What Is Tandem Cylinder
A tandem cylinder consists of two cylinders arranged in series, where the piston rod of the first cylinder is connected to the second. This configuration often allows for increased force output within a compact design.
Tandem cylinders serve as crucial components in various hydraulic and pneumatic systems, providing enhanced efficiency and performance. Understanding their design and functionality is essential for engineers and professionals working with these systems.
What Is Tandem Cylinder
A tandem cylinder contains two cylinders aligned in series. It uses hydraulic or pneumatic pressure. The primary mechanism involves transferring the force from one cylinder to the next, enhancing overall output force. Unlike single cylinders, tandem configurations handle higher loads without increasing the cylinder diameter significantly. This setup is ideal for applications requiring significant force but limited space.
Tandem cylinders consist of two piston-and-cylinder sets connected in a line. Fluid power drives the first piston forward, which then pushes on the second piston, effectively doubling the thrust force without needing a wider cylinder. The fluid moves sequentially between cylinders through internal passages or external piping.
Their design focuses on efficiency and power maximization within confined spaces. By distributing the workload between two cylinders rather than one, wear and fatigue are reduced, leading to longer service life and increased reliability.

How Does Tandem Cylinder Work
A tandem cylinder consists of two cylinders mounted in series. The primary mechanism enables fluid to flow from one cylinder to the next. When pressure is applied, it activates the first cylinder. This action then pushes the fluid into the second cylinder, initiating movement. The process increases force output without needing more pressure.
Each cylinder has a piston connected by a common rod. Pressure applied to the first piston transfers through the rod to the second piston. This mechanism amplifies force while keeping the system compact.
Tandem cylinders can be either hydraulic or pneumatic. In hydraulic systems, oil is the working fluid. For pneumatics, air drives the action. The choice depends on application requirements.
The sequential activation of pistons provides a steady and controlled extension or retraction. This control is crucial for precision tasks.
Their design allows for higher force application within limited spaces. By using two cylinders in tandem rather than a single larger one, they save space while providing substantial power.
Components Of Tandem Cylinder
The tandem cylinder consists of two or more cylinders arranged end to end. They are used in various applications, including hydraulic systems, where they provide sequential operation or increased force without an increase in the cylinder diameter. Below are the components typically found in a tandem cylinder:
Cylinder Barrels
These are the tubes that contain the hydraulic fluid and where the piston moves back and forth. In tandem cylinders, there are at least two barrel sections connected end to end.
Pistons
Located inside the barrels, the pistons separate the cylinders into chambers. These pistons move back and forth when hydraulic fluid enters the cylinder chamber, creating force.
Piston Rods
These rods are connected to the pistons and extend out from one or both ends of the cylinder barrels. They transmit the force generated within the cylinder to the application.
Seals
Seals are used throughout the tandem cylinder to prevent the leakage of hydraulic fluid. They are found around the piston, on the piston rod, and at the connection points between the cylinder barrels.
Rod Bearings
These are used to support the piston rod as it extends and retracts. They also help to maintain alignment and reduce friction.
End Caps
The end caps close the ends of the cylinder barrels. They can also house ports for the hydraulic fluid to enter and exit the cylinder.
Ports
Hydraulic cylinders have ports that allow hydraulic fluid to enter and exit. In a tandem cylinder, there are usually more ports than in a single cylinder due to the need to control fluid flow between the connected cylinders.
Cushions
Optional components that can be added to the cylinder to slow down the piston at the end of its stroke, reducing shock and wear on the cylinder.
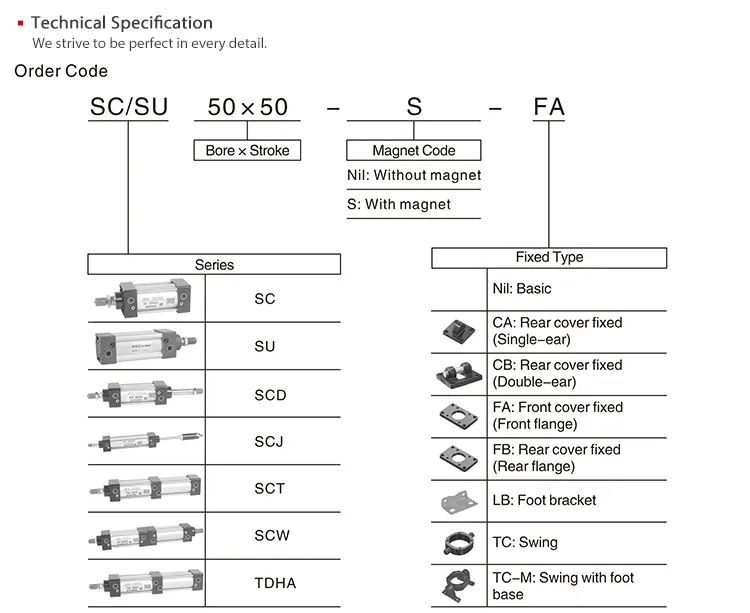
Benefits Of Tandem Cylinders
Increased Power Output
Tandem cylinders can significantly increase the power output of a system. By distributing the load between two or more cylinders, each cylinder can operate at a more efficient point in its power cycle. This leads to better overall performance and can be especially beneficial in applications requiring high power output, such as in industrial machinery or heavy-duty vehicles.
Improved Stability
The use of tandem cylinders often leads to improved stability in mechanical systems. The distributed load reduces the strain on individual components, leading to more balanced and stable operations. This can be particularly important in applications where precision and stability are crucial, such as in hydraulic lifts or aerospace technology.
Enhanced Durability
By sharing the workload among multiple cylinders, the wear and tear on each cylinder are reduced. This can significantly enhance the overall durability and lifespan of the system. Tandem cylinders can therefore be a cost-effective solution over time, as they may require less maintenance and fewer replacements compared to single-cylinder systems.
Better Control and Precision
Tandem cylinders can provide better control and precision in the movement and operation of machinery. With multiple cylinders, the force can be more finely adjusted and controlled, allowing for smoother and more precise movements. This is particularly beneficial in applications requiring delicate handling or fine movements, such as in robotics or in the medical industry.
Redundancy and Safety
In critical applications, the use of tandem cylinders can add an important layer of redundancy and safety. If one cylinder fails, the other can continue to operate, potentially preventing accidents and allowing for safe shutdowns. This redundancy is crucial in applications where safety is paramount, such as in passenger elevators or in the operation of heavy lifting equipment.
Versatility and Adaptability
Tandem cylinders offer increased versatility and adaptability in various applications. They can be designed and arranged in different configurations to meet specific needs, making them suitable for a wide range of industrial applications. Whether for lifting, pushing, pulling, or bending, tandem cylinders can be tailored to meet the precise requirements of the task at hand.
Types Of Tandem Cylinders
Synchronized Tandem Cylinders
Synchronized tandem cylinders consist of two or more cylinders connected in series, ensuring simultaneous movement of pistons. They are ideal for applications requiring uniform movement and force distribution across a large area.
Differential Tandem Cylinders
Differential tandem cylinders have pistons of varying sizes within the cylinders, allowing for different force outputs from each piston. This setup is beneficial in applications needing varied forces at different stages of operation.
Non-synchronized Tandem Cylinders
Non-synchronized tandem cylinders do not guarantee simultaneous movement of pistons. They are used where precise synchronization is not critical but where advantages like increased stroke length or force are needed without increasing the cylinder diameter.
High-pressure Tandem Cylinders
High-pressure tandem cylinders are designed to operate under extreme pressures and feature robust construction to withstand high operational stress. They are suitable for heavy-duty industrial applications.
Compact Tandem Cylinders
Compact tandem cylinders integrate two or more piston chambers within a single unit, providing double action without significantly increasing footprint. They are advantageous in space-constrained environments.
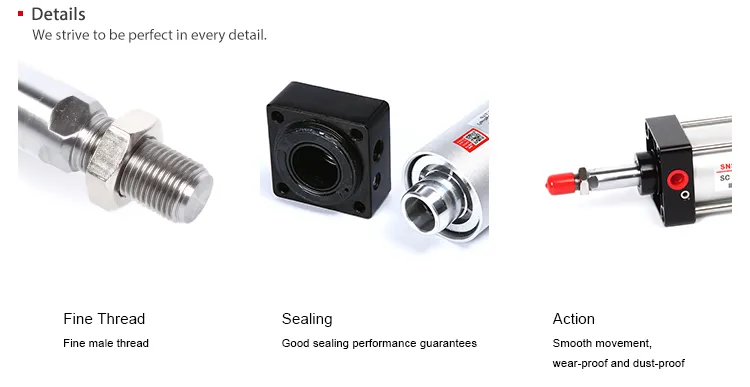
Applications Of Tandem Cylinders
Manufacturing Sector
Tandem cylinders are integral in press operations, providing the necessary force for molding, forming, or cutting materials with precision, ensuring tight tolerances and high-quality finishes.
Automotive Assembly Lines
Tandem cylinders are essential for tasks requiring significant force, such as pressing bearings into housings or installing components, ensuring efficient processes and reducing downtime due to equipment failures.
Heavy Machinery Operations
In construction and mining industries, tandem cylinders enhance lifting capacity without compromising stability or safety, improving the performance of equipment like excavators and bulldozers.
Material Handling Applications
Tandem cylinders facilitate the lifting of heavier loads with ease in warehouses and distribution centers, contributing to smoother operation logistics.
Aerospace Testing Equipment
Tandem cylinders provide precise movement controls under high load conditions, ensuring accuracy in aerospace testing equipment by evenly distributing forces.
What Does Tandem Mean In Hydraulics?
In hydraulics, “tandem” refers to a configuration where two cylinders are connected in a series. This setup allows one cylinder to follow the other in its movement, essentially doubling the force output without needing an increase in the diameter of the cylinders or the hydraulic pressure. The tandem arrangement ensures that when hydraulic fluid is pumped into the first cylinder, it extends, and once it reaches its full extension, the fluid is directed into the second cylinder, causing it to extend as well. This sequence provides a combined force from both cylinders while maintaining the advantages of compact design and efficiency.
Tandem cylinders offer a unique advantage in applications requiring high force output in environments where space constraints limit the size of a single large cylinder. Moreover, using two cylinders in tandem can enhance precision and control over extended distances because their sequential operation enables smoother motion control and distribution of load.
What Is The Difference Between A Duplex And A Tandem Cylinder?
Design and Function
- Duplex Cylinder: A duplex cylinder houses two pistons within a single barrel, each moving independently from the other. This design provides different stroke lengths and forces within a condensed physical form.
- Tandem Cylinder: Unlike duplex cylinders, tandem cylinders consist of two separate cylinders aligned in series. The system pressure propels the fluid through both cylinders, effectively doubling the force without increasing the cylinder size or system pressure.
Power Generation
- Duplex Cylinder: The versatility of duplex cylinders comes from their ability to perform two distinct movements or strokes using a single assembly, thanks to their independent pistons. These are beneficial in scenarios needing varying strokes from cycle to cycle, but where space constraints disallow the use of multiple single-stroke cylinders.
- Tandem Cylinder: In contrast, tandem cylinders offer increased power by leveraging two pistons housed in separate chambers but aligned end to end. With this setup, the active piston’s force can be practically doubled due to the backup from the second piston operating under hydraulic pressure.
Uses
- Duplex Cylinder: Duplex cylinders are often utilized when varying strokes or complex actions are needed within confined spaces. They offer customizable stroke lengths according to on-demand requirements without a significant alteration in physical dimensions.
- Tandem Cylinder: Tandem cylinders are primarily used within compact hydraulic systems when high force production is required. By facilitating sequential piston movement, these cylinders efficiently maximize force output under specific operating conditions.
In Conclusion
A tandem cylinder, characterized by its sequential arrangement of cylinders to enhance force multiplication without increasing the size of the cylinder footprint, represents a sophisticated solution for various industrial applications needing precise and powerful linear motion control.
Explore the potential that tandem cylinders can bring to your specific needs by engaging with our expert team. Don’t hesitate to reach out for further insights and customized solutions that can transform efficiency and performance in your operation