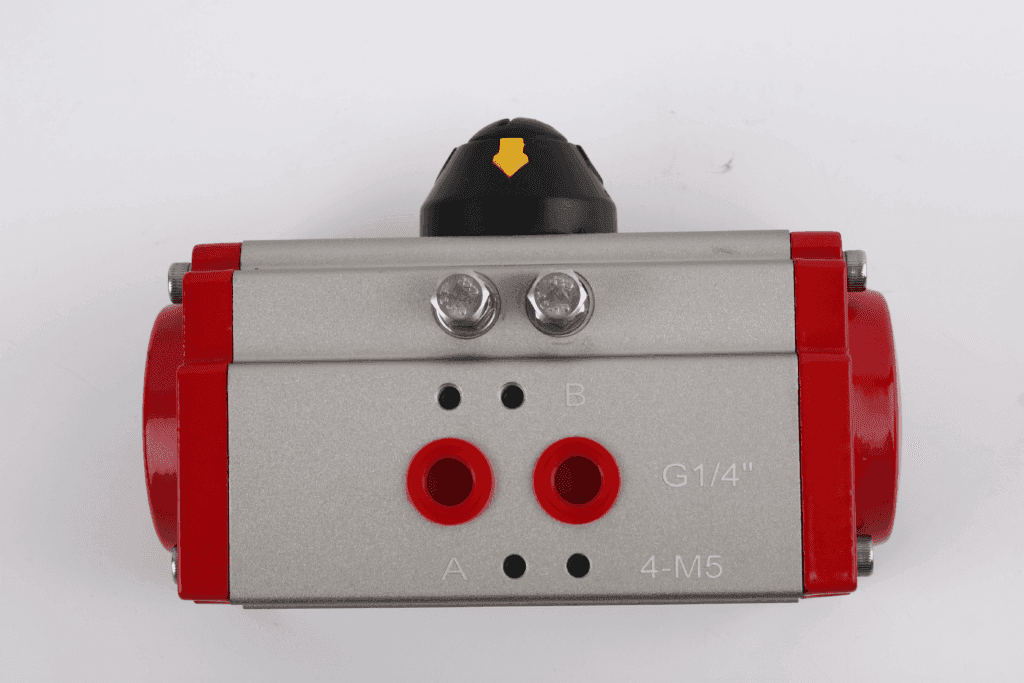
What Is Pneumatic Valve
A pneumatic valve is a device that controls the flow of air or gas through a system. It operates by translating an electrical or manual signal into movement. This movement then alters the path through which the air or gas moves.
The core function of this type of valve is to manage how air or gas moves within a pneumatic system. It can start, stop, and direct airflow efficiently.
These valves are powered by compressed air. No electricity is needed for their operation, making them safe to use in hazardous environments.
Components Of Pneumatic Valve
Pneumatic valves are essential components in various industrial applications, controlling the flow and pressure of air. Understanding their components is crucial for selection and maintenance. These valves consist of several key parts:
- Body: The valve body houses internal components, providing pathways for air to flow.
- Actuator: This mechanical device moves the valve’s stem or spool to control airflow. Actuators can be manual, pneumatic, electric, or hydraulic.
- Stem or Spool: Connects to the actuator. In spool valves, it slides to open or close ports. In other types, it might lift or rotate.
- Ports: Openings in the valve body where air enters and exits. The number of ports defines the valve type (2-way, 3-way, etc.).
- Springs: Often used to return the valve to its default position when not actuated.
- Seals and Gaskets: Ensure airtight connections between different parts of the valve to prevent leaks.
How Does Pneumatic Valve Work
A pneumatic valve controls air flow. It operates by channeling compressed air. This process involves two main actions: opening and closing pathways.
Opening enables air to move. Closing stops air movement. The valve’s structure determines its function. Some valves direct flow, others regulate pressure or flow rate.
Actuation is key in operation. Manual, solenoid, and piloted are common types. Manual requires physical effort to operate. Solenoid uses an electromagnetic coil for movement. Piloted operates with air pressure difference.
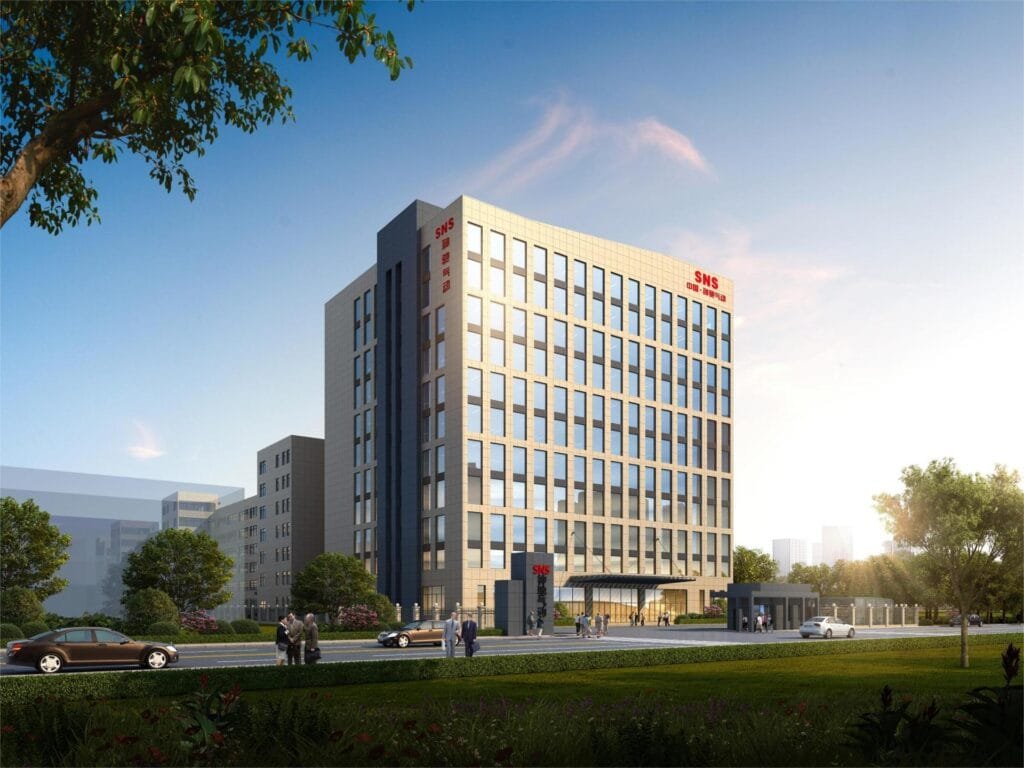
Benefits of Pneumatic Valve
Pneumatic valves, integral components in pneumatic systems, offer several benefits for controlling the flow and pressure of air or other gases. Here’s a list of their key advantages:
- Speed: Pneumatic valves enable rapid operation of system components, such as cylinders and pneumatic actuators, due to the fast action of air flow control.
- Simplicity: Their design is generally straightforward, making them easy to install, understand, and maintain.
- Reliability: These valves are highly reliable as they have fewer moving parts compared to other types, reducing the likelihood of mechanical failure.
- Cost-effectiveness: Pneumatic systems, including their valves, are often less expensive to install and maintain than their hydraulic or electric counterparts.
- Safety: They are intrinsically safe and do not pose a risk of fire or explosion, making them ideal for use in hazardous environments.
- Durability: Pneumatic valves are designed to endure harsh conditions, including high moisture and dusty environments.
- Energy Efficiency: They can be more energy-efficient, especially in applications where compressed air is readily available or where energy can be recycled.
- Clean Operation: As they use air, pneumatic systems do not contaminate the surrounding environment, unlike systems that rely on oils or other fluids.
- Versatility: Pneumatic valves can be used in a wide range of applications, from simple on-off control to complex automation systems.
- Force and Torque: Pneumatic systems can generate significant force and torque from small actuators, making them suitable for various industrial applications.
- Adjustability: The pressure and speed of pneumatic valves can be easily adjusted to suit specific requirements, offering flexibility across different applications.
- Low Power Requirements: They typically require less power to operate, as the energy is mainly used to compress air, which can be efficiently managed and controlled.
Types Of Pneumatic Valve
2-Way Valves
2-way valves are fundamental in the pneumatic systems, designed for simple operations: they either stop or allow flow. Their structure is straightforward, consisting of one inlet and one outlet. This design facilitates the direct control of fluid flow, making them ideal for basic on/off functions in many applications.
The operation of 2-way valves is quite simplistic. When activated, they open to allow flow from the inlet to the outlet. Conversely, when deactivated, they close to halt flow entirely. This binary mode of operation contributes to their reliability and ease of use.
3-Way Valves
A 3-way valve has three ports connected through passageways within the valve body. It can connect or divert the paths of pressurized air within a pneumatic system. These valves primarily serve two functions: controlling the flow of air and acting as directional valves, deciding where air should move in the system.
Each port in a 3-way valve serves a distinct role. Typically, these include the inlet (P), outlet (A), and exhaust (EA) ports. The configuration allows for either normally open or normally closed operations. In the normally open setting, air flows from P to A when no signal is applied; it reroutes to exhaust when activated. Conversely, in normally closed valves, applying a signal causes air to flow from P to A.
4-Way Valves
4-way valves are pivotal in the pneumatic valve landscape. They direct air flow efficiently, controlling actuators with precision. Typically, these valves offer four ports: two for inlet pressure, one for exhaust, and another connecting to the actuator. This design allows for reversible movement in a pneumatic system. Actuators can extend or retract based on the valve’s position.
The unique utility of 4-way valves lies in their ability to change direction swiftly. They excel in applications requiring the control of double-acting cylinders or actuators. Each slide of the valve opens and closes specific ports, directing airflow to either side of an actuator. This results in either extension or retraction.
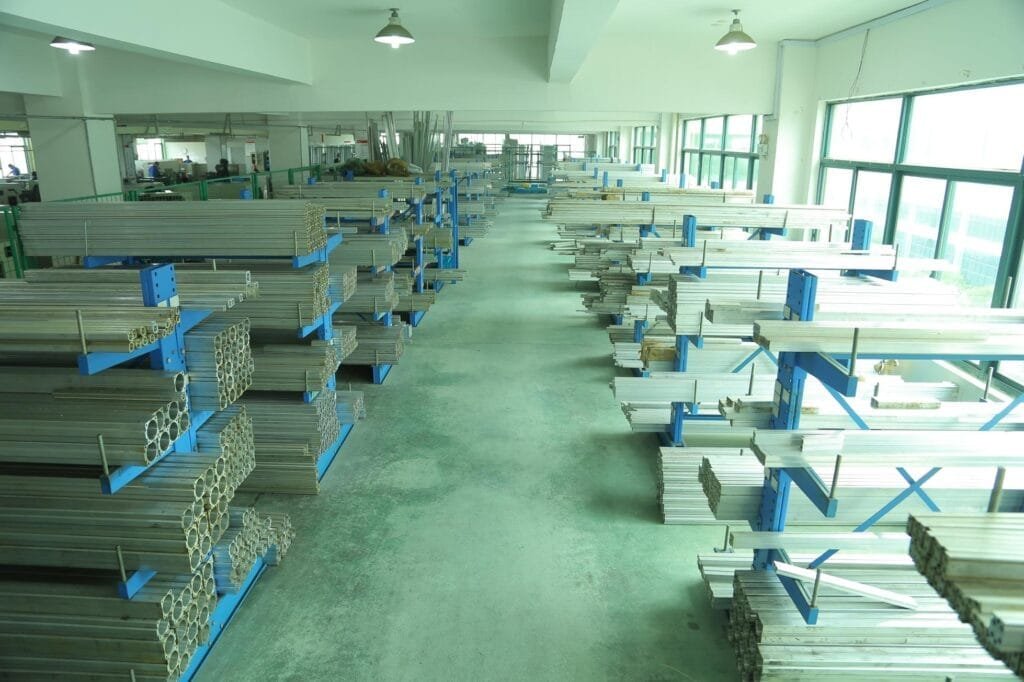
What Is The Most Common Pneumatic Valve?
The most common pneumatic valve is the 4-way valve. Its popularity stems from its versatility and efficiency in controlling air flow direction in pneumatic systems. The 4-way valve, often used in actuation applications, can direct pressurized air to both extend and retract actuators. This dual-action capability makes it indispensable for operations requiring precise motion control.
Applications of Pneumatic Valve
Manufacturing Industries: Automate and control processes, ensuring efficient and safe operation of pneumatic machinery.
Automotive Industry: Used in production lines for precise assembly of parts.
Packaging Sector: Facilitates speedy packaging, adjusting air pressure in machinery to optimize performance.
Medical Field: Used in devices like ventilators and patient handling equipment, enhancing care and safety.
Food and Beverage Industries: Helps in processing and bottling operations while maintaining sanitary conditions.
Energy Sectors: Manages flow in pipelines and controls refuelling systems to ensure safety and environmental protection.
Transportation Systems: Air brakes in buses and trucks rely on these valves for efficient functioning.
How Do I Choose The Right Pneumatic Valve For My Application?
Selecting the appropriate pneumatic valve is vital. Consider flow rate, size, pressure, and environment.
Flow Rate
Flow rate is critical in selecting a pneumatic valve. It refers to how much air can move through a valve in a given time. Measured in cubic feet per minute (CFM) or liters per minute (L/min), it determines the valve’s capacity to perform its function efficiently. The flow rate needed depends on the application’s demand.
A higher flow rate is necessary for applications requiring rapid movement or high power output. For instance, large pneumatic cylinders may need valves with high flow rates for fast actuation. Conversely, applications with smaller actuators or those that prioritize precision over speed might not require valves with very high flow rates.
Valve Size and Port Size
The valve size refers to the physical dimensions of the valve itself. It’s crucial because it determines how well the valve will fit into your system, both in terms of space and compatibility with other components. The wrong size could lead to installation challenges or inefficient operation.
Port size, on the other hand, indicates the size of the inlet and outlet openings on a valve. This dimension is paramount as it dictates how much air can pass through the valve at any given time. Larger ports allow more air flow, which is necessary for applications requiring high flow rates.
Operating Pressure
Operating pressure is a critical factor for pneumatic valves. It denotes the pressure range within which the valve operates effectively. This range impacts the valve’s performance and suitability for specific applications.
Pneumatic valves are designed to work within a defined minimum and maximum operating pressure. Exceeding these limits can damage the valve or impair its function. Lower-than-recommended pressure may not actuate the valve properly, leading to inefficiency or failure in the system.
Environmental Considerations
Firstly, temperature is a vital aspect. Both the ambient temperature and the media temperature within the system can impact valve performance. Certain valves are designed to withstand extreme temperatures, both high and low. It’s essential to choose a valve that suits your specific environmental conditions.
Secondly, contamination levels are a consideration. In environments where dirt, dust, or corrosive substances are present, it’s important to select valves with appropriate protective measures. Some valves come with enclosures rated for use in contaminated or hazardous areas.
Moisture levels also affect pneumatic valve performance. Water vapor can cause corrosion or freezing in pneumatic systems, leading to malfunction or damage. Valves made from corrosion-resistant materials or equipped with moisture protection features are necessary for humid or wet environments.
Lastly, consideration should be given to the environment’s cleanliness level required by the application. For instance, food processing or pharmaceutical industries often require equipment that meets specific hygiene standards. Pneumatic valves intended for these applications may need to be easy to clean or made from materials approved for contact with foods or medicines.
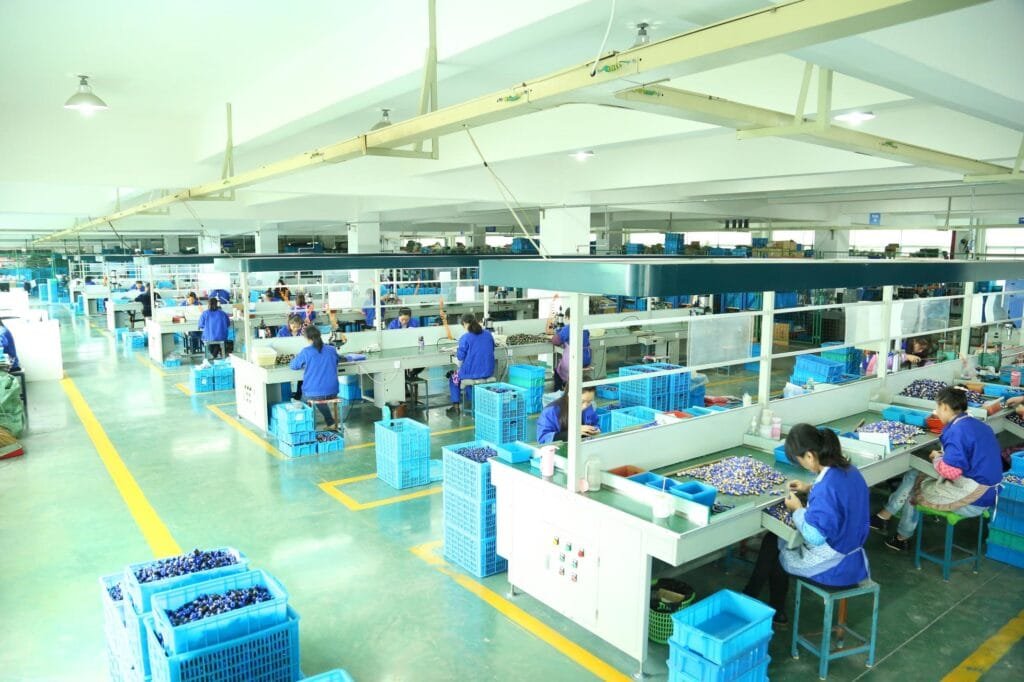
What Is The Difference Between Control Valve And Pneumatic Valve?
Mode of Operation
- Control Valve: These valves can be operated manually, or automatically via electric, pneumatic, or hydraulic means. They adjust the flow rate, pressure, or temperature of the passing fluid in response to changes in certain process conditions.
- Pneumatic Valve: These are a subset of control valves which are operated solely by air pressure. Pneumatic actuators control these valves by converting the energy from compressed air into mechanical motion.
Application and Versatility
- Control Valve: They are highly versatile, finding application across liquids, gases, and mixtures. These valves can adapt to a wide range of pressures and temperatures, making them suitable for various industries and process control applications.
- Pneumatic Valve: These valves are typically used in systems dealing primarily with air or gases at relatively low pressure. Their primary function is to regulate the flow of air and other gases within the pneumatic system.
System Requirements
- Control Valve: The choice of using control valve depends on the specific requirements of the system that includes media type (whether the media is liquid or gas), operating environment (temperature and pressure ranges), and the desired level of precision in controlling flow rates.
- Pneumatic Valve: Being solely reliant on air pressure for their operation, the choice of using these valves is primarily dependent on systems where the media includes air or gases at relatively low pressures.
In Conclusion
Pneumatic valves play a critical role in controlling the flow and pressure of air within various industrial systems, ensuring both efficiency and reliability in automated processes.
Discover how integrating pneumatic valves can optimize your operations. Visit our website or contact one of our experts today to learn more about our range of solutions tailored to meet your specific needs.