What Is Pneumatics
Pneumatics harnesses the power of compressed air to perform work.
In this blog post, we’ll explore how this technology powers industries and everyday devices.
What Is Pneumatics
Pneumatics is a branch of engineering that uses pressurized air or gas to power machines and tools. It is commonly used in industries such as manufacturing, construction, and mining to provide a safe, reliable, and cost-effective alternative to electric motors and hydraulic systems.
In a pneumatic system, a central compressor compresses air, which is then distributed through pipes or hoses to various devices like cylinders, air motors, and actuators. The compressed air is used to generate linear or rotary motion, enabling these devices to perform tasks such as lifting, pressing, cutting, sorting, or stacking.
How Pneumatic Systems Work
The main components of a typical pneumatic system include an air compressor, air tank or receiver, filters, regulators, lubricators, control valves, pipes/tubes, and actuators like cylinders or motors.
It all starts with the air compressor, which takes in air from the atmosphere and compresses it to a higher pressure, typically between 60 to 120 PSI (pounds per square inch). The compressed air is then stored in an air tank or receiver. This allows the system to maintain a steady supply of pressurized air and helps smooth out pulsations from the compressor.
From the tank, the compressed air passes through a series of filters to remove any contaminants like dust, dirt, or moisture that could damage the downstream components. The air then flows through a pressure regulator, which maintains the desired air pressure for the system. Some systems also include a lubricator that adds a fine mist of oil to the air to lubricate moving parts and prevent corrosion.
Next, the clean, dry, and regulated compressed air is directed through a network of pipes or tubes to the control valves. These valves are like traffic controllers, directing the flow of air to the actuators based on signals from the system’s controls. The most common type is a directional control valve, which can send air to different ports to extend or retract a cylinder, for example.
Finally, the compressed air reaches the actuators, which convert the air pressure into mechanical force or motion. Pneumatic cylinders, for instance, have a piston inside that moves back and forth as air is directed to either side of it. This linear motion can be used for tasks like lifting, pushing, or clamping. Rotary actuators or air motors, on the other hand, convert the air pressure into rotational motion for applications like driving a conveyor belt or powering a tool.
Once the compressed air has done its work at the actuator, it is exhausted back into the atmosphere. The cycle then repeats as long as the system is running and there is a supply of compressed air.
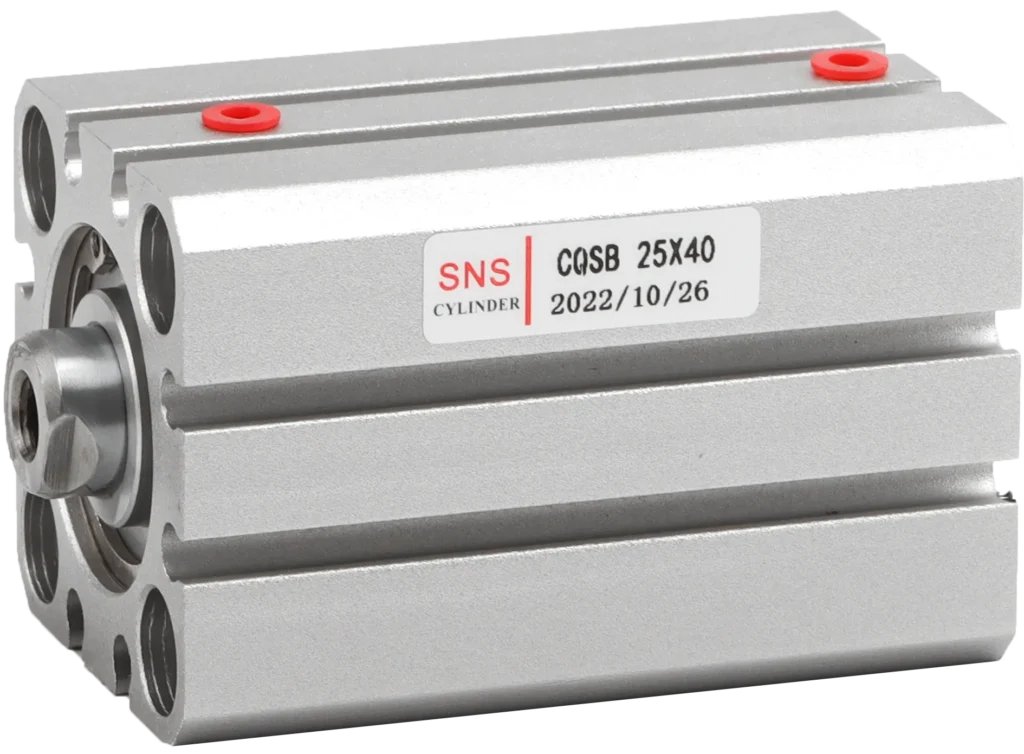
Advantages of Pneumatic Systems
- Safety: Pneumatic systems, using compressed air or inert gases, offer lower fire and explosion risks compared to hydraulic systems with flammable liquids. They also pose minimal electrical hazard and release non-toxic air in case of leaks.
- Reliability: Pneumatic components are durable, require less maintenance, and operate consistently across various temperatures due to clean, contaminant-free air.
- Cost-effectiveness: Initial and operating costs are lower than electric or hydraulic systems, with simple designs and inexpensive manufacturing of pneumatic components.
- Simplicity: Pneumatic systems have fewer moving parts, making them easier to understand, troubleshoot, and install, requiring only a single hose for air delivery.
- Compactness: Smaller pneumatic components allow for compact machine designs, with lightweight, flexible tubing ideal for weight-sensitive applications like robotics.
- Environmental cleanliness: Clean compressed air eliminates messy leaks and spills associated with hydraulic oil, crucial for industries prioritizing cleanliness like food processing and pharmaceuticals.
- Adjustability: Pneumatic cylinders offer easily adjustable force and speed through air pressure regulation and airflow controls, with built-in pressure relief valves for overload prevention.
What Gas Is Used in Pneumatics
- Compressed Air: Widely used in pneumatic systems for its abundance and ease of compression. It’s inexpensive and safe but requires moisture removal through filtration and drying.
- Nitrogen: Commonly used for its inert, non-flammable, and non-reactive properties. Prevents fires and oxidation but can cause asphyxiation, requiring good ventilation.
- Other Gases: Less commonly used gases in pneumatic systems include carbon dioxide and argon.
Common Components of a Pneumatic System
- Compressor: Draws air from the atmosphere and compresses it to about 80-120 psi, storing it in a receiver tank.
- Air Receiver Tank: Holds compressed air, allowing the compressor to run intermittently, thus enhancing efficiency and lifespan.
- Air Dryer and Filter: Removes moisture and particulates from compressed air, preventing corrosion and operational issues.
- Pressure Regulator: Adjusts the pressure from the tank to the required level for pneumatic devices, maintaining consistent output.
- Directional Control Valves: Manages airflow direction in the system, featuring ports for pressure, tank, and actuator connections. Includes solenoid options for electrical control.
- Actuators (Cylinders and Motors): Transforms compressed air into mechanical motion, either linear (cylinders) or rotary (motors).
- Tubing, Hoses and Fittings: Forms the network connecting system components and channels compressed air, using metal pipes, plastic tubing, and various fittings for assembly.
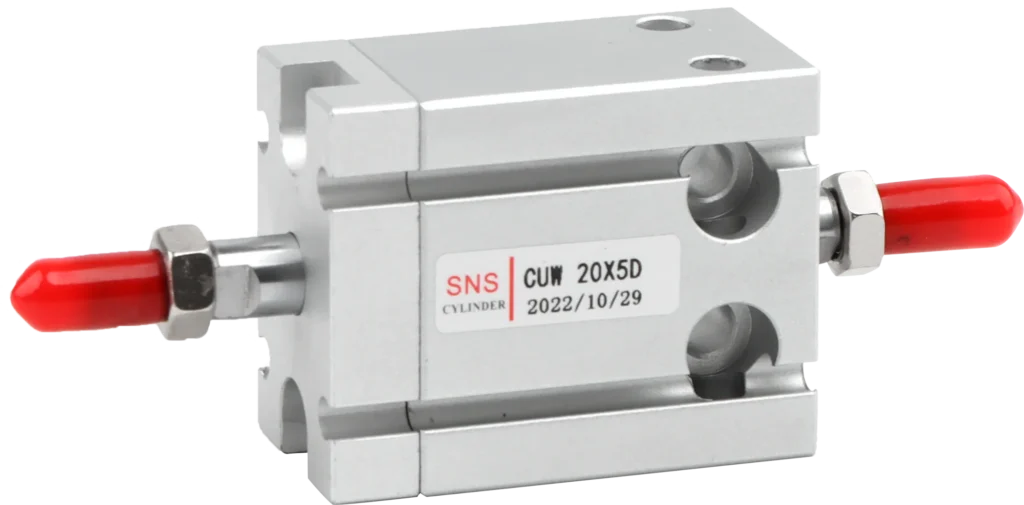
Applications and Examples of Pneumatics
Industrial Automation
One of the most common applications of pneumatics is in industrial automation. Pneumatic systems are widely used to power machines and equipment in factories and manufacturing plants. Examples include:
- Pneumatic cylinders that move, clamp, and position parts during assembly processes
- Pneumatic presses and stamping machines for metalworking
- Robotic arms and grippers that use pneumatics for picking and placing objects
- Automated conveyor systems that use pneumatic diverters and stops to route products
Construction and Mining Equipment
Pneumatic tools and machinery are also heavily used in the construction and mining industries. Examples include:
- Jackhammers and rock drills for breaking concrete and rock
- Pneumatic nail guns and staplers for fastening
- Sand blasters and pressure washers for surface preparation
- Pneumatically powered winches and hoists for lifting
Vehicle Systems
Many systems on vehicles and heavy equipment utilize pneumatics. Notable examples include:
- Air brakes on trucks and buses
- Air suspension systems for a smoother ride
- Pneumatic seats for driver comfort and vibration isolation
- Central tire inflation systems on off-road vehicles
- Air horns on trucks, trains, and boats
- Automatic doors on buses and trains
Other Examples
A few other interesting examples of pneumatics being used include:
- Dental tools like high-speed drills
- Air blasters for cleaning and drying parts
- Pneumatic tube systems for sending documents and small items
- Wind instruments like pipe organs
- Amusement park rides and animatronics that use pneumatics for motion
What Is the Difference between Pneumatic and Hydraulic
Working Fluid
Pneumatic systems use easily compressible gases like air or pure gas.
Hydraulic systems use relatively incompressible liquids like mineral oil, ethylene glycol, water, or other fire-resistant fluids.
Force and Power
Hydraulic systems can generate much higher forces and transmit more power compared to pneumatic systems.
This is because liquids are almost incompressible, so they can efficiently transfer force. Pneumatic systems using compressed air cannot match the force levels of hydraulics due to the compressibility of gases.
Typical pneumatic systems operate around 80-100 psi, while hydraulics can go up to 10,000 psi or more.
Speed and Precision
Pneumatic systems tend to be faster in operation compared to hydraulics.
The lower viscosity of air allows for quicker movement. However, pneumatics are less precise in their motions due to the compressibility of air, which can cause jerky or spongy movements.
Hydraulic systems provide smoother, more controlled and precise motion, but at slower speeds.
Size and Complexity
Pneumatic systems are usually more compact, simpler in design, and easier to maintain compared to hydraulics.
Hydraulic systems tend to be larger, as they need fluid reservoirs and more complex components. Pneumatics operate with just compressed air, requiring less equipment.
Safety and Environment
Pneumatic systems are generally safer and cleaner.
A leak of compressed air is not a major issue. Hydraulic fluid leaks can be messy and potentially hazardous, contaminating products or the environment.
Pneumatic systems are preferred where safety and cleanliness are priorities.
Cost and Efficiency
Pneumatic systems typically have lower upfront and operating costs.
Compressed air is readily available and cheaper than hydraulic fluids. However, pneumatics are less efficient, as compressed air can lose pressure and cause energy losses.
Hydraulics are more expensive to set up and maintain but provide higher efficiencies in power transmission.

FAQS
Which Is Safer Hydraulic or Pneumatic
Pneumatic systems are generally considered safer than hydraulic systems. This is because pneumatics use compressed air which is less likely to cause fire hazards and environmental damage compared to the hydraulic fluids used in hydraulic systems.
Are Pneumatics Stronger Than Hydraulics
No, pneumatics are not stronger than hydraulics. Hydraulics can generate much higher levels of pressure and force due to their use of incompressible liquids, making them more suitable for heavy-duty applications.
Is Pneumatic Cheaper Than Hydraulic
Yes, pneumatic systems are generally cheaper than hydraulic systems. This cost difference is mainly because pneumatic systems use air, which is abundant and free, and they have simpler, less expensive components and maintenance requirements.
Who Invented Pneumatics
Pneumatics, the technology of using pressurized air to perform mechanical tasks, was not invented by a single individual but has evolved over centuries.
Early contributions were made by Ctesibius of Alexandria in the 3rd century BC, who discovered the elasticity of air and developed early pneumatic devices.
Conclusion
Pneumatics plays a crucial role in various industries by utilizing compressed air to create movement or force.
This technology offers reliability, efficiency, and safety, making it indispensable in modern engineering and automation.
Explore more about how pneumatics can enhance your business operations by contacting a specialist today.