Why Does My Air Regulator Leak Air
An air regulator, an essential component in compressed air systems, controls the pressure of air output to ensure optimal performance of pneumatic tools and processes. However, users may sometimes encounter a situation where the air regulator begins to leak, compromising system efficiency and safety. This article delves into the common causes behind air regulator leaks and outlines practical troubleshooting steps. Understanding these aspects is crucial for maintaining system integrity and preventing downtime or damage resulting from inconsistent air pressure levels.
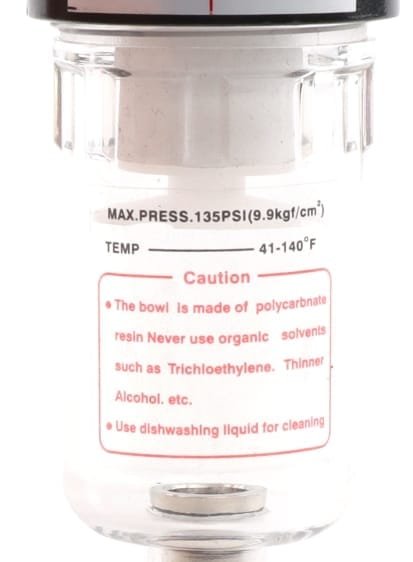
Are Air Regulators Supposed to Leak?
No. Air regulators are designed to control air flow efficiently without any leakage. Leakage is not a characteristic or an intentional feature of an air regulator’s function but rather indicates an underlying issue needing attention.
Leakage in air regulators can stem from several sources such as wear and tear of internal components, defective seals, or incorrect installation. These leaks not only compromise the efficiency of the air compressor system by causing fluctuations in air pressure but also lead to increased operational costs over time due to wasted energy. In industries where precision and reliability are paramount, even minor leaks can significantly impact performance and safety standards.
Common Causes of Air Regulator Leaks
Air regulators play a pivotal role in managing the air pressure in compressors and pneumatic tools, ensuring operational efficiency and safety. However, they are not immune to issues, and leaks can occur, impacting system performance. Understanding the common causes behind these leaks can help in identifying and rectifying them promptly.
Damaged Seals and O-rings: One of the most frequent reasons for air regulator leaks is damage to seals and O-rings. These components are crucial for maintaining airtight connections but can deteriorate over time due to wear or exposure to extreme temperatures and chemicals, leading to air escape.
Cracked Diaphragms: The diaphragm within an air regulator helps regulate pressure by expanding and contracting. If it becomes cracked or torn, possibly from material fatigue or improper handling, it compromises the regulator’s ability to maintain desired pressure levels, resulting in leaks.
Loose Fittings or Connections: Air leakage might also stem from loose fittings or connections within the air regulator setup. Such issues typically arise from inadequate tightening during installation or gradual loosening caused by machine vibrations during operation.
Improper Installation: An incorrectly installed air regulator may lead to immediate or future leaks. This includes cross-threading pipes during assembly which can damage threads and seal integrity. Ensuring that components are correctly aligned and secured is vital for preventing leakage.
Vibrations: Continuous vibrations from machinery can weaken joints and fastenings over time. This mechanical stress often leads to small gaps forming between connections, through which air can leak.
Threaded Pipe Issues: Lastly, problems with threaded pipes—whether due to incorrect thread type usage, damaged threads, or insufficient thread tape—can contribute significantly to leakage in air regulation systems.
Identifying these common causes is the first step towards addressing air regulator leaks effectively. Promptly dealing with damaged components, ensuring tight connections, proper installation practices, and regularly inspecting the system for signs of wear can mitigate these issues before they compromise the efficiency of your compressed air system.
Damaged Seals and O-rings
One of the primary reasons air regulators leak is due to damaged seals and O-rings. These components are crucial for maintaining a tight seal within the regulator, ensuring that air only flows where it is intended. Over time, exposure to air, moisture, varying temperatures, and pressure fluctuations can cause these seals and O-rings to wear out or degrade. This degradation can lead to small fissures or complete breaks in the seal integrity.
When seals and O-rings become compromised, they no longer provide an effective barrier against air escape. Consequently, you might notice a decline in the performance of your air compression system as it struggles to maintain the desired pressure levels due to leaking air.

Cracked Diaphragms
A cracked diaphragm within an air regulator is a significant issue that can lead to air leaks, impacting the efficiency and performance of pneumatic systems. These diaphragms are designed to flex and move within the regulator, controlling the flow and pressure of air as it passes through the system. Over time, due to regular wear or exposure to harsh conditions, these diaphragms can develop cracks.
The integrity of the diaphragm is crucial for maintaining precise control over air pressure. Once cracked, the ability of the diaphragm to effectively manage air flow is compromised, leading to inconsistencies in pressure regulation and potentially causing the regulated pressure to fluctuate or drop unexpectedly. This not only impacts tool performance but can also lead to increased energy consumption as the system attempts to compensate for lost pressure.
Loose Fittings or Connections
These components are pivotal in ensuring airtight seals within the air pathway but can become compromised over time due to various factors such as human error during installation, natural wear and tear, or even thermal expansion and contraction which alters the fit between connected parts.
When these components do not securely fasten as intended, they permit the uncontrolled escape of air. This not only leads to a decrease in system pressure that can adversely affect tool performance but also increases operational costs due to wasted energy.
Identifying loose fittings or connections typically involves a meticulous inspection process. Key signs include audible hissing sounds at connection points or visible signs of movement between coupled parts. Once identified, tightening these components is often straightforward using appropriate tools. However, care must be taken not to over-tighten, as this could lead to thread damage, creating another potential leak path.
In scenarios where fittings continue to demonstrate leakage despite being properly tightened, it might indicate issues beyond mere looseness – such as damaged threads or incompatible part sizes – necessitating further investigation and possible replacement of the affected components.
Improper Installation
Improper installation is a common cause of air regulator leaks and can compromise the efficiency and safety of pneumatic systems. Achieving a secure, leak-free installation requires careful attention to several key factors, including correct alignment, adequate tightening, and the use of appropriate thread sealants.
An incorrectly installed air regulator may exhibit misalignment between the regulator and its connecting pipes or hoses, leading to stress on the fittings that can cause small gaps through which air can escape. To prevent this issue, it is vital to ensure that the regulator is aligned correctly with the airflow direction indicated by arrows on its body before securing it in place.
Over-tightening or under-tightening connector nuts can also result in leaks. Excessive force can damage threads or deform components creating pathways for air leakage, while insufficient force might not sufficiently compress seals to form an airtight connection. Manufacturers typically provide torque specifications to help users achieve the right balance.
Additionally, improper use or absence of thread sealant can be a culprit behind leaking connections. Teflon tape or pipe dope are commonly used to fill gaps between threaded connections, enhancing their seal. However, applying these materials requires precision; excess material can enter the air system causing blockages or other issues, whereas too little might not effectively seal threads against leaks.
Vibrations
The constant motion generated by an operating air compressor or the environment in which the regulator is housed can loosen fittings, degrade internal components like diaphragms, seals, and O-rings, and cause micro-cracks in the material of the regulator itself. It’s imperative to understand how these seemingly innocuous oscillations can have such a profound effect.
Firstly, vibrations may cause fasteners and connections within the system to become loose over time. This loosening allows air to escape where it otherwise would not, leading to inefficiencies and leaks. Regular maintenance checks are necessary to tighten these elements and ensure they remain secure against vibratory forces.
Secondly, vibrations directly affect the wear and tear of internal components. The recurring stress weakens materials like rubber O-rings and diaphragms, which are crucial for maintaining tight seals within the regulator. These parts may crack or warp under the strain, losing their ability to prevent air from leaking out of the system.
Lastly, prolonged exposure to intense vibrations can lead to fatigue in metal parts of the regulator itself. This phenomenon results in fine cracks that might not be immediately visible but can allow air leakage over time. Such structural damage often requires more than just tightening or replacing small parts; it may necessitate complete replacement of the afflicted component.

Threaded Pipe Issues
These leaks are often a result of improper thread engagement or damage to the threads themselves, which can compromise the seal and allow air to escape. Thread tape or thread sealant is commonly used to enhance sealing in threaded connections, but incorrect application can lead to its own set of problems.
When applying thread tape or sealant, it’s vital to ensure that it’s done so in a manner that doesn’t impede the threads’ ability to form a tight seal. Over-application of tape or sealant can cause blockages within the air pathway, while under-application might not sufficiently cover the threads, leaving gaps for air to escape through. Additionally, cross-threading during installation is a prevalent error that can damage both male and female threads, compromising the connection’s integrity.
It’s also important to consider the material compatibility of thread tape or sealant with both the piping and the air compressor system. Certain chemicals found in some sealants may react adversely with specific materials used in piping or regulators, leading to degradation over time and eventual leakage.
How to Fix Air Regulator Leaks
Identifying and fixing leaks in air regulators is essential for maintaining the efficiency and longevity of your air compressor system. The process involves several steps, tailored to address various common causes of leaks. Here’s a guide on how to repair these leaks effectively.
Inspect Seals and O-rings: Begin by examining the seals and O-rings within your air regulator. These components are often the culprits behind air leaks. If they appear worn out or damaged, replacing them should be your first step. Ensure you use replacements that precisely match the specifications required for your particular regulator model.
Check Diaphragms: A cracked diaphragm within the regulator can also lead to air leakage. Carefully inspect the diaphragm for any signs of wear or damage. In case of any defects, replacing the diaphragm with a new one is necessary. Always refer to the manufacturer’s guidelines when selecting a replacement to ensure compatibility.
Tighten Loose Fittings or Connections: Sometimes, leaks result from fittings or connections that have become loose over time. Examine all connections on your air regulator, including where it attaches to the air compressor line. Use appropriate tools to securely tighten these connections without over-tightening, which could potentially cause more damage.
Ensure Proper Installation: Incorrectly installed air regulators are prone to leakages. Verify that your regulator is installed according to the manufacturer’s instructions. Pay special attention to thread orientation and sealing procedures since improper installation can lead not only to leaks but also potential safety hazards.
Address Vibrations: Continuous vibrations can loosen fittings over time, leading to leaks. Implementing vibration dampening measures or checking for misalignment in connected equipment can mitigate this issue. Regular maintenance checks are advisable to preemptively tighten connections before they lead to leakage.
Resolve Threaded Pipe Issues: For regulators connected via threaded pipes, ensuring that threads are properly sealed is crucial. Teflon tape or pipe dope can be used as sealants on threaded connections, enhancing their leak resistance. Apply these materials carefully around the threads before making the connection secure.
Repeated instances of continuous leaking despite addressing these areas might indicate a more complex problem within your air compressor system requiring professional attention. Maintenance and repairs conducted timely not only save on repair costs but also extend the life span of your systems significantly while maintaining operational efficiency.
Can a Leaking Air Regulator Damage the Air Compressor?
YES. When an air regulator leaks, it fails to maintain consistent pressure, leading to potential overworking of the air compressor.
Continually operating under such strain can result in undue wear and tear on the compressor’s internal components. This scenario often leads to a decrease in performance efficiency, as the compressor has to work harder and longer to achieve the desired pressure levels. Over time, this increased workload can cause overheating and result in premature failure of parts or even necessitate complete replacement of the compressor unit.
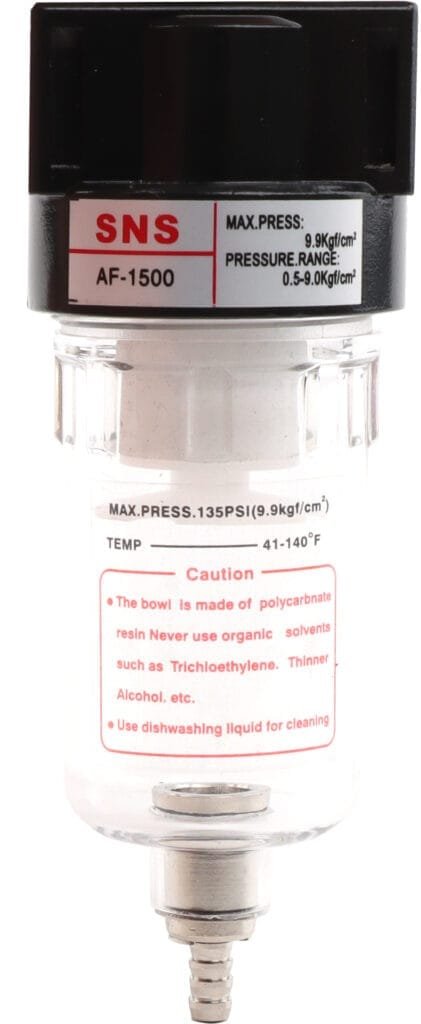
What Should I Do If My Air Regulator Leaks Continuously?
Initially, try to identify the source of the leak. Often, continuous leakage can be attributed to damaged seals or O-rings, cracked diaphragms, loose fittings or connections, improper installation, vibrations affecting the equipment, or issues with threaded pipes.
Firstly, inspect all visible parts of the air regulator for any signs of damage or wear and tear. Pay special attention to seals and O-rings since they are commonly affected areas and can be relatively straightforward to replace if found defective.
Secondly, ensure that all fittings and connections are tight and properly aligned. Sometimes, simply tightening a loose connection can resolve the issue without further intervention needed.
If you suspect improper installation might be the culprit behind the continuous leak, reassessing the setup according to the manufacturer’s guidelines can provide insight into any adjustments that need to be made.
Furthermore, consider whether external factors like vibrations from nearby machinery could destabilize your air regulator over time. In such cases, securing or relocating equipment may help mitigate these effects.
Should these attempts not stop the leakage or if you’re unable to pinpoint its source accurately, seeking professional assistance becomes imperative. A specialist in compressed air systems will have both the expertise and tools necessary to diagnose complex issues accurately and perform repairs safely.
Procuring quality replacement parts is equally important when fixing any component of your air compressor system. Using substandard materials could lead not only to recurrent leaks but also potentially degrade other parts of your system over time.
Lastly but significantly, regularly maintaining your air compressor system can prevent many common causes of leaks in air regulators before they start. Adhering to a planned maintenance schedule helps catch potential problems early on while ensuring your setup operates efficiently for longer periods.
In Conclusion
In summary, air regulators leak due to worn-out seals, improper pressure settings, or physical damage, necessitating timely inspection and maintenance.
To ensure the longevity and proper functioning of your air regulator, consider scheduling regular maintenance checks with a certified technician. Additionally, for any immediate repair needs or preventative advice, do not hesitate to contact us for professional assistance.