Why Is My Air Regulator Not Working
An air regulator is a crucial component in compressed air systems, designed to maintain a constant output pressure despite variations in the input pressure from the air supply. When an air regulator fails to operate as expected, it can lead to inefficiency in pneumatic tools and processes, potentially causing operation disruptions or damage to equipment. This article explores common causes and troubleshooting steps for non-functioning air regulators to help you quickly identify and address the underlying issues.

What Happens If Your Air Regulator Is Not Working?
When an air regulator malfunctions or ceases to work, it results in a disruption of the air pressure control in your system. This critical component is designed to maintain a consistent output pressure despite fluctuations in the input pressure from the air supply. A non-functional air regulator can manifest in various operational challenges, such as the inability to precisely control pneumatic tools and equipment, potentially leading to damage or inefficient operation.
At its core, an air regulator aims to provide steady air pressure to downstream applications. Without this regulation, equipment might receive either too low or excessively high-pressure levels. Low-pressure scenarios can cause pneumatic tools to underperform, lacking the power or speed required for optimal operation. Conversely, excessive pressure poses a risk of overloading the tools or creating unsafe operating conditions that might lead to equipment failure or pose hazards to operators.
Moreover, certain processes and applications rely on precise pressure adjustments to achieve desired outcomes. In these contexts, an unreliable air regulator disrupts process consistency and quality control, possibly leading to product defects or increased wastage.
The repercussions of a failing air regulator extend beyond immediate operational inconveniences. Continuous exposure of pneumatic components to inappropriate pressures may accelerate wear and tear, shortening their lifespan and increasing maintenance costs over time. In industrial settings where production efficiency and safety are paramount, ensuring that your air regulator is functioning correctly becomes indispensable for sustaining performance levels and safeguarding against potential risks associated with unregulated air flow.
Common Air Regulator Problems
Air regulators are crucial components in pneumatic systems, ensuring that downstream equipment receives consistent pressure despite fluctuations in the upstream supply. However, like all mechanical devices, air regulators can encounter several common issues that disrupt their operation. Understanding these problems is key to diagnosing and rectifying them effectively.
- Leakage: Air escapes from the regulator due to damaged seals or connections, leading to energy waste and reduced system efficiency.
- Downstream Pressure Fluctuations: The regulator fails to maintain stable pressure for downstream equipment due to wear and tear, improper size selection, or mechanical failures.
- Upstream Pressure Fluctuations: Inability of the regulator to accommodate significant variations in supply pressure, affecting those with insufficient Supply Pressure Effect (SPE) tolerance.
- Creep: Gradual increase in downstream pressure when the system is at rest, indicating an internal leak or fault within the regulator mechanism.
- Supply Pressure Effect (SPE): Changes in upstream pressure cause changes in downstream pressure, challenging regulators with high SPE sensitivity to maintain consistent output.
- Incorrect Regulator Size: Leads to inefficiency or malfunction due to inadequate flow rate handling or inaccurate pressure control at lower flows.
- Damaged Seals: Result in leaks and performance degradation, caused by wear and tear, exposure to incompatible chemicals, or extreme temperatures.
- Debris Or Contamination: Obstructs internal mechanisms, causing malfunctions such as sticking or inability to adjust pressures effectively.
- Improper Installation: Including incorrect orientation or use of inappropriate thread tape on fittings, leads to operational issues.
- Wear And Tear: Affects all mechanical devices over time, leading to worn-out components and impacting performance and reliability.
- Wrong Type Of Regulator: Using a regulator not suited for specific applications can cause numerous problems; selecting one that closely matches requirements is crucial for optimal performance.
Leakage in Air Regulators
This problem occurs when air escapes from the regulator through its external components or the areas meant to seal connections within the system. Several factors can contribute to leakage, including damaged seals, loose connections, and cracks in the regulator body.
Damaged seals are often the primary culprit behind leakage. Over time, these seals can deteriorate due to wear and tear or exposure to extreme temperatures and chemicals. When seals become brittle or break, they fail to maintain an airtight seal, allowing air to escape.
Loose connections are another significant source of leakage. If the regulator is not properly connected to the hoses or fittings, gaps may allow air to leak out. Ensuring that all connections are secure and correctly tightened is crucial for preventing this type of leakage.
Additionally, cracks or damage to the regulator body itself can lead to air escaping from unintended places. This typically results from physical impact or stress on the regulator over time. Inspecting the regulator for any visible signs of damage can help identify this issue early on.
Downstream Pressure Fluctuations
Downstream pressure fluctuations in air regulators are irregular changes in the output pressure that deviate from the desired set point. These fluctuations can severely impact pneumatic systems, leading to operational instability and potential equipment failure. The root causes of downstream pressure fluctuations vary, encompassing a range of factors from mechanical wear and tear to external environmental influences.
One common cause of these fluctuations is the presence of contaminant particles within the system. Debris or contamination can obstruct the internal passages of the regulator, preventing smooth operation and leading to erratic pressure outputs. Similarly, damaged seals within the regulator can compromise its ability to maintain consistent pressure levels; wear on these components over time is inevitable but can be exacerbated by environmental conditions or improper installation practices.
Another contributing factor is incorrect regulator size or selection for a given application. An undersized or oversized regulator may struggle to efficiently manage airflow, resulting in unstable downstream pressures. Moreover, external factors such as variations in supply pressure also play a pivotal role; supply pressure effect (SPE), where changes in inlet pressure influence outlet pressure despite adjustments made to the regulator setting, exemplifies this issue.
To mitigate downstream pressure fluctuations, ensuring regular maintenance and system checks is vital. This involves inspecting for signs of wear on seals and other internal components, verifying that the regulator is correctly sized for its intended application, and checking for any contaminants that could impede functionality. Addressing these aspects promptly can significantly improve system stability and prolong the lifespan of both the regulator and connected equipment.
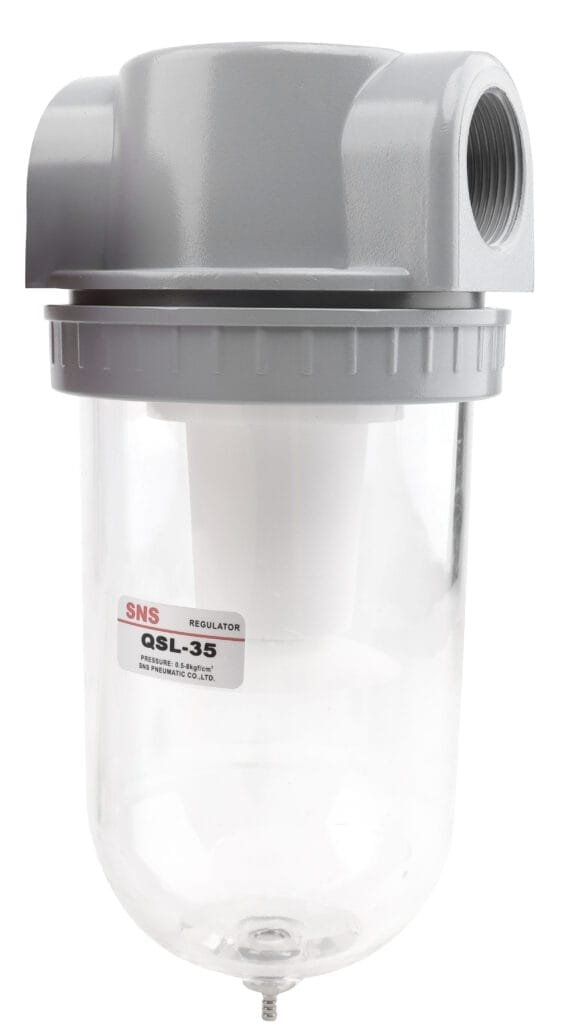
Upstream Pressure Fluctuations
In essence, these are variations in the pressure coming into the regulator from its supply source. Typically, an air regulator is tasked with maintaining a consistent output pressure despite variations in the input or demand; however, excessive fluctuations in the upstream pressure can overwhelm the regulator’s ability to compensate, leading to performance issues.
There are several reasons why you might encounter significant upstream pressure fluctuations. These can range from issues within your compressed air system itself, such as compressor cycling on and off, to external factors like changes in ambient temperatures or variances in supply demand from other equipment connected to the same source.
Identifying upstream pressure fluctuation involves monitoring the input pressure over time to spot variances. It’s essential to equip yourself with accurate gauges and perhaps even data logging equipment if fluctuations are subtle or periodic. Recognizing this problem early allows for corrective measures such as installing a receiver tank closer to the point of use or adjusting your compressor settings.
Creep
Creep in an air regulator refers to a phenomenon where the downstream pressure slowly increases over time, even when there is no change in the upstream pressure or any demand from the system. It’s a critical issue that can lead to equipment malfunction or damage if not addressed promptly. The cause of creep is usually related to internal component failure within the regulator itself. Commonly, it’s attributed to damaged seals or valve seats that fail to close completely. These small gaps allow air to pass through continuously, causing the pressure on the outlet side (downstream) of the regulator to build up gradually.
Addressing creep involves inspecting and possibly replacing these compromised internal components. In some cases, debris or contamination inside the regulator can also contribute to creep by preventing a complete seal. Cleaning the internals of the regulator may remedy this situation without needing complete parts replacement. However, it’s crucial for users to conduct routine maintenance checks and ensure their equipment is properly installed and matched with their specific application needs to mitigate creep effectively.
Supply Pressure Effect (SPE)
The Supply Pressure Effect, colloquially known as SPE, constitutes a notable factor often overlooked when diagnosing issues with air regulators. This phenomenon occurs when there is a change in the supplied pressure, which leads to a variation in the output pressure of the regulator, despite the fact that the setting of the regulator hasn’t been altered. In essence, SPE can be viewed as an indicator of how much the output pressure changes in response to fluctuations in supply pressure.
A regulator’s sensitivity to SPE is largely dependent on its design and quality. High-quality regulators are typically engineered to minimize this effect, ensuring that the output pressure remains stable even if there are changes in the supply pressure. Conversely, low-quality or poorly designed regulators may exhibit significant sensitivity to SPE, leading to unpredictable and fluctuating downstream pressures.
In cases where SPE is determined to be a problematic factor, upgrading to a higher-quality regulator designed to mitigate these effects may be necessary. Additionally, ensuring that your system operates within its recommended supply pressure range can help minimize the impact of SPE on your air regulator’s performance.
Regulator Size
The size of an air regulator should be based on the flow rate requirements of the downstream equipment it is meant to serve. A common mistake is choosing a regulator that is either too small or too large for the intended application.
A regulator that is too small can restrict flow, leading to insufficient downstream pressure which could hamper the performance of pneumatic tools or processes. This scenario forces the regulator to work harder than it should, possibly leading to premature failure due to increased wear and tear.
Conversely, a regulator that is too large for the system’s requirements may not regulate pressure as precisely as needed. In larger regulators, minor adjustments can have less impact on the output pressure, making it difficult to achieve precise control required for sensitive applications. Additionally, larger regulators often come with a higher cost not only in terms of initial purchase price but also in installation space requirements and maintenance efforts.
The optimal selection involves calculating the maximum flow rate your system requires at any given time and choosing a regulator size that can handle this volume adequately without significantly exceeding those needs. It’s also important to consider future expansion or changes in demand that could affect these calculations.
Damaged Seals
Damaged seals in an air regulator are a common issue that can lead to a variety of operational problems, such as leakage and pressure fluctuations. The seals within an air regulator serve as vital components in ensuring the device maintains the required pressure levels by preventing air from escaping. Over time, these seals can deteriorate due to factors like normal wear and tear, exposure to extreme temperatures or chemicals, or simply the age of the regulator itself.
When these seals are compromised, air may begin to leak either internally within the regulator or externally to the atmosphere. This not only reduces the efficiency of the air system but also poses safety risks and increases operational costs due to wasted energy. In addition to leaks, damaged seals can result in downstream pressure fluctuations. As the ability of the seals to maintain stable pressure is diminished, users may observe irregularities in device operation requiring precise pressure settings.
Addressing this problem involves inspecting the regulator for visible signs of damage or wear on its seals. If damaged seals are identified, they typically must be replaced with new ones matching the specifications of your regulator. It’s critical for operators or maintenance personnel to consult the manufacturer’s guidelines or seek professional advice when selecting and installing replacement seals to ensure compatibility and restore optimal functionality of the air regulator.
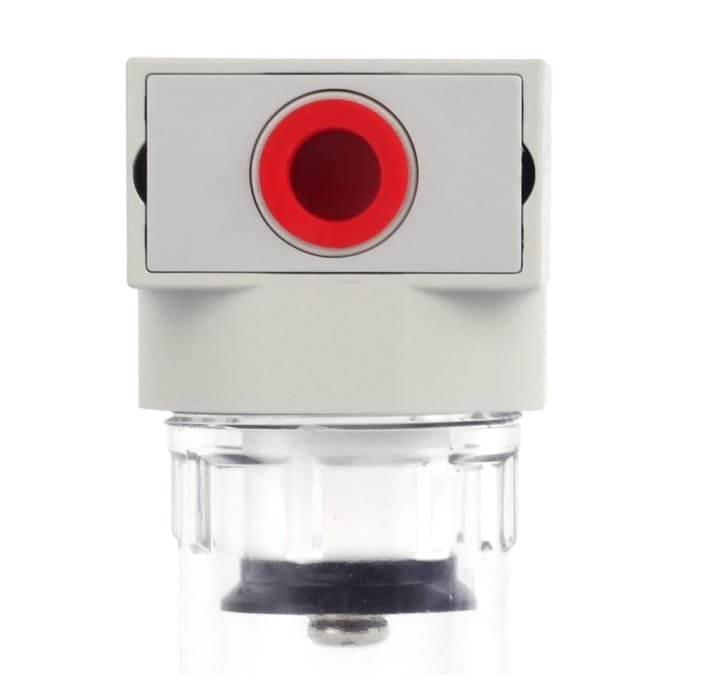
Debris or Contamination
Debris or contamination within the air regulator can lead to various operational issues, impacting both its efficiency and the quality of airflow. Over time, particles such as dust, rust, or other small debris may enter the air system, causing blockages or impairing the internal mechanism of the air regulator. This contamination often occurs due to insufficient filtration upstream or due to wear and tear of internal components that generate particulate matter. These contaminants can affect the accuracy of pressure regulation, leading to inconsistent downstream pressure that may not align with the desired settings.
To address this issue effectively, it’s essential to periodically inspect and clean the air regulator. Inspecting involves disassembling parts according to manufacturer instructions and visually checking for any signs of dirt accumulation or damage. Cleaning should be conducted using appropriate tools and solvents recommended by the regulator manufacturer to avoid further damage. In situations where contamination is significant or if damaged components are discovered during inspection, replacing parts—or in some cases, the entire regulator—may be necessary.
Additionally, installing proper filtration units upstream can significantly reduce the risk of debris entering the air regulator. Choosing filters with an appropriate micron rating for your application will help ensure that most particulate matter is captured before it can reach sensitive components.
Regular maintenance checks and preemptive measures are crucial in preventing debris-related issues within air regulators. By keeping these systems clean and free from contamination, you can enhance their performance longevity and ensure a steady supply of clean, regulated air for your applications.
Improper Installation
Incorrect installation can result from misinterpreting the flow direction, inadequate thread engagement, or failing to use the appropriate thread sealant where necessary. Misaligning the flow direction not only hinders the regulator’s ability to manage air pressure accurately but also might damage its internal components.
Moreover, insufficient thread engagement might cause air leaks that reduce system pressure and efficiency. It’s essential to follow manufacturer guidelines on how many threads need engagement and whether a specific type of thread sealant or tape should be applied to prevent leaks. Many overlook the subtleties in these instructions, leading to compromised connections between the regulator and the air system it’s intended to regulate.
Lastly, one must ensure that the regulator is compatible with both the physical setup and the pressure requirements of the system. A mismatch in specifications can culminate in operational failures, such as inability to handle desired pressure levels or physical incompatibility with existing fittings, which can create additional stress on system components.
Correctly installing an air regulator involves meticulous adherence to manufacturer guidelines regarding orientation, connectivity, and environmental compatibility (e.g., avoiding exposure to corrosive substances). Consulting technical documentation prioritize each connection uses specialized tools as recommended (such as wrenches meant for precise tightness), and testing installations for leaks through methods like soap solution tests are all prudent steps towards ensuring optimal performance of an air regulatory system.
Wear and Tear
Wear and tear on air regulators is an inevitable occurrence over time, stemming from the constant friction and pressure changes they undergo during operation. This degradation can manifest in several ways, impacting the efficiency and functionality of the regulator. Key components such as O-rings, seals, springs, and diaphragms are particularly susceptible to wear, leading to a decrease in performance that may include leaks, inaccurate pressure control, or complete failure. To mitigate these issues, it’s essential for users to conduct regular inspections and maintenance of their air regulators.
Identifying signs of wear early can prevent more significant problems down the line and extend the lifespan of the equipment. In situations where wear and tear have led to substantial damage, replacing affected components—or in severe cases, the entire regulator—may be necessary to ensure optimal performance. Regular training on the proper care and handling of air regulators can also reduce premature wear, ensuring these vital tools perform reliably for as long as possible.
Wrong Type Of Regulator
Choosing the wrong type of regulator for your air system can lead to a variety of issues, including inadequate pressure control and premature equipment failure. Each air regulator is designed to perform within specific parameters, tailored to certain applications and media it controls. When the wrong type of regulator is selected, it may not handle the required flow rates or pressures, leading to suboptimal performance or even damage to the regulator itself.
For instance, a regulator designed for low-pressure applications will not be adequate in a high-pressure system, potentially causing an unsafe environment due to the inability to withstand the pressure exerted upon it. Conversely, utilizing a high-pressure regulator for low-pressure requirements can result in poor control accuracy due to its design for handling much higher pressures.
Moreover, materials play a critical role in selecting the correct type of regulator. Air systems might introduce moisture or other contaminants that certain regulators are not designed to cope with, leading to corrosion or internal damage over time. Such scenarios underscore the importance of matching the regulator not only with the pressure and flow requirements but also considering compatibility with the environment it operates in.
In addition, specialty applications require specific types of regulators. For example, medical gas delivery systems demand precise and reliable regulators that adhere to stringent standards for safety and cleanliness. Employing a general-purpose air regulator in such settings could jeopardize patient safety and contravene regulatory requirements.
Ultimately, ensuring you have chosen the right type of regulator necessitates understanding your system’s demands thoroughly—including pressure, flow rate, medium composition—and how they interact with the available types of regulators on the market. Consulting with professionals or manufacturers during selection can mitigate risks associated with using an inappropriate device for your needs. Selecting properly helps avoid unnecessary downtime, extends equipment life span, ensures operational safety, and maintains optimal system performance.
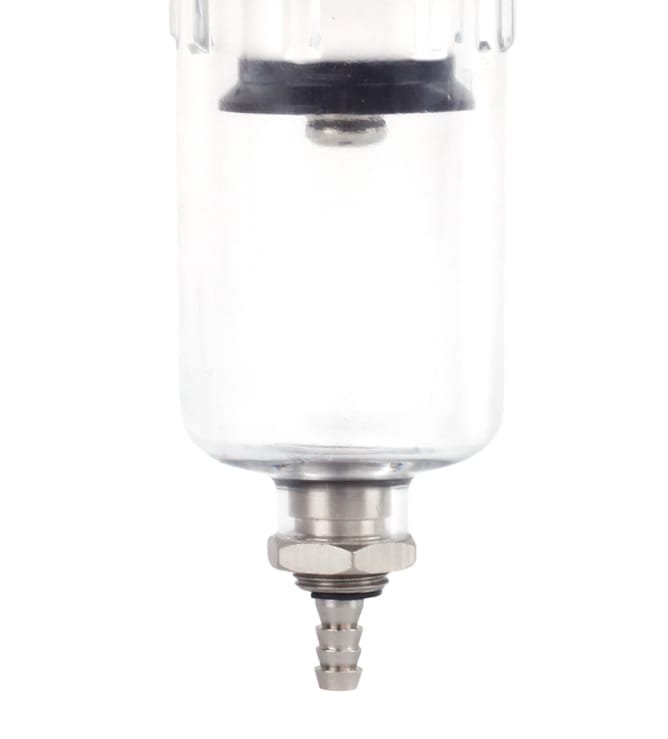
How To Replace The Air Regulator
Replacing an air regulator is a task that requires attention to detail and understanding of the system you’re working with. If your air regulator is not functioning correctly due to issues such as leakage, downstream pressure fluctuations, creep, or wear and tear, following these steps can help ensure a successful replacement.
Step 1: Safety Precautions Before attempting any repairs or replacements, ensure all safety protocols are followed. This includes turning off the air supply and releasing any pressure in the system to avoid accidental injuries.
Step 2: Remove the Faulty Air Regulator Locate the faulty air regulator within your system. Use appropriate tools to carefully disconnect it from the system. This may involve loosening fittings or clamps that secure the regulator in place. Handle all parts gently to prevent damage to surrounding components.
Step 3: Prepare for Installation Inspect the area where the old regulator was situated for any debris or contamination that could impair the function of the new regulator. Clean this area thoroughly before proceeding with installation of the new unit.
Step 4: Selecting the Right Type of Replacement Regulator Ensure that your replacement air regulator matches your system’s requirements, including size, pressure ratings, and compatibility with your media type (air or gas). Using a regulator that doesn’t meet your needs can result in operational failures.
Step 5: Install the New Air Regulator Carefully position the new air regulator in place, making sure it aligns correctly with all connection points. Secure it firmly without overtightening to avoid damaging seals or threads. Ensure that its orientation follows manufacturer guidelines for proper airflow direction.
Step 6: Re-establish Connections Once securely installed, reattach any hoses or tubes previously disconnected during removal of the old unit. Make sure these connections are tight and leak-free but again be wary of overtightening which could cause damage.
Step 7: Test Functionality Slowly turn on your air supply while continuously monitoring for leaks around newly made connections. Adjust your inlet pressure according to manufacturer specifications using appropriate calibration tools if required. Validate correct operation through functional tests relevant to your application, such as checking response time and stability under varied pressures.
By following these detailed steps, replacing a non-working air regulator can be performed efficiently while minimizing risks associated with improper installation or selection errors. This methodical approach ensures not only a return to optimal operation but also contributes significantly toward maintaining safe working conditions within pneumatic systems environments.
In Conclusion
In conclusion, a malfunctioning AIR regulator can stem from a variety of issues, including improper setup, contamination within the system, or internal damage to the regulator itself.
To ensure your operations remain efficient and safe, it’s essential to diagnose and address any problems with your AIR regulator promptly. Consider consulting with a professional or seeking expert services to accurately identify and remedy the issue at hand.