What is the Difference Between Solenoid Valve and Pneumatic Valve
The primary difference between a solenoid valve and a pneumatic valve is their mode of actuation; solenoid valves are electrically actuated using a solenoid, whereas pneumatic valves are air-powered. Moreover, solenoid valves typically control the flow of liquid or gas, while pneumatic valves control air pressure in systems.
Understanding the distinct functionalities and applications of solenoid and pneumatic valves is crucial for selecting the right component in industrial, mechanical, or fluid control systems. This article delves into the operational principles, advantages, and typical uses of both types of valves to inform your decision-making process.
What Is Solenoid Valve
A solenoid valve is an electromechanically operated valve. It utilizes an electromagnetic solenoid for its functioning. The role of the solenoid is to control the opening and closing of the valve. When electric current passes through the solenoid coil, a magnetic field is generated. This magnetic field moves a plunger inside the coil, thereby opening or closing the valve. The operation hinges on electrical energy to actuate the valve.
These valves can operate in either a normally open (NO) or normally closed (NC) state when de-energized. This functionality depends on the design and requirement of the system it’s integrated into. Solenoid valves offer precise control over fluids and gases, which makes them essential in applications requiring accurate flow regulation.
Types Of Solenoid Valve
Solenoid valves are divided based on their operation mechanism, construction, and applications. The main types include direct-acting, pilot-operated, 2-way, 3-way, and 4-way solenoid valves.
Types of Solenoid Valve: Based on Operation Mechanism
- Direct-Acting Solenoid Valve: These valves are simple in design, using a plunger to either open or close the valve. When energized, the coil lifts the plunger, allowing fluid flow. They are particularly useful in low-flow situations.
- Pilot-Operated Solenoid Valve: These valves use system pressure to regulate the opening and closing of the valve. Comprising of a pilot and main valve body, they require less power to control larger fluid flows, compared to direct-acting valves.
Types of Solenoid Valve: Based on Number of Ports
- 2-Way Solenoid Valve: These valves feature two ports – an inlet and an outlet. They are employed to allow or inhibit fluid flow. Their straightforward nature makes them suitable for a wide array of applications.
- 3-Way Solenoid Valve: Equipped with three ports, these valves are designed to switch fluid flows between two outlets, making them popular in applications that require an alternative path for fluid flow.
- 4-Way Solenoid Valve: These versatile valves feature four ports, allowing for the direction of flow along multiple paths in pneumatic control systems.
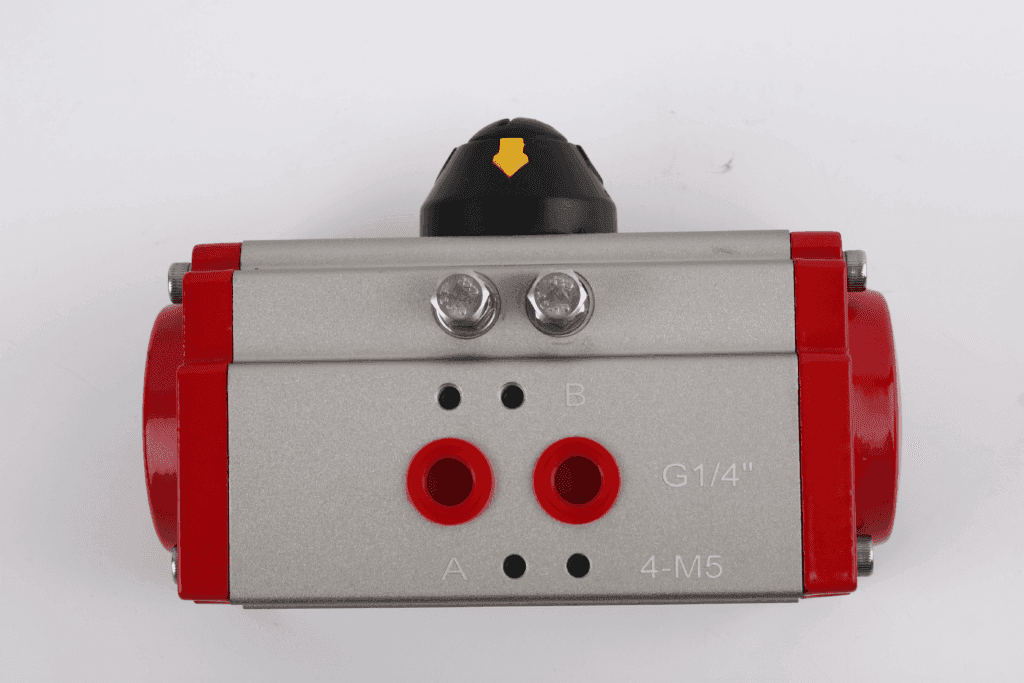
Advantages Of Solenoid Valve
Accurate Control: Solenoid valves offer precise start, stop, and flow direction control, essential for processes requiring exact fluid or gas control.
Lower Power Consumption: Once activated, solenoid valves maintain their state with minimal energy, ideal for continuous use and energy efficiency.
Fast Response Times: Solenoid valves can open or close quickly, ideal for tasks needing rapid action like emergency stops or system startups.
Compact Size: Smaller than most pneumatic valves, solenoid valves can fit into tighter spaces where space is a premium.
Versatility: Solenoid valves can handle various media types — air, water, oil, chemicals — useful across diverse industries.
Easy Installation & Maintenance: Solenoid valves’ simplicity allows for quick installation and low maintenance, reducing downtime and operational costs.
Pressure Capabilities: Solenoid valves can operate effectively under different pressures, from vacuum conditions to high-pressure settings.
Reliability: With fewer moving parts than pneumatic valves, the risk of malfunction decreases, enhancing system reliability.
What Is Pneumatic Valve
A pneumatic valve is a device used to control the flow of compressed air. It operates by allowing or blocking this airflow in a pneumatic system, which powers various industrial applications. These valves come in different types, each serving specific functions within pneumatic systems. Some common types include directional control valves, flow control valves, and pressure relief valves. Directional control valves adjust the path of air flow. Flow control valves regulate the speed and volume of air passing through. Pressure relief valves maintain safe pressure levels by releasing excess air.
Types Of Pneumatic Valve
Directional Control Valves are fundamental in pneumatic systems. They control the path of air flow, directing it to specific parts of a system when needed. These valves vary by the number of ports and flow paths, commonly referred to as 2-way, 3-way, or 4-way valves. The selection depends on whether a system requires air to be directed in two directions, mixed, or divided.
Flow Control Valves, regulate the flow rate of air within a pneumatic system. Adjusting the flow rate can control the speed of actuators or tools connected to the system. These valves ensure movements are smooth and controlled rather than rapid and unregulated.
Pressure Regulating Valves manage the pressure within a pneumatic system by maintaining or limiting it to a preset level. High-pressure situations can be dangerous and lead to equipment damage; hence these valves are vital for safety and longevity of system components.
Check Valves, also known as non-return valves, allow airflow in one direction only. They prevent backflow which could potentially damage the system or disrupt operation. Check valves are essential in systems where airflow directionality needs strict regulation.
Advantages Of Pneumatic Valve
Safety: Pneumatic valves, powered by compressed air, are safe for use in explosive environments and don’t rely on electricity, eliminating electrical fault risks.
Durability: Withstanding harsh conditions and substances, like chemical exposure, vibrations, and temperature shifts, these valves offer a longer lifespan and less frequent replacement.
Rapid Operation: Pneumatic valves can open and close exceptionally fast, ensuring quick system responses crucial for swift action-demanding processes.
Simplicity & Ease of Maintenance: Their straightforward design and fewer moving parts make servicing less complicated and time-consuming, improving operational efficiency by minimizing downtime.
Energy Efficiency: Well-designed pneumatic systems with these valves consume less power compared to other actuation methods, reducing operational costs over time.
Control Precision: Pneumatic valves provide precise control over flow rate and direction with minimal leakage, improving system reliability and productivity. This precision is essential for optimal outcomes in applications requiring exact parameter management.
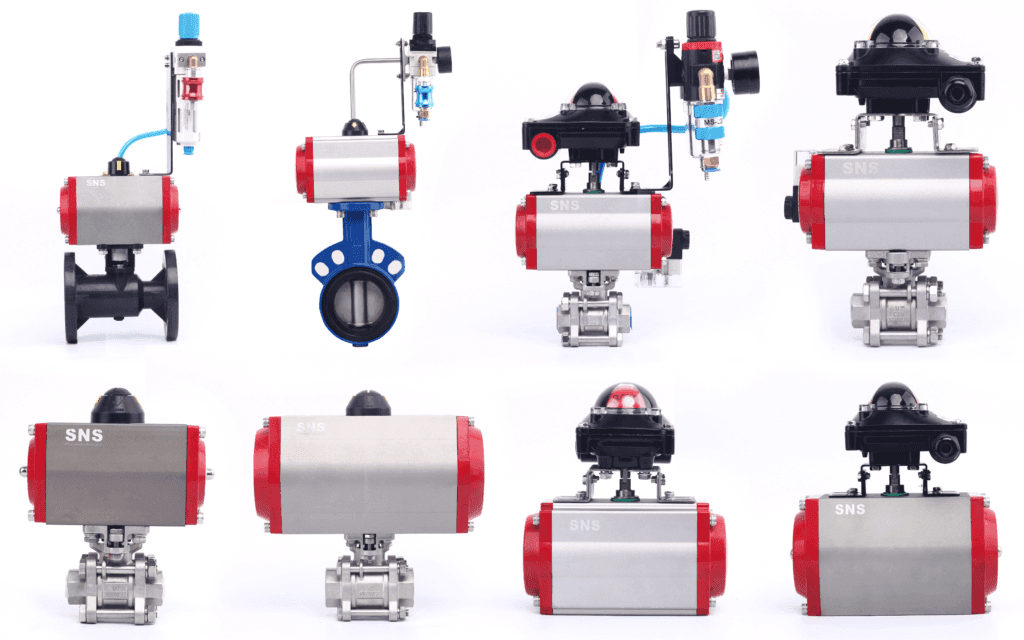
Key Differences Between Solenoid And Pneumatic Valves
Solenoid valves and pneumatic valves serve similar functions but differ significantly in their operation, applications, energy source, operational speed, response times, reliability, and maintenance requirements.
Mechanism Of Operation
A solenoid valve operates electronically. It has a coil that, when energized, creates a magnetic field. This magnetic field moves a plunger inside the valve, opening or closing it. It’s a direct action process. Solenoid valves can be normally open or normally closed, changing state when powered. Their operation is straightforward – electricity on or off dictates the valve’s position.
Pneumatic valves, on the other hand, use air pressure for their operation. They rely on pneumatic actuation to open, close, or modulate flow. Air pressure acts upon a piston or diaphragm within the valve, causing it to move and change the state of the valve. The mechanism depends on air flow and pressure rather than an electric current.
Applications
Solenoid valves are vital in controlling the flow of fluids in various systems. They serve a range of applications, from simple water dispensing mechanisms to intricate fuel regulation in automotive systems. Their design allows them to be used in both liquid and gas mediums, making them versatile components in industrial, residential, and commercial settings.
Pneumatic valves, on the other hand, regulate air pressure within systems. They are commonly found in factory automation setups where they manipulate air to control mechanical movements. These valves play crucial roles in actuating pneumatic cylinders, controlling process flows, and managing material handling operations. Their reliability and speed make them indispensable in scenarios requiring rapid and precise control over air movement.
Energy Source
Solenoid valves use electrical energy to operate. When electricity is applied to the coil in the valve, it generates a magnetic field. This field moves a plunger inside the valve, opening or closing it. Thus, solenoid valves need an external power source, usually from an electrical grid or battery.
Pneumatic valves, on the other hand, are powered by pressurized air. Air pressure is used to move parts within the valve to open or close it. These valves rely on a supply of compressed air, which may come from an air compressor or a centralized pneumatic system.
Speed of Operation and Response Times
Solenoid valves respond rapidly to control signals. Their operation can be almost instantaneous, usually within milliseconds. This makes solenoid valves suitable for applications where time is critical, such as in fluid power systems or emergency shutdowns. The swift action stems from the direct electromagnetic actuation involved in their operation.
Pneumatic valves, while also capable of quick response times, typically do not match the speed of solenoid valves. Their response time is influenced by factors like air supply quality and pressure, tubing length, and valve design. Although fast, pneumatic valves often have response times measured in tens of milliseconds or more.
Reliability And Maintenance Requirements
Reliability and maintenance are critical aspects that differentiate solenoid valves from pneumatic valves. Solenoid valves boast higher reliability in controlled environments with electrical power. Their operation relies on electromagnetic forces, minimizing physical wear and tear. This feature generally results in lower maintenance needs compared to mechanical systems. However, solenoid valves require a stable power supply, and their performance can be affected by voltage variations or electrical disturbances. Electrical components may also need periodic inspection or replacement, particularly in harsh environments.
Pneumatic valves, on the other hand, depend on air pressure for their operation. They exhibit high durability in rough conditions and can handle larger flow rates than solenoid counterparts. Pneumatic systems tolerate moisture and dust better, making them suited for outdoor or industrial applications where such conditions are prevalent. Maintenance involves ensuring a clean and dry air supply to prevent internal corrosion or malfunction. Additionally, seals and moving parts may require regular checks for wear and lubrication to maintain optimal performance.
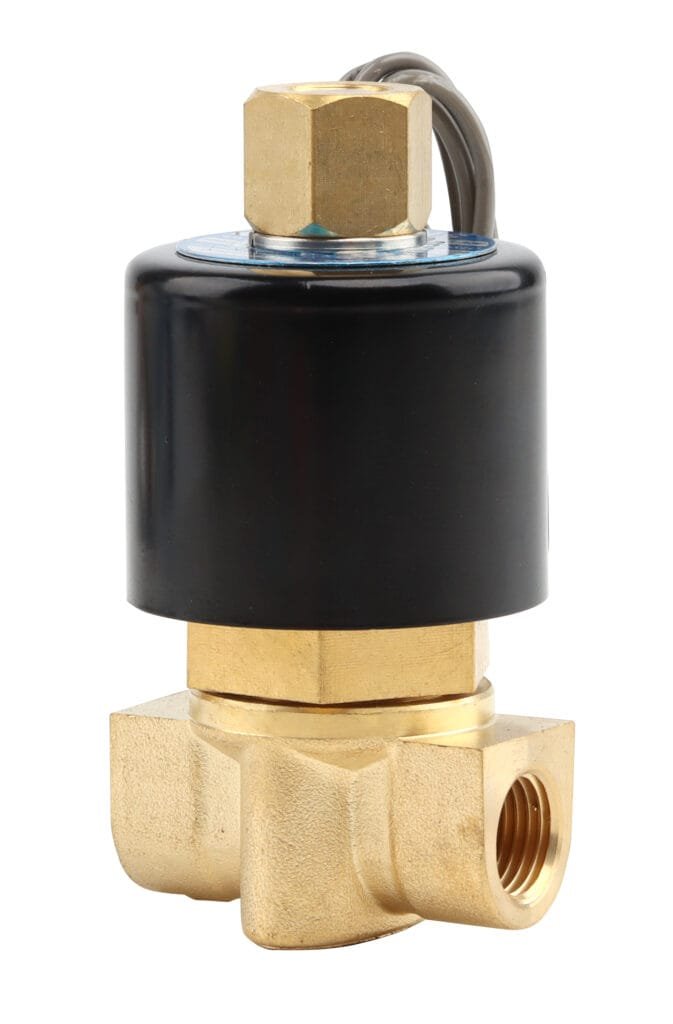
Factors To Consider When Selecting A Valve
Media: Consider what the valve will control — gases, liquids, or semi-solids. Certain materials like corrosive chemicals may necessitate special valve materials.
Pressure: The valve must be capable of withstanding the maximum system pressure. Inadequate pressure rating can cause valve failure.
Temperature: High temperatures may require valves made from materials resistant to thermal stress to prevent deformation or deterioration.
Environment: The site of valve installation, especially harsh environments with extreme temperatures or corrosive atmospheres, require more durable valves.
Can A Solenoid Be Pneumatic?
Yes, a solenoid can be part of a pneumatic system. A solenoid valve controls the flow of air in pneumatic equipment. It does this by using an electromagnetic solenoid to open or close the valve. When electricity activates the solenoid, it moves a plunger. This movement either opens or closes the valve, allowing or stopping air flow.
Are Solenoid Valves More Expensive Than Pneumatic Valves?
Solenoid valves tend to have a higher initial cost compared to pneumatic valves. This difference in pricing is attributed to the complexity of solenoid valves. They incorporate electromechanical components which are typically more expensive to produce than the mechanical parts used in pneumatic valves. Additionally, solenoid technology requires precision in manufacturing and often involves higher quality materials.
How Quickly Do Solenoid Valves Respond Compared To Pneumatic Valves?
Response times for solenoid valves are often measured in milliseconds. This speed enables high-efficiency operations in various contexts. Conversely, pneumatic valves might take several seconds to respond. Their speed depends on factors like air flow rate and pressure.
Can Solenoid Valves Be Used With Any Type Of Fluid?
No, solenoid valves cannot be used with any type of fluid. They are designed for specific types of fluids, and using them with incompatible liquids or gases could damage the valve or cause it to malfunction. Therefore, it’s essential to ensure the solenoid valve matches the fluid used in your system.
In Conclusion
In essence, while solenoid valves are driven by electrical signals to control the flow of liquids or gases, pneumatic valves rely on air pressure for operation, each serving distinct purposes in various industrial applications.
To gain a deeper understanding of how these valve types can optimize your processes and energy efficiency, we encourage you to explore further. Connect with our experts today for tailored solutions that match your specific needs.