What Psi Should A Pressure Regulator Be
Navigating the world of pressure regulators and the ideal psi settings for various applications can be complex, but understanding these can significantly impact the efficiency and longevity of your equipment.
Whether it’s for your home water supply, irrigation, or compressed air systems, getting the pressure right is crucial.
Here, we’ll explore how to achieve the optimal psi for your needs and the consequences of not doing so.
The Ideal Psi For Different Applications
You need to understand that the ideal psi settings vary considerably across applications, each demanding a precise adjustment for best performance.
Home Water Supply
Selecting the optimal psi (pounds per square inch) for home water supply systems is crucial. The ideal range is 40 to 60 psi. This ensures efficiency and safety.
A psi within 40 to 60 supports everyday tasks. These include showering and dishwashing. It prevents damage to pipes and appliances.
Going above 60 psi risks the plumbing infrastructure. It can cause premature wear and failures.
Below 40 psi, water flow becomes inadequate. This impacts appliances and fixtures reliant on water.
Irrigation Systems
Drip irrigation systems operate effectively at pressures ranging from 20 to 30 psi. This lower pressure ensures water reaches plant roots directly. It minimizes water loss through evaporation.
In contrast, sprinkler systems need 30 to 50 psi. Higher pressures cover larger areas efficiently.
Compressed Air Systems
Compressed air systems play a crucial role in a wide range of applications. These systems, from powering industrial machinery to running pneumatic tools, rely heavily on precise psi (pounds per square inch) settings. Achieving the correct psi setting is vital for both performance and equipment longevity.
For industrial applications, the psi settings typically fall between 70 and 90. This range ensures that machinery operates effectively without the risk of over-pressurization. Over-pressurization can cause significant damage, leading to costly repairs or replacements.
Pneumatic tools, in contrast, usually require a slightly higher psi setting, generally from 90 to 100. This specific range optimizes tool performance by balancing force and precision. It ensures that tools function at their peak, extending their service life.
Consultation of tool and machinery manuals is critical. Manufacturers often provide recommended psi settings. These recommendations are based on extensive testing and should be adhered to for optimal results. Deviating from these suggestions can result in inefficiencies or even damage to the equipment.
Gas Grills And Rvs
For gas grills, the standard psi setting is around 0.4. This precise pressure is key for maintaining an even cooking surface. It helps in avoiding flare-ups, which can pose a danger. Achieving the correct temperature balance is crucial for cooking food evenly.
RVs, with their complex gas systems, also require a careful psi setting. The standard is 11 inches water column, about 0.4 psi. This pressure ensures that appliances like stoves and heaters work properly. Consistent and reliable gas flow is essential for these systems to operate smoothly.
Using a pressure regulator is necessary for both gas grills and RVs. It must be accurately adjusted to the required psi settings. This ensures the safety and efficiency of these units. An incorrect psi setting can lead to operational failures or even safety risks.
It’s important to emphasize the role of precision in setting the correct psi. Both too high and too low pressures can cause problems. For gas grills, incorrect pressure can lead to uneven cooking or dangerous conditions. For RVs, it can mean malfunctioning appliances.
Hydraulic Systems
Hydraulic systems require precise pressure adjustments for optimal performance and safety. Different applications necessitate varying psi levels. For example, manufacturing equipment often demands higher psi for efficient heavy lifting. Conversely, automotive brake systems need lower psi to ensure smooth operation and reduce wear.
Understanding the specific requirements of the machinery is crucial. Environmental factors also play a significant role in determining the correct psi settings. Incorrect adjustments can lead to system failures or create safety risks. Setting the psi too high may cause equipment breakdowns. On the other hand, too low a setting can result in insufficient force or sluggish performance.
It is essential to consult the system’s specifications for accurate psi settings. A hydraulic engineer can provide expert guidance on the ideal pressure levels. This ensures the machinery operates safely and efficiently, tailored to its particular application.
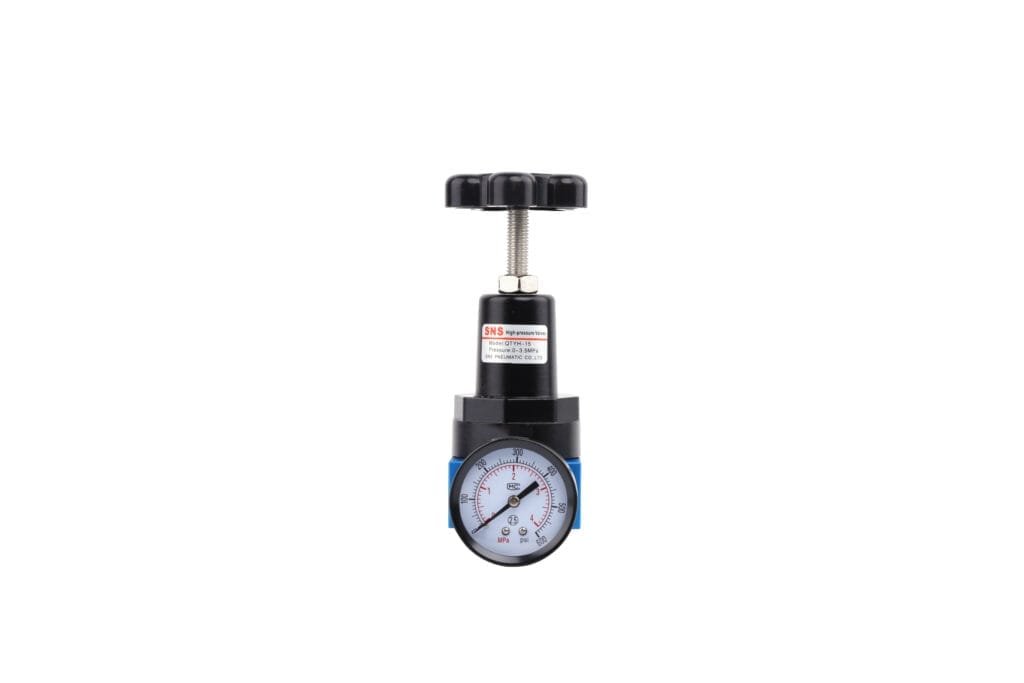
Considerations For Setting Pressure Regulator Psi
Manufacturer’S Specifications
Adjusting the pressure regulator psi with precision is crucial. This ensures optimal equipment function and maintains safety standards. Different manufacturers design their regulators for specific conditions. These include the range of inlet and outlet pressures and how much flow they can handle.
Neglecting manufacturer guidelines can cause several problems. Equipment may not work as efficiently. There’s also a risk of damage to the equipment. In some cases, it can even create dangerous situations.
The manufacturer’s instructions or technical support will provide necessary details. These specifications are essential for proper setup.
It’s important to choose a regulator that fits the system’s needs. For example, systems requiring high flow rates need regulators that can manage such demands. This ensures the system remains stable and precise.
Following these specifications is key for safety. It also helps in prolonging the lifespan of both the regulator and the equipment it supports.
Application Requirements
To set the pressure regulator psi accurately, it’s crucial to first understand the manufacturer’s specifications. This foundational step is key to aligning with the specific needs of your application.
Next, evaluate your system’s operational conditions. This involves a close look at the flow rate demands. For applications requiring high flow rates, a corresponding increase in psi setting may be necessary. This adjustment ensures the system remains efficient and avoids performance issues.
Additionally, consider the viscosity of the fluids your system handles. Systems dealing with more viscous fluids often need a higher pressure setting. This is because thicker fluids move more slowly and require additional force to propel them through the system efficiently.
Adjusting the pressure regulator to match these requirements is vital. It optimizes performance and prevents undue stress on system components. Precise calibration, based on flow rate and fluid viscosity, ensures the system functions within its optimal parameters.
This careful calibration also plays a crucial role in extending the lifespan of your system. By operating within the intended parameters, the risk of premature wear or failure is significantly reduced.
Safety Margins
Adding safety margins to pressure regulator psi settings is crucial. It ensures your system works safely and effectively. To find the right psi, consider the highest operating pressure. Then, add a safety margin. This step helps manage unforeseen pressure spikes or changes.
A safety margin prevents wear on components. It also extends their life and maintains system reliability. Usually, adding 10-20% more than the maximum load is enough. This extra buffer protects without causing extra strain or wear.
It’s important to look at your system’s specific needs. Consider flow rates and what materials are compatible. Adjust the safety margins based on these factors. This customization is key to getting it right.
Setting the margin too high can stress parts unnecessarily. Setting it too low could lead to system breakdowns. So, precise calculations are essential for both safety and efficiency.
Water Hammer Effect
To prevent the water hammer effect, adjusting psi levels on pressure regulators is crucial. This effect causes sudden pressure surges, damaging pipes. It happens when fluid flow is abruptly halted or redirected, generating a pressure wave. This can result in pipe failure or leaks.
To counteract this, set the pressure regulator to an optimal psi. This balance minimizes shock while maintaining flow. It requires calculating water velocity and how quickly the system can close valves. Correct psi settings reduce water hammer risk and ensure efficient flow.
Precision in setting psi is vital for the system’s durability and reliability. Each adjustment must carefully consider flow rate and potential shock impact. This approach ensures the longevity of piping systems and prevents damage.

Faqs
What Is The Standard For Pressure Regulators?
The standard for pressure regulators is critical for ensuring these devices function within safe and efficient parameters. Regulatory standards are established by authoritative entities like the American Society of Mechanical Engineers (ASME) and the International Standards Organization (ISO). These entities set the criteria that pressure regulators must meet. Such criteria include maximum pressure, temperature ranges, and material compatibility requirements.
For instance, ASME B31.1 and B31.3 are recognized codes. They guide the design and fabrication of pressure regulators. ASME B31.1 focuses on power piping, while B31.3 pertains to process piping. These codes cover design, materials, testing, and inspection aspects. Their purpose is to guarantee reliability and safety across various applications.
Adherence to these standards is vital for manufacturers. Compliance ensures that their products meet global market demands and regulatory expectations. This adherence isn’t just about meeting legal requirements. It also signals to customers that a product is reliable and safe for its intended use. Therefore, understanding and following these standards is a cornerstone of manufacturing and deploying pressure regulators.
How Many Psi Is A High Pressure Regulator?
High-pressure regulators are essential for managing gas or liquid pressures from tanks or pipelines. They typically function within a range of 100 to 6000 psi. This range varies based on the application and the specific demands of the industry in question.
Selecting the correct high-pressure regulator is crucial. It must have a maximum inlet pressure capacity that ensures both safety and operational efficiency. This selection process involves understanding the required outlet pressure and the necessary flow rate for your system.
Can The Psi Of A Pressure Regulator Affect Water Bills?
A pressure regulator’s psi setting can indeed influence your water bills. This effect stems from the relationship between water pressure and flow rate.
When the psi is set higher, water flows through pipes more rapidly. This accelerated flow means that more water is used over the same period than with a lower psi setting.
Therefore, a high psi setting on your pressure regulator may lead to increased water usage. This, in turn, can cause a rise in your water bills.
Finding the right psi setting is crucial. The goal is to balance strong water pressure for daily needs with mindful water consumption.
Experts often recommend a psi setting between 50 to 60. This range is considered optimal for both efficient water use and maintaining satisfactory water pressure.
By adjusting your pressure regulator to this recommended psi, you can help control your water usage. This adjustment could result in lower water bills.

What Happens If The Psi Is Set Too High?
Setting the psi too high in your pressure regulator can have serious consequences. This condition strains the entire plumbing infrastructure.
High psi forces pipes, joints, and fixtures to work under undue stress. This increases the likelihood of leaks. In extreme cases, it can cause bursts.
Valves and seals wear out faster under high pressure. This leads to early failures. Replacing these parts can be expensive.
Appliances like washing machines and dishwashers are affected. They may operate less efficiently or sustain damage. This inefficiency or damage can raise maintenance costs.
Water consumption escalates with high psi. This results in a higher water bill. Monitoring and adjusting the psi is crucial to avoid these issues.
What Should I Do If My Pressure Regulator Doesn’ t Maintain A Consistent Psi?
When facing irregular psi levels from your pressure regulator, swift action is essential. This prevents potential system failure.
Start by examining the regulator. Look for physical damage or wear. These issues can hinder its performance.
Ensure the regulator’s installation is correct. It must align with the system’s specifications. Incorrect installation or mismatched specs can cause psi fluctuations.
Inspect for debris or blockages. These can obstruct flow, leading to pressure inconsistencies. Clean both the regulator and the system to remove any obstructions.
If issues persist, professional advice may be necessary. Alternatively, replacing the pressure regulator could be the solution. A malfunctioning regulator fails to maintain stable psi. This compromises the system’s efficiency and safety.
Conclusion
In conclusion, the ideal psi for a pressure regulator is contingent on the specific needs of the application and the equipment it serves.
Ensure you consult your equipment’s manufacturer guidelines for the most accurate psi settings.
For optimal performance and safety, don’t hesitate to seek professional advice for precise calibration.