What Is The Air Used In A Pneumatic System?
Pneumatic systems rely on compressed air to transmit and control energy, powering a vast array of tools and machinery. The quality and properties of the air used are crucial for the system’s efficiency and longevity. Understanding the characteristics of this air is essential for those who design, maintain, or utilize pneumatic equipment.
This article will dissect the composition of air in pneumatic systems and delve into its preparation process. Learn about the role of air quality in ensuring optimal performance and preventing equipment degradation.
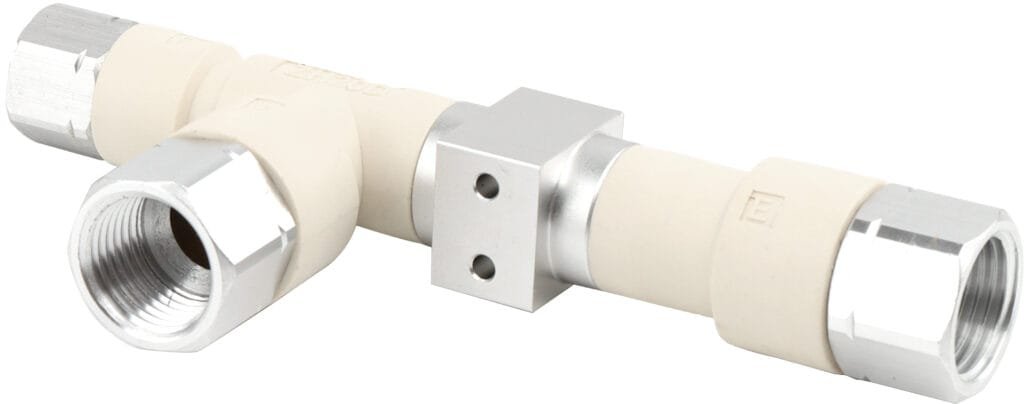
What is the air used in a pneumatic system?
- Air
- Nitrogen
- Carbon Dioxide
Air
Pneumatic systems function by utilizing compressed air to transmit energy and perform work. The air must be clean, dry, and free from oil or contaminants to avoid damage to equipment components. Sophisticated filtration systems are often integrated within these setups to ensure the quality of the air utilized.
The rationale behind using compressed air lies in its abundance and safety; it is readily available in the environment and non-flammable, which minimizes risks associated with its use compared to other gases. When pressurized within a pneumatic system, this air can be controlled with great precision through valves and actuators, making it incredibly versatile for various industrial applications.
One critical consideration when using compressed air is managing moisture content because water vapor can condense within the system, leading to corrosion or malfunctioning of parts. Thus, pneumatic systems typically include dryers that remove moisture and protect against related issues.
Moreover, different operating pressures are required based on the specific application’s demands – from delicate operations that need low pressure to those requiring high-force output which mandates higher pressure levels. Compressed air’s adaptability allows it to cater seamlessly across this spectrum while maintaining efficiency.
Property | Specification |
---|---|
Medium | Compressed Air |
Availability | Abundant |
Safety Characteristics | Non-flammable |
Environmental Impact | Minimal |
Quality Requirement | Cleanliness (free from oil/contaminants) |
Moisture Management | Essential (use of dryers) |
System Components | Filters, Dryers, Valves, Actuators |
Versatility | High (suitable for varied industrial applications) |
Operating Pressure Requirements | Low-High (based on application-specific demands) |
Nitrogen
Nitrogen, due to its stable and inert properties, has become the most prevalent gas utilized in pneumatic systems.
Pneumatic systems, which rely on controlled amounts of compressed gas to transmit force and motion, often harness nitrogen over other gases because of its distinct advantages. As an inert gas, nitrogen is less reactive than oxygen-laden air, reducing the risk of oxidation and corrosion within system components. This property lengthens the lifespan of both the system itself and the equipment it powers. Furthermore, nitrogen’s low moisture content ensures that humidity-related issues such as freezing or water vapor-induced degradation are minimized in critical applications.
Nitrogen’s consistent quality is another reason why it is favored in pneumatics. It can be produced to a high degree of purity, ensuring reliable performance without contamination from other gases or impurities which could cause fluctuations in system behavior.
Additionally, safety concerns play a role in nitrogen’s popularity for pneumatic applications; it reduces fire hazard risks compared to air-filled systems since nitrogen is non-flammable. In industries where flammability hazards are inherent—such as oil and gas or chemical manufacturing—using nitrogen can therefore contribute significantly to overall safety measures.
Another relevant factor is the ease with which nitrogen can be stored and handled. High-pressure cylinders or on-site generation deliver this versatile gas effectively to point-of-use without major complexities related to transportation or storage.
Despite these numerous benefits provided by nitrogen in pneumatic systems, care must be taken when using pressurized gases—especially during equipment servicing—as they do present safety risks such as potential pressure-related accidents if not managed appropriately.
Aspect | Detail |
---|---|
Stability | Less reactive than oxygen; minimizes oxidation |
Moisture Content | Low; decreases humidity-related problems |
Purity | Can be produced at high purity levels |
Safety | Non-flammable; lowers fire hazards |
Storage & Handling | Easily stored and transported |
Risk Management | Requires careful handling due to pressurization |
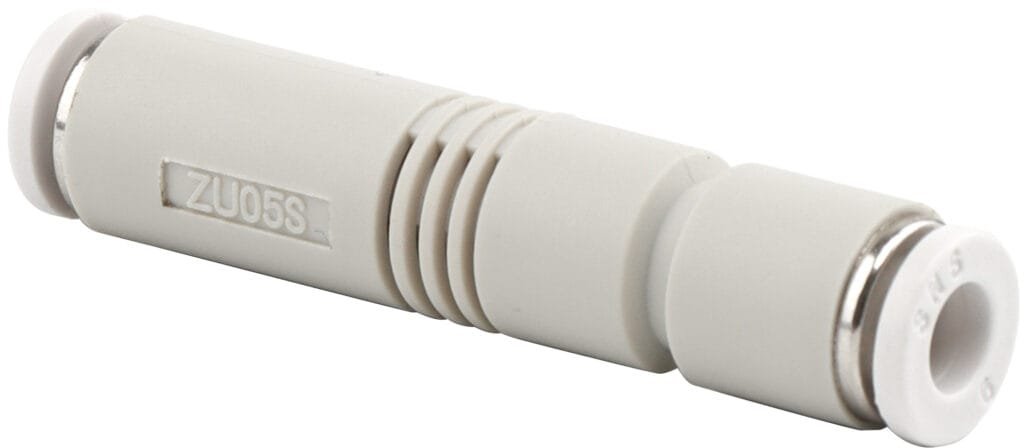
Carbon Dioxide
Carbon dioxide is less commonly used in pneumatic systems compared to air and nitrogen, but it has specific applications where its properties are advantageous.
In pneumatic systems, the use of carbon dioxide (CO2) is somewhat niche but still significant in certain industries. CO2 is a heavier gas than both air and nitrogen, which can impact the behavior and design of a pneumatic system. One key attribute of carbon dioxide is that it can exist as a liquid at a higher pressure within cylinders, allowing for more gas to be stored in a smaller volume. This property makes CO2 well-suited for portable pneumatic tools that need compact energy sources.
However, there are aspects to consider if employing carbon dioxide in pneumatics. For instance, it can react with water to form carbonic acid, which may corrode metal components over time; this emphasizes the need for moisture control within the system. Additionally, CO2 can undergo substantial changes in pressure due to temperature fluctuations because of its critical point characteristics—a factor that must be accounted for in system planning and operation.
Despite these concerns, carbon dioxide offers certain benefits such as reduced fire risk when compared with flammable gases or oil-lubricated systems due to its inert nature coupled with inherent fire suppression qualities. Given these characteristics and potential issues, the selection of carbon dioxide for a pneumatic system should be done carefully with consideration for all operational parameters.
Factor | Details |
---|---|
Usage | Less common – specific applications where advantageous |
Weight | Heavier than air and nitrogen |
Storage | Can store as a liquid at high pressure – allows more gas in smaller volume—beneficial for portable tools |
Reactivity | Can form corrosive carbonic acid if mixed with water – need for moisture control |
Temperature Sensitivity | Subject to pressure change from temperature fluctuations due to critical point – requires careful planning |
Safety | Reduced fire risk compared to flammable gases or oils; inert nature provides fire suppression capabilities |
In Conclusion
In summary, a pneumatic system utilizes compressed air as its working fluid to perform various industrial tasks through energy transfer.
To learn more about how pneumatic systems can optimize your operations, don’t hesitate to contact our experts. Discover the power and efficiency of tailored pneumatic solutions for your business needs today.